一种小型叉形接头的精密加工技术
2017-12-26 来源:天津航天长征火箭制造 北华航天工业学院 作者:葛佳 崔鑫 谢成雨 范大伟 杨昊
摘 要:针对小型叉形接头结构尺寸较小,在加工过程中存在小直径深孔难加工、形位公差难保证、微小结构难装夹等难题,通过设计一套集定位、装夹、钻模为一体的组合钻模,改进钻头结构,既实现了产品可靠装夹,又保证了产品加工精度,加工效率大大提升。
关键词: 深孔加工 小孔加工 装夹定位 组合钻模
随着航空航天技术的发展, 越来越多的精密零件趋于小型化,零件常采用微孔、深孔等结构,微孔、深孔的精密加工是机械加工领域的难点之一。
笔者通过研究小型叉形接头的精密加工工艺,设计了一套集定位、装夹、钻模为一体的组合钻模,解决了叉形接头小直径深孔加工的难题,为同类型小型工件的加工装夹、小直径深孔加工提供了加工经验。
1 、加工现状
1.1 产品结构分析
叉形接头结构如图 1 所示。
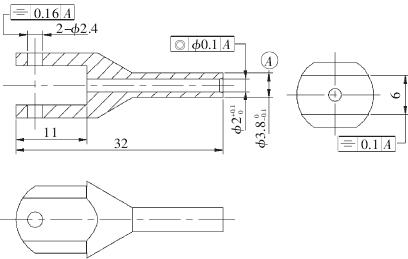
图 1 叉形接头产品结构
可看出叉形接头属于小直径深孔零件, 孔径 2 mm, 深 21 mm, 长径比达10.5。由于外圆直径为 3.8 mm,壁厚不足 1 mm,属于薄壁零件。 此外, 要求内孔相对外圆的同轴度为 准0.1mm,2-准2.4 孔 相对外圆轴心线对称度为 0.16 mm,叉形槽相对外圆轴心线对称度为 0.1 mm。零件材料为 45号钢。
1.2 加工存在的问题
1.2.1 装夹困难
叉形接头在加工 准2.4 mm 孔和叉形槽时, 需以准3.8 mm 外圆轴心线为基准来保证对称度公差要求 。但是叉形接头结构尺寸小,无有效夹持点,小端壁厚不足 1 mm,刚性差,容易造成装夹变形,加工装夹困难。
1.2.2 孔径小
机械加工中将孔径小于 3 mm 的孔称为小孔。 叉形接头钻 准2 mm 孔时由于麻花钻钻芯厚度小,强度不够,螺旋槽窄,不易排屑,钻头易折断[1]。
为了保证有效的切削速度,钻孔时采用较高的转速,切削产生的温度很高,加剧了钻头的磨损。 另外,由于麻花钻钻芯厚度小,刚性差,容易弯曲导致钻头倾斜,产品报废。
1.2.3 深孔
机械加工中将长径比大于 5 的孔称为深孔, 叉形接头的长径比为 10.5,在钻孔过程中,由于钻头细长,刚性差,冷却困难,排屑不畅,切削热不易散出[4]。
综合上述加工问题, 为了保证叉形接头 准2.4 mm孔和叉形槽对称度精度,需以 准3.8 mm 外圆轴心线为基准装夹。 因此装夹要求定位准确,装夹可靠,同时要提高叉形接头的结构强度,避免装夹变形。
另外应提高钻孔所用细长钻头的刚性,改善排屑情况。
2 、加工方案
2.1 装夹方案
叉形接头加工装夹时主要考虑以 准3.8 mm 外为装夹基准,提高产品结构刚性,避免装夹变形。
笔者设计了一套集定位、装夹、钻模为一体的组合钻模,用于叉形接头加工装夹,便于钻孔,保证加工精度。先对工件进行粗加工、半精加工。在数控精密车铣复合机床(高精密微型轴类零件一次车铣加工成形)上车 准3.8 mm 外圆、大端外圆至设计尺寸,在同一次装夹中钻 准2 mm 孔,以保证同轴度要求。 由于在机床上钻孔过程不可控,加工过程排屑不畅,钻头刚性差,易发生钻偏或钻头折断,因此在机床上钻 准2 mm 孔时, 只钻 6~7 mm 深的底孔。
最后在同一次装夹中铣大端两侧平面, 以保证平面与轴心线的平行。 加工后的叉形接头半成品如图 2 所示。
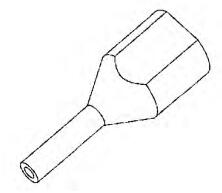
图2 叉形接头半成品工件
笔者设计的组合钻模由底座、钻模盖板、紧固螺钉组成,结构如图 3 所示。
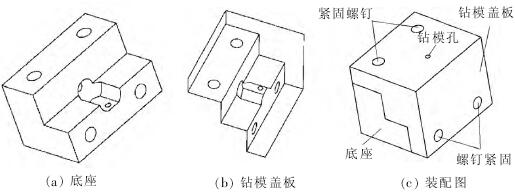
图 3 叉形接头组合钻模
底座设计有 准3.8 mm 孔,用于装夹找正叉形接头 准3.8 mm 外圆; 设计有圆弧平底槽,用于装夹找正叉形接头的扁头。钻模盖板也设计有圆弧平底槽, 用于装夹找正叉形接头的扁头; 设计有准2.4 mm 钻模孔及耐磨钻套, 用于加工叉形接头扁头平面的 准2.4 mm 孔[5]。将叉形接头半成品工件装夹在底座中, 以 准3.8mm 孔定位并找正叉形接头准3.8 mm 外 圆柱面 , 以圆弧平底槽限制叉形接头扁头的旋转自由度。 将钻模盖板安装在底座上, 使钻模盖板圆弧平底槽与叉形接头扁头紧密接触,钻模盖板后板顶住叉形接头端面,如图4 所示,最后用螺钉将底座和钻模盖板连接紧固。
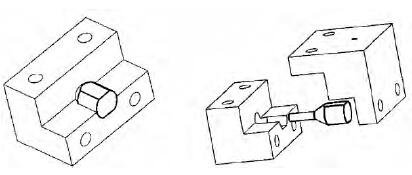
图 4 组合钻模装夹原理
由于叉形接头各面与底座、钻模盖板紧密接触,其装夹状态稳定可靠。
2.2 钻孔方案
用螺钉将底座和钻模盖板连接紧固后, 叉形接头工件在组合钻模内得到完全约束。 用虎钳装夹组合钻模的侧面,找正 准2.4 mm 钻模孔后,以钻套作为导向,在摇臂钻床上钻 准2.4 mm 孔。 钻孔过程中需不断退出钻头,便于切屑的排出。 退出钻头的同时及时添加切削液,降低钻头及切削区域的温度[6]。
在加工叉形接头小端 准2 mm 孔时,同样使用该组合钻模装夹。用虎钳装夹组合钻模侧面, 找正工件上已加工的 准2mm 底 孔 ,以 准2 mm 底 孔为导向 ,在摇臂钻床上钻 准2 mm 孔,如图 5 所示。
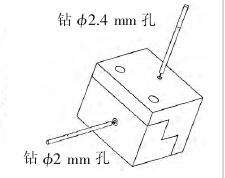
图 5 叉形接头钻孔过程
钻孔过程中为排出切屑, 需不断退出钻头排屑。退出钻头的同时及时添加切削液,降低钻头及切削区域的温度。纵向进给时要注意手劲及感觉,钻头弹跳时,应使它有一个缓范围,以防钻头折断。钻小直径孔时常采用整体式扁钻。由于扁钻无螺旋槽, 除刀头切削部分外,刀体为整体圆柱。 与麻花钻相比,整体式扁钻结构刚性好,钻孔时钻头弯曲较小,另外整体式扁钻的钻尖对称性较好。但是整体式扁钻无螺旋槽,负前角大,导致钻削时切削力大,切屑难排出,切削液难进入切削区域进行降温, 因此整体式扁钻不适于加长径比大的微小孔[7]。 麻花钻具有螺旋槽及正前角,切屑易排出,切削液易进入切削区域进行降温。
但是小直径麻花钻由于钻芯厚度小,钻头刚性差,钻孔时钻头易发生弯曲。为提高麻花钻刚性,选用钻芯厚度大、切削刃对称的钻头。 但是随着钻芯厚度的增大,钻头横刃加长,钻孔时走刀抗力增大。在使用前应修磨麻花钻,缩短横刃长度,加大后角,增大钻头顶角,使横刃产生的切屑变少且变长[8]。
另外需在麻花钻两个主切削刃的后刀面磨出分屑槽, 通过分屑减小切屑形成过程的塑性变形和切屑卷曲程度,减小切屑与钻头、孔壁的摩擦,便于切屑的顺利排出[9]。
上述加工完成后,在叉形接头 准2 mm 孔中插入芯轴,在数控精密车铣复合机床上装夹 准3.8 mm 外圆并找正,以 准3.8 mm 外圆轴心线为基准铣叉形槽。 最后铣叉形接头扁头 R6 mm 圆头,完成叉形接头成品零件加工。
2.3 加工效果
组合钻模的使用, 使叉形接头在加工中装夹稳定可靠, 各自由度完全约束。 装夹以叉形接头 准3.8 mm外圆柱面作为装夹基准,与设计基准重合,保证了加工后 准2.4 mm 孔的对称度和 准2 mm 孔的同轴度。
装夹中叉形接头与组合钻模各面紧密贴合,装配精度高,增强了叉形接头的产品刚性, 避免了其在加工过程中产生的装夹变形,使加工更加简单易行。通过改进钻头刃磨,完善钻孔工艺,使钻孔过程更加稳定,钻头刚性得到提升,排屑顺畅,钻头使用寿命得到有效延长。采用上述加工技术后,叉形接头各结构尺寸、形位公差满足使用要求,产品合格率达 100%。
3 、总结
笔者通过设计一套组合钻模,改进钻头结构,实现了小型叉形接头的可靠装夹, 解决了叉形接头小直径深孔的加工难题,改善了小直径深孔钻削的排屑效果,保证了产品的形位公差,取得了预期的加工效果,为同类型小型工件加工装夹、 小直径深孔加工提供了加工经验。
如果在小直径深孔加工中结合振动钻削技术、内排屑钻头、喷吸钻、枪钻[10]等先进技术,加工效果将得到进一步提升。
投稿箱:
如果您有机床行业、企业相关新闻稿件发表,或进行资讯合作,欢迎联系本网编辑部, 邮箱:skjcsc@vip.sina.com
如果您有机床行业、企业相关新闻稿件发表,或进行资讯合作,欢迎联系本网编辑部, 邮箱:skjcsc@vip.sina.com