高速滚珠轴承电主轴热态特性分析(下)
2018-10-16 来源: 哈尔滨工业大学深圳研究生院 广州市昊 作者:姜本刚 雷 群 杜建军
3 、电主轴热态特性的有限元分析与试验
为了便于实验验证仿真结果,以 DGZ60E. S 球轴承高速电主轴为研究对象进行 ANSYS 仿真。这款电主轴的前、后轴承均为 FAG hcs7003c 脂润滑轴承,内置电机为GZ1-060,额定功率为 1. 8 k W,效率为 10% 。
3. 1 电主轴有限元分析模型
电主轴整体上可以看作轴对称结构,选取其剖视图的 1 /2 作为热分析模型,将电机等效为圆柱筒,省略螺钉孔等细微结构。在保证相应结构精度的情况下,简化后的模型导入有限元分析软件 ANSYS,选择 PLANE55 单元,经过处理后的有限元模型如图8 所示。
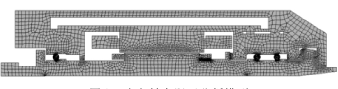
图 8 电主轴有限元分析模型
3. 2 电主轴温度场分析
所研究对象为油脂润滑轴承支承的电主轴单元,则润滑剂的散热影响可忽略。在进行电主轴单元的热仿真分析前,需要进行以下假设:( 1) 电主轴工作环境温度 Te为 25 ℃ ;( 2) 电主轴选用水冷进行冷却,冷却水的流量为 0. 5 L/min,入口水温 Ti为 20 ℃ ,出口水温 To根据实验监测确定为 40 ℃ ,则定性温度 Tf为 30 ℃ 。表 2 所示为该条件下电主轴的热边界条件。
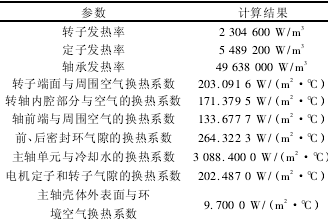
表 2 电主轴单元的热边界条件
为了研究稳定的热载荷对高速电主轴温度场的影响,需要对电主轴进行稳态热分析。在进行瞬态热分析之前一般需要先进行稳态热分析,以确定电主轴初始温度分布场或瞬态热分析最后一步的温度场分布情况。将表 2 热边界条件加载到电主轴的有限元模型,图 9 所示即为求解所得的电主轴的稳态温度分布云图。可知,电主轴稳态温度最高点出现在内置电机转子靠近定子一侧区域的中间部分,为 63. 890 4 ℃ ,同时可以通过比较计算得到电主轴整体最高温升高达38. 890 4 ℃ ,这是由于电机转子本身生热率比较大,并且电机整体处于一个封闭的空间,冷却液对其温度影响也有限,这样就形成一种生热多、散热困难的情况。前、后轴承的最高温度都出现在轴承滚珠的中心位置,其中,前轴承组的最高温度在 62. 5 ℃ 左右,后轴承的最高温度则为 62 ℃ 左右,由此可知,电主轴的轴承温升为 37 ℃ 左右。支承轴承温度较高的原因主要有 2 个: 一是电主轴高速旋转导致轴承磨损加剧,从而使得轴承发热量较高; 二是由于电机转子的发热量通过接触件的热传导作用影响到轴承的发热。
另外,可以看到,不论前、后轴承,轴承内圈的平均温度均要远高于轴承外圈,大约平均高出 30 ℃ ,这是因为轴承内圈与温度较高的主轴直接接触,而轴承外圈则是距离冷却管路更近,由于热传导的作用,产生了该现象。电机定子的发热率也是比较高,但是它的最高温度大约只有 39 ℃ ,这里,流过电主轴壳体的冷却水起到了关键作用,带走了定子产生的大部分热量。
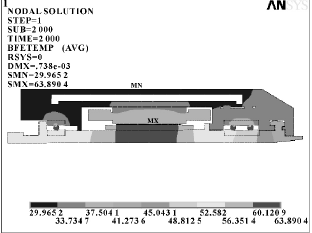
图 9 电主轴温度分布
高速电主轴瞬态热分析用于分析其温度场随时间的变化情况。瞬态热分析与稳态热分析的区别在于其载荷是随时间变化的。现假设电主轴空载运行了1 000 s,对电主轴进行瞬态热分析。在电主轴前轴承、后轴承、电机转子上分别选取温度较高的节点,相应地绘制各节随时间变化的温度曲线,如图 10 所示。

图 10 电主轴特定节点温升曲线
由图 10 可知,在 0 ~ 400 s,不论电机转子、前轴承和后轴承节点,它们的温度上升速率在整个温升过程中都为最大,其中,前轴承升温速率比后轴承大,而后轴承的温升速率又比电机转子大; 在 400 ~800 s 区间,三者的温度上升趋势逐渐趋于平缓,并持续保持转子温度高于前轴承,前轴承温度高于后轴承; 从 800 s 左右开始,三者都基本达到稳态温度,温度大小排序维持不变。基于以上现象,有如下分析: 电主轴的温度上升主要经历了急剧上升、缓慢上升和稳定 3 个阶段。在第一阶段,由于前轴承为 2 个轴承组成的轴承组,而后轴承为单一的轴承,则后轴承的发热量明显低于前轴承,因此出现了前轴承温升大于后轴承的现象。在第二、第三阶段,主要由于冷却水的持续作用,使得电主轴的温升逐渐趋于平稳,并最终达到稳定状态。通过以上分析可见,在该电主轴以60 000 r/min转速开始工作前,先让其空转 800 s左右以达到预热目的,然后再进行加工操作,从而可以大大降低由于主轴温升造成的加工误差。为了分析电主轴的热位移及热应力分布情况,需要进行热 - 结构耦合分析。本文作者采用间接法进行热 - 结构耦合分析。在前述稳态热分析的基础上,进行如下操作:
(1) 在前处理器中转换热分析单元 PLANE55 为相对应的结构单元 PLANE182。(2) 设置添加电主轴材料的物理参数。将电主轴各部件材料的弹性模量、线膨胀系数和泊松比进行设置。(3) 将上述稳态热分析的结果以温度载荷的形式加载到有限元模型。(4) 指定电主轴的参考温度为 25 ℃ 。默认在参考温度时,热应力为 0。(5) 进行求解及后处理。按照上述步骤操作完毕后,电主轴轴向位移场如图 11 所示。
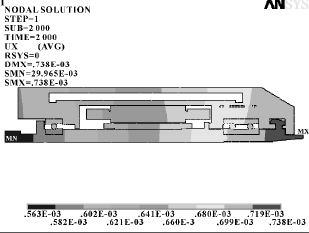
图 11 电主轴轴向位移场
由图 11 可知: 在稳态温度热载荷作用下,主轴的轴向位移量基本上是从轴的前端向后端逐渐减小,电主轴整体的轴向热位移最大点出现在主轴的最前端,为 0. 738 mm,热位移最小点出现在主轴的最末端,为 0. 563 mm,这一情况对电主轴的加工精度的影响是明显的,由此可见对电主轴适当冷却散热的重要性。另外,通过采用弹性模量较大或热膨胀系数较小的材料作为电主轴材料可以达到减小主轴轴向变形量的目的。图 12—14 示出了电主轴轴向、径向和周向的热应力分布云图。

图 12 电主轴轴向应力场
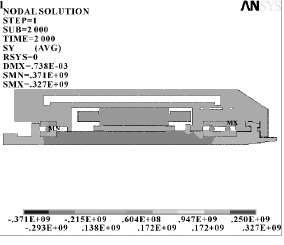
图 13 电主轴径向应力场
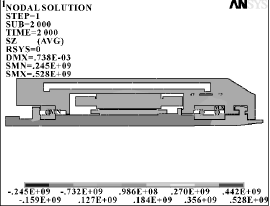
图 14 电主轴周向应力场
3. 3 实验
为了验证理论计算及仿真分析的可行性,设计温度测定实验,装置如图 15 所示。
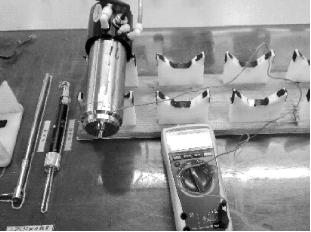
图 15 实验装置
电主轴以 60 000 r/min 转速空转 1 h 后,分别选取电主轴外壁、前端及主轴内壁靠近转子部分若干点,采用万用表和热敏电阻测量各点温度,并与仿真结果中对应各点温度进行比较,如表 3 所示。测量数据与仿真数值的偏差基本维持在 10% 以内,说明文中的理论方法是可行的。
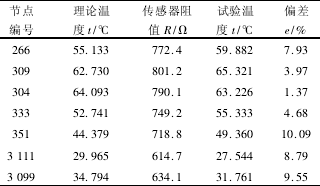
表 3 节点温度的理论值与实际值
4、 结论
(1) 采用局部热计算方法计算滚珠轴承生热功率,分析发现轴承转速及轴向受力都对轴承生热具有显著影响,且 轴 承 滚 珠 自 旋 是 轴 承 的 主 要 的 发 热形式。(2) 利用有限元分析软件 ANSYS 对电主轴模型的温度场、轴向位移场及应力场进行仿真,分析发现电主轴的最高温度出现在内置电机转子上且转轴前端的轴向位移最大,说明电主轴的热源生热对其加工精度及稳定性具有决定性的影响。(3) 通过温升 测定实验 验 证了理论方 法的可行性。
投稿箱:
如果您有机床行业、企业相关新闻稿件发表,或进行资讯合作,欢迎联系本网编辑部, 邮箱:skjcsc@vip.sina.com
如果您有机床行业、企业相关新闻稿件发表,或进行资讯合作,欢迎联系本网编辑部, 邮箱:skjcsc@vip.sina.com
更多相关信息