关于直纹滚压加工装置的设计
2017-3-9 来源:齐齐哈尔轨道交通装备有限责任公司 作者:范俊超
摘要:介绍了一种直纹滚压加工装置的设计参数及关键技术,并阐述了其结构特点、工作原理、试验情况及相比传统工具的优势等,试验分析结果表明,该装置大大提高了效率,提升了质量,到达了设计要求。
关键词:滚压;直纹;多次成形
1. 滚压设备现状
现有的直纹加工方式分为刨床加工、插床加工和滚压设备等几种加工方式,其中刨床加工和插床加工效率很低,单件加工耗时长;传统滚压设备由固定装置、滚压装置组成,工作时将工件放入固定装置中固定好,再将滚压装置安装到位,由压力机压入,通过滚纹刀具在工件表面滚动使工件变形形成直纹。这种滚压方式存在以下几个问题:第一,由于工件外形尺寸误差,造成一批工件滚压完成后,直纹深度不一致,有深有浅。第二,当需要增加直纹深度时,将滚压装置取下后重新放入工作位置再次滚压时,由于工件表面已经存在直纹,故无法完全与滚轮上的纹路对齐,造成“双眼皮”现象。第三,滚压后的工件在首段和尾段部分,由于与滚轮初期接触阶段工件本身“支撑性”较差,产生了弯曲现象。结构示意如图1所示。
2. 新型滚压装置的结构设计
结合实际加工情况反应出的问题,新型装置应具备以下特点:①滚压深度可调整。②能够实现多次滚压,多次滚压时纹路不应改变。③通过改变工艺顺序,使工件加工完毕后直纹平整性一致。
(1)滚压过程
将工件装入后,通过旋转调整螺栓使中间楔块上下运动,进而推动两侧楔块向左右运动从而调整工件与滚轮相对位置(见图1中箭头)。调整完毕后,油压机进行滚压,滚压过程如图2所示,第一次滚压结束后,若直纹深度较浅,可用工具继续转动调整螺栓到合适位置(此时滚纹刀具位于工件薄壁位置可以很轻松转动螺栓),再将除底座外的其余装置整体翻转180°,以确保工件与滚纹刀具的相对位置不变,用以避免出现“双眼皮”现象。将装置放好后进行第二次滚压,滚压完成后,可以讲工件两端薄壁部分切除,来保证工件直纹的平整性。
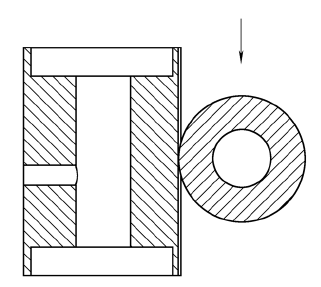
图1 现有滚压方式简要示意
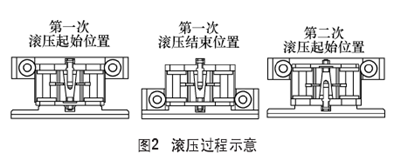
(2)设计理念
使用该装置滚压成功的关键步骤在于第二次滚压起始位置,传统方法存在的问题是第一次滚压完成时滚纹刀具和工件是分离的,再次滚压时需将工件重新装入设备,而新方法则是将其整体翻转后,在保证滚纹刀具和工件不分离的情况下再次滚压(设有限位装置),即保证了不出现“双眼皮”现象,如图3所示。
(3)滚轮材料改进
传统的滚压方式使用普通材料45钢制作滚纹刀具,由于滚压时滚轮受力比较大,滚轮经常损坏,每制作5个左右工件必须更换一次滚纹刀具,导致加工成本上升,加工效率下降。经过多次试验,最后选用Cr12Mo V作为滚轮的材料,大大延长了滚轮更换周期,每300~400个工件需要更换一次滚纹刀具。
(4)通过该装置改进工艺顺序
传统的工艺顺序,工件滚压为最后一道工序,无法避免滚压后带来的两端受力不均匀带来的变形问题,这次我们调整了加工顺序,实行滚压后再对工件两端进行切除加工的方案,可将多余的变形的部分切掉,保证了滚纹的一致性。
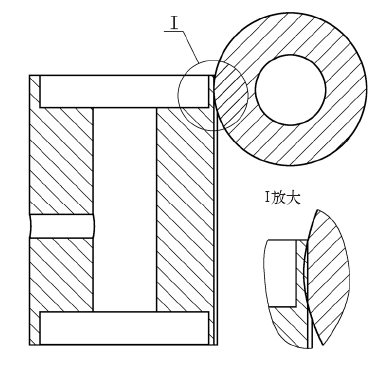
图3 第二次滚压起始位置示意
3. 应用前景
目前该装置已经在我厂大范围投入使用,各项指标均能达到加工要求。根据该装置的设计理念,可以逐步推广至其他零件的加工,以传统设计方法为基础,结合creo技术建立模型,利用UG有限元分析思想对该装置在实际工况进行受力分析,疲劳强度分析等,得出该装置重要部件在正常工况下的应力云图和应变云图,为其安全可靠提供依据。相信该方法在其他加工领域中中可以得到更加广泛的应用。
投稿箱:
如果您有机床行业、企业相关新闻稿件发表,或进行资讯合作,欢迎联系本网编辑部, 邮箱:skjcsc@vip.sina.com
如果您有机床行业、企业相关新闻稿件发表,或进行资讯合作,欢迎联系本网编辑部, 邮箱:skjcsc@vip.sina.com