叶片泵转子叶片槽的分度铣床夹具设计
2017-7-7 来源:北京工商大学材料与机械工程学院 作者:刘玉德,侯亚茹,吴 刚,张 浩,王 硕
摘要:设计用于卧式铣床加工的叶片泵转子叶片槽的分度铣床夹具,铣刀每次加工一个槽,通过分度装置使工件转动一定角度到达加工位置,依次完成其它槽的加工。
关键字:叶片泵;分度;铣床;夹具
0.引言
夹具最早出现在 18 世纪后期, 随着科学技术的不断进步,夹具已从一种辅助工具发展成为门类齐全的工艺装备。 夹具可快速、方便地将工件安装到指定位置,大幅提高了产品精度,使工艺更加便捷
,使用相当广泛。 按用途分,可将夹具分为焊接夹具、机床夹具、装配夹具、检验夹具等。
1.零件图分析
被加工的零件如图 1 所示, 零件的毛坯为 40Cr,金属模铸造,技术要求与尺寸精度都不高,生产批量为 2 000 件,其加工工序为:车外圆,保证 Φ50mm 外圆→车端面,保证 24mm 的长度→中心钻孔、扩孔、铰孔至尺寸要求→铣槽。 其中,铣槽的过程需要用到分度装置,铣刀每加工一个槽,通过分度装置使工件转动一定角度到达加工位置,以便完成其它槽的加工。
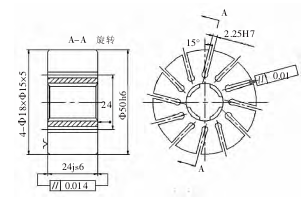
图 1 工件零件图
2.夹具设计
保证工件加工质量是机床夹具设计的基本要求,也是夹具设计的首要任务。 为此,必须正确地设计与选择定位方法、定位件及夹紧装置。 在设计之前,要认真了解工件的作用、特点、材料、生产规模及技术要求, 详细分析加工工艺过程及本工序的加工要求,如加工余量、加工精度、加工表面、定位基准以及前后工序的联系等。 本文夹具的设计主要分成以下几个方面:定位方案、夹紧方案、分度装置、夹具体和连接元件的设计。
2.1 定位方案
工件定位是指在工件加工之前,将工件放在相对于机床、刀具一个比较准确的加工位置。 工件的定位,实质上是对空间自由度的限制,根据工件自由度被约束的情况,工件定位方式有完全定位、不完全定位、欠定位、过定位 4 种。本设计因加工的需要,在铣槽的过程中零件不能发生任何移动,6 个自由度都要进行约束,故选用完全定位。 定位方法为花键孔和主轴端面定位,图 2 为定位主轴设计图。
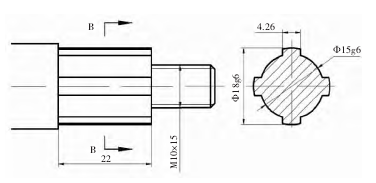
图2 定位主轴图
空间 6 个自由度的限制,虽然解决了工件在加工过程中“定与不定”等问题,但每个工件在加工过程中所占据的位置并不一致,这就涉及到“准与不准”的问题。 工件在夹具中所占据的位置不准确,加工的工件尺寸必然不一致,就会形成误差,称之为定位误差,用ΔD 表示。 生产中为了保证加工精度,一般要求定位误差不超过工件加工公差 T 的 1/5~1/3。 定位误差包括基准位移误差和基准不重合误差,当无基准位移误差时,ΔY=0;当定位基准与工序基准重合时,ΔB=0;若两项误差均没有, 则 ΔD=0。 分析和计算定位误差的目的,是为了验证定位方案能否保证定位要求,以便对不同方案进行比较,从而选出最合理的方案。从零件设计要求可知, 工件和轴的配合尺寸为φ18H7/g6, 查阅国标轴、 孔的基本偏差表有:ΔB=0;ΔY=ES-ei=0.021-(-0.017)=0.038mm;ΔD=0.038mm。按照 GB/T 1804—2000 《未注公差的线性和角度尺寸公差》要求,指明工件加工公差等级为中等 m,则T =0.1 -(-0.1) =0.2mm。 而 ΔD =0.038mm ≤(1/5 ~1/3)T =0.04~0.067mm,定位方案合格。
2.2 夹紧方案的设计
在夹紧过程中,工件应能保持在既定位置,即在夹紧力作用下工件不应离开定位支承;夹紧力的大小要适当、可靠。 既要使工件在加工过程中不产生移动和振动,又不使工件产生不允许的变形和损伤,夹紧装置的自动化程度和复杂程度应与工件的产量和批量相适应。夹紧装置主要由动力装置、中间递力机构、夹紧元件组成。 常用的夹紧装置有楔块、螺旋、偏心轮等,楔块夹紧可改变夹紧力方向,但使用效率低,多用于机动夹紧装置中;螺旋夹紧结构简单、自锁性好、夹紧可靠、紧行程不受限制,远比楔块夹紧力大,其通用性大,但效率低,多用于手动夹紧装置中;偏心夹紧机构产生的夹紧力较小,自锁性能不好,一般用于切削力不大且无振动的场合,对夹紧尺寸要求严格。 可见各夹紧装置都有各自的优缺点,应结合设计要求选择合理的夹紧装置。 综合以上特点,本设计选用螺旋夹紧装置。花键主轴上的螺杆、开口垫圈和夹紧螺母为主要的夹紧元件。 当旋紧夹紧螺母时,通过开口垫圈将工件夹紧在花键主轴上。 查阅资料,旋紧螺母时使用扳手的六角螺母:当螺纹直径=10mm,螺距=1.5mm,手柄长度=120mm,作用力=45N 时,夹紧力=3550N。为了保证装夹的稳固和加工时的刚性,需要在夹具后部设置支承机构,将安装工件的螺杆顶住,如图 3所示。 支撑机构中除顶尖外,还有尾架、端盖、螺杆、锁紧旋钮、手轮、手柄等。 通过手轮、手柄使螺杆旋转,推动顶尖向左移动, 从而将花键主轴上的螺杆部分顶住,再拧紧锁紧旋钮,防止顶尖松动。 尾架和端盖在这个机构中起支撑作用。
2.3 分度装置的设计
分度装置是能够实现角向或直线均分的装置。 工件被夹紧,完成一个工位的加工后,夹具不松开,工件通过移动一段距离或者转动一个角度,达到下个加工工位,从而完成整个工件的加工。 由零件的设计要求可知,槽的分度精度要求并不高,因此采用圆柱销定位分度结构,该结构简单、易制造。 操纵机构选用手拉式,如图 4 所示。 通过转动手柄,根据手柄转动的圈数来确定加工的工件旋转角度。 旋转一定角度后,将定位销通过手柄上的孔插入到分度盘上的槽中,实现分度的锁紧。
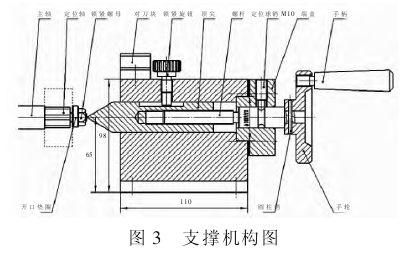
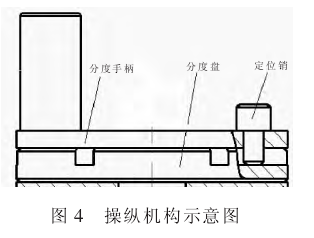
分度的传动机构是通过蜗轮蜗杆传动来实现的,其特点是传动平稳、啮合冲击小,能获得较大的传动比,且结构紧凑。 蜗杆是齿数 z1=1 的单头蜗杆,蜗轮的齿数 z2=30,即蜗杆转动一圈,蜗轮转动 1/30 圈。 应工件加工要求,每加工一个槽工件转动 30°,即蜗轮转动1/12 圈。 由此可计算出蜗杆所需转动的圈数为 2.5 圈,即转动分度手柄时,每次转动两圈半即可。 蜗轮蜗杆传动机构及分度盘如图 5、图 6 所示。
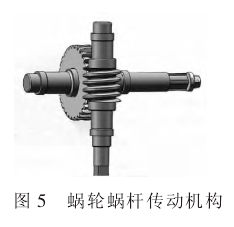
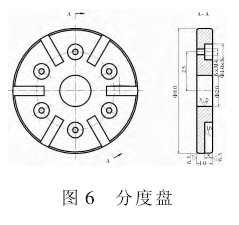
(1)定位键。 铣床夹具以定位键和机床工作台 T型槽配合,每个夹具一般设置两个定位键,起夹具在机床上的定向作用,并用埋头螺钉把定位键固定在夹具体的键槽中。 材料选用 45 钢。(2)带 U 型槽的耳座。 在铣床夹具纵向两端底边上,设计带 U 型槽的耳座,机床上有对应的螺孔,螺栓穿过 T 型槽与机床上的螺孔,将夹具体紧固在工作台上。 材料选用 HT300。
2.5 夹具体的设计
夹具体一般是夹具上最大最复杂的基础元件,其形状和尺寸主要取决于组成该夹具的各种元件、机构和装置。 同时,在进行夹具设计时,还应考虑到因夹紧力、切削力而产生的冲击和振动,保证夹的强度和刚度需求。 另外,在铣槽的过程中,会有一些碎屑掉到夹具体里面, 时间长了会损害传动机构或其它零件,为保证夹具正常工作,应考虑到排屑的方便性,且夹具应该便于装卸。本夹具体采用铸造结构, 铸造的生产周期长,且因铸造时的内应力缘故,易引起变形,从而影响夹具体精度的持久性。 为此,铸造夹具体必须进行时效处理,而与焊接结构相比,铸造可以铸出形状复杂的结构, 故本夹具体采用铸造结构比较合适。 材料选用HT200,壁厚 4mm。3 结语本文分析了被加工工件的特点、作用、材料、生产规模及技术要求,并通过相关计算设计了一套专用的带分度装置的铣床夹具。实际上,在生产中,零件的状是千差万别的,没有任何一种夹具能适用于所有的零件,合理、灵活的设计并使用夹具能够降低生产成本,提高工作效率,降低废品率。
投稿箱:
如果您有机床行业、企业相关新闻稿件发表,或进行资讯合作,欢迎联系本网编辑部, 邮箱:skjcsc@vip.sina.com
如果您有机床行业、企业相关新闻稿件发表,或进行资讯合作,欢迎联系本网编辑部, 邮箱:skjcsc@vip.sina.com