单拐曲轴多向挤压模具的设计与优化
2019-1-17 来源: 北京机电研究所 作者:刘丽英,石一磬,徐春国,陈钰金,郑建,等
摘要: 单拐曲轴多向挤压成形较传统生产方式大大缩短了工艺流程,实现了单拐曲轴的全流线成形,且批量生产对其模具设计也提出了更高的要求,针对单拐曲轴多向挤压工艺模具的特点,从模具的服役环境出发,对多向模具结构中镶块部分进行分析和优化。根据镶块分模面的位置不同,设计了 “窄镶块”和 “宽镶块”两种类型,通过数值模拟和实验验证的方法,进行了较深入的分析和对比。研究结果表明: 采用镶块方式设计模具具有可行性, “宽镶块”模具结构具有较高强度和刚度;实验中窄镶块易出现 “折痕”缺陷,而采用宽镶块结构有效避免了该类缺陷。镶块结构有助于降低单拐曲轴模具制造成本和提高产品质量。
关键词: 单拐曲轴; 多向挤压; 镶块设计; 镶块分模面; 模具设计
单拐曲轴是动力机械中重要的传动构件,主要应用于农用机械、小型动力机械、园林机械等设备,实现动力的输出。曲轴在工作过程中受连杆传递的压力、惯性力及惯性力矩的作用,且承受交变载荷,因此,要求曲轴具有足够的刚度和疲劳强度以及良好的冲击性能。
目前,国内外单拐曲轴主要生产商仍采用 预 锻、终 锻、切 边 等 一 系 列 工 序 进 行 生产,该工艺材料利用率低,材料浪费达 30% ,综合成本较高。然而,单拐曲轴多向挤压工艺是近年来新兴的成形方法,该工艺采用楔横轧预制坯实现坯料的高效精确成形,采用弯曲工艺实现轴颈材料的转移,采用闭式双向挤压工序实现最终锻件形状的成形,该成套工艺具有易于实现自动化、产品精度高、材料利用率高等明显的技术经济优势和良好的应用前景。
1 、单拐曲轴多向挤压成形工艺
单拐曲轴可分为主轴颈、连杆颈、平衡块 3 个组成部分,如图 1 所示。
主轴颈主要用来支撑曲轴,连杆颈用来安装连杆的大头一端,是将活塞的往复运动转化为循环旋转运动,连杆颈通常被制成中空,目的是为了减轻曲拐旋转部分的质量,以减小离心力; 平衡块的作用是平衡曲轴的离心力和离心力矩。
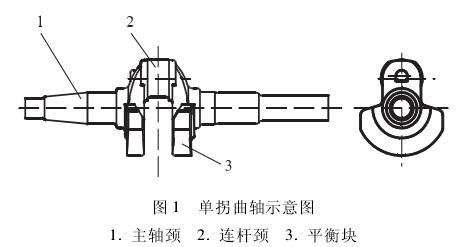
单拐曲轴多向挤压成形新工艺由下料、楔横轧制坯、压弯、闭式挤压工序组成,如图 2 所示。其中,楔横轧制坯和压弯工序主要实现材料的体积分配和转移,即楔横轧工序精确地预分配了两端平衡块所需的金属体积,并完成了主轴颈台阶轴的精确成形,压弯工序实现了平衡块部分和连杆颈相对位置的偏心特征,闭式挤压工序完成了两侧平衡块部分的最终成形以及主轴颈和连杆颈部分的精整,整个工艺只有楔横轧料头的材料损失,材料利用率高达 90% 以上。
整个锻造成形过程由高刚度楔横轧机和多向模锻液压机两台设备完成,楔横轧机的进料、轧制、出料等自动完成,该工艺的生产线易于实现全自动生产
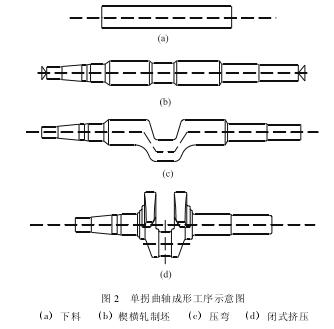
2 、单拐曲轴多向挤压模具设计
根据产品特点,单拐曲轴多向挤压模具主要采用上下分模,方便锻件的放入和取出,以平衡块形状为基础,通过左右冲头的双向挤压成形两侧的平衡块,从而实现单拐曲轴锻件的少无飞边成形。
如图 3 所示,采用整体式上下模具的方式,该方式有效地保证了该区域模具强度,但由于模具磨损不可避免,需更换整体上下模具。连杆颈和左右平衡块部分金属流动较为复杂,是模具磨损和热应力产生的重要区域,也是模具设计的关键部分。
考虑到经济性,将平衡块内侧部分采用镶块结构代,如图 4 所示。当磨损严重时,只需更换镶块部分模具,从而降低模具成本。
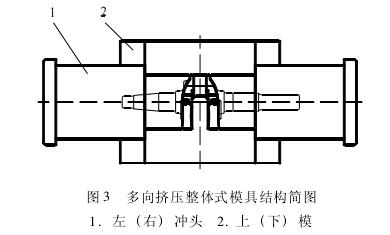
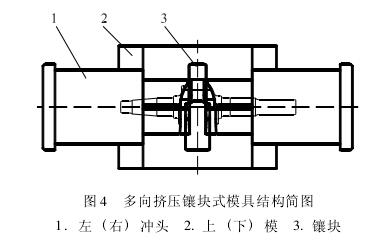
从单拐曲轴锻件的形状可以看出,该零件的左右部分 ( 包括平衡块) 是非对称的,连杆颈和平衡块沿轴线也是非对称的,而从上下合模方向来看,是对称的。因此,设计镶块结构需兼顾考虑通用和防错装。
上下对称部分设计为对称结构,在连杆颈和平衡块的非对称方向上,连杆颈一侧设计出一个宽度不一致的台阶形状,以实现自动防错安装,如图 5 所示。单拐曲轴多向挤压工艺的上下模具、中间的平衡块内裆和连杆颈部分形成凸块,该部位的金属流动剧烈,是整个模具最主要的受力区域,也是模具磨损的重点区域,因此,将该凸块部位设计为镶块结构,该镶块的宽度基本与左右方向的分模面重合,如图 5a 示。
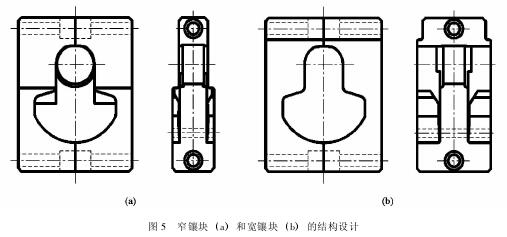
综合考虑镶块的强度和锻件的成形质量,可将镶块适当加宽,使镶块的宽度大于最终成形的单拐曲轴锻件的平衡块宽度,使平衡块的最大轮廓部分的金属充填过程完全在镶块内完成,加宽后镶块部分的刚性更好,如图 5b 所示。
前者镶块质量小,加工方便,节约较昂贵的模具材料,后者强度和刚度较好,锻件成形质量更好。
3 、镶块的有限元分析
3. 1 模拟条件
根据上述问题对模具镶块部分强度和刚度进行数值模拟分析,分别对窄镶块和宽镶块进行数值模拟,分析其强度和刚度。镶块采用 H13 模具 钢,200 ℃ 下材料弹性模量为 210 GPa,泊松比为 0. 3,屈服强度 Re L为 520 MPa,抗拉强度 Rm为 808 MPa。由于多向模锻液压机两侧缸存在一定的同步误差,故设置镶块与坯料接触面的压力为 200 k N,设置另一侧的镶块与模具接触为完全固定约束,底面限制一个方向的自由度,如图 6 所示,将其离散为三维四面体二次实体单元进行模拟。
3. 2 模拟对比结果
3. 2. 1 等效应力对比分析
窄镶块和宽镶块的等效应力云图如图 7 所示。由图 7 可知,窄镶块的最大等效应力为 765 MPa,宽镶块的最大等效应力为 507 MPa。根据应力分布区域可知,窄镶块的大部分区域尤其是成形连杆颈部位应力较大,而宽镶块因周围材料的约束而应力有所改善。因此,宽镶块强度较好,有效地改善了应力分布。
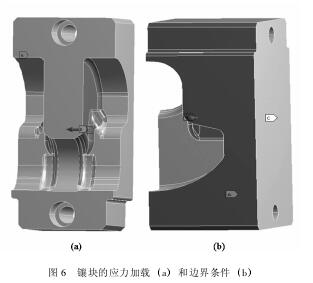
3. 2. 2 镶块刚度分析
图 8 为窄镶块和宽镶块的等效应变云图。由图8 可知,两者应变分布区域相似,成形连杆颈处模具的等效应变值较大,窄镶块的最大等效应变值为0. 011,宽镶块的最大等效应变为 0. 0025。为考察镶块在厚度方向的变形,图 9 为镶块 X 方向 ( 即宽度方向) 位移图,窄镶块最大位移为 0. 057 mm,宽镶块最大位移为 0. 0567 mm,变形量相差甚微。
图10 为镶块受力面示意图。黑色阴影部分为镶块与坯料接触部分的投影,由窄镶块的受力可以看出,坯料在成形时,由于左右侧缸不同步,产生的位移量为 0. 057 m,会增大模具间隙,从而会在曲轴平衡块位置留下痕迹。对于宽镶块而言,由于与坯料接触部分的投影,包含在整个镶块的投影范围内,故虽然产生一定的弹性变形量,但不会在平衡块位置留下痕迹。
综上分析可知,窄镶块的刚度较差,而采用宽镶块结构有效地改善了刚度,且改善了单拐曲轴平衡块位置的成形质量。
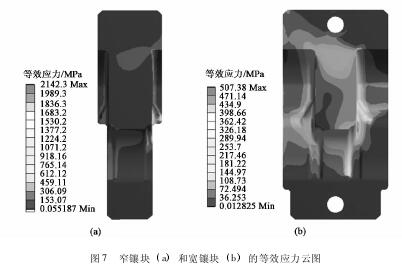
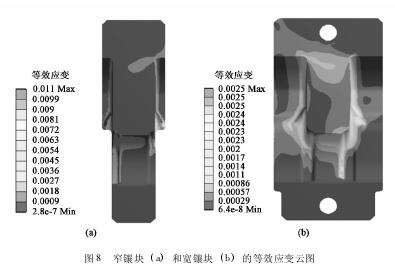

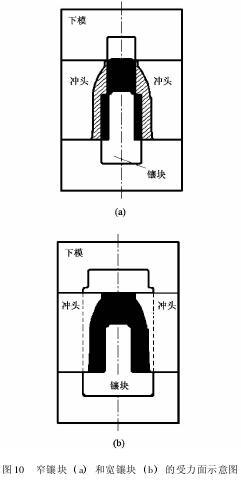
4 、实验验证结果与讨论
4. 1 实验设备与模具
单拐曲轴实验设备采用多向模锻液压机,其主缸最大成形力为 4000 k N,左右侧缸成形力为 4000 k N,分别采用窄镶块和宽镶块进行实验,实验镶块对比如图 11 所示。
4. 2 实验结果与讨论
图 12 为采用镶块结构成形出的样件。由图 12可知,样件成形质量较好,验证了采用镶块结构具有可行性,比整体式模具结构具有综合优势。
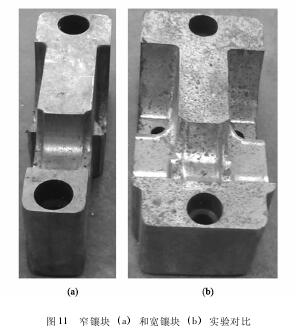
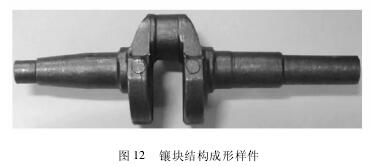
实验过程中发现,采用窄镶块成形时,锻件连杆颈边缘表面会产生 “折痕” 缺陷,如图 13a 所示。而采用宽镶块成形时,该处成形较好,如图13b 所示。根据有限元分析和实验验证可知,镶块成形杆颈位置处的变形较大,镶块压缩变形,且窄镶块在平衡块内侧为接缝位置,综合影响下,产生了较大的模具间隙,该间隙导致了 “折痕” 缺陷。而宽镶块变形较小,且其接缝位置远离平衡块一段距离,包含了整个连杆颈和平衡块部分,避免了“折痕”缺陷的产生。
5 、结论
( 1) 采用镶块结构代替整体式模具结构具有可行性,具有加工成本低、寿命高等综合优势。
( 2) 宽镶块比窄镶块具有更高的强度和刚度。
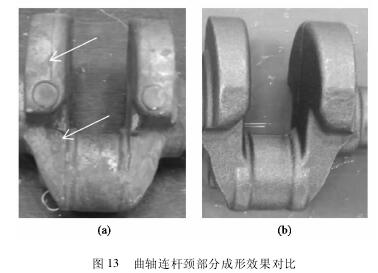
( 3) 实验中 “折痕”缺陷主要是由于窄镶块宽度方向变形较大和模具接缝间隙综合原因导致,宽镶块结构可以有效避免 “折痕”缺陷的产生。
投稿箱:
如果您有机床行业、企业相关新闻稿件发表,或进行资讯合作,欢迎联系本网编辑部, 邮箱:skjcsc@vip.sina.com
如果您有机床行业、企业相关新闻稿件发表,或进行资讯合作,欢迎联系本网编辑部, 邮箱:skjcsc@vip.sina.com