冷镦机床身再设计孔洞的形状优化
2017-7-21 来源:湖北理工学院 作者:何 彬
摘要:针对冷镦机床身的拓扑优化在剔除材料的同时削弱了床身的整体力学性能,提出在冷镦机床身结构拓扑优化后的再设计孔洞区域进行形状优化,即以床身多约束拓扑优化后的再设计孔洞,作为形状优化的设计变量,建立多边界的形状优化模型;描述了形状优化中的 Laplacian 光顺算法,构建了冷镦机床身再设计孔洞的形状优化过程,并在 Abaqus中分别实现了某型号冷镦机床身再设计后单一孔洞和多孔洞的形状优化,分析了不同优化结果对床身整体性能的影响,验证了所提出方法的有效性。
关键词:冷镦机;床身;孔洞;拓扑优化;形状优化
1.引言
锻压机床是机床中钢材消耗量最大的一类机床,而床身又是锻压机床中占体积和重量比重最大的一部分,对床身进行合理减重是实现锻压机床轻量化的关键[1]。冷镦机是典型的锻压机床,拓扑优化是冷镦机床身轻量化设计中最常见也是最有效的方法之一,但是由于拓扑优化过程中材料的删减不同程度削弱了冷镦机床身整体力学性能,而材料删减所形成孔洞的形状是影响应力、变形等指标的关键因素[2-3],因此,将拓扑优化和形状优化有机结合是提高床身轻量化设计质量的重要途径。提出针对冷镦机床身结构拓扑优化后的再设计孔洞进行形状优化,是在保证减轻床身重量的前提下,尽可能通过对拓扑优化后再设计区域的形状优化来改善床身的整体力学性能,从而提高床身轻量化设计的质量。
2.形状优化模型
形状优化通过使得某些物理量达到特定的边界要求,来实现设计区域几何形状的改变,以优化结构、改善相关性能[4]。形状优化所寻求的目标可以是最小化结构面积或体积、应力集中系数,也可以最大化结构的疲劳寿命等。同时,区域边界还必须要保持光滑的连续性条件,优化的形状边界须满足可制造性原则。在基于有限元分析技术的形状优化中,最大缺点是在优化迭代过程中,容易发生有限单元网格的畸变或扭曲,因此必须要满足网格的最大曲扭要求。设计变量一般以设计区域边界形状的几何参数为主,如单元网格的节点坐标等,也可选择非几何参数如虚荷载变量等[5-6]。形状优化是边界形状的不断迭代过程。优化区域形状的改变会导致应力的重新分布,一旦应力分布有利于优化函数的收敛,同时约束条件也得到满足,则会以实时的边界形状为优化变量,进行下一次迭代;若不满足约束条件或不利于优化函数的收敛,则以新的边界形状进行迭代,直到条件满足为止[6-8]。冷镦机床身形状优化是对拓扑优化后所设计的孔洞进行优化,由于孔洞的数量大于 1 且离散分布,因此可界定为多边界的形状优化问题,设待优化孔洞形成的边界数量为 n,多边界的形状优化问题可以描述为[8-10]:
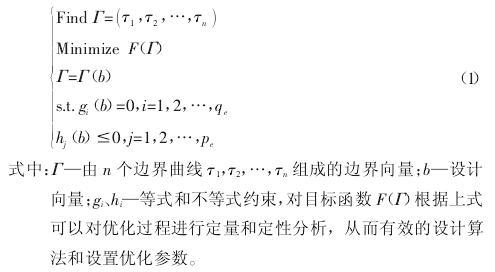
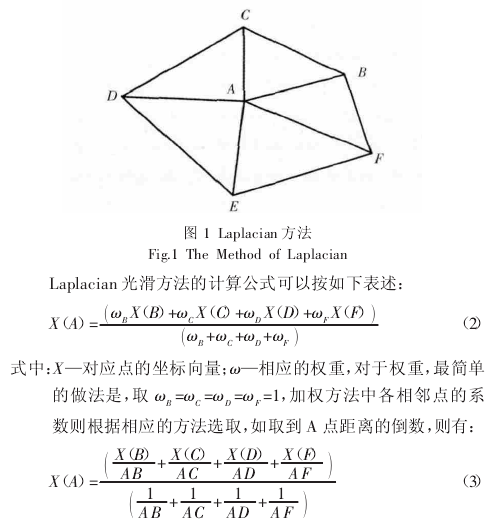
上述 Laplacian 以及各种加权方法的实现都相对简单,计算速度极快,效率高,在一般区域都只要计算数次就能获得理想的结果,但当区域内网格品质较差、网格狭长或存在小孔洞时,多会产生无效网格,因此,在很多形状优化的软件中,往往采用带约束的 Laplacian 光滑方法,主要针对网格品质引入判断量,根据网格点移动前后的品质逐一比较,仅在网格品质提高时才进行网格点的移动,否则,当品质较差时则取消移动,保持先前的网格点不动。如不能提高品质时,则将移动距离减小为原来的一半,到指定次数仍不能提高网格品质,则保持点不动;从而保证所有网格品质的提高,减少计算量,改善优化性能。
4.优化过程模型
冷镦机床身拓扑优化在于通过剔除材料而达到减重的目的,形状优化是在不改变减重效果的前提下,对拓扑优化后所设计的孔洞形状进行优化,使形状更趋于合理,从而改善床身的整体力学性能。通过拓扑和形状优化的联合作用,形成具有合理结构的孔洞。其求解的顺序可以描述为:
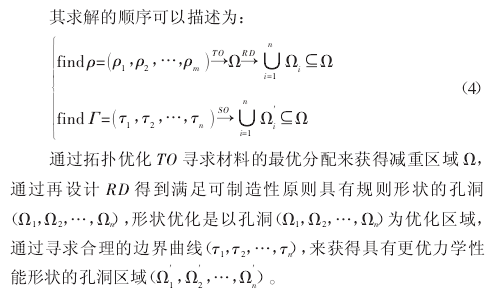
冷镦机床身形状优化的实现流程,如图 2 所示。在优化过程中,首先针对所有的再设计孔洞区域进行形状优化,也就是多边界的整体形状优化,然后再分别以单独的孔洞区域为对象进行形状优化,对两种优化方案进行分析,由于同一孔洞在整体和单独优化后形状改变的程度,决定了该区域对床身整体机械性能的影响程度,从而可以确定出关键区域,并综合床身的可制造性原则,选定最优的设计方案。
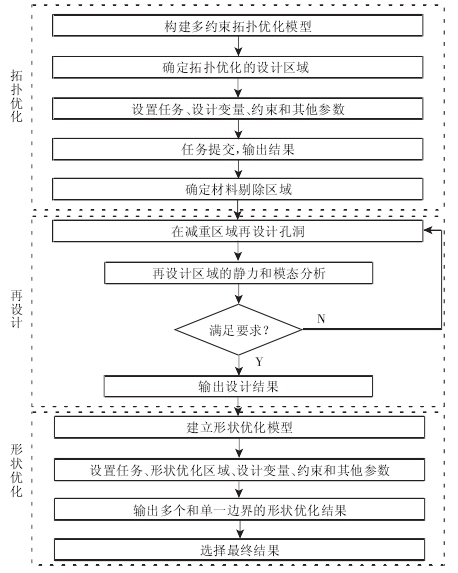
图 2 冷镦机床身结构形状优化的实现流程
5.应用实例
以某型号冷镦机床身为实例,验证所提出方法的正确性。在工作过程中,冷镦机床身主要承受镦断力的作用。该冷镦机床身的受力分析和初始设计参照文献[2],拓扑优化模型采用应变能最小为目标函数,以体积、最大应力、最大位移等为约束,经过 10 次设计循环,得到剔除孔洞后的拓扑优化结果。根据拓扑优化结果,在材料剔除区域按照可制造性原则,设计孔洞形状[2],如图 3 所示。
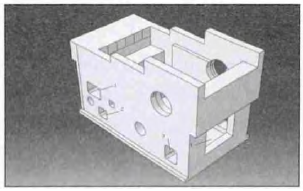
图 3 再设计结果
5.1 再设计孔洞的形状优化
形状优化是为了进一步改善床身的力学性能,在本例中,主要对再设计的孔(1~4)进行形状优化,为了分析不同再设计孔洞对床身力学性能的影响,首先设置 4 个孔洞为形状优化区域,以再设计床身的最大主应力最小化为优化目标,体积不变为约束,采用带约束 Laplacian 光顺算法,验证 4 个孔洞整体形状优化结果和收敛过程,如图 4 所示,在经过 14 次设计循环之后,整体形状优化基本上趋于收敛。从优化后的应力云图和位移云图可知,整体形状优化后,在不改变体积的前提下,床身最大应力和位移分别从由优化前的 115MPa 和 0.679mm 分别减少到 58.59MPa 和0.06098mm,床身力学性能明显得到了改善。
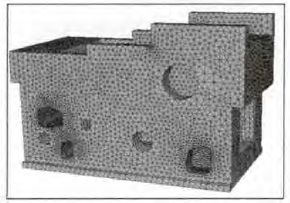
图 4 多孔洞整体形状优化结果
其次分别以孔(1~4)为形状优化区域,优化函数、体积约束和其它参数都不变,可以得到单一孔洞的形状优化结果,如图 5所示,图中 a)-d)分别表示了孔(1~4)的形状优化,与整体形状优化相比较,单一孔洞形状优化的最大应力和位移基本上没有多大改变,但是从优化后的形状看(主要从优化后孔的大小和曲线形状进行评价),孔 1 和孔 2 的形状改变较大,而孔 3 和孔 4 形状改变较小。
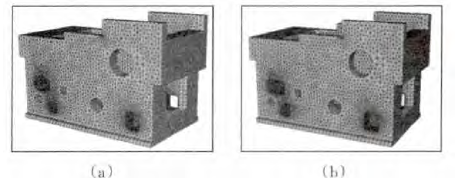
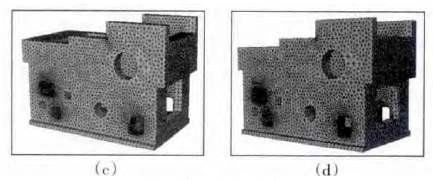
图 5 单一孔的形状优化
5.2 结果分析
从本例中冷镦机床身的形状优化结果可知,4 个孔洞整体形状优化与单一孔洞形状优化后的最大应力和位移基本不变,孔 1和孔 2 的形状改变较大,而孔 3 和孔 4 形状改变较小,说明孔 3和孔 4 的形状对床身最大应力和位移影响较大,因此如果要进一步改善拓扑优化后再设计床身的力学性能,可以着重考虑孔 3 或孔 4 的形状优化结果,而无需改变再设计床身中孔 1 和孔 2 的形状,从而简化冷镦机床身的设计过程,提高设计效率。形状优化可明显改善拓扑优化后冷镦机床身的力学性能,从而使设计更趋于合理。
6.结论
提出冷镦机床身拓扑优化后再设计孔洞的优化,是拓扑和形状优化的协同求解过程,拓扑优化用于减重,形状优化是对拓扑优化后设计区域的边界求解,结果表明,整体和单一孔洞的形状优化对床身力学性能的影响差异不大,不同位置的孔洞形状对床身最大应力和位移有不同程度影响;通过优化,不仅冷镦机床身重量减轻了,而且相比拓扑优化后的再设计床身,最大应力和位移分别也有一定程度的下降,说明将拓扑与形状优化结合起来具有必要性和有效性。
投稿箱:
如果您有机床行业、企业相关新闻稿件发表,或进行资讯合作,欢迎联系本网编辑部, 邮箱:skjcsc@vip.sina.com
如果您有机床行业、企业相关新闻稿件发表,或进行资讯合作,欢迎联系本网编辑部, 邮箱:skjcsc@vip.sina.com