WMEM|整体叶盘先进制造技术应用与发展
2019-5-10 来源:转载 作者:-
摘要:国外航空发动机研制应用了大量高端装备及制造技术。本文以国外整体叶盘发展为切入点,介绍了航空发动机部分先进制造技术的应用现状及发展方向。
整体叶盘是航空发动机的重要转动部件,在离心力、气动力等多变载荷下工作。为提升气动性能以及保证服役周期,国外整体叶盘带有弯掠特征的复杂叶片构型,采用钛合金、高温合金等难加工材料,形位精度及尺寸公差严,加工表面完整性要求高,材料去除量大。国外整体叶盘加工采用了高精度、高效率、高可靠性的先进制造技术。
一、数控加工技术
国外航空领域不断采用高端装备和高新技术来解决整体叶盘复杂叶型高效能加工难题,采用了从加工工艺到工艺装备的整体解决方案。新材料、新工艺不断推动着整体叶盘制造技术的进步。
1.铣削与自动抛光技术
高精度尺寸及形位公差要求,大扭转、长薄壁的空间曲面叶片构型,钛合金、高温合金等难切削的工件材料,要求整体叶盘叶型铣削技术具有高效、精密、安全、低成本等特点。通用五坐标加工中心已不能完全满足整体叶盘质量、效率与成本方面的综合需求。由于整体叶盘在航空发动机上的广泛应用,促使整体叶盘新型专用数控机床、刀具系统、工艺装备与相应编程软件、加工工艺的综合进步。
整体叶盘叶型加工工艺应以提升铣削精度和加工表面质量为要点,保证叶片几何精度与物理性能。整体叶盘叶片薄长,气流通道空间狭窄,叶型截面曲率在前后缘区域变化剧烈。叶型铣削加工方案注重增强叶片实时加工刚性,减小叶片加工变形,控制刀轴矢量变化,维持切削力基本平稳。国外整体叶盘加工主要采用型腔填充减振材料以及粗精混合加工方案,采用高性能、长耐用度刀具刀柄系统(见图1),有效增强铣削过程中的叶片刚性,对保证前后缘形状与叶片轮廓度起到重要作用。
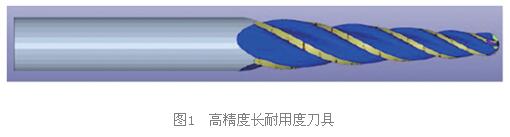
国外加工整体叶盘的五轴联动加工中心向高速度、高精度、智能化方向发展,具有如下特点:
(1)高动态性能。部分线性轴采用直线电机驱动,线性轴加速度可达0.8g以上,转动轴采用力矩电机直接驱动,提高转动轴加速性能和重复定位精度,保证多轴联动精度,提升加工表面质量。
(2)高主轴转速。加工中心配备高速铣电主轴(见图2),可以在低转速时以高扭矩、大切深的方式进行粗加工,在高转速时以大进给、小切深的方式进行精加工。高速铣电主轴采用油气润滑及油雾润滑等润滑方式。
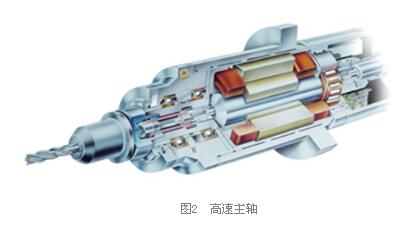
(3)智能监测功能强。加工中心具有在线测量分析、切削振动监测、刀具寿命监控、主轴断电回退、主轴温度补偿、碰撞监控急停、故障自诊断与智能报警等功能,有效提高整体叶盘加工可靠性与安全性。
(4)驱动参数优化与机床误差修正准确快捷。深度开发机床数控系统,方便进行人机交互,结合叶盘加工特点,可进行RTCP精度检测、坐标轴运动特性分析与伺服系统驱动参数调整。不同叶盘零件重量差异较大;同一叶盘从叶片毛坯状态加工至叶片最终成型状态,重量不断变化。可对承载零件的转动轴驱动参数进行优化,提高动态响应性能,使各轴动态响应特性达到最佳匹配状态,降低机床路径跟随误差。整体叶盘叶型铣削对环境温度恒定性要求高,在加工中心长时间加工运转以及环境温度变化较大时,可采用球杆仪等工具准确分析和补偿机床各轴运动误差,保证对刀数据准确性,提高叶身及流道加工精度。
加工环境温度变化、机床冷热状态转变、不同规格刀具加工,这些因素使叶片部位难以避免地产生接刀痕、局部铣削缺陷。此外,整体叶盘加工表面质量要求较高,在前后缘一定距离内不允许出现横向加工痕迹;叶身型面表面粗糙度等级高,叶身型面、流道面与叶根圆角需要光顺圆滑转接。在整体叶盘叶型铣削后,通过柔性机器人或多轴联动磨抛机床,采用砂带、砂轮、抛光轮等磨具对整体叶盘叶片及流道进行自动化抛光。
国外整体叶盘全型面、多要素自动化数控磨抛技术,处于不断发展和完善之中。自动化抛光设备在磨抛介质选型、磨抛参数选择、加工精度控制、运动路径规划等方面有待进一步研究。对于大扭转、长悬伸、窄间距的整体叶盘,叶片前后缘、叶根圆角与流道面一直是自动化抛光的难点,在叶盆、叶背等开敞性好、曲率变化小的区域可基本实现自动化抛光。现阶段主要通过优化铣削策略,控制表面粗糙度与接刀痕大小,再采用自动化抛光设备去除接刀痕迹或局部铣削缺陷,降低表面粗糙度值,保证叶片型面尺寸,防止过抛、欠抛,尤其避免前后缘出现削边、平头、尖边等问题。整体叶盘自动化抛光技术将向柔性随形加工、自适应局部抛修、磨抛与检测一体化方向发展。
2.程序分析与优化技术
整体叶盘铣削加工属于强时变工况。在加工曲面光顺性差、切削力非线性剧烈变化、加工参数匹配性欠佳等条件下,叶身型面容易出现振纹、凹坑等问题,铣削过程容易存在主轴功率过大、刀具异常振动等现象。在叶盘正式加工前,需要反复迭代试验,试验周期长,调试难度大。整体叶盘加工可利用专业软件与仪器来优化数控铣削程序,缩短加工周期,提高加工表面质量。
基于均衡切削力、均衡主轴功率的原则,整体叶盘叶型铣削程序可通过Production Module切削工艺分析软件、OMATIVE自适应控制系统等工具进行优化(见图3)。通过综合分析机床、刀具、工件与程序,优化整体叶盘叶型铣削程序中的切削参数数据,降低切削力峰值,平衡主轴负载,提高加工效率,延长刀具寿命,保证加工过程平稳,使数控机床工作在最佳的加工状态。在整体叶盘叶型精铣时应适当避免进给速度的频繁变化,保持加工表面质量的一致性。
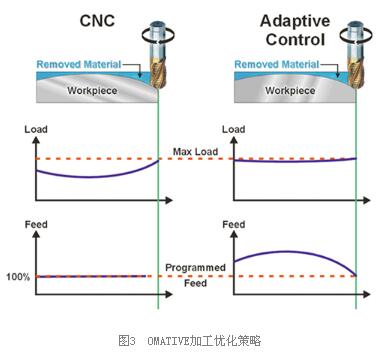
整体叶盘叶型高速铣削加工时,机床几何轴运动速度及方向不断改变,刀轴矢量快速变化,引起叶片加工表面出现条状纹理、颤纹等问题。国外部分叶盘加工专用软件可对机床运动状态进行测试记录,识别各运动轴换向点,计算各运动轴速度、加速度以及加加速度,分析叶型铣削加工是否超出机床运动性能极限,进而优化叶型铣削程序。按整体叶盘加工状态,在机床主轴上装载特定刀具并空运行铣削程序,CUTPRO切削动力学分析软件可分析叶型铣削颤振稳定域,通过调整主轴转速与进给速度,提高刀具悬伸、主轴转速与切削力匹配度,预防刀具振动,提高加工表面质量。
3.自适应加工技术
自适应加工技术能够自动适应零件形状进行加工,在国外摩擦焊叶盘精密成形铣削及整体叶盘修复领域具有广泛应用。
线性摩擦焊技术适用于加工大扭转、长悬伸整体叶盘,可以节省毛坯材料,缩短铣削加工周期。采用线性摩擦焊技术将多个叶片焊接到轮毂的轮缘位置后(见图4),需要将焊接工艺台等多余材料去除。焊接式叶盘所用叶片实际形状不尽一致,受焊接精度限制各叶片在焊接后位置不尽一致,需要采用自适应加工技术针对各叶片进行个性化精密数控铣削。

整体叶盘采用叶片与盘体一体化结构,并出现了多级整体叶盘焊接结构、叶盘与轴颈焊接结构等更加复杂的整体式结构,制造成本更高,加工周期更长。
叶片局部区域受到外物损伤或疲劳断裂后,需要采用补片焊接与自适应精密铣削加工等方法进行修复。在精密铣削时必须基于叶片实际状态进行自适应加工。
自适应加工技术需要采用数字化测量技术,检测整体叶盘待加工叶片的实际形状和位置,基于检测数据与理论模型构建自适应加工工艺模型,确定铣削基准,计算刀具轨迹,保证加工后相关部位尽量接近理论设计模型并光顺接平。国外在该领域已有较成熟的自适应加工软件与制造工艺。
德国BCT公司的自适应加工技术、瑞士斯达拉格集团TTL公司自适应加工编程软件已分别应用于MTU公司、罗罗公司的整体叶盘自适应加工。自适应加工工艺模型构建方法、自适应铣削策略设计是整体叶盘自适应加工技术研究与工程化应用的重点。
二、叶片测量技术
整体叶盘的加工质量对飞机发动机的气动性能以及服役周期影响甚大,需要对叶片部位的型面和形位精度进行高精度、高效率的检测评价。整体叶盘叶片采用三元流设计,叶片前后缘逐步采用高阶抛物线形,前后缘尺寸薄小且曲率变化大,叶身型面为复杂的空间自由曲面,叶片间气流通道窄小,而整体叶盘叶片数量及检测项目众多。整体叶盘检测需要具有高精度、高效率以及高可靠性。
整体叶盘检测包括测量路径规划、数据采集、模型配准、数据处理与误差评定等基本过程。国外整体叶盘检测目前主要采用接触式坐标测量技术,并逐步采用非接触式扫描测量技术。在整体叶盘接触式测量中,通常采用两种方案:
(1)采用配置精密转台的高精度三坐标测量机实现四轴联动,进行点接触式测量。
(2)采用配置多轴测座及高精度接触式扫描测头进行测量。雷尼绍公司的五轴测座和无级变速测头系统在坐标测量机上能实现高精度、超高速扫描测量(见图5)。
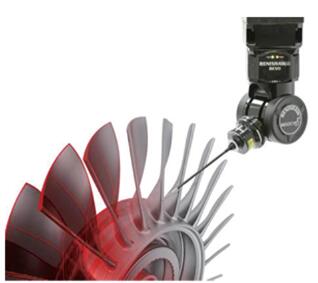
整体叶盘非接触测量技术主要采用光学扫描测头,测量速度快、采样频率高,避免接触式扫描引入的余弦误差。国外高端检测设备厂家的光学三维测量系统能高效高精度地完成整体叶盘非接触式检测,提供完整的误差分析和评价结果。目前,相比非接触式测量技术,接触式三坐标测量技术具有更高的可靠性和测量精度。
整体叶盘主要检测和评定叶片上若干等高截面的加工情况,后续将向整体型面误差评定以及加工误差可视化方向发展。为分析加工误差及改进加工质量,保证空气动力学性能,专业测量软件将注重分析统计功能开发,将已有检测数据录入专用数据库,方便查询和分析各检测项目的误差分布规律。
三、表面强化技术
作为航空发动机压气机单元体中的转动部件,整体叶盘在高温、高压和高转速的工况下运转,容易出现疲劳断裂。大量疲劳破坏故障表明,多数疲劳断裂始于零件表层,加工表面质量成为影响整体叶盘疲劳强度的重要因素。采用抗疲劳表面强化技术,提高加工表面完整性,增强整体叶盘疲劳强度,对保证整机使用性能以及服役寿命具有重要意义。
国外整体叶盘通常采用磨粒流加工、振动光饰、喷丸强化、激光喷丸等加工技术,提高叶片部位加工表面完整性。磨粒流加工与振动光饰通过减小加工刀痕深度及锐度,降低应力集中程度,提高表面粗糙度等级,来改善加工表层状态。喷丸强化、激光喷丸通过在加工表层产生塑形变形,引入残余压应力,细化晶粒组织,提高位错密度,抑制或延缓疲劳裂纹的萌生及扩展,增强整体叶盘疲劳抗力。国外整体叶盘表面强化技术主要在提高表面强化能力、叶片强化加工变形控制与补偿等方面开展研究。
四、结语
先进制造技术是航空发动机研制的重要支撑。作为航空发动机的重要转动部件,整体叶盘加工始终追求高质、高效、低成本目标。在制造技术日新月异、航空产品不断升级的大背景下,整体叶盘加工技术将不断提升。
来源:《世界制造技术与装备市场(WMEM)》杂志 杨万辉 徐新发 杨金发 中国航发沈阳黎明航空发动机有限责任公司
投稿箱:
如果您有机床行业、企业相关新闻稿件发表,或进行资讯合作,欢迎联系本网编辑部, 邮箱:skjcsc@vip.sina.com
如果您有机床行业、企业相关新闻稿件发表,或进行资讯合作,欢迎联系本网编辑部, 邮箱:skjcsc@vip.sina.com