数控机床虚拟装配系统的研究
2025-4-10 来源:南京工业大学工程训练中心 作者:马康荣
1.引言
在现代机械制造业中,数控机床作为核心装备之一,其性能与制造精度直接影响着工业生产的效率和产品的质量。随着全球市场竞争的加剧及技术进步的推动,中国机械制造业迈向数字化、定制化和智能化的新阶段。此背景下,传统的数控机床设计与装配流程面临着诸多挑战,尤其是设计周期延长和装配校验成本提高等问题已成为制约行业发展的瓶颈。因此探索一种能够提高设计效率、降低装配成本并确保机床性能的新技术尤为迫切。
2. 数控机床虚拟装配系统总体设计
2.1 系统结构设计
在数控机床虚拟装配系统的研发过程中,系统结构设计扮演了至关重要的基础性角色(图 1)。
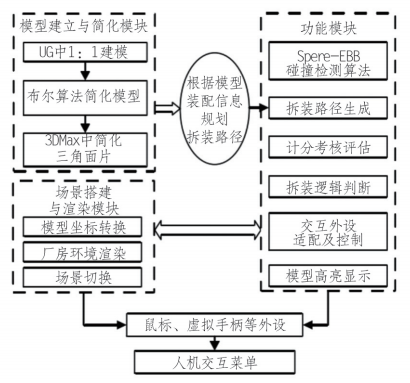
图 1 系统整体结构
系统旨在构建一个跨平台兼容、用户友好的虚拟装配环境,通过高度的沉浸感和直观高效的操作体验,提升用户工作效率。为达到这一目标,系统被细分为 4 个核心模块 : 模型建立与简化模块、场景搭建与渲然模块、功能模块和人机交互模块。
场景搭建与渲染模块负责将模型放置于接近现实的虚拟环境中,通过光源等渲染技术增强场景的真实感,为功能模块的实施提供视觉基础,确保用户体验既真实又舒适。
系统的核心组成部分是功能模块,其集成装配路径规划、零件拆卸与拾取等关键操作,在严格遵循机械工艺标准的基础上,设计并生成最佳的装配路径。为提高操作的精确度和响应速度,模块中引入碰撞检测机制。此外,功能模块还包含多功能区域,例如演示、练习和考试评估,以满足不同用户群体的训练和评价需求。
人机交互模块负责实现场景的无缝漫游和切换。通过融合 Steam VR 插件,用户可以利用头戴式显示器和 Vive 操控器,从第一人称视角进行场景探索和零件操纵。这一设计极大地提升了用户的沉浸感和操作的直观性。
2.2 系统设计方法
在数控机床虚拟装配系统的实现研究中,为确保最终系统功能完备、用户沉浸感强,系统设计方法须具备科学性和合理性。本研究采用Unity 3D 作为开发引擎,详细规划了从模型构建到最终系统集成与发布的全过程,系统搭建框架如图 2 所示。首先,采用 UG(现称为 NX)软件对目标数控机床进行 1:1 的精确测绘工作,确保模型的几何精度与实物相符合。完成测绘后,将模型以标准转换协议格式 STEP 导出。随后,将所得的 STEP 格式模型引入至 3D Max 软件环境中,进行必要的优化处理。这一阶段主要移除模型中存在的冗余几何元素,包括非必要的多层面等,以及为模型赋予适当的材料和纹理,进行渲染处理,从而提升视觉效果,确保模型在虚拟环境中的真实性和逼真度 。
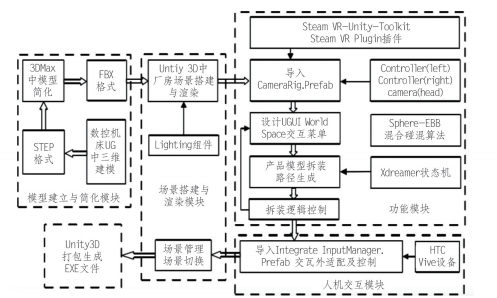
图 2 系统框架搭建
3. 数控机床虚拟系统三维模型建构
3.1 机床模型建构
在数控机床虚拟装配系统的开发研究中,机床模型的构建是系统的基础和核心要素。三维建模技术在此过程中发挥了重要作用,它运用计算机图形学技术,精确地复制现实物体的几何结构和表面特征,以创造出高度逼真的复杂三维模型。在高度精细的虚拟仿真领域构建三维环境,包含各种厂房、拆卸工具和设备。这些建筑和工具以精确的三维模型形式呈现,其真实度直接影响用户沉浸感的强度及整个系统交互性能的优劣。
通过实地测量、综合分析相关文献资料,精心捕捉实体设备的准确尺寸、外观颜色和材料特性等关键信息。利用专业建模软件进行几何结构的精确复制,并根据应用需求设定相应的约束条件。为降低系统资源消耗,对模型的顶点数量和三角面片数量进行优化 ; 为增强现实感,向模型中添加物理属性,包括重力和加速度。本研究选择了 UG 软件来构建数控机床模型,该软件在处理复杂实体和造型方面具有显著优势,并支持多种建模技术的融合。
数控机床采用自底向上的方法,先构建基础零件,再逐步组装成上一级部件,最终完成整个机床的装配。这种方法有助于提高装配效率,简化装配路径规划,并防止在零件绘制过程中出现遗漏。在机械装配工艺中,必须注意使用标准工具避免损害精密零件 ; 紧固螺栓时应均匀对称操作 ; 所有电气元件的导线接头需做好标记。依据实物数据,将零件模型拆解并分层级,利用多边形编辑和高级命令生成简单几何体,然后通过布尔算法构建复杂零件。
3.2 机床碰撞检测算法
混合层次包围盒算法(Hybrid HierarchicalBounding Volume Algorithm)是一种先进的碰撞检测技术,其在构造包围盒树时,通过融合多种包围盒的互补特性,于树的不同层级上部署不同性能的包围盒。该算法的设计旨在提升碰撞检测的准确性和效率,有效避免模型间的相互穿透问题。
算法的实施过程可划分为 3 个关键阶段 : 预处理、初步检测和精确检测。
在预处理阶段,算法涉及包围盒的选择,这一步骤需要考虑到包围盒的几何特性、系统资源配置及模型的特定属性。在此基础上,精心规划边界体积层次结构(Bounding VolumeHierarchy,BVH)的结构设计和遍历策略,以确保高效的碰撞查询性能。
在初步检测阶段,算法利用所选包围盒进行快速排除测试,以减少后续阶段需要处理的候选物体数量。在此过程中,选择球形(Sphere)包围盒作为根节点的包围体,其优势在于能够迅速排除大量不相交的物体,显著降低三角基元的检测负担。
在精确检测阶段,进行算法执行包围盒间及三角形基元间的详细相交测试,确保碰撞检测的高精度性。
包围盒层次结构树的构建策略主要有 3 种 :自顶向下、自底向上和插入法。
(1)自顶向下的策略是最为广泛采用的构建方法,其核心在于递归算法的应用。这一策略的构建过程在逻辑上模拟了自然界中树木的生长机制。在具体操作过程中,首先选择包含整个模型所有几何信息最外层的包围盒作为层次结构树的根节点。依据树的平衡原则和相关数据信息,通过递归的方式将根节点划分为多个子集,这些子集作为父节点即 “分叉”,继续对各个子节点进行递归划分,直至达到叶节点,即一个三角形基本元素。
(2)自底向上的策略主要通过聚类合并算法来实现构建。在初始阶段,需要对模型的三维数据进行全面处理,获取全部三角基本元素的信息。针对每一个基本元素构建出最紧密的包围盒,作为包围盒层次结构树的底层叶节点。根据三角基本元素间的相关性,将多个叶节点进行聚类,逐步合并为一个新的子节点,然后继续进行节点类的合并,直至形成根节点。
(3)插入法主要是根据成本函数,将单个三角基本元素按照最低成本插入到树型结构的节点处。通过不断重复此过程,将每个基本元素进行填充,最终构建出成本最低的包围盒层次结构树。
4. 数控机床虚拟装配系统的实现
4.1 人机交互实现
在数控机床虚拟装配系统的开发过程中,人机交互的科学设计及精确实现对提升用户体验、增强系统实用性具有决定性作用。该系统融合了多种输入设备,包括鼠标、触屏及虚拟现实(VR)手柄,以实现一系列丰富的交互功能。系统的人机交互设计支持多硬件平台,包括智能手机、电脑 PC 端和 VR 设备,确保了使用方式的多样性和广泛的可访问性。用户可以通过不同的设备执行操作,例如进行场景切换、状态机响应和碰撞反馈等。
碰撞反馈机制通过Unity 3D 的射线和Gameobject 组件来实现。当模型间发生接触时,系统会提供文字提示,从而增强操作的直观性和指导性。此外,人机界面的设计采用 UGUI 系统,不仅直观易用,而且允许开发人员在运行过程中实时调整 UI 元素,从而提高开发效率和界面的适应性。整个系统的人机交互实现经过精心规划与设计,使得数控机床虚拟装配系统不仅具备强大的功能,还拥有友好的用户界面,确保用户能够轻松地与系统进行高效交互。这种交互设计的深度与广度为用户提供了一个高度逼真、互动性强的虚拟装配环境。
4.2 功能模块实现
基于数控机床的装配结构树和位置约束,可以制作符合实际工艺的拆卸动画。在 Unity 3D中,使用 Animation 控件的关键帧功能来关联各个动画,完成制作。以纵向进给系统为例,先根据机械规则和几何建模信息逆序求解拆卸序列,然后从零件库中调用所需的模型和工具,并设置时间区间、路径、偏移等参数。
用户可通过点击 “演示” 按钮进入功能界面。界面提供时间轴播放器、步骤列表等提示框,以便辅助学习拆卸过程。系统集成了人机交互的手柄功能按键,包括触控板、菜单按钮等。用户可以通过手柄控制器上的脚本实现自主漫游。
虚拟装配功能使用 C++ 语言编写碰撞检测算法,并与后台进行集成。在选中零件时,系统进行预处理,读取三角面片的顶点索引,并生成包围盒层次树。当发生碰撞时,系统读取 ID 信息,并将其反馈到文本框中。图 3 所示的手轮触碰尾架盖时,系统会做出相应的响应,并弹出提示框,以指导用户的操作,提升其实操能力。
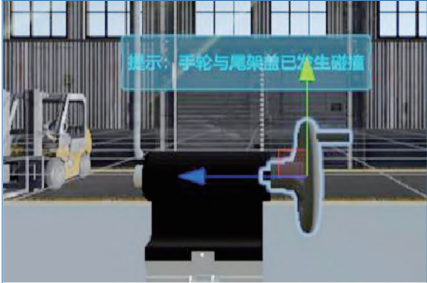
图 3 零件发生碰撞效果
5. 结束语
本次研究成功实现数控机床虚拟装配系统的功能模块搭建 : 首先,进行数控机床模型的构建,采用自下而上的装配层次树构建方法进行模型建设 ; 其次,基于混合层次包围盒算法的碰撞检测技术验证其在碰撞检测时间和检测精度方面的优越性 ; 最后,完成数控机床虚拟装配系统的设计和实现。通过该系统用户可以进行真实感的虚拟装配操作,并获得实时的反馈和提示信息,提高用户的实操水平。
投稿箱:
如果您有机床行业、企业相关新闻稿件发表,或进行资讯合作,欢迎联系本网编辑部, 邮箱:skjcsc@vip.sina.com
如果您有机床行业、企业相关新闻稿件发表,或进行资讯合作,欢迎联系本网编辑部, 邮箱:skjcsc@vip.sina.com
更多相关信息