发动机缸体三轴镗组合机床的设计*
2016-7-27 来源:大连华根机械有限公司智能制造研究所 作者:周江辉 赵鑫 谢哲 李瑾
摘要: 文章针对汽车发动机缸体三轴镗组合机床加工精度提高的要求,在现有产品和技术的基础上,进行三轴镗组合机床设计的研究。对机床的整体布局方法进行介绍,着重对数控机械滑台、夹具等关键部件的结构改进和创新以及功能性进行说明,同时对产品的刀具特点、机械手的输送和机床的环境保护方面进行关注。三轴镗组合机床的成功设计,促进我国汽车发动机缸体关键工序加工国产化的进程,以此为基础的组合机床产品还在国家重大专项中获得应用。
关键词: 缸体; 精镗三轴孔; 组合机床
0、引言
2009 年,我国超越美国和日本成为世界第一大汽车生产国和最大的汽车市场,但是我国还并非汽车生产强国,尤其在关键零部件和关键工序的加工设备方面与国外有较大差距。缸体是发动机的本体,是最重要的关键部件之一,而主轴孔、凸轮轴孔、机油泵孔( 俗称三轴孔) 的加工是缸体加工的关[1]。以缸体三轴镗组合机床为例,国外先进设备在保证加工的前提下,已经普遍采用机械手配合自动滚道输送的敏捷物流系统形式[2]; 相比之下,尽管经过技术的引进、消化吸收、自主开发及产业化等几个阶段,国产三轴镗组合机床在加工精度方面已经大幅度提高,但是在敏捷物流系统方面才刚刚起步,在高效、高精、可靠性等方面与国外仍存在差距[3],国内相关设备尤其是精加工设备的进口率依旧达90%以上。
本文以三轴镗组合机床项目为背景,从方案设计入手,通过合理布局机床和零部件结构,优化刀具参数和性能等方法,提高加工精度和可靠性; 采用机械手输送,提升敏捷物流系统水平,设计出满足使用需求的高精、高效、高可靠性三轴镗组合机床,并在生产中获得用户的认可。
这种三轴镗组合机床形式还应用于国家数控重大专项,并进一步得到完善。目前,设备已在用户现场使用,加工产品精度和设备性能获得用户好评。
三轴镗组合机床的研究与设计成功,加快三轴镗组合机床国产化步伐,打破国外设备的垄断,提高国产发动机的制造能力,降低生产成本; 促进机床行业和汽车行业的共同发展,由技术引进型向技术自主型转化,具有显著的经济效益和社会效益。
1、机床方案的设计
1. 1 被加工零件基本情况
材料: 合金铸铁;
硬度: HB210-HB235;
重量: 400 kg。
精度要求:
( 1) 主轴孔: 孔径加工至120. 625 + 0. 020 mm,同轴度为0. 02 mm,表面粗糙度为Ra3. 2,各档圆度0. 012mm,圆柱度0. 012mm;
( 2) 凸轮轴孔: 孔径加工至68. 237 + 0. 0250 mm,同轴度为0. 025mm,表面粗糙度为Ra3. 2,各档圆柱度0. 012mm;
( 3 ) 机油泵安装孔: 孔径加工至126. 987 + 0. 020 mm,表面粗糙度为Ra3. 2;
( 4 ) 辅助驱动支撑安装孔: 孔径加工至133. 337 + 0. 020 mm,表面粗糙度为Ra3. 2;
( 5) 前端面销孔: 孔径加工至12. 675 + 0. 020 mm,深度加工至16. 65 ± 0. 3mm,表面粗糙度为Ra3. 2。
( 6) 第7 档止推面: 加工范围152mm,全跳动0. 025mm,表面粗糙度为Ra3. 2。
1. 2 机床整体布局
三轴镗组合机床由数控移动工作台配以专用数控滑台、主轴箱、镗削头、夹具、桁架机械手机动滚道以及排屑、冷却等部分组成。
三轴镗组合机床为湿式加工,采用大流量冲屑,具体机床总图如图1 所示。单件加工工时11min,即每小时被加工零件数为5. 5 件。
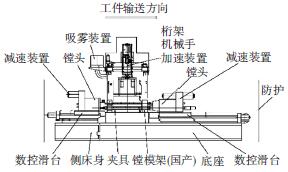
图1 机床整体布局图
2、关键部件设计
由于被加工零件尺寸大、精度要求高,对机床也提出了非常高的要求。设计过程中对机床的夹具、滑台、模板等方面进行了攻关,对刀具、机械手也进行了重点分析,确保机床各方面达到使用要
求。
2. 1 数控滑台
数控滑台是机床的关键动力部件,直接关系到机床的加工能力。本次设计的三轴镗组合机床在机床两侧分别配置了一个数控滑台,为缸体三轴孔加工提供动力支持。两侧的数控滑台均采用具有自主产权的功能部件为基础,根据设计的实际需要进行改进。
左侧数控滑台的型号为SEM-F500 /630,滑台行程为630mm,右侧数控滑台在SEM-F630/1000 型号基础上进行改进,如图2 所示,增加了滑座的行程,保证满足1900mm 的行程需求。
数控滑台的滑动部分由两根矩形导轨和贴塑导轨板组成,动态性能更好; 在极限位置采用极限保护开关,保证安全性。在设计中,优化部件结构,改进原有通用部件的“十”字形加强筋为“米”字型加强筋,提高强度和刚性,提高数控滑台的结构稳定性。
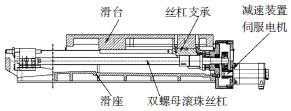
图2 右数控滑台装配图
数控滑台动力部分采用伺服电机驱动高精密双螺母滚珠丝杠的形式。在设备的使用中,为降低由于滚珠丝杠因温度变化导致运动精度变化对加工精度的影响,滚珠丝杠采用中空冷却设计,配合温度控制系统来改善热变形,同时在滑台上配置有光栅尺系统,对滑台运动精度进行双重保障。
数控滑台通过集中润滑系统,为导轨之间以及其他部分提供润滑。在导轨和贴塑导轨板之间形成油膜,大幅度降低相对运动时的摩擦系数; 润滑油的循环也能够起到降温控制热变形的作用。
2. 2 夹具
夹具是机床的核心部件,用于加工过程中对被加工零件的定位和夹紧。夹具的定位精度直接决定了产品的加工精度,夹紧的可靠性与否直接决定了产品在加工中的稳定性和加工质量。
设计中,采用一面两销[4]的定位方式,即选择一个平面和平面上两个定位孔作为基准,限制6 个自由度,配合辅助支承装置保障定位的准确性和稳定性; 夹紧通过液压夹紧装置实现,即液压油缸带动压板夹紧,配合辅助夹紧机构,保证夹紧的可靠性和安全性,定位夹紧原理示意图如图3 所示。
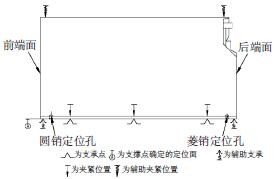
图3 定位夹紧原理示意图
夹具部件如图4 所示。定位块1、3、6 通过修磨定位块下的调整垫,保证高度尺寸满足80 ± 0. 01mm 要求,同时三个定位块组成的定位平面的平面度要求0. 01mm 以内,允差不超过0. 005mm; 辅助支承装置5、9、17,用于保障被加工零件的定位稳定性。
夹紧油缸2、4、7 对应的压板16、13、10 完成被加工零件的夹紧和松开; 辅助夹紧油缸12、14 带动辅助压板11、15,配合夹紧被加工零件,确保加工过程中的可靠性。
定位动作过程为: 被加工零件输送到上料位置,抬起落下装置20 处于上料姿态。机械手将被加工零件放置于抬起落下装置20 的支承块上,随后松开,完成上料动作; 同时抬起落下装置油缸19 启动,带动齿条向下运动,开始落下动作。落下过程中,首先,抬起落下装置20 落下一定高度,被加工零件的定位销孔落到对应的圆销装置18 和菱销装置8 上,此时系统进行让刀位置气动开关打开状态确认,如图5 所示,确认后滑台快进将刀杆引入,完成让刀; 之后,抬起落下装置20继续落下,被加工零件下落至由定位块1、3、6 组成的定位平面上; 最后支承块落下到位,被加工零件定位于定位平面,完成整个插销定位过程。
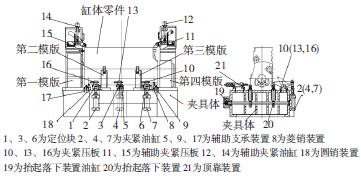
图4 夹具设计图
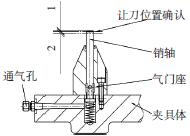
图5 让刀位置气动开关打开状态确认结构
被加工零件夹紧过程为: 被加工零件和抬起落下装置20 落下到位后,开关发令,顶靠装置21 启动靠紧动作,固定位置; 随后,夹紧油缸2、4、7 启动,推动对应夹紧压板16、13、10 压紧; 最后,辅助夹紧油缸12、14启动,推动对应的辅助夹紧压板11、15 辅助压紧被加工零件,完成夹紧动作。
2.3 模板
加工曲轴孔、凸轮轴孔时,悬伸的镗杆细而长,刚性差,受力变形严重,易产生振动和抖动[5],为提高镗杆的刚度,设置了模板。
模板又被称为镗模架,主要用于机床刀具加工时的导向和定位,是保证加工位置准确性的关键部件。本次设计有4 块模板,均固定在夹具体上,模板的主体采用铸造结构,分布有加强筋板,在满足刚度和强度的要求下,最大程度的有利于加工排屑。模板在夹具体上的装配图如图6 所示。
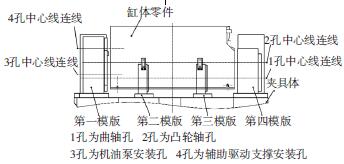
图6 模板在夹具体上的装配图
第一模板和第四模板分布于夹具体两侧,通过第一模板和第四模板上各孔的位置精度,来保证刀具的位置精度和所加工各孔的相对位置精度,同时模板上的导套还兼顾具有导向的作用。
被加工零件为六缸缸体,总长度超过1100mm,曲轴孔和凸轮轴孔又均为多档的间断长孔[6],跨距大,在第一模板和第四模板之间设置了第二模板和第三模板,又称之为中间模板。
为保证精度,除了采用精密三坐标加工之外,还设计了多个专用调整垫。安装时,修磨调整垫,保证模板的1 孔同轴度在0. 005mm 以内,模板的1 孔中心线连线与定位平面A 的平行度达到0. 005mm/1000mm,1孔中心线连线与定位块安装平面的高度范围在181. 6 ± 0. 01mm 内; 各模板1 孔中心线与定位销中心连线平行度达到0. 01mm 要求,尺寸范围在144. 46 ±0. 01 以内。同时确保模板上2 孔的同轴度达到0. 005mm 要求,保证2 孔与1 孔的平行度满足0. 005mm/1000mm。
由于第二模板和第三模板处于中间位置,为方便安装和维修,在设计中采用了分体设计的方法,即1 孔和2 孔在不同的模板分体上,通过修磨各自分体之间的调整垫,保证2 孔与1 孔的相对位置117. 476 ±0. 005mm 和143. 868 ± 0. 005mm 符合设计要求。
根据相关使用和维护经验,模板导向部分的精度要求很高,与刀具( 镗杆) 配合使用,磨损严重,更换繁琐,设计中将模板导向部分改为镶嵌导套的结构。以第一模板为例,如图7 所示。全部导套均采用可调式导套设计,在安装中,导套与模板通过配磨,调整两者的间隙达到0 ~ 0. 003mm 的设计要求; 导套与刀杆之间也采用配磨,调整两者间隙在0. 003 ~ 0. 008mm 之间。这种结构磨损后只需更换导套重新配磨即可,大幅度的减少材料的损失和调整时间,延长了模板使用寿命。
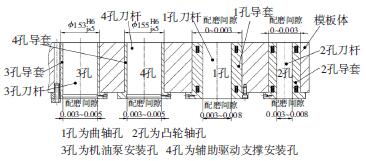
图7 第一模板镶嵌导套结构图
2. 4 机械手
机械手是敏捷物流系统的核心部分,主要负责被加工零件在上、下料位和加工位置之间的高效、快速、精确的输送。当被加工零件处于上料工位时,机械手自动抓取,将被加工零件放置到加工位置; 当加工完成后,机械手自动抓取加工后的零件,输送到下料工位,完成一次动作循环。
机械手结构图如图8 所示。机械手主要由运动部分和抓取部分组成,其中运动部分包括伺服电机1、减速装置2、直线导轨3、开关7、平衡油缸8 等,负责机械手的运动控制和保护。伺服电机1 启动后,通过减速装置2 进行变速,传递到直线导轨3 上,带动机械手抓取部分实现Z 轴( 即竖直方向) 的运动,Z 轴总行程为655mm,其中使用行程为653mm,备量为2mm; 开关7负责Z 轴方向运动的极限保护,当抓取部分随直线导轨到达极限位置时,开关7 发令,电机停止; 机械手不抓取被加工零件时,平衡油缸8 能够防止机械手由于重力而自行落下,避免部件损坏和安全隐患。
抓取部分主要由手爪5 和控制油缸6 组成。抓取被加工零件时,控制油缸6 带动手爪5 同时向内侧或外侧等速匀速移动,保持手爪5 对中性和被加工零件位置的对中性,确保在抓取和移动过程中的定位准确性。
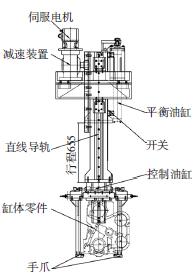
图8 机械手结构图
2. 5 刀具
在刀具加工形式选择时,考虑到被加工零件尺寸大、加工部分跨距大,加工时受力性等多方面因素,最终选择拉镗的加工形式。拉镗时,镗杆受到拉应力,能够保证加工过程的平稳性,有利于保证精度。镗杆自主设计,委托玛帕公司制造,镗杆示意图如图9 所示。
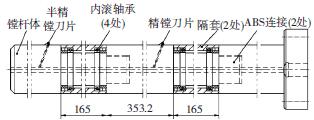
图9 镗杆示意图
镗杆上,半精镗刀片2 和精镗刀片4 分前、后装使用,采用向后排屑的刀片来排出铁屑,不会划伤被加工零件表面,保证光洁度。主轴孔采用精镗单元,车止推面的刀安装在加工曲轴孔镗杆上,确保被加工零件加工精度。受到被加工零件内部空间限制,凸轮轴孔镗杆中间部分支撑空间不足,设计中采用内滚轴承4,通过ABS 结构6 连接,在有限空间内给镗杆增加导套,起到扶持的作用,提高精度,提高线速度。
该三轴镗组合机床可用于精加工曲轴孔、凸轮轴孔、机油泵孔、辅助驱动支撑安装孔以及销孔。其中曲轴孔单边余量0. 3125mm,凸轮轴孔单边余量0. 3685mm,机油泵安装孔单边余量0. 3435mm,辅助驱动支撑安装孔单边余量0. 3685mm,销孔单边余量0. 2875mm。
曲轴孔加工刀具如图10 所示,刀具主要参数为:
半精加工V = 113. 4m/min,n = 300r /min,S =0. 112mm/r,Sm = 33. 6mm/min;
精加工V = 113. 7m/min,n = 300r /min,S =0. 112mm/r ,Sm = 33. 6mm/min。
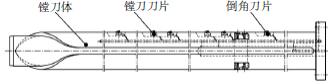
图10 曲轴孔加工刀具
凸轮轴孔加工刀具如图11 所示,刀具主要参数为:
半精加工V = 102. 6m/min n = 480r /min S =0. 07mm/r Sm = 33. 6mm/min;
精加工V = 102. 9m/min n = 480r /min S =0. 07mm/r Sm = 33. 6mm/min。
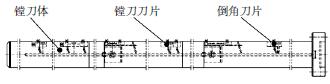
图11 凸轮轴孔加工刀具
机油泵安装孔加工刀具如图12 所示,刀具主要参数为:
半精加工V = 119. 4m/min,n = 300r /min,S =0. 1mm/r,Sm = 33. 6mm/min;
精加工V = 119. 7m/min,n = 300r /min,S =0. 1mm/r,Sm = 30mm/min。
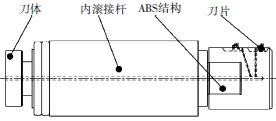
图12 机油泵安装孔加工刀具
辅助驱动支撑安装孔加工刀具如图13 所示,刀具主要参数为:
半精加工V = 125. 4m/min,n = 300r /min,S =0. 1mm/r,Sm = 30mm/min;
精加工V = 125. 7m/min,n = 300r /min,S =0. 1mm/r,Sm = 30mm/min。
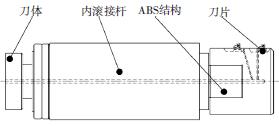
图13 辅助驱动支撑安装孔
2. 6 环保处理
随着社会的发展,三轴镗组合机床的发展不仅要求机床加工精度高、加工性能稳定,而且对加工过程中的环境要求也越来越高,绿色环保的加工理念已经成为普遍要求。
基于这样的发展理念,设计中,将电气、液压进行分散控制; 为降低加工过程中机床对环境的影响,本文介绍的三轴镗组合机床在整体防护的基础上,设计了机床加工区全封闭防护。
针对加工过程中所产生的废气、废水、废液及铁屑,也分别进行处理,利用安装在加工区域的吸雾装置,将产生的废气、油雾、水雾等第一时间收集,定期按照相关规定进行统一处理; 对于切削液和切屑,利用机床配备的上排系统,高压抽送到空中管路中,回液由于自身重力而流入过滤装置中,从而将切削液和铁屑相分离,进行相应处理。
3、应用情况
三轴镗组合机床安装后,先后开展了机械手调试试验,夹具定位夹紧试验,测试各动作灵活性、定位准确性和夹紧的可靠,刀具与模板的磨合试验,配磨导套与模板体、导套与刀杆之间的间隙; 设备空运转和试机,优化设备运行参数等。
表1 设备加工精度比较表
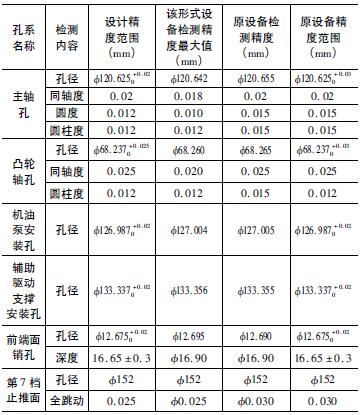
在完成以上试验之后,三轴镗组合机床在实际工况中进行连续切削,测试设备的自身的性能和产品加工精度。该设备连续加工后,检测加工精度,将各孔系加工最大值统一记录; 并在原有三轴镗组合机床进行相同试验,比较加工精度变化,如表1所示。
通过对上表的比较分析,可以得到如下结论:
( 1) 该形式三轴镗组合机床的连续加工试件均能够达到设计精度要求;
( 2) 该形式三轴镗组合机床与原设备相比,在主轴孔、凸轮轴孔和第7 档止推面的加工精度均有提高。综合以上结论,证明该形式三轴镗组合机床在的加工性能和加工精度方面得到提高,满足使用要求,设计达到预期目的。
4、结论
本形式三轴镗组合机床,以现有产品为基础,从方案设计入手,先后完成数控滑台的改造、夹具和模板的研究与设计、机械手的应用、刀具的设计与优化和绿色环保处理等工作内容,开展了相关试验、调试、生产,检测产品达到设计精度,设备满足使用要求; 通过与原有设备的加工精度比较,得到在主轴孔、凸轮轴孔和止推面的加工精度上均有提高,实现了预期设计目的。
三轴镗组合机床采用机械手物流,提高了敏捷物流系水平; 夹具、模板、机械手等核心部件从设计到加工均国产化,加快了三轴镗组合机床国产化步伐,促进了汽车发动机关键工序加工设备的研究和发展,由技术引进型向技术自主型转化,具有显著的经济效益和社会效益。
以该形式为基础的三轴镗组合机床在“锡柴重型柴油发动机缸体、缸盖柔性加工生产线示范工程( 课题编号2013ZX04012071) ”获得应用,发挥了巨大作用,受到了广泛认可。
[参考文献]
[1]王志兰,龚臣. BJ483 缸体三轴孔镗床加工方案的改进[J]. 机电产品开发与创新, 2011, 24( 4) : 161 - 163.
[2]宫德海,谭延林. 有关缸体缸孔精加工技术在汽车发动机中的应用[J]. 科技传播,2012( 1) : 138 - 139.
[3]李凡,张树礼. 发动机缸体缸盖加工自动线现状及发展趋势[J]. 现代零部件, 2014( 5) : 35 - 37.
[4]丁国琴. 柴油机气缸体三轴孔及曲轴止推面精镗床的设计[J]. 轻型汽车技术, 2003( 1) : 32 - 35.
[5] B Moetakef-Imani,N Z Yussefian. Dynamic simulation ofboringprocess [J] . International Journal of MachineTools&Manufacture, 2009( 49) : 1096 - 1103.
[6]罗刚,邓贤森,马慧斌. 论柴油机气缸体试制开发机加工工艺[J]. 装备制造技术,2010( 5) : 112 - 113.
( 编辑赵蓉)
投稿箱:
如果您有机床行业、企业相关新闻稿件发表,或进行资讯合作,欢迎联系本网编辑部, 邮箱:skjcsc@vip.sina.com
如果您有机床行业、企业相关新闻稿件发表,或进行资讯合作,欢迎联系本网编辑部, 邮箱:skjcsc@vip.sina.com
更多相关信息
- target=_blank>空芯轴式光源在机床照明中的应用
- target=_blank>VERICUT 软件构建五轴机床仿真模型的方法及应用
- target=_blank>基于不确定性测度的再制造曲轴平衡性控制方法
- target=_blank> 四方电气工控产品在自动对折缝边机上的应用
- target=_blank>内燃机缸套活塞环弹流润滑数值分析
新闻资讯
| 更多
- target=_blank>MB2120B型数控内圆磨床电主轴变频器的改造
- target=_blank>【雷尼绍】RESOLUTE™与MELSERVO-J5强强组合,实现更快速、精确、可靠的运动控制
- target=_blank>NSK开发低摩擦轮毂单元轴承 可增加电动汽车续航里程
- target=_blank>T68卧式镗床进给系统的数字化改造
- target=_blank>AGV+协作机器人在零件数控机床加工上下料中的应用
- target=_blank>2020年7月高端装备制造业、工业机器人,行业运行简述
- target=_blank>浅谈线切割机床中走丝与慢走丝
- target=_blank>ANCA整体PCD铣刀 —— 提高生产效率带来新的发展机遇
- target=_blank>伊斯卡,不止专注于金属加工
- target=_blank>EMAG成功收购Scherer Feinbau(舍勒公司),极大扩展了公司产品范围以及客户群体