往复式压缩机曲轴动态特性分析
2016-7-18 来源:合肥通用机械研究院压缩机技术国家重点实验 作者:鲍军 张成彦 姜慧君 邢志胜
1、引言
在往复式压缩机中,曲轴是最主要的运动件之一,曲轴结构的合理性、加工的优劣和尺寸参数的精确性对压缩机的工作性能有着巨大的影响。在压缩机的工作过程中,曲轴的工作状态是周期性变化的,需要面对气体压力、旋转运动所带来的巨大惯性力,并且曲轴的工作环境随着压缩机各项指标的逐渐上升变得越来越严苛,因此对曲轴的强度与刚度提出了更高的要求,所以如何保证曲轴具有较好的刚度强度以及动态特性成为近年来曲轴的研究重点。另一方面,压缩机在工作过程中产生的噪音很大程度上也是由于曲轴运动发生振动所造成的,因此对曲轴的工作状态进行深入的理论研究和分析,是具有非常重要的现实意义的[1]。
2 、曲轴实体模型的建立
曲轴是压缩机中关键零件,其形状特征决定了结构几何参数的复杂性,而各个结构参数对曲轴动态特性影响程度也不尽相同。因此在建模过程中,依据简化原则选择性地忽略一些对动态特性影响程度较小的结构参数,从而在不影响模型参数分析条件下,建立较为简化模型后对模型进行有限元分析,能够得到精度较高的计算结果[2]。CCS-210/40 螺杆活塞串联压缩机往复机部分为两列立式,共三级压缩,容积流量为210m3/h,最高排气压力可达40MPa,转速为1000r/min,曲轴材料为40Cr。网格划分时根据曲轴的结构特点,对轴颈圆角处进行局部控制,网格划分的相对较密,单元长度取为2.5mm,而在其它区域可采用较疏的网格划分,单元长度取为8mm。模型包含了364793 个节点,256346 个单元,如图1 所示。
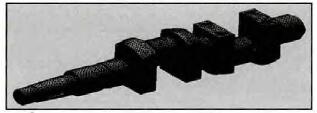
图1 曲轴有限元模型
3 、曲轴动力学分析
在压缩机的工作过程中,曲轴的运动状态是非常复杂的,其需要承受复杂的运动载荷,而这些运动载荷在曲轴的不同运动状态中对其造成的作用力也是不同的。因此为了保证有限元分析的精确性,曲轴的分析采用多体动力学模型方法,建立的压缩机曲轴系模型由曲轴、主轴承、连杆轴承、连杆、活塞、飞轮、曲轴平衡块等组成,对两列活塞施加变化的气体压力,将曲轴转速设定为1000r/min,进行仿真分析可以得到曲轴在压缩机整个工作循环内的力边界条件,包括曲轴所受的力、力矩、加速度、角速度及角加速度等,这为曲轴的动态特性分析提供了可靠的边界条件。
通过多体动力学分析得到的曲轴轴颈的载荷随时间的变化过程,如图2、图3 所示。这些数据对下一步计算曲轴的动态特性具有重要的意义。
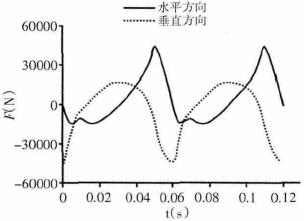
图2 第一列轴颈载荷
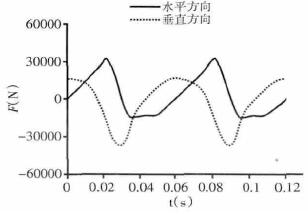
图3 第二列轴颈载荷
4 曲轴动态特性分析
4.1 曲轴模态分析
在往复式压缩机中,曲轴必须承受各种复杂载荷,其性能的好坏对压缩机的使用寿命具有重要的影响。当激振频率与曲轴自身的固有频率相当时,将引发曲轴的剧烈振动和声辐射,造成曲轴刚度下降和响应振幅增加,最终引起共振,造成曲轴弯曲疲劳或扭转疲劳的失效。在压缩机的设计制造过程中,为保证曲轴不出现共振现象,通常使曲轴的固有频率f0≠(0.8~1.2)f,f为激振频率。但在以往的设计中,静力校核计算无法解决上述问题,因此在设计中就必须对曲轴进行模态分析。
4.1.1 不加约束的自由模态分析
在曲轴的模态分析过程中,如果不加入任何约束,其分析结果就是曲轴的自身特性。在通常情况下,压缩机共振主要发生在低阶次频率。因此,根据这一规律,在曲轴的模态分析中,对曲轴的前八阶振型加以分析。而前六阶的模态都是在无约束边界的条件下进行的,计算结果为0,表明其是刚体模态。因此第七阶才是真正的第一阶模态。
不加约束曲轴前八阶振动频率,如表1 所示。不加约束曲轴前八阶振型图,如图4 所示。
(后文图表中省略了前六阶刚体模态,因此第一阶实为第七阶,第二阶实为第八阶,以此类推)

表1 不加约束曲轴振动频率
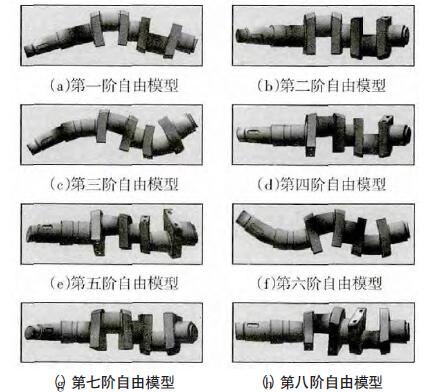
图4 不加约束曲轴前八阶自由振型图
4.1.2 施加约束的模态分析
在曲轴模型中设置适当的约束条件能够真实地反映出曲轴在实际工作状态下的各项特性,对于约束条件的处理,通常要视实际情况而定,因为在约束作用下,有些模态将无法反映出来或者已经被改变了,因此必须建立适当的约束条件,才能够使模态分析准确地反映出曲轴实际工况下的动态特性;另一方面,在模型中使用不同的约束条件,其分析结果也不尽相同。计算分析时根据曲轴实际装配情况,将曲轴的支撑面上加以径向约束,而曲轴绕主轴颈轴线做旋转运动,因此不施加周向自由度约束。
施加约束的曲轴前八阶振动频率,如表2 所示。施加约束曲轴前八阶振型图,如图5 所示。

表2 施加约束的曲轴振动频率
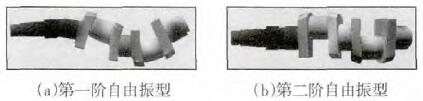
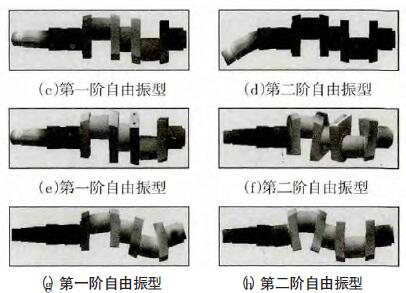
图5 施加约束曲轴前八阶振型图
4.1.3 模态计算结果分析
通过分析曲轴在上述两种条件下的模态,得到了曲轴在前八阶的固有频率和相应振型,其分析结果表明,在无约束条件的情况下,曲轴前三阶以整体弯曲振动为主,只是弯曲方向不同,第三阶和第四阶表现为整体扭转振动,第五阶至第八阶表现为弯曲和扭转相结合的复杂振动。曲轴在加上位移约束后,其振动频率明显提高。
曲轴弯曲振动的激振力频率:f= fc×n,式中:fc—压缩机运行的频率; n—压缩机的列数,所以当压缩机转速为1000r/min 时,激振力频率为33.33Hz,不同阶的固有频率均比激振频率要高出许多,因此在上述转速条件下,曲轴不会发生共振现象,从而也不会出现因大幅振动而造成曲轴损坏。
4.2 曲轴动态响应分析
对曲轴进行动态响应分析主要用于确定由动载荷引起的响应即变形和应力等。从理论分析上讲,实际上就是含外部载荷的结构振动微分方程组的解。求解方法主要有直接积分法和振型叠加法。针对复杂的载荷因素,在实际计算中,选取直接积分法来对曲轴动态响应问题进行求解。
根据前文的动力仿真结果,在曲轴响应的轴颈处加上随时间变化的载荷后进行响应计算,动力仿真时得到曲轴载荷为两个周期内即曲轴旋转720°时间范围内的受力数值,如图2、图3 所示。由于曲轴转速为1000r/min,因此将响应计算时间设置为0.12s。为了能够准确的捕捉到其响应过程,将时间步长设置为0.00033s,因此共需要计算360 个子步,每隔5 步记录一次,一共得到72 个数据结果。在数据结果中,只分析研究了部分具有代表意义时刻的应力和位移分布情况。
(1)当曲轴转动60°时,也就是t=0.01s 时刻,此时曲轴的最大应力为78.1MPa,最大变形为0.0492mm,如图6、图7 所示。
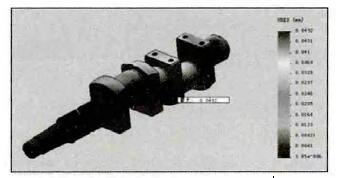
图6 曲轴转动60°时的位移云图
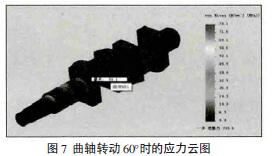
(2)当曲轴转动180°时,也就是t=0.03s 时刻,此时曲轴的最大应力为177.7MPa,最大变形为0.0808mm,如图8、图9 所示。
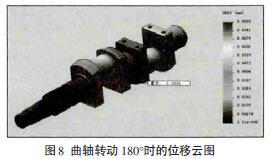
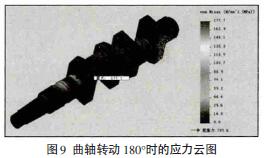
(3)当曲轴转动660°时,也就是t=0.11s 时刻,此时曲轴的最大应力为170.6MPa,最大变形为0.0827mm,如图10、图11 所示。
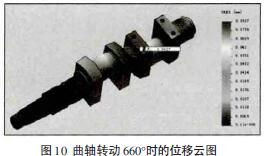
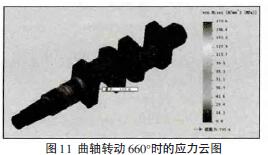
动态响应分析的作用还在于可以根据需要计算得出曲轴特定部位的位移和应力情况,曲轴应力集中部位的应力随时间变化曲线,如图12 所示。其所在位置,如图13 所示。从动态响应分析结果可以得出,最大应力值为177.7MPa,出现在曲轴转动180°时,位置位于危险部位1 即靠近扭矩输入端主轴颈与曲柄相连的过渡圆角处。且对比可以发现,曲轴危险部位1 在各种工况下的最大应力值都高于其它危险部位,为曲轴疲劳失效风险最大的部位。经校核分析,曲轴疲劳强度安全系数为3.01,静强度安全系数4.42,均高于允许值,因此该曲轴具有较高的可靠性,可以达到设计和运行工况的要求。
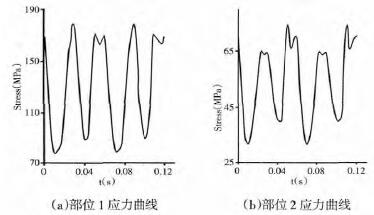
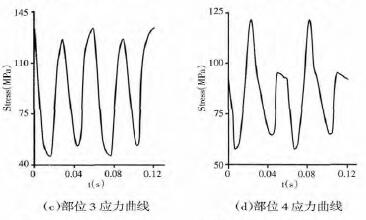
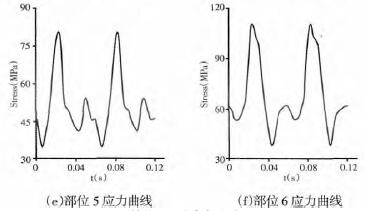
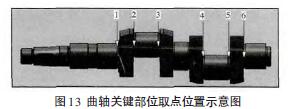
5 总结
通过建立压缩机曲轴动力学模型可以求解出对曲轴动态响应分析所需的激励力,通过对曲轴的模态分析得到了曲轴在自由状态和约束状态下的固有频率和模态振型。分析认为,所建立的曲轴有限元模型较好地反映了曲轴实际结构的动态特性。
曲轴的动态响应分析结果显示了曲轴在压缩机不同工作时刻下的位移和应力的分布情况,有助于发现容易导致疲劳失效的风险以及其它潜在问题,为曲轴的结构优化提供理论依据和改进方向,提出一些具有针对性的优化方案。在CCS 型压缩机曲轴改进设计中,针对失效风险最大的前端圆角部位重新优化调整了圆角的结构型式和尺寸参数,同时减小了曲柄厚度。改进后的曲轴动态响应分析结果显示曲轴疲劳强度安全系数提高了30%,重量减轻了4.6%。这样有效地缩减了曲轴的开发周期和制造成本,显著提升了设计的质量。
参考文献
[1]张弘钧.大型工业压缩机曲轴动态特性分析[D].南京:南京理工大学,2007: 1-3.(Zhang Hong-jun.The dynamic characteristic analysis of the crankshaft ofa mainframe industrial compressor [D] .Nanjing:Nanjing University ofScience and Technology,2007: 1-3.)
[2]杨瑞峰,崔志琴.柴油机曲轴的动态特性研究[J].内燃机,2002(5): 3-5.(Yang Rui-feng,Cui Zhi-qin.Study on dynamic feature of crankshaft[J].Internal combustion Engines,2002(5): 3-5.)
[3]王磊,刘杰,刘树英.往复式活塞隔膜泵曲轴的动态特性分析[J].机械设计与制造,2010(5):238-240.(Wang Lei,Liu Jie,Liu Shu-ying.Analysis on dynamic characteristic of crankshaft of reciprocating piston diaphragm pump[J] .Machinery Design& Manufacture,2010(5):238-240.)
[4]刘成武,钱林方,桑光云.基于虚拟样机技术的压缩机曲轴动态特性研究[J].流体机械,2007,35(9):29-32.(Liu Cheng-wu,Qian Lin-fang,Sang Guang-yun.Dynamic characteristic
of compressor crankshaft based on technique for virtual prototype[J].Fluid Machinery,2007,35(9):29-32.)
[5]宋春青. 车用空压机曲轴连杆机构的动力学分析与仿真[D].武汉:武汉理工大学,2009: 1-2.(Song Chun-qing.Dynamic analysis and simulation of the crankshaft andconnecting rod mechanism of air compressor for vehicle [D] .Wuhan:Wuhan University of Technology,2009: 1-2.)
[6]高合瑞. 空气压缩机组合曲轴断裂失效研究[D].西安:西安电子科技大学,2009:37-38.(Gao He -rui. Research on fracture failure of air compressor combinedcrankshaft[D] .Xi’an:Xidian University,2009:37-38.)
[7]张海峰.大型压缩机曲轴特性研究[D].南京:南京理工大学,2005: 2-3.(Zhang Hai-feng.Study on the characteristics of large compressor crankshaft[D] .Nanjing:Nanjing University of Science and Technology,2005: 2-3.)
[8]张晋伟. 4125A 型柴油机曲轴结构有限元动力分析[D]. 咸阳:西北农林科技大学,2009: 1-5.(Zhang Jin -wei. Analysis of 4125A diesel engine crankshaft structuredynamic finite element[D]. Xianyang:Northwest A&F University,2009:1-5.)
[9]刘成武.大型压缩机动力学分析与噪声预测[D].南京:南京理工大学,2006:65-70.(Liu Cheng-wu.Large scale analysis and noise of the compressor dynamicsprediction [D] .Nanjing:Nanjing University of Science and Technology,2006:65-70.)
投稿箱:
如果您有机床行业、企业相关新闻稿件发表,或进行资讯合作,欢迎联系本网编辑部, 邮箱:skjcsc@vip.sina.com
如果您有机床行业、企业相关新闻稿件发表,或进行资讯合作,欢迎联系本网编辑部, 邮箱:skjcsc@vip.sina.com
更多相关信息
- target=_blank>基于有限元方法的曲轴模态分析
- target=_blank>自动化车床刀具检测优化模型研究
- target=_blank>航空风冷发动机缸体传热模拟及翅片形式研究
- target=_blank>飞机维修引入自动化 “智修时代”正式来临
- target=_blank>减速器箱体镗孔工装设计
新闻资讯
| 更多
- target=_blank>MB2120B型数控内圆磨床电主轴变频器的改造
- target=_blank>【雷尼绍】RESOLUTE™与MELSERVO-J5强强组合,实现更快速、精确、可靠的运动控制
- target=_blank>NSK开发低摩擦轮毂单元轴承 可增加电动汽车续航里程
- target=_blank>T68卧式镗床进给系统的数字化改造
- target=_blank>AGV+协作机器人在零件数控机床加工上下料中的应用
- target=_blank>2020年7月高端装备制造业、工业机器人,行业运行简述
- target=_blank>浅谈线切割机床中走丝与慢走丝
- target=_blank>ANCA整体PCD铣刀 —— 提高生产效率带来新的发展机遇
- target=_blank>伊斯卡,不止专注于金属加工
- target=_blank>EMAG成功收购Scherer Feinbau(舍勒公司),极大扩展了公司产品范围以及客户群体