摇杆零件的数控铣削工艺分析及其夹具设计
2023-10-27 来源: 东莞市机电工程学校 作者:邹萍
摘要:随着数控铣床加工工艺的发展,轴类零件的加工越来越普遍。根据整体式摇杆的结构特点,分析其存在的主要加工难点,主要包括薄壁部分零件的加工工艺及尺寸精度控制问题、轴的装夹及定位问题以及轴在加工过程中因振动引起的尺寸偏差问题。通过合理设计加工工艺,可以解决薄壁零件的尺寸精度问题。通过
设计专用夹具,能够解决摇杆的装夹及定位问题。通过误差补偿控制,可在一定程度上修正细长轴因振动引起的尺寸偏差问题。
关键词:摇杆零件;数控铣床;专用夹具
轴类零件在铣床加工中的一个主要难点就是装夹问题。为了提高定位精度,可以采用 V 形块进行定位,并通过压板压紧来限定所有的自由度。另外,V 形块具有较大的接触面积,降低了轮轴单位面积表面的压
力,减小了因夹紧而产生的变形 。
1、摇杆零件图纸结构分析
1.1 摇杆零件图纸
某工厂需要加工小批量的摇杆,零件材料为铝。摇杆零件图,如图 1 所示。由于数量有限,使用模具生产成本较高,采用机械加工的方式。在加工过程中,如何合理设计加工工艺,在保证尺寸精度的同时提高生产效率,是需要着重分析和解决的问题。
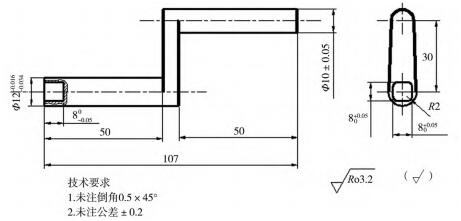
图 1 摇杆零件图(单位 :mm)
1.2 加工难点分析
由图 1 可知,零件主要由两个偏心轴和一根连接杆组成。轴 Φ12-0016(上角)-0.034(下角)mm和轴 Φ10 mm±0.05 mm 的高度均为 50 mm,都属于细长轴。加工过程需要合理设置加工工艺,同时考虑轴的定位问题及轴在加工过程中因振动引起的尺寸偏差。采用数控铣床通用夹具台虎钳较难装夹,装夹过程很难保证轴向的转动和偏移,因此正面装夹时配合使用 V 形块,反面装夹时考虑设计专用夹具。在一端的细长轴加工完进行反面装夹时,如何保证装夹稳固、定位精度高,是设计过程中尤其需要注意的问题。另外,8 mm×8 mm×8 mm方形槽的边缘厚度接近 2 mm,属于薄壁加工。薄壁零件的共同特点是受力形式复杂、刚度低,加工时极易引起误差变形或工件颤振,降低加工精度。因此,在加工过程中需要选择合理的装夹方式及铣削工艺,以保证零件的加工精度。
2、摇杆零件夹具设计方案
2.1 首次装夹的夹具设计
工件在铣床上的装夹方式有很多。在数控铣床加工过程中,如果原材料为块料,可以直接使用虎钳进行装夹。如果原材料为棒料,那么普通的虎钳无法对其进行合理的定位及夹紧,通常需要使用 V 形虎钳。但 V 形虎钳造价较高,在数控铣床加工中的使用效率低,一般不选用。因此,在装夹铝棒毛坯时,需设计专用夹具。采用合理的工装夹具设计并调整工艺,可一次装夹多个工件,从而减少换刀次数 。
根据工件的形状和尺寸要求,此工件毛坯选用Φ45 mm×110 mm 的铝棒料。先铣削轴 Φ12-0016(上角)-0.034(下角)mm和连接杆一端,为了加工的稳定性,一次只能装夹一件毛坯。装夹时,将铣床的机用平口钳和 V 形块进行组合装夹,工件正面装夹如图 2 所示。完成后的零件如图 3 所示。
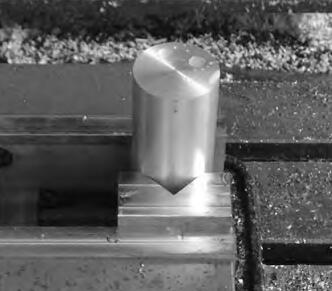
图 2 工件正面装夹
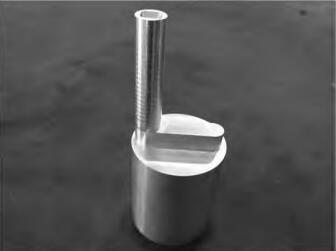
图 3 正面铣削产品
2.2 二次装夹的夹具设计
反面铣削的装夹问题是一大难题,由于 Φ12-0016(上角)-0.034(下角)mm是细长轴,很难采用 V 形块进行装夹,考虑设计专用夹具。为了保证夹具在加工过程中能够夹紧工件,考虑拆除平口钳上的固定钳口和活动钳口板。首先在铝板上的相应位置钻阶梯孔,其次用螺钉将铝板锁紧在平口钳的固定钳口和活动钳口上,再次将铝板铣削成夹具,最后将工件反面装夹在铝板夹具中。工件的反面装夹示意图如图 4 所示,夹具设计如图 5 所示。
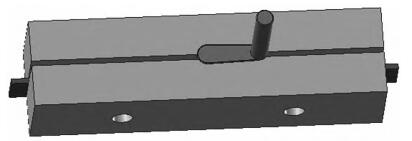
图 4 反面装夹示意图
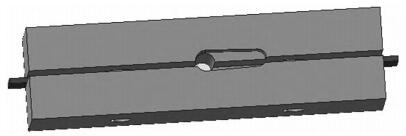
图 5 夹具设计
3、工件加工工艺分析
3.1 工件的变形控制
铝合金在加工过程中容易出现变形,且引起变形的因素较多。机床方面的影响主要有定位精度和刚度,其中定位精度的影响最大。另外,刀具对铝合金材料加工变形的影响也非常大,刀具的刃数参数、材质以及刚性直接影响铝合金材料的加工效果 。由于铝合金质地较软且刚性较差,在装夹时应尽量使夹具和工件大面积接触。同时,切削加工铝合金时要尽量利用高速加工的原理,保持高转速、少切、快跑。考虑铝合金的特性,夹紧力不宜过大,在工件开粗时应尽量选择较小的切削参数。由于轴 Φ12-0016(上角)-0.034(下角)长度为 50 mm,属于细长杆,直径较小的铣刀可能刀柄长度达不到要求,选用 Φ20 mm 的铣刀进行开粗。它的转速为 1500r·min-1(上角),进给为 500 mm ·min-1(上角),背吃刀量为 2 mm。在加工轴 Φ12-0016(上角)-0.034(下角) mm 和轴 Φ10 mm±0.05 mm时,为了更好地做好误差控制,粗加工时单边余量留0.3 mm。粗加工后,测量工件的尺寸误差,将误差计入工件的尺寸中进行半精加工,余量留 0.1 mm。测量后,调整参数进行精加工。摇杆正面铣削时, Φ12-0016(上角)-0.034(下角)mm 内部有一个 8 mm×8 mm×8 mm 的方形孔。在工艺安排上应尽量先加工方形槽,再加工外圆柱。如果先加工圆柱再加工方形孔,在加工方形孔时由于壁厚较小,由振动和切削热变形所带来的变形量过大,可能会导致圆柱和正方形的中心同轴度误差过大。在铣削时,首先选用 Φ4 mm 的铝用合金刀具,采取沿轮廓下刀的方式,每层 0.2 mm进行粗加工。其次,选用 Φ3 mm 铝用合金刀具,采用区域方式精加工底面,以达到深度尺寸要求。最后,选用 Φ3 mm 铝用合金刀具,采用轮廓精加工的方式加工轮廓,直至达到尺寸精度要求。
另外,为了减少温度对加工变形产生的影响,在整个切削过程中一定要打开切削液,最大限度带走加工热量,控制变形,防止铝料被融化。
3.2 工件加工工序安排
根据数控加工工序的安排原则,粗加工时尽量去除大部分材料。半精加工前测量工件尺寸,计算机床误差,并将其加入工件的尺寸余量中。精加工前再次测量工件的尺寸误差并进行调整,以获得精确的尺寸和光洁的表面 [5]。具体加工工序如下。
(1)用机用平口钳和 V 形块组合装夹 Φ45 mm×110 mm 的铝棒毛坯,用 Φ20 mm 的铣刀铣削毛坯上表面。
(2)用 Φ4 mm 的铣刀粗铣中间 8 mm×8 mm×8 mm带半径2 mm圆角的方槽。粗加工转速为4 500 r·min-1,进给为 800 mm·min-1(上角),背吃刀量为 0.2 mm。底部及侧壁单边留余量 0.15 mm。
(3)采用数显游标卡尺测量方形槽尺寸余量,并与之前所留余量 0.15 mm 相比,根据机床误差调整余量参数。用 Φ3 mm 的铣刀精铣中间 8 mm×8 mm×8 mm带半径 2 mm 圆角的方槽底部及侧壁。精加工转速为6000 r · min-1(上角),进给为 400 mm · min-1(上角),背吃刀量 1 mm。
(4)用 Φ20 mm 的铣刀铣削对轴 Φ12-0016(上角)-0.034 mm (下角)进行粗加工,转速为 1500 r·min-1(上角),进给为 500 mm·min-1(上角),背吃刀量为 2 mm。底部及侧壁单边留余量 0.3 mm。
(5)测量轴 Φ12-0016(上角)-0.034 mm (下角)的尺寸,将工件因振动引起的变形及机床误差计入程序参数中。用 Φ20 mm的铣刀铣削对轴 Φ12-0016(上角)-0.034 mm (下角)进行半精加工,转速为1700 r·min-1(上角),进给为 400 mm·min-1(上角),背吃刀量为10 mm。底部及侧壁单边留余量 0.1 mm。
(6)测量轴 Φ12-0016(上角)-0.034 mm (下角)的尺寸余量进行精加工,转速为 2 500 r · min-1(上角),进给为 400 mm · min-1(上角)。 用Φ20 mm 的铣刀铣削中间连接杆,按照粗加工、半精
加工和精加工 3 个步骤进行铣削。
(7)用 45°倒角刀对工件进行倒角,转速为4 500 r · min-1(上角),进给为 300 mm · min-1(上角)。
(8)将工件反面装夹在铝板专用夹具中,并使用平口钳夹紧。
(9)用Φ20 mm的铣刀铣削对轴Φ10 mm±0.05 mm进行粗加工,转速为 1 500 r·min-1(上角),进给为 500 mm·min-1(上角),背吃刀量为 2 mm。底部及侧壁单边留余量 0.3 mm。
(10)测量轴 Φ10 mm±0.05 mm 的位置及尺寸偏差,并计入程序参数中。用Φ20 mm的铣刀铣削对该轴进行半精加工,转速为 1 700 r · min-1(上角),进给为 400 mm · min-1(上角),背吃刀量为 10 mm。底部及侧壁单边留余量 0.1 mm。
(11)测量轴 Φ10 mm±0.05 mm 的尺寸余量,进行精加工,转速为 2 500 r · min-1(上角),进给为 400 mm · min-1(上角)。
(12)用倒角刀对工件进行倒角。
4、结语
通过分析摇杆的结构特点,确定了正、反面加工的装夹方案,合理设计了加工时的专用夹具。对摇杆零件中的薄壁结构进行合理的工艺设计,保证零件薄壁部分的尺寸精度。通过工艺设计在一定程度上补偿了工件的变形误差,保证了零件的形位公差和粗糙度要求。
投稿箱:
如果您有机床行业、企业相关新闻稿件发表,或进行资讯合作,欢迎联系本网编辑部, 邮箱:skjcsc@vip.sina.com
如果您有机床行业、企业相关新闻稿件发表,或进行资讯合作,欢迎联系本网编辑部, 邮箱:skjcsc@vip.sina.com