新能源汽车大型压铸件尺寸精度研究
2025-6-26 来源:重庆赛力斯新能源汽车设计院有限公司 作者: 林真廷 叶小军
【摘要】: 赛力斯汽车推出具有地面最强悍性能的 SUV 问界 M9,其车身结构采用了先进的一体化压铸全铝底盘,有效减轻了簧下质量,进而提升了操控性能,然而压铸件尺寸精度如何控制成为行业最大的难题。提出了一种在生产过程中针对压铸工艺过程、免热处理材料、校型工装设备、过程管控及压机参数调试等方面优化的控制策略,这一策略不仅有助于提升新能源汽车的制造水平,同时也为压铸行业的发展提供了有益的参考和借鉴。
【关键词】: 一体式压铸工艺 ; 铝合金后车体 ;免热处理材料 ; 尺寸精度
随着 “双碳” 目标的实施,全球汽车行业对节能环保的重视程度日益提升。为实现节能减排,各国纷纷认可并支持新能源汽车的发展。在这一背景下,新能源车企为满足消费者对轻量化、高效能的需求,不断加大研发和生产投入。一体化压铸技术,以其在生产效率、成本降低和减重方面的显著优势,正成为新能源车身结构发展的关键技术。特斯拉、蔚来、小鹏等领先新能源车企已积极布局一体化压铸领域,预示着压铸机将逐步取代焊接机器人,成为新能源汽车制造的核心装备。该技术的核心在于大型压铸机的卓越性能、创新的免热处理材料配方、精密的压铸模设计以及优化的压铸工艺参数。特别是铝合金一体化压铸技术,其轻量化和高效生产的特性使其成为新能源车企的标配技术。本文旨在深入探讨一体化压铸技术在新能源汽车制造中的后车体尺寸精度控制运用。
压铸工艺介绍
1.压铸定义
压铸 ( High Pressure Die Casting ,HPDC),是高压铸造的简称,是指将熔融的液态金属或半固态金属以较大的压力(20~120MPa)和速度(20~100m/s )压入模具型腔,并使之在较高的外部压力作用下凝固的成型工艺。在压铸过程中,金属液能够快速的充满模具型腔,在外部压力作用下,不仅能够保持金属液与模具型腔尺寸和形状的一致性,而且在模具型腔的强冷作用下,外部压力使得金属液与模具紧贴,从而使铸件 - 模具作为整体具有优异的散热性,使金属液在极短的时间内完成凝固,获得晶粒细小、组织均匀的铸件。
一体化压铸,是指将传统的多个单独、分散的小件进行重新设计高度集成,在利用大型压铸机进行一次成型,省略焊接的过程直接得到一个完整的大型件的新型压铸工艺。压铸岛如图 1 所示。
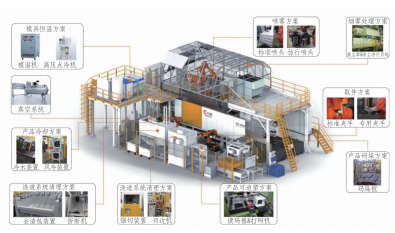
图 1 压铸岛
2.传统压铸与一体压铸的区别
(1)材料选择 传统压铸工艺所使用的的铝合金发展起步较早,材料的工艺特性相对成熟可控。传统铸造结构件因其尺寸较小,在铸造成型后还可进行 T6、T7 热处理,以提高零件的力学性能及耐腐蚀性。常用 ADC12、ADC14、A360、A380、ENAC-43400、ENAC-4600 及 SF36(AlSi10MnMg)。
一体化压铸件由于尺寸较大,形状复杂,热处理带来的热胀冷缩可能会引起零件的尺寸变化和表面裂纹等缺陷。因此需选用免热处理的铝合金材料。材料同时还需具有高强韧性、高流动性、高的连接包容性等性能特点。常用 C611、560 合金、A152。
(2)模具 传统压铸由于传统铸件尺寸较小,结构相对简单,模具设计中的分模方案,浇注系统,排气系统,顶出系统,模温系统的设置较为简单。且在模具设计前期计算冗余度设定较高,模具后期进行试模调整也更加方便。
一体化压铸模具结构尺寸更大,结构也更为复杂。这对模具设计中的浇铸系统,模温系统,顶出系统以及真空度的设置有更高的要求。在前期设计时需进行充分的模拟分析,风险评估,以减轻模具后续调整难度。在模具材料选取和机械加工工程中,也要充分考虑模具的寿命和可靠性。
(3)设备 传统压铸工艺由于零件尺寸较小,开模方向的投影面积较小,铸造过程中所需的锁模力不大。对压铸机的性能要求不会太高,所需吨位一般不超过 4500t,压铸岛配套设备尺寸、数量都较小。
一体化压铸件整合集成了多个小件,所以其重量和开模方向的投影面积相比于传统压铸零件增大不少,对压铸机的锁模力吨位也提出了更高的要求。目前市面上用于一体化压铸成型的压铸机吨位一般不会低于 6000t,周边设备尺寸、数量也相应增加。
(4)工艺 传统压铸工艺人们主要依靠经验来做出判断和决策,过往的压铸从业人员将其经验汇总成经验公式或者是经验图表,供行业
参考。
一体化压铸可以参考的类似产品较少,且许多工艺参数都突破了传统压铸的工艺参数上限,传统经验公式是否有效还需进一步验证。为保证铸件的成型质量,对压铸合金的纯净度,喷涂材料的低发气性,冲型前型腔真空度都有更高的工艺要求。
(5)用途 传统压铸汽车领域主要适用于电动机外壳、变速器外壳、电控外壳壳体类零件。一体压铸主要应用于扭力梁、前舱总成、后地板及侧围 CD 柱内板等车身轻量化部件。
3.一体压铸后车体制造工艺
(1)制造工艺 一体压铸后车体生产过程是一个精密而复杂的工艺流程,它涉及多个关键步骤,从毛坯压铸开始,一直到装配标件并检测合格交付产品。压铸工艺是一体压铸后车体生产过程中的关键环节,它涉及将熔融的金属注入模具中,通过高压和冷却使其凝固成所需形状。在压铸前,要准备好模具,模具的精度和质量直接影响到最终产品的品质。模具的制造需要依据产品的设计图样,经过精密加工而成。
毛胚压铸首先需要调整压铸机的参数,如压力、速度、温度等,以适应不同产品的生产需求。接着,压铸机通过高压将熔融的金属以压入模具中,并使其充满模具的每一个角落。这个过程需要严格控制时间和压力,以确保金属能够充分凝固并达到所需的密度和强度。如图 2 所示。
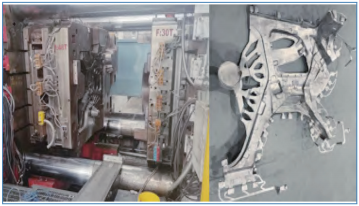
图 2 毛胚压铸
毛胚铸件表面可能还附有一些多余的金属或毛刺,需要进行切水口和打磨等处理。接下来是毛坯校型,通过对铸件进行精确的测量和调整,使其符合产品设计的尺寸和形状要求。如图3所示。
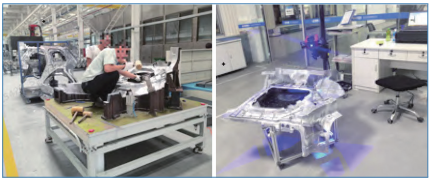
图 3 毛坯校型 图 4 蓝光扫描
最后,通过蓝光扫描技术,可以快速、准确地获取产品的三维数据,并与设计数据进行比对分析。这种检查方式不仅提高了检测效率,更能发现肉眼难以察觉的微小缺陷,从而确保产品质量的稳定性和可靠性。如图 4 所示。
总的来说,一体压铸后车体生产过程中的压铸工艺是一个复杂而精细的过程,它涉及多个环节和步骤,需要严格控制每一个细节,以确保最终产品的质量和性能达到要求。随着技术的不断进步和工艺的不断优化,一体压铸技术将在汽车制造等领域发挥越来越重要的作用。
尺寸精度控制方案
1.材料选择
为减少大型铸件热处理后的变形,当前主要方法是研发免热处理材料。在汽车结构件领域,研究集中于 Al-Si 系和 Al-Mg 系铝合金。这些材料通过添加化学元素和优化压铸条件,形成细小晶粒,实现与传统材料相当的力学性能。主流材料包括 C611(美国铝业公司)和 SF36(德国莱恩金属),它们已广泛应用于汽车结构件生产,如蔚来 CD 柱和奥迪 A8 车身。这些材料在特定工艺下具有出色的延伸率,适用于多种车身部件。C611 和 SF36 化学成分以及力学性能见表 1、表 2。
表 1 压铸铝合金各元素质量分数 (单位 :%)

表 2 压铸铝合金拉伸力学性能要求

2.校型工装设备
(1)定位基准 校型工装定位选择如图5所示,A1~A4作为基准目标,限制Z向移动以及绕Y轴、X 轴转动的三个自由度 ; 选择 B 孔作为主定位孔,限制 X 向以及 Y 向移动的两个自由度 ; 选择 C 孔作为次定位孔,限制绕 Y 轴的转动。
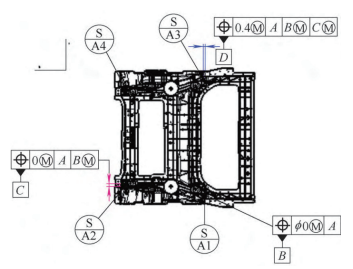
图 5 一体式后车体 GD&T 图样
(2)校形工装 切边整形模指利用冲模修边工序件的多余边缘废料,使其具有一定高度、直径和形状的冲压模具。切边模主要用于修整拉申的边缘,让端面平整美观,确保零件的一致性便于下一步装配。如图 6 所示。
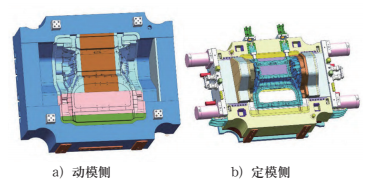
图 6 压铸模具
通过 RPS 点将零件定位在校形检具上,针对需要控制的形状、尺寸及位置进行校形,使零件满足尺寸精度要求。
3.过程管控
(1)蓝光扫描 分别对毛坯校型、机加(面、孔)及成品校型后进行扫描测量,并针对扫描的结果进行反馈,以便提前识别问题点提前规避尺寸缺陷。
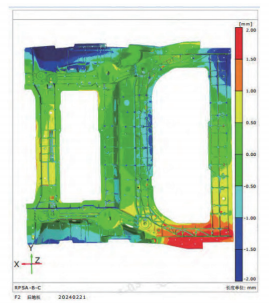
图 7 成品校形扫描结果
如图 7 所示,可以看出绿色部分 ±0.5mm为合格区域,红色及蓝色分别为 ±2mm 偏差区域,根据图示可以看出两边轮罩区域及前部与门槛梁搭接区域存在严重超差情况。
(2)成品检具测量 成品检具作为零件合格交付前的最后一道检测关卡,在尺寸精度把控方面起到至关重要的作用。为减少工作量提高工作效率,针对不同零件可以进行关键点位选取制作为如图 8 所示测量记录表进行百分之百监控测量。
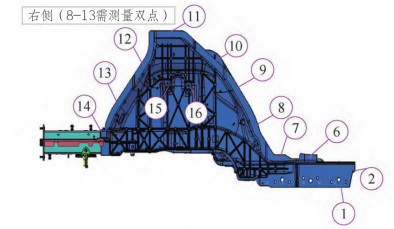
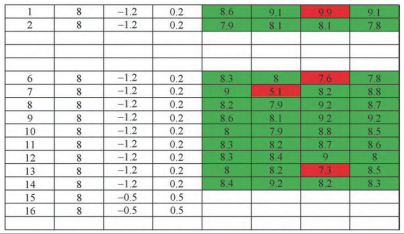
图 8 关键测点检测工艺卡
4.压机参数调试
1)压力 : 压射比压常规设置为 30~90MPa,增压比压一般设置在 50~300MPa。
2)速度 : 低阶段速度为 0.1~0.5m/s; 高速阶段速度为 3~6m/s; 内浇口速度为30~60m/s。
3)时间 : 充填时间由压铸件体积、平均厚度,填充速度决定,薄壁件一般不超过 0.1s; 持压时间薄壁件 1~2s,厚壁件 3~5s; 留模时间主要由产品尺寸结构和工艺温度决定。
4)温度 : 浇注温度通常由定量炉内金属液温度表示,一般为 700~740℃ ; 预热模具温度一般为150~180℃,连续工作温度一般为180~220℃。
改进前后对比分析
通过材料选择、校型工装设备、过程管控及压机参数调试四个方面,压铸件整体尺寸精度质量均有较高提升,结合改进前后一体式后车体进行抽样测量并做分析,得出以下结论。
选取测量点 6~14 号,结合统计分析软件Minitab 通过双样本对比分析,具体见表 3~ 表 5。
表 3 描述统计量
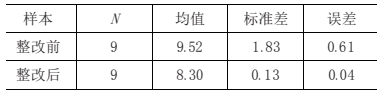
表 4 差值的估计值

表 5 检验值

方法 :μ1 为整改前的总体均值 ;μ2 为整改后的总体均值 ; 差值 μ1 - μ2 已针对此分析假定了
等方差。
原假设 :H0=μ1 - μ2=0
备择假设 :H1=μ1 - μ2 > 0
由分析结果可知差值下限为 0.153 >假设差值 0,同时 P 值为 0.032 < 0.05,充分证明原假设被拒绝,备择假设成立,整改后改善明显。充分证明选择最优的材料,通过校型工装百分之百校正,通过过程管控及压机参数调试,最终能明显提高压铸件尺寸精度。
结语
中小型一体压铸结构件在车上的应用方面已经成熟,大型一体压铸后车体工艺结构设计任然是技术难点,需要车身设计与工艺技术人员紧密协作共同开发。从制造工艺角度看,目前压铸机和模具等主要工艺装备已具备配套条件,可支撑投影面积 20000cm2铸件的开发,C611 和 SF36的免热处理材料已在部分铸件上生产试用,具备配套条件。压铸件尺寸精度也可通过工装定位、面热处理材料、校型工装、压机参数调试及过程管控确保外观尺寸一致性。
投稿箱:
如果您有机床行业、企业相关新闻稿件发表,或进行资讯合作,欢迎联系本网编辑部, 邮箱:skjcsc@vip.sina.com
如果您有机床行业、企业相关新闻稿件发表,或进行资讯合作,欢迎联系本网编辑部, 邮箱:skjcsc@vip.sina.com
更多相关信息
- target=_blank>HA-C轴承开始为汽车提供解决方案
- target=_blank>ISCAR创新金属加工解决方案,助力电动汽车制造升级
- target=_blank>三项对策技术首次同时采用,滚道磨损量下降90%以上
- target=_blank>国宏工具助力南京航空航天大学工艺优化 化解老大难问题
- target=_blank>博世中国与腾讯深化战略合作,推动智驾智舱业务深度合作
新闻资讯
| 更多
- target=_blank> 智能冷却与切屑控制,开启加工新时代
- target=_blank> 数控车床在不稳定工况下的切削加工及先进刀具几何形状对降低切削力的影响
- target=_blank>LOGIQUICK:重返钻削领域
- target=_blank>大型数控镗铣床疑难故障诊断方法研究及应用
- target=_blank>台达CNC数控系统NC5系列 与您共塑精密制造新未来
- target=_blank>EMO Hannover—访德国机床制造商协会(VDW)执行总裁马库斯·赫尔宁博士
- target=_blank>以车铣复合加工跑出发展加速度--访森泰英格(成都)数控刀具股份有限公司常务副总夏科尧先生
- target=_blank>Creaform 形创推出专业版扫描到 CAD 应用模块
- target=_blank>新产品丨机床主轴用“脂润滑轴承专用润滑油供给单元”
- target=_blank>覆盖件模具数控加工刀库自动化应用