集成旋转涨刀油缸的开发应用
2018-1-8 来源: 广西玉柴机器股份有限公司 作者: 陈 隆
【摘要】: 旋转场合应用的油缸为了保证旋转的状态而采用的密封方式一般为间隙密封方式,间隙密封是一种最简单而应用广泛的密封方法。它依靠相对运动零件配合面间的微小间隙来防止泄漏。由于配合面存在微小间隙,所以需要达到防止泄漏,也是技术难点之一。本文从在压力场合下,利用的间隙密封技术结合聚四氟乙烯密封材料密封案例应用于精密的控制场合,开发出集成旋转涨刀油缸应用。突破了多方面的技术瓶颈,具有典型的借鉴意义。
【 关键词】: 间隙密封技术; 集成旋转涨刀油缸; 聚四氟乙烯; 热效应
1.引言
间隙密封是一种最简单而应用广泛的密封方法。其优点为,具有自润滑特性、无需密封件,不易磨损等特点。但是间隙密封难以完全消除泄漏,零件加工精度要求高,应用的场合也受到很大的限制,主要利用在液压阀组方面居多,但在一些压力较高、高端精密的场合很少推广利用间密封的技术案例。本文从生产现场珩磨设备应用的旋转涨刀油缸存在设计缺陷方面进行分析探索,结合了间隙密封技术与聚四氟乙烯密封材料在旋转压力场合进行密封的典型案例,具有推广价值。
2.原设计的旋转涨刀油缸缺陷分析
我们使用的珩磨设备为珩磨柴油机气缸体缸套底孔的精密设备。由于原设计的旋转涨刀油缸存在设计缺陷,导致珩磨加工气缸体缸套底孔时经常产生表面粗糙度、圆柱度或圆度超差,主要缺陷主要从以下几方面进行分析。
2.1 旋转涨刀油缸的分体结构分析
旋转涨刀油缸为分体结构,液压控制腔及压缩气体通道腔独立设计,如图1 所示。其内部分体旋转结构分为三层,由里向外分别是旋转芯轴、芯轴浮动轴套、旋转芯轴安装套。芯轴浮动轴套通过销钉浮动固定在芯轴安装套上,当旋转芯轴旋转时,芯轴浮动轴套可以在径向圆周上产生一定的微量移动。芯轴浮动轴套与芯轴安装套为非旋转件,旋转芯轴为旋转件。气体介质进入珩磨头的旋转与非旋转结构密封采用橡胶O 型密封件密封,密封件安装在旋转芯轴上,并作用于相对股固定且有一定微量浮动的轴套孔密封,为孔用动密封。致使O 型密封件与密封轴套均是易损件,磨损形式为接触磨损。
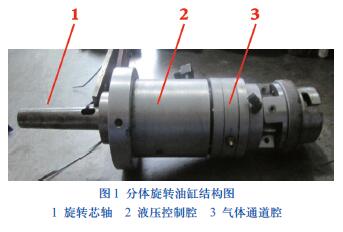
分体式结构的旋转涨刀油缸,在结构上零件数量多,各零件的配合精度要求非常高,维修过程若频繁更换密封件后,精度难以保证。另一方面较多零件的结构和浮动的转芯轴轴套,在油缸旋转传动时,振动较大,这些振动会转移到珩磨头,不仅导致珩磨机体缸孔的粗糙度下降,对体缸孔的圆柱度和圆度精度影响也非常大,经常出现缸孔锥度和椭圆而精度超差。珩磨气缸体缸孔采用的是缸孔自动导向珩磨工艺,若旋转油缸振动越大,对珩磨头的外圆精度尺寸导向性要求也非常高。在我们的生产实践中,也经常出现从厂家磨回来的珩磨头能磨得出合格产品的只有30% 左右,无形中影响了生产和增加操作者的工作量,还产生了磨削成本的过度浪费。
2.2 旋转涨刀油缸内置涨刀功能分析
原设计的旋转涨刀油缸具有涨刀功能,使用液压控制涨刀。涨刀机构设置在旋转涨刀油缸的旋转芯轴内,液压油进入旋转芯轴上的涨刀机构(涨刀活塞)也一样存在上述的旋转体与非旋转体的密封结构,也是采用丁腈橡胶O 型密封件密封,与压缩空气结构一样,密封件安装在旋转芯轴上,并作用于相对固定且有一定微量浮动的轴套孔密封,为孔用动密封,同样磨损形式为接触磨损。
2.3 旋转涨刀油缸的密封材料性能分析
原设计的旋转涨刀油缸的分体结构及涨刀功能结构中,均采用了丁腈橡胶O 型密封件密封。丁腈橡胶(NBR)O 型密封圈密封,是丁二烯和丙烯腈共聚合成橡胶。丁腈橡胶的动静摩擦系数1.5μ,摩擦系数和磨损均随载荷的增加而降低。在较低载荷时,丁腈橡肢表现为滞后摩擦; 在较高载荷时,表现为粘着摩擦。干摩擦条件下,丁腈橡胶的摩擦系数随转速的增加先减少再增加,主要磨损机理为粘着磨损; 原油润滑条件下丁腈橡胶的摩擦系数是随转速的增加先增加后减少而后又增加,主要磨损机理为湿磨粒磨损。同时原油介质的腐蚀性及溶胀作用对橡胶摩擦磨损规律具有直接影响。另外,由于工作中存在摩擦,温度影响也非常大。丁腈橡胶温度适用范围-30℃ ~100℃,工作压力< 800N/cm2 ,随着温度的升高耐压强度降低非常明显,如100℃,工作耐压< 392N/cm2。丁腈橡胶的线膨胀系数为5.7~7.9×10-4 ℃ -1,膨胀系数较大,对温度的影响相对较大。也就是说,在工作中密封件受温度升高的影响而膨胀,磨损有急剧上升的趋势。对于丁腈橡胶O 型密封圈的优点为耐油性好,但用于旋转及压力的密封场合,是避开此类密封件的优点利用,是设计上的一大失误。
2.4 旋转涨刀油缸维护维修现状及对质量影响
由于压缩空气密封通道与液压油密封通道使用O 型密封件密封,在压力旋转的交变载荷场合下,O 型密封件极易磨损。O 型密封件需要每周更换1 次,占用生产时间1.5 小时; 而相对固定且有一定浮动的轴套,6 个月更换1 次, 占用生产时间4 小时。加工缸孔的珩磨头出现精度异常,1 个月更换珩磨头1 次,更换加调整时间需要8小时左右。
由于旋转涨刀油缸存在漏油、漏气的不稳定性,珩磨气缸体缸孔时存在很大的质量隐患,操作人员珩磨气缸体每个缸孔均需要进行检测缸孔的圆柱度和圆度,不能按一定频次的抽检方式进行,大大约束了生产的正常发挥。操作人员稍有不慎,容易就出现废品,工作强度及压力极大。
3.旋转涨刀油缸设计开发方向
针对原旋转涨刀油缸的结构及密封缺陷,在开发设计中必须避开上述缺陷。主要从三方面进行开发探索,一方面拟采用集成结构方式,另一方面拟采用新型密封材料密封,第三方面为涨刀油缸采用间隙密封设计。
3.1 集成结构旋转涨刀油缸从减少零件及降振方面进行优化设计
上述分析到,原分体式结构的旋转涨刀油缸振动较大,这些振动会转移到珩磨气缸体缸孔的表面,造成表面质量粗糙度大。为了减少振动,通过从减少零件的数量来消除多零件间的装配间隙及装配误差,进一步降低由于这些误差在旋转状态下的振动,从而减少振动源的产生。优化设计的关键核心技术在于具有一定压力的液压油和压缩空气集成于一个结构控制腔中。其密封要求需要解决高压液压油和低压压缩空气不同介质的密封和压力不平衡的异类介质结构腔内的内泄漏技术难题。旋转涨刀油缸的改造关键核心技术主要是集成与减振,具体为:
3.1.1 旋转涨刀油缸的集成设计
取消芯轴浮动轴套设计,放弃原旋转油缸的三层结构,设计改进为双层结构: 旋转芯轴和旋转芯轴安装套,旋转芯轴通过两个轴承安装于旋转芯轴安转套内,如图2 所示。
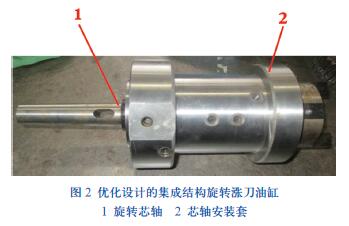
集成设计的旋转涨刀油缸工作时,只有旋转芯轴安装套支承,旋转芯轴旋转,减少了油缸旋转时的振动产生源头,防止振动通过旋转运动传递,提高旋转油缸的旋转精度。
3.1.2 旋转涨刀油缸的旋转芯轴及其安装套设计分析
由于转轴密封面的线速度较高,所以表面粗糙度对密封效果和密封件的寿命影响较大。实践经验表面,表面粗糙度Ra0.2~0.5μm 时,密封件的寿命为最佳。若转轴密封表面有螺旋形加工痕迹时,便具有螺杆泵的作用,当螺旋方向与轴的转向一致时,(从轴伸出端看),就会泄漏,转速愈高泄漏愈严重,因此要设法避免。所以设计时,我们把密封件设计安转在旋转芯轴上,如图3 所示; 把摩擦面设计在旋转芯轴安装套上,如图4 所示。而旋转芯轴安装套采用两种材料结构,实现一种零件两种材料的有效组合。安装套主体材料采用45 钢或40Cr,与密封件的密封接触面采用表面镀硬铬材料,内孔采用研磨技术研磨,达到粗糙度Ra0.4,进一步减少油缸旋转的密封件与安装套的摩擦阻力。
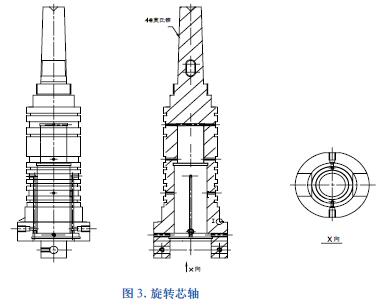
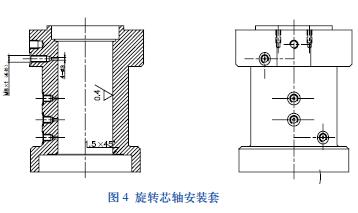
3.2 集成结构旋转涨刀油缸密封设计分析
密封的技术关键是解决主要两大方面的抽象难题: 一方面是设计旋转油缸中旋转体与非旋转体间的密封技术保障旋转油缸的密封可靠性。另一方面是旋转涨刀油缸的振动产生及传递问题,保障气缸体缸孔珩磨的精度。
3.2.1 旋转涨刀油缸的旋转密封原理
旋转涨刀油缸的密封件可安装于转轴上或非转轴的固定套上,如图2 所示,密封件安装槽设计在旋转芯轴上。密封件其密封接触部分与非旋转件间为减少磨损及发热,必须有一层薄薄的润滑油膜。如果密封接触部分与密封圆周的压力过小,则油膜太厚容易泄漏。反之,若压力过大,密封接触部分会将油液全部挤出而不能形成油膜,则工作时摩擦热增加,油封可能很快磨损及老化失效。因此,密封接触部分的密封压力要适度、均匀和持久。密封件与旋转面接触的密封接触部分不宜过宽,以免发热严重,因此标准密封件不能承受液体压力的作用。故选用聚四氟乙烯材料的格莱圈密封。
3.2.2 拟采用新型密封材料聚四氟乙烯密封分析
聚四氟乙烯(PTFE)具有优异的物理化学性能,耐腐蚀性极强,耐高低温,是一种广泛应用的高性能工程塑料。利用PTFE 的粘弹阻尼和摩擦阻尼耗能,可以在苛刻条件下的机械结构中作为减振元件应用。所以聚四氟乙烯减振性能符合使用要求。
聚四氟乙烯材料的其它性能: 其摩擦系数为0.04μ,比丁腈橡胶小将近40 倍。聚四氟乙烯材料的摩擦系数随着负荷的增加,在一定范围内,其摩擦系数将减小,通常四氟的静摩擦系数f 和负荷之间存在f=0.178(w-0.5)) 的关系。如在高速高压下,其摩擦系数可低于0.01μ,是一种非常优越的自润滑材料,而摩擦系数不随温度而变化。除此之外,聚四氟乙烯材料耐磨性高,除具有一定的吸振功能外,还具有细长纤维和节组成的膨体结构,由一定的间隙补偿功能。聚四氟乙烯材料温度适用范围广-180℃ ~260℃间,其线膨胀系数在19℃突然上升为48×10-5/℃,在30℃又是一个转折点为25×10-5/℃。膨胀系数相对丁腈橡胶也小得多,随温度的变化量如图4所示:
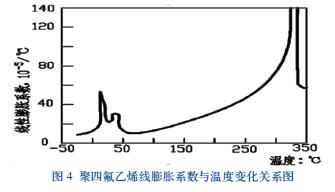
3.2.3 聚四氟乙烯密封与结合体工作状态膨胀分析
集成结构旋转涨刀油缸的旋转芯轴还是旋转芯轴安装套不管是45 钢或40Cr,其材料膨胀系数非常接近,在20~100℃时约为12×10-6/℃,而作为密封件的聚四氟乙烯线膨胀系数20~48×10-5/℃,相差10 倍。也就是说,当在同一温度下聚四氟乙烯比45 钢或40Cr 膨胀量大。所以在设计旋转芯轴安装密封件的沟槽时,应结合两种材料的膨胀特点留有有足够的轴向膨胀空间,沟槽的轴向膨胀为0.2mm。为了保证在各种状态下具有良好的密封性能,旋转芯轴与旋转芯轴安装套的配合间隙配合,间隙为0.03mm。
3.2.4 聚四氟乙烯密封线速度分析
温度过高是密封件老化的主要原因,摩擦是热的主要来源。密封表面线速度愈高发热愈严重。因为材料的耐热性不同,所以不同材料的封面件所允许的速度范围也不同,选用材料时应注意。如图5 所示,为丁晴橡胶NBR、聚丙烯橡胶ACM 和聚四氟乙烯PTFE 密封件所允许的线速度范围。从图5 可知,四氟乙烯PTFE 密封件所允许的线速度较大,耐热性好; 并且与旋转体的轴径有较大关系,旋转体的轴径越大,线速度越高。在设计中,可参考图示的线速度范围。如图所示,当密封的轴径为65mm 时,若采用聚四氟乙烯PTFE 密封件,其允许线速度为16m/s。
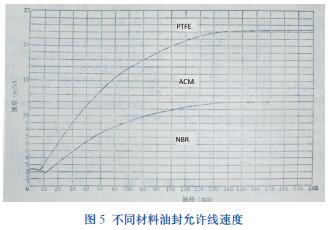
3.3 集成结构旋转涨刀油缸涨刀油缸间隙密封设计
间隙密封是一种最简单而应用广泛的密封方法。它依靠相对运动零件配合面间的微小间隙来防止泄漏。间隙密封的特点是结构简单,摩擦力小,耐用,但对零件的加工精度要求较高,且难以完全消除泄漏。在设计中为得到最佳的间隙配合,必须探讨三个技术课题: 泄漏量、热楔力及液压卡紧。
3.3.1 间隙密封原理中配合间隙与泄漏阻力关系分析
采用间隙密封时,油缸活塞与缸筒的配合间隙与哪些条件相关联,影响最大?首先,引入液体流过间隙时单位流量的压力损失公式对其原理进行分析,间隙密封原理简图如图6 所示。
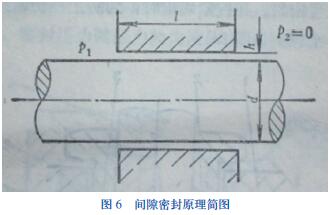
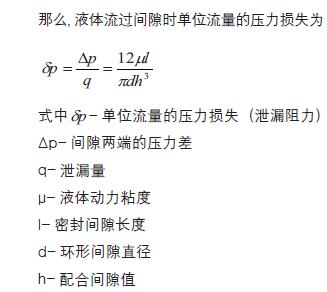
由上式中可知,泄漏阻力与配合间隙h 的三次方成反比,因此可用减小配合间隙的办法来减少泄漏,这就是要求提高配合面的加工精度。故此,为保证较高的活塞与缸筒的配合间隙精度,我们利用研磨的手段来提高配合间隙精度。
3.3.2 配合间隙内的热效应分析
在高温及高压下,油液的粘度将随温度和压力发生较大的变化,为此应考虑其影响。活塞运动时,缸筒固定,活塞移动,在密封长度L 方向上形成剪切流,如图7 所示。
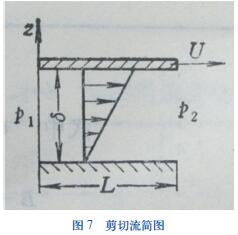
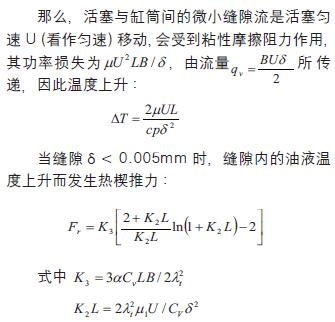
以上系数公式中,α 为油液的体积膨胀系数,为油液每单位体积的定容比热, 为油液的粘温系数,随油液不同而异(如表1 所示), 为缝隙进油口处油的动力粘度。
因此,在设计集成结构旋转涨刀油缸涨刀油缸的活塞与缸筒的配合间隙时,结合前面所述的泄漏阻力与配合间隙h 的三次方成反比的特性,应> 0.005mm 考虑,但又不宜过大。活塞组合件1 如图8 所示,活塞的基本尺寸为φ40mm,上差为-0.005mm, 下差-0.010mm; 如图9所示与活塞配合的缸筒基本尺寸为φ40mm,上差为+0.010mm, 下差+0.008mm; 公差大于0.005mm。同理,活塞组件2 与缸筒2 配合公差也大于0.005mm。

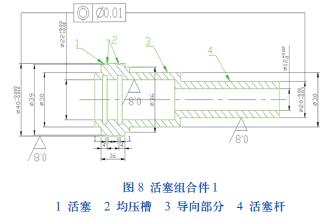
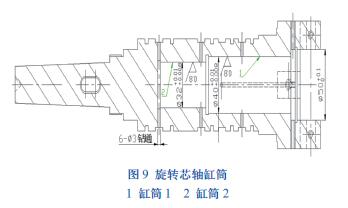
3.3.3 旋转涨刀油缸涨刀油缸的活塞与缸筒的液压卡紧分析
间隙密封结构中,当活塞与缸筒间液流的径向力不平衡,而使活塞偏心加大,最终使活塞压向缸筒的内侧壁面,出现卡紧现象,称为液压卡紧,如图10 所示。液压卡紧发生条件:
1、活塞与缸筒存在偏心。
2、活塞与缸筒间的配合间隙有锥度。
3、在锥度缝隙中,沿液体流动方向缝隙是逐渐扩大的。
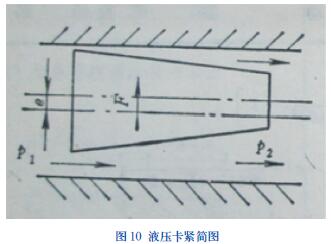
当以上三个条件同时出现时,才会出现液压卡紧,或当活塞有凸起部分时,也可能产生液压卡紧。液压卡紧力:
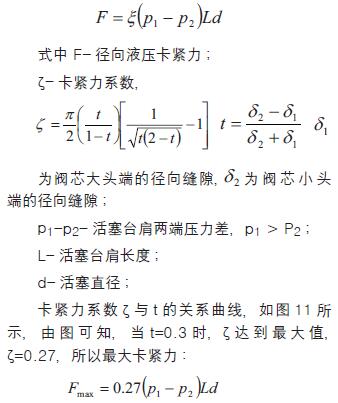
液压卡紧力乘缸筒间的干摩擦系数μ 则得活塞移动时的轴向摩擦阻力
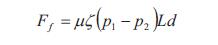
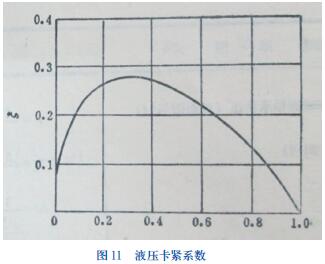
从以上的分析可知,液压卡紧的产生,对于零件的加工中产生的配合偏心、锥度等应该避免。在实践中应该考虑间隙密封活塞两端的压力差。除此之外,液压卡紧系数也息息相关。
3.3.4 旋转涨刀油缸涨刀油缸活塞与缸筒间隙密封结构采取消除液压卡紧方法
针对上述分析,在设计旋转涨刀油缸涨刀油缸时,为杜绝间隙密封中液压卡紧的弊端,分别从以下各措施进行改善。
1、提高各配合零件的加工精度和装配精度,避免偏心。
2、目前,间隙密封在液压阀组中应用例子较多,普遍采用的办法为开均压槽。即在活塞台肩上开平衡径向力的均压槽,示意图如图12 所示。图示中,槽的位置尽可能的靠近高压侧,一般开两条槽已见效,三槽以上效果不大,当均压槽开在台肩1/4 处时,对减少液压卡紧的效果为最佳。我们在设计旋转涨刀油缸涨刀油缸的活塞组合件时,在其活塞位置设计均压槽,即在高压侧(左侧)离活塞台肩的1/4(活塞总长为16mm,离高压侧4mm 处)开均压槽设置,并开双均压槽设置,如图13 所示。
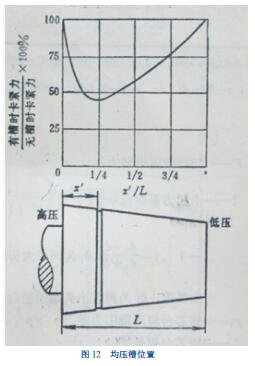
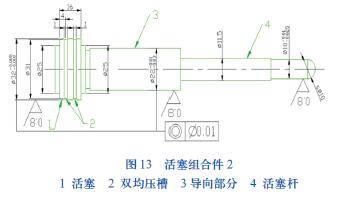
3、油液中若含有不均匀高分子添加剂和其它杂质均会使缝隙堵塞,卡紧现象更容易发生,为此应注意保持液压系统的油液清洁。
4.集成旋转涨刀油缸设计开发效果
通过上述系统的分析,旋转涨刀油缸的开发应从避免上述技术弊端进行设计,其关键技术突破了原旋转涨刀油缸的设计弊端,其技术设计实现四大特点: 结构集成设计、防振设计、耐磨设计和间隙密封设计,如图14 所示。
4.1 集成结构设计
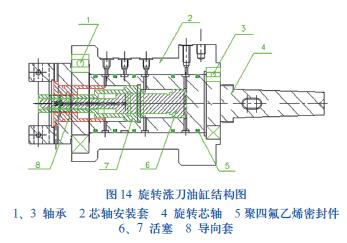
压缩空气与液压油两种介质集中于旋转芯轴与旋转芯轴安装套的各密封腔,利用聚四氟乙烯密封圈密封,互不干扰传输,实现分体结构到集成结构设计转型。
4.2 防振设计
在减振方面,分体结构的零部件具有分散性,产生振动来源点多。集成结构的零件大大减少,零件具有集中性,再有在配合上精度要求更高,部分动态零件的配合使用研磨配合工艺,在运转工作时,振动自然就减弱。另一方面,使用聚四氟乙烯密封件代替原丁腈橡胶(NBR)O 型密封圈密封,摩擦阻力更小,且具有一定的吸振功能,进一步控制了振动源的产生,实现防振设计。
4.3 耐磨设计
旋转芯轴安装套采用两种材料结构,实现一种零件两种材料的有效组合。安装套主体材料采用45 钢或40Cr,与聚四氟乙烯密封件的密封接触面采用表面镀硬铬材料,其内孔采用研磨技术研磨,粗糙度Ra0.4,减少油缸旋转的密封件与安装套的摩擦阻力,提高耐磨的目的。另一方面,旋转涨刀油缸的旋转芯轴设计精密轴承安装于旋转芯轴安装套内,并非是依靠密封件导向旋转,
是密封件能够均匀磨损,提高使用寿命。
4.4 间隙密封设计
集成旋转涨刀油缸的旋转芯轴,内置的涨刀活塞采用双级涨刀活塞设计,活塞设计为免装密封件设计,只依靠活塞与其配合的缸筒精密间隙配合实现间隙密封设计。间隙密封技术分别从泄漏、热楔力及液压卡紧等方面进行系统的分析其弊端而进行扬长避短优化设计。
集成旋转涨刀油缸的开发设计,已经成功运用于我们公司的柴油机气缸体缸孔珩磨机床上,解决了温度变化和压力变化的旋转密封瓶颈。在质量控制方面,由于集成旋转涨刀油缸自振问题和检测介质压缩空气泄漏问题的解决,珩磨机体缸孔的质量更加稳定受控。
5.结束语
聚四氟乙烯密封材料在集成旋转涨刀油缸开发设计中的成功利用,探索出了在旋转交变载荷场合中,如何达到减振及耐磨功效典型案例,具有很好的推广价值。
投稿箱:
如果您有机床行业、企业相关新闻稿件发表,或进行资讯合作,欢迎联系本网编辑部, 邮箱:skjcsc@vip.sina.com
如果您有机床行业、企业相关新闻稿件发表,或进行资讯合作,欢迎联系本网编辑部, 邮箱:skjcsc@vip.sina.com
更多相关信息
- target=_blank>鉴于QC的发动机缸体铸造质量问题改善
- target=_blank>枪钻在复合设备中的应用
- target=_blank>蒸汽发生器管板深孔钻加工及清洗防护
- target=_blank>浅析UG技术在汽车模具中的应用
- target=_blank>一种小型叉形接头的精密加工技术
新闻资讯
| 更多
- target=_blank>创新有形:Creaform 形创增强版 HandySCAN 3D 提升便携式三维扫描性能
- target=_blank>Creaform 形创推出全新升级版光学三坐标三维扫描仪和探测组合套件
- target=_blank>五轴超精密加工机床底座设计技术研究
- target=_blank>基于精雕系统的七级叶轮加工技术实践
- target=_blank> 以柔性制造加固核心壁垒—访西派集团有限公司董事长梁桂华先生
- target=_blank>HELI系列的新发展
- target=_blank>坚定投资中国 助推高质量发展——访埃斯维机床(苏州)有限公司总经理 Norbert Wiest 先生
- target=_blank> 最是步稳能致远—访台湾雷威精密机械有限公司总经理熊健男先生
- target=_blank>直击CES 2024:西门子瞄准沉浸式工程和人工智能,驱动工业元宇宙创新
- target=_blank>汽车轮毂加工方法与工艺分析