枪钻深孔加工颤振稳定性及振动加工技术综述
2019-2-18 来源:江西洪都航空工业 南京航空航天大学 作者: 汪洋华 李亮 龙韬 何俊杰 马晓波 等
摘 要: 深孔枪钻加工中的颤振问题,严重地影响了产品的加工质量和机床的效率。以钛合金小直径深孔的枪钻加工为研究对象,从实验研究、理论分析、颤振预测、振动加工等几个方面,对目前小直径深孔枪钻加工技术进行分析,为后续的枪钻深孔加工钻削稳定性与振动加工技术的基础研究提供理论依据。
关键词: 深孔加工; 枪钻; 稳定性; 颤振预测; 颤振抑制; 振动加工
0 引言
深孔加工是机械加工领域的一个重要分支。孔加工在整个机械加工中约占 25%,而深加工的总量在孔加工的比例达到了一半。深孔加工技术和应用开发过程崛起于炮管生产。20 世纪 60 年代以前,深孔加工技术主要用于生产枪管、炮管,此后随着生产格局的转变,深孔加工技术也转向能源、航空航天、冶金、汽车、化工和机床行业。
20 世纪 90 年代以后,随着我国经济建设的加速发展,极大地推动了上述行业对深孔加工技术的需求,传统的孔加工方式已不能满足生产需求。因此,采用较先进的专用刀具及特殊的深孔加工技术进行深孔加工是非常有必要的。深孔加工系统按照排屑方式可分为外排屑和内排屑两类,其中外排屑系统有枪钻、深孔扁钻和深孔麻花钻等; 内排屑系统因所用的加工系统不同,分为 BTA 深孔钻系统、喷吸钻系统和 DF 深孔钻系统等 3 种。
对于内排屑加工系统主要适用场合在直径>Φ18 mm 的深孔加工; 而外排屑加工系统中深孔扁钻和深孔麻花钻由于加工深度的制约,无法完成对于长径比>50 的超长小直径深孔的加工。通常长径比 L/D>10 的超长小直径深孔( Φ2 ~Φ20 mm) 均采用深孔枪钻加工工艺。目前航空航天、军事和民用产业中,超长小直径深孔加工的需求越来越多。例如: 在航天航空业中各类飞机舱门中导轨孔以及模具行业中大型汽车覆盖件的注塑模具水道孔。
所以本文提出针对超长小直径深孔枪钻钻削问题的研究,也正是符合国家航空航天、能源和汽车等行业发展的需求。
1 、深孔枪钻加工工艺
深孔枪钻加工工艺有以下的特点:
1) 是小直径深孔加工范畴最有效的刀具,且长径比越大,优越性越显著;2) 生产效率高(转速高,进给量较大,且是连续进给,不需要中途退刀排屑) ;3) 孔径尺寸较稳定( 钻和铰一次完成) ,孔径变化范围较小;4) 被加工孔表面较为光滑,标准钢材表面粗糙度可达 Ra3.2~ Ra1.6,铸铁表面粗糙度可达 Ra0.8;5) 具备高的形位公差,孔圆度 < 0. 005 mm,轴线平行度<0.2 mm/1 000 mm;6) 适应范围广,被加工材料硬度>HRC45,仍可加工;7) 孔钻通后,孔口无飞边、毛刺。
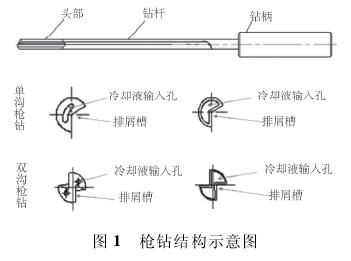
深孔枪钻结构如图 1 所示。分为枪头、钻杆和钻柄 3部分。有单沟枪钻和双沟枪钻 2 种类型。钻尖形状如图2 所示,钻尖结构复杂,几何参数较多。
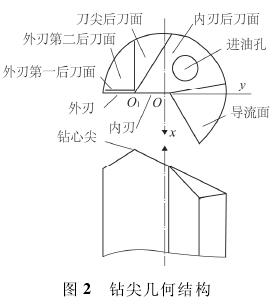
深孔加工中,由于加工过程属于封闭式或半封闭式切削,所以在切削加工过程中存在切屑的断屑、排屑、切削液的流动、钻削刀具选择和工件的散热以及刀具的导向等问题,这些问题会导致零件加工表面质量恶化。
难加工材料( 钛合金等) 的超长小直径深孔的加工,因其孔径小,孔深长,加工过程中的影响因素更加复杂,所以加工尤为困难。在小直径深孔枪钻加工过程中,由于被加工孔较深,且枪钻钻杆又细又长极易诱发钻削的颤振现象。颤振一直是影响枪钻加工质量和机床切削效率的关键问题之一。深孔钻削产生的颤振不仅会恶化零件的加工表面质量,降低机床和刀具的使用寿命,严重时会使钻削加工无法进行。
其形成的原因包括切屑无法顺利的排出产生的颤振、钻杆加工时悬伸量过长导致刚性不足产生的颤振、钻削过程中切削液与工件之间的流固场耦合作用力产生的颤振、钻削刀具崩刃或堵屑产生的颤振、加工参数选择不当引起的颤振等等。因此迫切需要揭示深孔枪钻加工过程中颤振的产生本质,拓展深孔钻削颤振的基础理论,创新深孔钻削颤振抑制方法。
2 、深孔加工颤振稳定性分析研究
通过资料的检索,现有研究主要是建立相应的钻削颤振模型,通过解析法或数值方法来求解,推导出钻削稳定性 lobe 图,并结合稳定性 lobe 图来分析钻削系统稳定性,进而为颤振控制提供理论依据。
小直径深孔枪钻过程中,随着钻孔深度的增加,钻杆的悬伸长度不断增加,是一个典型时变系统。此外,钻头除了切削刃部分与工件接触,导向部分也与已加工的孔壁接触,使得这一时变系统的动力学问题更为复杂。
目前对于深孔加工颤振稳定性的研究主要针对的是小直径麻花钻和 BTA 钻削系统,而关于
深孔枪钻系统颤振稳定性的研究较少。Mehrabadi 和 Nouri 等人提出了一个考虑弯曲振动的模型。
通过该模型可以预测出 BTA 深孔加工过程中的颤振稳定域,利用欧拉数值法模拟出钻头的运动轨迹。结合稳定域图形,可以分析出钻头在不同的转速下加工出的的孔形状和精度的差别。Arvajeh 和 Ismail提出了一个BTA 钻削颤振的动力学模型。
该模型综合研究了由于弯曲产生的横向振动和由于扭转产生的轴向振动,并考虑了回转效应。Weinert 等用统计方法更全面地解释了加工参数和表面粗糙度的关系,他指出 BTA 钻杆的大长径比和较低的弯曲刚度使钻杆容易发生颤振现象。Messaoud等指出深孔加工中出现的颤振现象也是导致直线度降低的原因之一,并用非线性连续建模的方法对加工过程的动态变 化 建 立 了 一 个 实 时 的 模 型。Chin提 出 了BTA 深孔加工切屑状态监测的数学模型,在此基础上对刀具断屑、排屑状态与切屑液流体动态压力变化的联系进行了研究,并提出了一套新的关于切屑状态监测的仿真计算方法。Bayly将理论分析与实验结果相比较,对钻杆系统的扭转振动进行了分析,详细地考察了刀具颤振频率的分布范围以及稳定性判据,指出深孔加工过程中钻杆系统存在明显的非线性特征。
国内一些高等院校和科研机构也在深孔加工颤振方面做了研究。张秋丽根据二元直角切削模型,提出了三元切削模型,推导出枪钻的钻削力数学模型。白万民等人以枪钻为研究对象,分析了深孔钻削时刀具的受力状况,给出了深孔钻的力学模型和求解方程,提出了一种测量和计算相结合的方法来求解钻削力分量。哈尔滨工业大学提出了利用多个特征参数综合监测钻削过程,通过大量实验,观察刀具在破损、折断等异常情况下,各个特征参数的变化规律,并设定闭值,对钻削加工过程进行监测。
西安理工大学李言、孔令飞等设计了一种将周期值作为参数一起参与打靶迭代的算法,通过优化确定迭代过程中的增量值。针对单孔和槽孔两种孔结构形式,将非线性切削液流体力及其 Jacobian 矩阵联合求解法与改进的打靶法及 Floquet 论相结合,研究了 BTA 深孔加工系统中中钻杆系统非线性动态行为。唐英等利用小直径麻花钻进行微小孔高速钻削实验研究表明: 钻削过程中,在一定速度范围内,随着转速的增加、轴向力和转矩下降,说明摩擦型颤振的发生条件。
高本河等分析了深孔加工孔轴线的偏斜机理,提出了利用静止外力进行纠偏的理论和方法,并确定出合适的纠偏位置。试验证明该方法具有良好的纠偏能力,为深孔钻削孔轴线偏斜的纠正提供了理论和实践依据。国内外现有针对深孔钻削颤振的理论研究,主要还是以线性理论为主,虽然能成功揭示和预测发生颤振的临界条件,但无法揭示切削颤振增长的过程与规律以及探求抑制颤振振幅的途径与措施,并且研究方法主要是将物理模型转化为时滞微分方程,然后通过半解析法或数值方法来求解,并结合稳定性图表来分析系统稳定性,从而指导钻削颤振控制; 并且研究的重点主要集中在小直径麻花钻和BTA 深孔钻削系统,对于枪钻颤振的系统研究较少。
且对于一些难加工材料如钛合金等,钻削参数调整范围远小于铝合金等易切材料零件,稳定性 lobe 图的应用价值并不显著,难以用来指导工程实际。深孔枪钻加工中颤振产生的主要动力学根源是由于系统阻尼或者系统刚度出现负值,现有的颤振判断难以区别出对于这种多自由度系统中,是哪一个阻尼、或者刚度对颤振的影响较大。而深孔枪钻加工系统中阻尼可分为机床结构阻尼和由枪钻后刀面与工件表面相互干涉而产生的过程阻尼,及钻头的支撑部位和已加工孔壁的接触摩擦产生的过程阻尼。采用劳斯判据的优点在于可以把阻尼、刚度进行等效,实现阻尼归一化。较为直观判断各阻尼项和刚度项对颤振的影响,为颤振控制提供了鉴别工具。
3 、深孔加工颤振抑制方法研究
颤振研究的最终目的是抑制颤振的产生和减小颤振的影响。目前,抑制颤振的方法一般可以分为被动型控制、半主动控制、主动型控制和变参数控制。因为半主动控制颤振和变参数控制颤振在控制方法上的简便性和易操作性,一直是大多数研究者研究的重点。半主动控制主要是通过增加钻削系统刚度、阻尼或者附加动力吸振器吸收振动来抑制颤振的方法。
要是采用各类减振器。例如: Tewani 和 Sanjiv G等设计在深孔加工镗杆上面加吸振器来抑制颤振。变参数控制的实质则是通过调整切削参数( 如刀具工作角度、进给量和切削速度等) 将切削工作位置从不稳定区移到稳定区,实质就是破坏颤振产生的条件。例如: Tarng 等通过 Nyquist稳定标准分析了切削速度、宽度与颤振频率的关系图,找到在一定颤振频率下,主轴转速以及稳定切削速度与内外调制相位变化的关系,提出了利用改变主轴转速来抑制钻削中颤振的方法。
王仁德等通过频率扫描法分析再生颤振的衰减系数模型,提出了一种新的变速切削抑制振动机理,指出变速切削时系统频率和衰减系数会随转速变化而变化,变速范围增加会使系统衰减系数增加,从而实现抑振。从实际应用效果看,半主动控制和调整切削参数法均具有一定的局限性。对于深孔枪钻加工而言,加工过程是单刃多点接触,刀具后刀面与工件表面相互干涉而产生的阻尼,钻头的支撑部位和已加工孔壁的接触与摩擦,产生的摩擦阻尼,都属于过程阻尼的范畴。因此必须在颤振模型中考虑过程阻尼的影响。目前国外研究人员开始研究利用加工过程中的非线性力学行为来抑制颤振,即充分考虑过程阻尼对切削稳定性的影响,通过改变过程阻尼来实现颤振抑制。
目前对于过程阻尼的研究主要集中于车削和铣削。例如: Altinta通过一系列正交试验,识别动态切削力中的过程阻尼系数,该试验由快速伺服系统控制,使得刀具 以 预 期 频 率 和 振 幅 振 荡。Turkes E,Orak S 等人基于刀具剪切角变化以及后刀面和工件表面波纹之间干涉力的变化,建立了车削过程阻尼模型,对零阶频率法的临界切深表达式进行逆求解,识别过程阻尼率。
Huang C Y,Wang J-J. Junz 等人提出了包含切削阻尼的铣削动能模式,模式中包含剪切、犁耕两种切削机制,以及切削力大小及方向变动所产生的阻尼效应,建立线性周期性时变的铣削动能模型。Budak 和 Tunc 等人克服了试验建模的弱点,在过程阻尼建模和系数辨识方面,进行了较为细致的工作。Ahmadi 和 Ismail 等人基于小振幅假设,将过程阻尼等效为线性粘性阻尼,利用半离散法,计算铣削稳定性极限,该模型具有一定局限性,预测出的稳定性极限低于实验值。
李欣和李亮等人利用隐式龙格库塔法,计算典型钛合金材料铣削加工中干涉产生的侵入面积以及阻力,建立考虑过程阻尼效应的非线性铣削动力学模型。在现有文献中,深孔钻削稳定性分析均采用较为传统的线性模型,未考虑过程阻尼,其在低速区会产生很大误差。特别对于一些难加工材料如钛合金加工来说,为保证刀具寿命,切削速度一般较低,这时如果还采用常用的线性模型,预测的极限切深远低于实际极限切深,势必会影响加工效率。而且过程阻尼的大小和刀具几何参数息息相关,设计几何参数,利用过程阻尼来减振的文献,国内则更为缺乏。
4 、深孔加工振动钻削技术国内外研
究现状振动钻削是振动切削的一个重要分支,其与传统切削的主要区别是在钻孔过程中可以通过振动装置使钻头与工件之间产生可控的相对运动,使切削速度、进给量、切削深度按一定的规律变化,改变工件与刀具之间的时间与空间分配。
在振动钻削过程中,合理选择振动参数( 振动频率和振幅) 、进给量、主轴转速等加工工艺参数,可明显提高孔加工精度,减小出口毛刺,降低切削力和切削温度,延长钻头寿命。振动钻削技术使传统钻削加工技术有了质的飞跃。目前,国内外学者对振动钻削技术的研究主要集中振动钻削本质与机理研究、振动钻削系统装备研究、振动钻削数学模型建立三个方面,而且均取
得了很大成果。
在振动钻削本质与机理研究方面,1954 年,日本宇都宫大学的隈部淳一郎教授提出振动钻削理论,并在其著作《精密加工与振动切削( 基础与应用) 》中对振动钻削做了详细的介绍与实验研究,认为振动钻削与传统的钻削加工相比具有断屑排屑效果好、切削力小、加工精度较高、刀具寿命较长等优点。
在此基础上,隈部淳一郎教授率先提出了超声波振动钻削的“钻头刚性化效果”理论,为超声波振动钻削的钻入定位精度奠定了理论基础。随后,其又提出了脉冲能量与应力集中理论,认为在分离型振动钻削时,钻头由普通钻削时的连续切削转变成振动钻削时的脉冲式切削,特别横刃由连续挤压工件转变成脉冲式楔入工件。1973 年,前苏联鲍曼工学院的 V.N. Poduraev 通过实验研究提出了振动钻削的冲击理论,认为振动钻削时钻头横刃的冲击作用能明显改善横刃的切削条件,并运用弹塑性理论对振动钻削的动力学机理进行了分析论证。1979 年,日本学者足立胜重提出了枪钻低频振动断屑理论,该理论指出相邻切屑若存在非零的振动相位差,就会出现薄弱环节而折断,否则,无法实现断屑。1982 年,薛万夫教授对深孔枪钻振动钻削时刀刃相邻运动轨迹波形进行了理论分析和计算,得出了保证断屑的条件,进一步丰富了足立胜重的振动断屑理论。
同时,他在实验研究的基础上,进一步提出了振动钻削的动态角度理论,指出主切削刃的前角和后角在钻削过程中是动态变化的,并给出了实际动态后角 α 的计算公式和计算图。在后续的研究工作中,动态后角的提出给加工塑性金属时可以改善刀具与工件的摩擦条件提供了理论依据。1984 年开始,王立江教授和他的课题组对高频和低频振动钻削都进行了系统的研究。研究成果无疑弥补了足立胜重从运动学角度对振动钻削分析时得出的零相位差不能断屑的缺陷和不足,使振动断屑理论进一步完善化。
其次,在研究中还提出了低频振动提高钻入定位精度的新观点,即具有“钻入-偏移-退回-恢复-重新钻入”的动力学特性。这一特性的发现无疑丰富了刚性化理论,推动了振动钻削理论研究的进程。1986 年刘华明教授在自制的超声波振动钻床上进行了实验研究,结果发现振动钻削使切削力下降、表面质量和孔径精度提高,并进一步探讨了钻头耐用度与振幅之间的关系,给出了两者的关系曲线。1995 年,杨兆军博士对微小钻头低频轴向振动钻削的动力学特性进行理论与实验研究时发现,指出由于微小钻头的固有频率极高,即使在阻尼比极小的情况下,振动能量迅速衰减,恢复变直后再重新钻入,具有低频振动钻削时微小钻头的“分离衰减多次校正”的动力学特性。2000 年杨兆军教授、王立平教授提出了三区段变参数振动钻削微孔的新工艺,探讨并研究了用非线性回归求取各区段最佳振动参数的方法,验证了以三区段最佳振动参数作变参数时,可以全面降低微孔加工误差的工艺效果。2004 年东华大学的黄志荣等人通过对普通麻花钻的改进,在 JCS-018 立式加工中心,加工不锈钢 316,孔径 2 mm,孔深 20 mm,加工参数为: 主轴转速: 2 500 r/min,转速倍率: 100%,进给速度:100 mm / min,取得一定的成果,实现小直径深孔的高速钻削。2006 年,张平宽研究了在轴向振动钻削过程中,各切削参数的变化,对钻头的工作角度会产生很大影响,给出了振动钻削参数选择的理论依据。2006 年,北京航空航天大学张德远等对微孔加工难题进行了研究,釆用超声振动加工将微孔寿命提高了 10 倍以上。
在振动钻削系统装备研究方面,隈部淳一郎教授成功研制出超声波扭转和低频轴向复合振动钻孔设备,极大地增强了振动钻削的加工能力。美国学者 W.Hansen 在对低频振动钻削的研究过程中,提出了低频振动钻削的概念和方法,研制了安装在自动车床上的用凸轮控制的机械式轴向振动钻削装置并进行了实验研究,发现低频振动钻削能够减少钻头烧伤,提高钻头寿命,加快排屑过程以及提高孔的位置精度。这一研究成果为“钻头刚性化效果”理论及脉冲能量和应力集中理论提供了强有力的依据,并为振动断屑理论的提出奠定了基础。1982 年,薛万夫教授成功研发出一种安装在机床溜板上的低频振动刀架,通过采用伺服电机驱动偏心凸轮实现钻头的低频轴向振动,并对钛合金等典型难加工材料进行验证实验。
实验证明,对于难加工材料,采用低频振动钻削可有效提高刀具耐用度、降低切削力、抑制刀杆振动以及保证断屑稳定。1986年,哈工大刘华明研发用于台钻的电磁振动工作台,并深入分析钻头耐用度与振幅之间的联系。1994 年,西安石油大学王世清教授等人设计研发了机械式轴向激振装置,其振幅与频率均连续可调。1997 年,原吉林工业大学高印寒教授研制开发出能够产生复合振动永磁振动钻削装置。2007 年西安石油大学深孔加工研究所的杨立合等人基于高频振动切削原理,自行设计阶梯型复合变幅杆,研制了一套旋转超声振动钻削装置,该装置在一定固有频率的情况下达到系统谐振,满足要求。
在振动钻削数学模型建立方面,2002 年,佳木斯大学卢红影在 Merritt 等人所建立的传统切削闭环模型的基础上,考虑刀具振动对机床的结构以及切削过程的动态特性的影响,建立低频振动切削数学模型,并提出了低频振动切削可使加工系统刚性化的观点。2006 年,华东理工大学王晓威从运动学角度分析研究振动切削的内在特性,并在传统切削模型的基础上给出了振动切削的数学模型。
提出振动切削切削力较小且切削过程比传统切削更稳定的观点。2012 年,西安理工大学李言等人在自由模态综合技术的基础上构建了深孔振动钻削加工过程中钻杆在轴向振动、振动切削力以及切削液流体力综合作用下的多跨动力学有限元模型,并通过该模型研究辅助支撑的位置及加工深度对孔直线度误差的影响,获得了孔直线度变化规律,为深孔振动加工机床的精度设计以及加工误差分析提供了理论依据。
中航工业佐景涛通过分析低频超声振动切削过程中的运动学特征,构建了低频超声振动切削力学模型,认为振动切削系统具有较高的稳定性。从上述国内外研究现状可以看出,虽然学术界在钻削颤振的研究方面已经取得了大量的成果,但从过程阻尼的角度探索钻削颤振的产生本质、影响因素及其控制等方面的研究还很少,尤其是针对钛合金这种难加工材料的超长小直径深孔钻削颤振控制基础理论与方法研究还不够深入和系统,现有深孔钻削颤振理论研究仍无法为颤振主动控制技术提供统一判据和基础支撑。
并且对于振动钻削的研究,学术界主要集中在使用高频超声振动和机械式振动钻削,研究的对象主要集中在麻花钻和 BTA 喷吸钻。对于小直径深孔振动钻削主要还是采用超声振动方案,刀具的选择还是为小直径的麻花钻。而对于枪钻的振动切削研究相对较少。
5 、总结与展望
深孔加工颤振一直是机加工领域无法回避和亟待解决的关键技术难题之一。加工过程中,钻削力大小和方向都随时间周期性变化,加上枪钻系统自身具有多自由度的结构动力学特性,使深孔钻削过程的稳定性分析变得非常复杂。国内外学者在深孔加工颤振方面的研究,主要集中在颤振稳定性分析和颤振控制等方面。因此仍存在以下问题有待继续深入研究。
1) 现有研究关于建立深孔钻削颤振模型,主要是将物理模型转化为时滞微分方程,然后通过半解析法或数值方法来求解,并结合稳定性 lobe 图来分析系统稳定性,或结合 Nyquist 判据或 Liapunov 判据来进行系统稳定性分析。该方法建模复杂,求解过程繁琐,实用性不高。能否引入统一的判据如劳斯判据建立钻削颤振模型,通过阻尼归一化的原理,系统的分析枪钻各部分结构在颤振中的作用机制,实现对深孔枪钻钻削稳定性的直观快速判别。
2) 当前难加工材料如钛合金等是研究的热点 ,其单位面积切削力倍增,可选加工速度范围有限,稳定性极限大大降低且范围窄,因此需要引入考虑过程阻尼效应的非线性理论,以扩大稳定域,提高加工效率。但目前对于过程阻尼的研究,主要集中在车削方面,对于深孔枪钻钻削加工的过程阻尼效应,尚缺少完善的动力学分析模型。
3) 深孔钻削加工中过程阻尼的大小,与枪钻结构参数如刀尖的后刀面、外刃的第一后刀面、内刃、导流面等密切相关,然而现有深孔枪钻钻削颤振控制方法中,枪钻结构的优化设计,均没有系统考虑过程阻尼效应,在减振枪钻结构设计方面仍缺少完善的理论支撑,因而有必要建立基于过程阻尼效应的深孔枪钻钻削颤振主动抑制刀具的设计理论与方法。
4) 深孔振动钻削的研究主要集中在低频超声振动钻削,研究对象也以麻花钻和喷吸钻为主。对于枪钻的振动钻削研究很少,而将钻削颤振转化为振动钻削的研究目前属于空白,如何设计这种自激振动钻削装置和实现其颤振的主动控制和如何选择其加工工艺的参数满足钛合金超长小直径的深孔加工,将是本项目研究的主要创新之处。
对以上问题,本课题将系统研究基于劳斯判据的深孔枪钻钻削颤振机理分析与颤振抑制策略,建立基于过程阻尼效应的非线性深孔钻削动力学模型和稳定性极限预测,提出小直径深孔钻削颤振主动抑制的设计理论与方法; 解决面向超长小直径深孔钻削振动主动抑制的工艺新技术。并为解决钛合金等难加工材料的超长小直径深孔钻削问题提供理论方法与技术支撑,促进航空航、能源、轨道交通等国家重点发展行业产品核心零件的“控形”与“控性”加工技术的进步,丰富制造技术基础理论,推动制造技术发展,为我国占领制造学科前沿奠定基础,项目研究具有重要的理论意义和工程应用价值。
投稿箱:
如果您有机床行业、企业相关新闻稿件发表,或进行资讯合作,欢迎联系本网编辑部, 邮箱:skjcsc@vip.sina.com
如果您有机床行业、企业相关新闻稿件发表,或进行资讯合作,欢迎联系本网编辑部, 邮箱:skjcsc@vip.sina.com
更多相关信息