280机车柴油机曲轴在船舶领域运用可靠性研究
2016-9-14 来源: 南车玉柴四川发动机股份有限公司等 作者:张伟华 刘云贵
摘要:针对280机车柴油机曲轴应用到船舶领域后出现疲劳断裂的问题,从该曲轴的结构及船用工况及工作特点,并结合断裂曲轴的理化分析,对该曲轴疲劳断裂的可能因素进行了分析,并据此制定了合理的改进方案。实践应用表明:曲轴结构改进设计后,不仅降低了加工难度,且提高了曲轴的可靠性。
关键词:柴油机;曲轴;加工;可靠性
0、引言
2010年南车玉柴四川发动机股份有限公司配属国内某航道工程局的一台16V280ZC/ZD型船用柴油机曲轴发生第二连杆颈断裂。经理化分析,该曲轴化学成分、力学性能、中频淬火淬硬层深度等均符合技术条件要求,该曲轴断裂是由于在连杆颈过渡圆角下方有大型夹杂物而引起疲劳断裂。但是,后期公司生产的该型船用柴油机曲轴在船舶运用过程中又陆续发生多起断裂事故,迄止2014年,该型船用曲轴共断裂10支。这些断裂的曲轴其断裂位置基本都在第四或第五连杆颈上,从疲劳裂纹的走向来看,是由主油道的工艺锥孑L扩展出来的。
本文针对该曲轴的应用工况及工作特点,并结合理化分析结果,对曲轴断裂的影响因素进行分析,并制定合理的解决方案。
1 、16V280ZC/ZD船用柴油机曲轴结构特点
船用柴油机工作时负荷突加、突卸情况较多,并且其运用工况较机车柴油机恶劣;同时由于工作特殊性,使得船用柴油机曲轴承受较大的扭转负荷。该16V280ZC/ZD船用柴油机曲轴是在16V280ZJA机车柴油机曲轴的基础上,根据船规要求进行强化设计的。相对于16V280ZJA机车用曲轴有以下变化:
(1)曲轴调质技术要求发生变化。根据船规要求:2008年起生产的船用柴油机,曲轴的性能试样从机车曲轴的自由端(冒口端)调整到了输出端(水口端);分体试棒改为连体试棒;机械性能指标按照船规要求进行了调整。
(2)曲轴连杆颈圆根中频淬火技术要求发生变化。要求船用柴油机曲轴连杆颈圆根中频淬火强化处理。事实上,从1998年生产16V280ZJA机车曲轴以来,图纸上均要求连杆颈圆根淬火,但是因为热加工不易控制,淬火后变形,并且,冷加工主油道加工质量差问题一直没有得到解决,所以该方案一直没有得以实施。现在因为船用曲轴要求强化程度高,必须要求曲轴连杆颈圆根中频淬火强化处理,因此,对曲轴工艺提出了工艺提升的要求。
2、16V280ZC/ZD船用柴油机曲轴断裂特点
断裂后的16V280ZC/ZD船用柴油机曲轴返厂后,由公司的检测中心对其断裂原因进行分析。
由于这些曲轴断裂的位置及状况均相似,故以其中一例来说明断裂情况。该曲轴编号为ZJ2008C一1025#,曲轴的断口形貌见图l。
断口形貌表明:该曲轴为疲劳断裂,疲劳裂纹走向比较复杂,分别向轴颈及曲柄臂扩展,在断裂曲柄臂的工艺锥孑L位置有一条裂纹,从疲劳裂纹的走向来看是由工艺锥孔扩展出来的。从该曲轴的断口形貌分析,可以判断是由于交变弯曲应力过大造成的疲劳断裂,疲劳源于曲柄臂的工艺锥孔与连杆颈的交接位置。由曲轴的工作状态分析,该位置受力最大。
在工艺锥孔处打开裂纹,发现疲劳源位于工艺孔的锥度面的交接位置,疲劳源处有明显的应力撕裂棱,见图2。从工艺锥孑L的表面观察,加工质量较差,见图3。
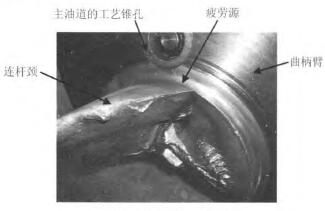
图1 曲轴的断口形貌
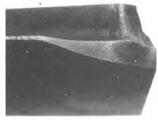
图2疲劳源区形貌
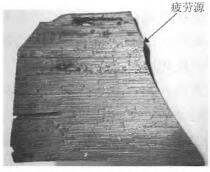
图3工艺锥子L;bn工质量
从曲轴断裂的方式来看,该曲轴除受正常的扭转弯曲应力外,可能还受到了比较大的附加应力。复杂的应力状况造成疲劳裂纹在圆根附近起源后同时向曲柄臂和轴颈方向扩展。而加工质量差可能导致应力集中而萌生疲劳源。
3、断裂原因分析及改进措施
3.1 原因分析
公司相关部门展开了多方面的分析,查找可能造成曲轴断裂的原因,开展了现场柴油机使用情况调研,失效分析,加工质量核查及设计分析工作。
(1)现场调研
现场了解:挖泥船一般使用工况下,柴油机转速范围在880~930(r·min。1);而在挖泥流量保持恒定(一般处于泥泵最大流量)的情况下,柴油机曲轴所受扭矩基本处于柴油机输出扭矩的最大范围;加上挖泥工况不稳定(泥浆浓稠度变化、泥浆泵出El节流变化等),轴系对中不好等问题,造成曲轴承受较大附加应力,可能导致曲轴疲劳断裂。
(2)失效分析
收集了5支断裂曲轴的热处理工艺及力学性能检测资料,均未发现异常。曲轴均是由于旋转弯曲应力过大引起的疲劳断裂。
(3)加工质量
经检测发现,16V280ZC/ZD船用柴油机曲轴断裂处油孔附近的加工质量差,粗糙度极差,造成后续淬火时该处易产生裂纹。在船机应用过程中弯曲应力过大时该处易产生疲劳源,引起疲劳断裂,与断裂曲轴的失效分析情况相符。故制定措施提高16V280ZC/ZD船用柴油机曲轴主油道的表面粗糙度质量。但是由于眭轴加工设备及热处理工艺的局限性,表面粗糙度质量问题始终得不到解决。
(4)设计计算分析
经过专业咨询公司的计算分析,该曲轴在理论工况下疲劳强度满足设计要求(不考虑加工质量影响、热处理状况等因素)。
3.2制定合理改进方案
综上所述,制定了三条具体改进措施:①明确用户对中情况要求,指定了在保修期内的船机安装情况检查计划,要求按照计划核实舱内泥泵柴油机对中情况,并对对中情况不符合要求的柴油机重新对中或要求用户立即实行停机整改;②明确后续船机均应激活限定功能;③由于加工质量方面仍存在问题得不到解决,受冷、热加工局限性的影响,该曲轴需要进行优化设计。
在设计方面:决定对16V280ZC/ZD船用柴油机曲轴做取消主油道孔的结构改进设计,以降低加工难度,减少疲劳源产生。设计优化方案为:取消贯通自由端到输出端的主油道,将整体油道结构改为每曲拐单独油道结构,改进前后结构见图4、图5。为了适应总体结构要求,必须对斜油孔进行改进,为了避免改进后结构影响曲拐强度,彻底放弃传统的交叉斜油孔结构,改为单侧斜油孑L结构,并设计为连杆颈偏心直油孔。
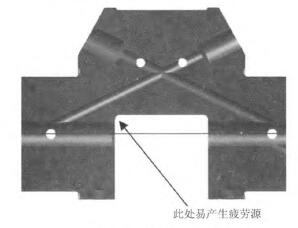
图4原整体式油道结构
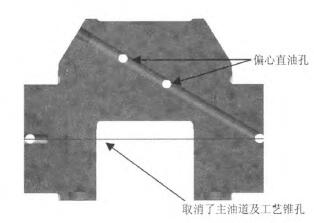
图5 改进后单独油道结构
3.3优化后相关计算校核
模拟16V280ZC/ZD船用柴油机曲轴在实际工况下动态应力情况,建立曲轴连杆机构动力学分析模型,见图6。考察曲轴设计方案工作情况,并进行疲劳寿命预测,借助有限元方法进行安全评估。
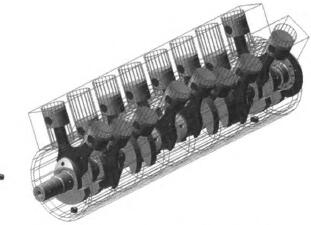
图6 曲轴连杆机构动力学分析模型
3.3.1 总体要求
强度考核指标:曲轴工作在安全许可应力范围内,小于材料许用应力。
疲劳考核指标:疲劳安全系数>1.5。
3.3.2计算结果
在l 000(r·min。1)标定功率下曲轴动态应力计算结果:各拐最大应力均位于曲柄销斜下方,最大动态应力较原方案的218 MPa(第4拐)略有降低,为190 MPa(第5拐),其各拐具体应力值见表1。
表1 优化前后最大动态应力值对比

动态应力分析表明:曲轴最大动态应力190MPa,小于屈服应力637 MPa,处于设计许可应力范围内。疲劳强度计算表明:曲轴疲劳安全系数为2.08,大于设计许可安全系数1.5。因此在标准工况下长期运行能保证曲轴的疲劳可靠性。
3.4简化工艺
采用每曲拐单独油道设计后,可取消原采用专机粗加工、镗床铰制的主油道长孑L加工工序;取消主油道油封组装工序,降低了加工难度,彻底解决了最初因为加工设备局限问题造成主油道表面及锥孔口粗糙度极差的惯性质量问题;并使曲轴的加工周期缩短。采用无主油道、连杆颈单侧油孔结构后,可减少斜油孔压套、斜油孔螺堵、主油道油封、拉杆螺栓等附件的生产、组装,节省了设备、刀具及人力资源。
4、结束语
2013年,首根16V280ZC/ZD船用柴油机曲轴试制成功后,安装在国内某船用柴油机上进行运行考核,公司售后服务部进行了为期一年多质量跟踪,反馈使用情况良好。2014年3月后进行了扩大化试装十根。至今,总体运用状况良好,未发生曲轴疲劳断裂的事件,达到了预期目标,实现了280机车柴油机曲轴在船舶领域的可靠运用。
投稿箱:
如果您有机床行业、企业相关新闻稿件发表,或进行资讯合作,欢迎联系本网编辑部, 邮箱:skjcsc@vip.sina.com
如果您有机床行业、企业相关新闻稿件发表,或进行资讯合作,欢迎联系本网编辑部, 邮箱:skjcsc@vip.sina.com
更多相关信息
- target=_blank>让沈鼓五年节省三千万 hyperMILL®是怎么做到的?
- target=_blank>细长轴加工工艺设计
- target=_blank>伊斯卡高速铝加工铣刀在航空工业的应用
- target=_blank>轴类零件多功能全自动智能测量仪的设计木
- target=_blank>复合材料螺旋桨纤维铺层对强度影响研究
新闻资讯
| 更多
- target=_blank>MB2120B型数控内圆磨床电主轴变频器的改造
- target=_blank>【雷尼绍】RESOLUTE™与MELSERVO-J5强强组合,实现更快速、精确、可靠的运动控制
- target=_blank>NSK开发低摩擦轮毂单元轴承 可增加电动汽车续航里程
- target=_blank>T68卧式镗床进给系统的数字化改造
- target=_blank>AGV+协作机器人在零件数控机床加工上下料中的应用
- target=_blank>2020年7月高端装备制造业、工业机器人,行业运行简述
- target=_blank>浅谈线切割机床中走丝与慢走丝
- target=_blank>ANCA整体PCD铣刀 —— 提高生产效率带来新的发展机遇
- target=_blank>伊斯卡,不止专注于金属加工
- target=_blank>EMAG成功收购Scherer Feinbau(舍勒公司),极大扩展了公司产品范围以及客户群体