汽车发动机用连杆裂解工艺及设备的合理性探讨
2018-3-14 来源:西安交通大学机械工程学院 作者: 董渊哲,赵升吨,张超,孟德安
摘要:连杆是发动机上的重要零件,其加工工艺及设备是发动机制造业发展水平的重要标志。对比传统发动机连杆制造工艺,阐述了剖分式连杆裂解的机制及过程,根据核心加工技术的不同对近年来国内外主要裂解工艺及设备进行了研究和分类,分析了包括芯轴胀式裂解、液压活塞式、水平滑块式等机械式裂解加工设备的原理及特点,并对复合铸造裂解、热处理(或冷冻)辅助裂解和疲劳拉伸裂解等新型裂解加工方法进行了合理性探讨。
关键词:发动机连杆;裂解工艺;加工设备
0 前言
连杆是汽车发动机及其他动力机械中的重要零部件,起着连接活塞和曲轴的关键作用。近年来,我国汽车生产、尤其是轿车生产的大规模化,连杆的行业需求量也急剧增加,传统的连杆加工技术因工序复杂、加工成本高、废品率高,已难以满足日益提高的发动机产品性能要求、难以适应全球化的激烈竞争,因此,研究节材、降耗、高生产率、低成本、优质价廉的连杆加工新技术变得越来越迫切。
连杆裂解技术¨。21是20世纪90年代在汽车工业发达国家发展起来的连杆加工新工艺,通过裂解加工设备使连杆在大端处裂解为连杆体和端盖,并穿人螺栓拧紧至要求扭矩,使断裂面完全啮合,从根本上改变了连杆的传统加工方法,对连杆加工工艺产生了重大变革。
1 、传统连杆制造工艺过程
目前,传统的连杆制造工艺主要有整体式和分体式两种‘引。整体式连杆加工如图I所示,主要包括以下工艺过程:(1)连杆体和连杆盖整体锻造或铸造;(2)锯切或铣切分离连杆体和连杆盖;(3)对分离面进行机加工;(4)分别加工连杆体和连杆盖的定位螺栓孔;(5)装配。
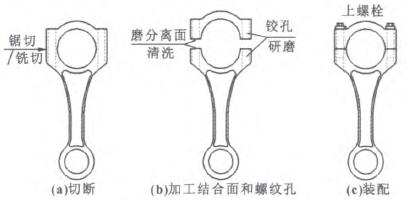
图1 传统分体式连杆加工过程
分体式连杆加工主要涉及以下工艺过程: (I)分别锻造或铸造连杆体和连杆盖;(2)机加工连杆体和连杆盖的结合面,常用铣削、拉削、磨削等方法;(3)加工大小头孔及螺栓孔、销孔等,包括粗加工及半精加工连杆体、大头孔、小头孔,精加工连杆盖的定位销孔及连杆体的螺栓孔;(4)装配连杆体与连杆盖,精加工大头孔和小头孔。
在两种工艺中,都需对连杆体和连杆盖的结合面进行铣、拉、磨等多道机加工工序,同时连杆盖的定位销孔要求较高的加工精度,导致连杆生产效率低、成本高,质量难以保证。
2、剖分式连杆裂解机制及过程
由脆性固体断裂力学H’可知,脆性合金材料在裂纹存在情况下应力集中严重,在承载远低于材料的屈服强度即可发生解理型低应力脆断,塑性变形小、断口方向与正应力垂直。剖分式连杆裂解加工即利用此原理,如图2所示,主要涉及以下过程”1:(I)在整体锻造的连杆毛坯大头孔内侧对称加工两条裂纹槽,形成初始断裂源;(2)施加垂直于预定断裂面的正应力使连杆在断裂源处脆性断裂分离成连杆体和连杆蔫:r3、将连杆体和连杆蔫精确复位。
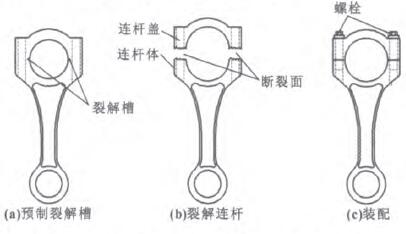
图2 部分式连杆裂解加工过程
2.1 裂解连杆材料
裂解工艺要求连杆材料具有较好的脆性,使断裂面呈现犬牙交错的解理特征哺],同时满足高强度及良好的机加工性能,目前,可用于连杆裂解的材料主要有微合金非调制碳钢、粉末冶金、球墨铸铁及可锻铸铁o¨。以C70S6材料哺1为代表的微合金非调制碳钢是目前应用最为广泛的连杆裂解材料,它具有良好的组织与力学性能,在汽车发动机连杆中得到了应用。
2.2 初始裂纹槽的预制
裂解槽的加工位置伴随着裂解加工技术的发展而不断衍化,目前常采用在连杆毛坯大头孔内侧对称加工两条裂纹槽归1,该方法具有加工工序少、连杆承载能力大的优点。裂纹槽几何尺寸主要由3个参数决定,即槽深^、张角a和曲率半径r,研究表明,尖角深槽可保证较大的应力集中系数¨0|。常用的裂解槽加工方法有机械拉削、线切割、水刀和激光加工等,其中,激光切割具有切槽窄、速度快、易裂解等优点,在一汽大众¨¨等现代车企中得到了广泛应用。
2.3 裂纹的受载扩展过程
如图3,在断裂力学中,裂纹尖端的基本受载形式有3种基本形式¨“,即I型(张开型)、Ⅱ型(滑开型)和Ⅲ型(撕开型)。其中,I型(张开型)承受与裂纹面垂直的正应力,裂纹沿y方向的解理面张开,与高脆性材料中的裂纹扩展方式最为接近,当材料的断裂韧性墨Ⅲ1达到l|缶界断裂韧度K。。时,裂纹尖端失稳扩展、直至形成整个断裂面。在几乎不发生塑性变形的情况下,在缺口处呈现犬牙交错的自然断裂,实现连杆体与连杆盖的无屑断裂剖分。
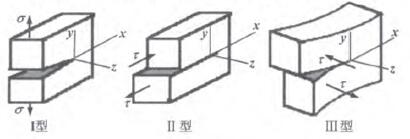
图3 裂纹尖端受载形式
3、剖分式连杆裂解加工工艺
目前剖分式连杆裂解主要采用楔形芯轴和胀套组合的机械式方法,在常温下施加准静态载荷完成裂解加工。同时,国内外学者也发展和研究了其他机械裂解加工设备,以及热处理(或冷冻)辅助裂解、复合铸造裂解和疲劳裂解等新型裂解加工方法。
3.1 机械式裂解加工设备及工艺
3.1.1 芯轴胀套式
该类型裂解设备中,在连杆大头孑L内均安置有由胀套及楔形芯轴组成的增力机构,通过液压活塞杆推动楔形芯轴进而推动胀套运动,使连杆大头孔内壁承受径向载荷而胀断。根据芯轴的插入方式不同,又可细分为“上楔人式”、“水平楔人式”、“下拉式”、“上拉式”等几类。
德国ALFING公司的“上楔入式”裂解设备¨4。如图4所示,当预制有裂解槽的连杆工件放人工作台平面后,由裂解油缸驱动楔形芯轴向下运动,通过楔形面推动裂解动套向外运动实现连杆的裂解。该设备采用准静态瞬时加载,裂解效率高,但采用“上楔入式”时,连杆在工位间的传送只能在机构下方进行,增加了工件传送的难度。该公司同时提出了一种“水平楔入式”裂解设备¨“,如图5所示,其胀块及芯轴均水平布置进行裂解,同时连杆大端底端油通过液压缸水平驱动楔块挤压支撑柱,使连杆大端在裂解过程中始终保持背压力,使大端孔圆度更高。美国福特公司采用的是“下拉式”连杆裂解加工设备¨引,如图6所示,与“上楔人式”不同的是楔形块由布置在连杆下方的油缸驱动下行。“上拉式”裂解机构结构与“下拉式”相似,裂解机构的布置方向不同,其裂解油缸布置在连杆上方,通过裂解油缸向上运动完成裂解过程。
研究表明,连杆胀断后的爆口现象是该类型工艺的主要问题。裂解槽的形状精度较低、槽深较浅、加载速度慢及芯轴、胀套的磨损等因素均易导致连杆爆口的产生。在裂解槽加工上,需要配备高精度的激光切槽机。在加载速度上,液压系统的工作压力、蓄势器参数、回路、管径、阀通径、泵流量、液压缸参数等均会影响裂解油缸的加载速度,因此对液压系统设备要求较高,有待实现加载速度的最优化控制。同时,现有的裂解方法只适合微合金非调制碳钢等脆性材料的连杆裂解,应用面有限。
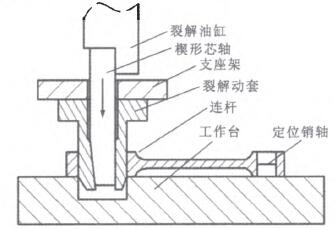
图4 “上楔入式”裂解设备
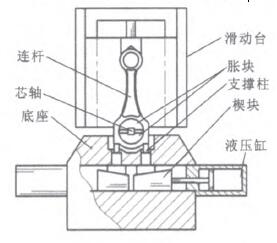
图5 “水平楔入式”裂解设备
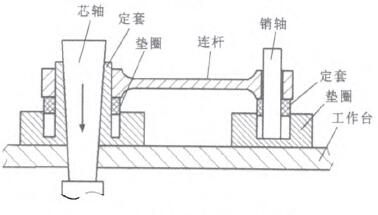
图6 “下拉式”裂解设备
3.1.2液压活塞式
该类型裂解设备取消了楔形块结构,直接将液压活塞及油路安置在了液压缸活塞设置在连杆大头孔的定套和动套之间,通过液压油缸推动活塞运动实现连杆的裂解。图7为美国MTS公司采用的“液压活塞式胀套”裂解加工设备Ⅲ。,这种裂解方式所需的裂解力小,分离面质量好,但对设备的加载速度特性要求较高,同时由于连杆大端孔径限制,导致活塞杆承压极高,对设备元件密封性要求极为严格,增加了设备成本。

图7 液压活塞式裂解设备
3.1.3水平滑块式
该类型裂解设备通过驱动滑块体,安装有裂解动套的滑块体进行驱动。图8为美国福特公司的水平力作用式裂解设备¨81,连杆大头孔内安置有裂解定套及动套,裂解定套与定块相连接,裂解动套与滑块相连接,连杆通过大端孔和小端孔定位座定位。裂解时,滑块在液压缸的驱动下向外运动,使裂解定套直接对连杆大头孔内壁加载,完成连杆盖和连杆体的分离。该种裂解方式也通过大头压块的对连杆大端保持有背压力,保证了断裂面的质量,提高产品成品率,但该机械系统要保证杆端与盖端两部分的定位及导向,机床定位系统较复杂,对于裂解设备的设计及加工要求较高。
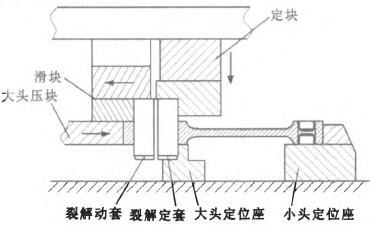
图8水平滑块式裂解设备
3.2 热处理(或冷冻)辅助裂解法
该类型裂解方法是将连杆工件的整体或局部通过一定方式加热或冷冻到一定温度后再进行裂解的新的加工技术。
3.2.1局部热处理式
局部加热加工采用激光¨9【、等离子体或高能电子束Ⅲ也¨对钢制连杆大端的分割区进行照射,并在真空中冷却,使局部由奥氏体组织变为马氏体组织,实现连杆脆断分离。使分割区域的材料由奥氏体组织变为马氏体组织,在胀断载荷作用下实现连杆脆断分离。这种工艺方法存在的最大问题是:激光或等离子体照射的区域不能有效控制,除了断裂区域外,断裂区附近部位也易发生脆化,它不仅减弱了连杆局部机械强度,而且不能有效的保证连杆在预定的分割部位断裂,裂解面易出现偏移等问题,这种工艺也不适合其他材料。
3.2.2冷冻脆化式
冷冻脆化加工方法心2瑙1提出将连杆在零下60℃到零下90℃温度下深冷5 min以上,改变材料的延展性,使连杆进入脆性状态,实现连杆的脆性断裂。对易于冷冻脆化的连杆材料,可在通过干冰加乙醇的混合冷冻方式实现零下60℃到零下80℃的冷冻,成本低;对难冷脆的连杆材料,可采用液氮实现零下190 oC的深度冷冻。但该工艺方法对整个连杆都进行了脆化,使连杆存在机械强度降低的危险;连杆脆性增加,要将其大头部分割开需要很大的断裂载荷,使断裂装置本身大型化,设备投入增加,这种工艺有待于新型连杆材料的进一步研制。
3.3复合铸造裂解法
如图9所示,该类型裂解方法主要针对铸造型钢制连杆,采用在连杆毛坯内人为设置脆性金属裂解面的工艺制造连杆,形成具有脆性界面的复合铸造连杆。按脆性金属裂解面的形成过程主要分“预制式”和“浇注式”两类。“预制式”铸造裂解法在连杆模具型腔大头孔内预先设置一层特殊金属箔材Ⅲ1或灰铸铁片旧列作为隔板,并由钢液的热量将隔板与钢液基体材料冶金结合,使其形成具有脆性界面的复合连杆铸坯。“浇注式”铸造裂解法心卅先浇铸连杆体与连杆盖,再抽离中间隔离板后浇注裂解用金属液,制成复合连杆铸坯。在实施裂解工艺时,利用界面材料的脆断性完成连杆体与连杆盖的裂解剖分。
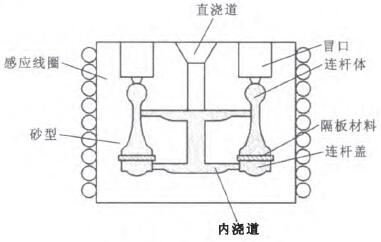
图9复合铸造裂解法
这种加工方式能有效降低裂解载荷、简化连杆加工工序,降低加工设备投资,但是存在以下问题:隔板材料强度低、易被氧化,若两侧金属液面上升不一致、充型不平稳,对隔板材料冲击大,则铸件内形成的脆性界面将偏离预定位置、或无法形成脆化界面,后续或将无法实施裂解剖分。
3.4 疲劳裂解法
该类型裂解方法利用应力集中效应和疲劳断裂原理,在加载上采用周期性疲劳载荷,对带有预制裂解槽的连杆大头端反复加载,完成连杆大端和连杆体的低应力疲劳分离"。281。如图9所示的裂解设备,连杆小端通过固定芯轴定位在工作台平面上,连杆大端内安置有固连于大端滑动座的移动芯轴,工作台平面上设置有沿连杆长度方向的导轨槽,大端滑动座通过液压缸系统实现上下循环加载,带动大端芯轴对连杆大端内壁周期加载。同时,该设备可进一步通过伺服控制实现加载力的变频调节。
与传统准静态加载方式相比,该裂解方式有效降低了能耗,即使是延性材料,断裂面也没有明显的塑性变形,使可裂解的连杆材料大为扩展,具有更广泛的应用前景,代表了绿色裂解的新的发展方向。但是目前的疲劳裂解设备在加载方式上还较为单一,主要采用直线式定向加载,难以保证大头孔的均匀受载,以伺服直驱式的周向疲劳加载将成为未来新的研究方向。
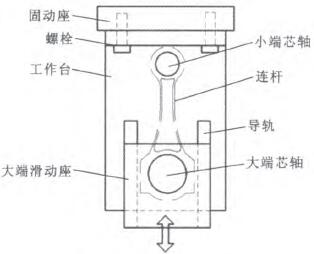
图10 疲劳裂解法
4、结论
(1)目前剖分式连杆裂解主要采用楔形芯轴和胀套组合的机械式加工方法,通过液压系统施加准静态载荷完成连杆的裂解力n-r_。虽然是较先进的一种加工方式,但只适合微合金非调制碳钢、粉末冶金、球墨铸铁等脆性材料的裂解,同时,为减少爆口问题产生,需通过高精度激光开槽技术开制高形状精度的深槽,并提高液压系统设备性能,以实现裂解加载速度的最优化控制。
(2)国外同时发展和研究了液压活塞式及水平滑块式等其他类型机械裂解加工设备,其中,液压活塞式裂解方式所需的裂解力小,分离面质量好,但对设备的加载速度特性要求较高,同时由于连杆大端孔径限制,导致活塞杆承压极高,对设备元件密封性要求极为严格;水平滑块式裂解方法通过大头压块的对连杆大端保持有背压力,保证了断裂面的质量,提高产品成品率,但该机械系统要保证杆端与盖端两部分的定位及导向,机床定位系统较复杂。
(3)随着新技术的发展,复合铸造裂解、热处理(或冷冻)辅助裂解,和疲劳裂解等新型裂解加工方法成为新的研究方向。热处理或冷冻辅助裂解通过不同工艺手段提高材料脆性以实现连杆的脆断,但易改变裂解区以外的材料性能,存在削弱连杆机械强度、裂解面易偏移等问题;复合铸造裂解能有效降低裂解载荷、简化加工工序,但充型工艺尚未成熟,易导致脆性界面偏离或失形;疲劳裂解方式改变了传统的准静态加载方式,可对延性材料进行裂解,并有效降低了能耗,具有更广泛的应用前景,但目前疲劳裂解设备加载方式较单一,主要采用直线式定向加载,难以保证大头孔均匀受载,以伺服直驱式的周向疲劳加载将成为未来新的研究方向。
投稿箱:
如果您有机床行业、企业相关新闻稿件发表,或进行资讯合作,欢迎联系本网编辑部, 邮箱:skjcsc@vip.sina.com
如果您有机床行业、企业相关新闻稿件发表,或进行资讯合作,欢迎联系本网编辑部, 邮箱:skjcsc@vip.sina.com