柴油机曲轴断裂失效的3种常见原因
2016-12-15 来源:武汉大学动力与机械学院 作者:陈勇 贺小明
摘要:曲轴断裂危害极大,所以寻找曲轴断裂失效的一般性原因非常有意义。通过对4起失效曲轴的外形、断口、机械性能、硬度梯度、化学成分和金相组织等进行分析。分别介绍热处理、原材料、机加工等原因对曲轴各项性能的影响。方便各厂家改进曲轴的生产与修理。
关键词:曲轴;断裂失效;热处理
1.曲轴断裂失效的共性特点
80%的曲轴失效是疲劳断裂.其起因是初始疲劳裂纹。若应力集中的位置同时存在表面不连续。就易诱发初始疲劳裂纹的产生。本文研究的4起曲轴断裂事故都是疲劳断裂。研究疲劳断裂的原因和过程时。通常先分析疲劳断口.一般可清晰地分辨出3个区:疲劳源、疲劳扩展区和瞬断区。
2.曲轴断裂的3种常见原因
2.1 热处理不当导致的曲轴失效
曲轴在热处理时,先后有纤维锻造、正火、调质和氮化处理等工序.能很好地改善曲轴材料的金相组织和各项性能。若不当,则可能引发曲轴早期失效。某柴油机工作698h后。输出端飞轮强烈摆动。紧急停车拆检.发现曲轴第1个主轴颈出现了明显裂纹。
(1)外形分析将曲轴沿主轴颈与曲柄方向割开。发现其裂纹源在其主轴颈的表面,如图l所示,在A位置有1个深褐色小断面.应是锻造时遗留的折叠层,为最早开裂的断面,位于曲柄工艺孔下面的轴颈圆角根部。分析形成原因:①曲轴在组装并工作一定时间后,该位置产生了小裂纹。机油渗入,由于高温产生了焦油痕迹:②曲轴在淬火前就存在该小裂纹,淬火时水玻璃溶液渗入。形成了该区域。
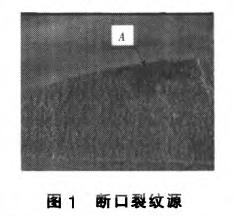
(2)微观分析使用电子探针来检测断VI,发现裂纹最初位置在曲轴表面的氮化层。在该位置也没有发现明显的夹杂物或其他缺陷。断口的晶粒有大有小.混晶现象十分明显。而产生混晶的原因主要就是热处理不当。用电子探针检测裂纹源的深褐色区域.发现上面有很多孔洞,放大观察,无撕裂棱等韧性断裂的特征。观察晶粒走向.为沿晶断裂,曲轴材料有过热的脆性倾向。
观察裂纹扩展区,如图2、图3所示,为典型的解理断裂特征.裂纹呈放射状。清楚分辨出河流状的花样。如图2所示,断口上发现有“人字形”花纹,图中有2个箭头:解理台阶和裂纹源的方向。分析断口特征,裂纹源产生后,发展迅速,且无大的塑性变形.脆性断裂特征清晰。如图2所示,可清晰看到二次裂纹.这是由于裂纹扩展速度大,在顶部产生了塑性区.导致二次裂纹的产生。二次裂纹不断扩大。部分裂纹扩大方向与裂纹源整体方向完全不一致.导致解理台阶的产生。总结分析结果。该曲轴为典型的脆性断裂。
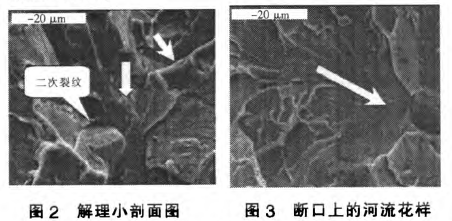
(3)硬度梯度检测从裂纹源处取样,测量轴颈表面和主轴颈圆角表面的硬度梯度。测得曲轴基体组织的硬度为HRC25(约HV270)。一般认为:与之相比.大于HV50的位置即为氮化层;达到HV550的位置。为有效硬化层。测得主轴颈圆角表面的氮化层约0.4 mm,有效硬化层的厚度约O.15 mm:主轴颈表面的氮化层的厚度约0.55 nlln.有效硬化层的厚度约0.2 mm。可见主轴颈圆角位置的氮化情况要坏于主轴颈表面的氮化情况.但总体情况尚可。
(4)曲轴的金相组织从主轴颈的基体组织中取样分析,为大量的铁素体、贝氏体和较少的回火索氏体所组成.且组织粗大。金相组织里的奥氏体的晶界清晰并呈平直状.这和失效断口的微观分析的结果相同,贝氏体也清晰并粗大,为羽毛形状,为典型的上贝氏体组织。但根据曲轴机械性能的要求.经过热处理后.需要的基体组织应是回火索氏体及较少的贝氏体。
(5)分析讨论曲轴基体组织中存在大量的铁素体和上贝氏体.且二次裂纹与混晶组织明显.为不合格的金相组织。产生原因主要是:热处理时正火不充分,保留了部分锻造组织。淬火不当导致了不良组织形态。导致曲轴的各项力学性能较差,屈服强度、基体硬度以及冲击韧性都达不到设计标准。曲轴中奥氏体的晶界平直.且有二次裂纹的产生.所以该失效曲轴有相对过热的可能。过热会导致缓冷生成的组织粗大,使得冲击韧性或硬度等静态指标降低。更致命的是会大大降低疲劳强度等动态性能指标。由于曲轴在锻造后的正火不够充分.加上淬火时奥氏体的温度太高.使得部分第二相粒子融人奥氏体中。第二相粒子分布较少的区域,晶粒较粗大;分布较多的区域.晶粒比较细小。奥氏体组织的晶粒大小不匀,导致混晶现象,使得曲轴材料的性能不均匀。曲轴材料为35CrMoA钢.正火后其组织应该由珠光体及铁素体。淬火后.期望其组织为马氏体及少量贝氏体所组成。但从该曲轴断裂位置的金相分析结果显示.其基体组织为回火索氏体和大量的铁素体及上贝氏体。大量的铁素体和上贝氏体的存在。是因为曲轴在淬火冷却时不足所致。正是由于这些不良组织,使得曲轴的强度和硬度大大降低。韧性减小,各项力学性能指标下降.特别是具有方向性的贝氏体铁素体群的析出。大大降低了冲击韧性。铁素体和贝氏体的晶粒越大,位错越小,钉扎现象越差,利于裂纹扩展.使得各项性能显著降低。金相构成影响曲轴的塑性和韧性等性能.若上贝氏体比例过高。会大大降低冲击韧性。贝氏体中的铁素体大小和碳化物的形态及分布决定了贝氏体的韧性。下贝氏体中.碳化物分布于贝氏体铁素体片内.且非常微小.在两者交界位置不易形成裂纹。假若出现解理裂纹.扩展时会被两者的高密度错位所阻碍.所以下贝氏体的冲击韧性较大.且由韧转脆的温度也较低。而在上贝氏体里,铁素体是平行分布的。呈束状,每个束可以理解为一个有效晶粒。且在上贝氏体中.碳化物是在贝氏体铁素体间连续分布,尺寸也较大。所以碳化物与贝氏体铁素体交界位置容易产生微裂纹.其一旦出现。就能引发解理裂纹。使裂纹快速扩大。
由此可推断。该柴油机曲轴失效的原因主要是:曲轴原材料在锻造时.在第一主轴颈与曲柄相接的圆角位置遗留了折叠层,为最初的裂纹源。同时由于淬火时的不当.使得曲轴的硬度、强度和冲击韧性等性能都有较大下降。当柴油机工作时.交变应力使得裂纹源失稳.加上热处理得到的组织不合格.使得裂纹扩展迅速,达到一定大小后,释放出部分应力,使得裂纹以撕裂状迅猛扩大。
2.2原材料因素引起的曲轴失效
提高曲轴原材料的各项性能是减少曲轴失效的重要方法。合金材料中的每个组元都会影响材料性能。冶炼材料时,除了会加入所需元素外.同时还无法避免地带入一些有害元素。有害元素分2类:①冶炼时带人的一些气体元素,例如:氧、氢、氮等:②其他一些非金属元素,比如:磷、硫等。而且原材料在冶炼时所遗留的偏析、疏松、杂质等缺陷也非常影响材料质量。
某柴油机工作时.润滑油压力骤降.呼吸器有润滑油渗出。拆捡发现。曲轴在第2、第6缸连杆轴颈的中间位置发生了断裂。
(1)断面分析裂纹源在2个油孔的开口位置.油孔粗糙度较大.表面裂纹的产生方向和曲轴的最大切应力方向一致.在断H可清晰地看到疲劳贝纹线(见图4),刚开始比较密集,随着裂纹的扩大,贝纹线的间距也慢慢增大。而疲劳断裂的重要特征就是清晰的贝纹线.因此可推断该断裂为多源疲劳断裂。在断面上可找到3个裂纹源,2个在油孔位置,1个在轴颈表面.然后分别朝心部和轴柄方向扩大。
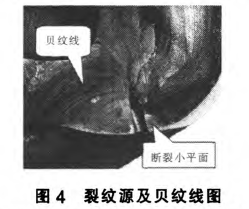
(2)氮化层分析从曲轴未磨损处取样测得,氮化层的硬度为HV。3575,厚度为0.3 rain,均达到设计标准。
(3)机械性能测试与金相组织分析从连杆轴颈上取样测量各项机械性能,结果为:抗拉强度879 MPa、屈服强度718 MPa、断面收缩率62.1%、延伸率18.7%、硬度HB290~300,均合格。从裂纹源处横向取样分析金相组织.其构成为:回火索氏体和较少的贝氏体.为合格的金相组织。
(4)曲轴材料化学成分分析从曲轴没有被破坏的基体组织中取样.检测化学元素组成。可发现材料中硫元素和磷元素的含量均低于0.025%.铜元素的含量低于0.20%,均达标。但是分析氢元素的含量,3个试样中氢元素的含量分别为:3.6 ppm、2.5ppm、2.6 ppm,平均值为2.9 ppm。
(5)失效原因讨论金属材料中氢元素为有害元素,会降低各项性能,只需1.0 ppm的氢含量就会使金属的脆性显著增加。氢元素和金属元素相互作用。使得金属变脆,较常见的氢脆有:氢蚀、氢化物致脆、白点和氢致延迟断裂等。氢元素在钢里面的溶解度较低.含量高于溶解度就可能产生白点。但因为钢内部本身有很多缺陷,缺陷表面都能吸附氢,所以一般氢含量小于2 ppm时,不会产生白点,但曲轴在工作时承受各种复杂应力.使得氢元素会向应力较大的区域转移,导致这些区域的脆性升高,引发断裂的发生。
氢元素含量超过2.7 ppm时.钢就很可能产生裂纹。该曲轴中氢元素含量最大达到了3.6 ppm,平均值也达到了2.9 ppm.超过了相关文献中所介绍的第2类氢脆极限(1~1.5 ppm)。所以可推测。该曲轴材料应该已经引发了第2类氢脆。氢元素更大的危害是使材料发生延迟破坏。是指:即便曲轴所受的应力较小。氢元素也会慢慢扎堆。使得基体原子之间的结合力减小,导致韧性降低,脆性升高,引发脆性断裂。所有证据都表明:该曲轴的断裂与原材料中氢元素的含量过大有直接关系.氢元素含量过大导致了原始裂纹源的生成.最终引发曲轴断裂。因此厂家在生产曲轴时,也应该选择氢元素含量较低的钢。同时。锻造后的热处理也非常重要。合金元素含量较大的钢.对氢元素更为敏感。所以应该按照钢在冷却时的金相转变特征来选择除氢方法。锻造结束后,应及时进行热处理。然后进行正火及除氢退火等工艺。前者使钢组织中的晶粒变小.后者使氢元素含量减少到最低并使其均匀分布.从而避免氢元素含量过大所引发的曲轴脆性增加。
2.3机械加工不当导致的失效
机械加工时遗留的加工缺陷,如粗糙度过大、遗留刀痕或残余应力过大等.会极大影响曲轴质量。某曲轴断裂事故.拆检后发现断裂位置处于输出端第1个连杆轴颈与曲柄相接的圆角位置.观察断口为典型的疲劳断裂。裂纹源在连杆轴颈内侧的圆角位置。在该断裂曲轴的连杆轴颈圆角位置.发现了比较严重的磨削加工时所遗留的刀痕.且该处粗糙度为1.2 la,m。而图纸标准为0.4¨m,可见粗糙度远远超标。
检测曲轴材料的化学成分均达标;分析金相组织,为回火索氏体和较少的贝氏体及铁素体.正常。所以可肯定导致该失效的原因是:严重的磨削加工所遗留的刀痕。以及圆角位置过大的粗糙度。另一柴油机发生了曲轴断裂失效事故。检测曲轴材料的化学成分均达标:金相组织为回火索氏体和较少的贝氏体及铁素体,正常。
测量其表面粗糙度:主轴颈表面粗糙度为0.23 la,m,设计标准为O.20 Ixm.尚可。主轴颈圆角位置的粗糙度0.75 p,m,图纸标准为0.4 la,m,远远超过了设计要求。仔细观察.发现主轴颈圆角位置有两段圆弧。这很反常.测得其大圆弧半径为R5.6 mm.在其大圆弧的中间位置有-d,段小圆弧,半径为R3.6 mm.而设计要求此处过度圆角的半径为R6.0 mill。并且要求圆滑。回顾这2起事故,其曲轴材料均合格.热处理也恰当.但在2起事故曲轴的圆角位置。都找到了机械加工时所遗留的缺陷:第l台是在机械加工时。留下了严重的磨削刀痕.且圆角处粗糙过大;第2台是在应力最为集中的圆角位置居然有2段圆弧.且过渡圆的半径大小也没能达标。正是这些刀痕和加工失误.使得在圆角位置的应力高度集中.随着工作时间的增多.就产生了疲劳裂纹源,最后导致曲轴断裂。
3.结语
(1)曲轴的早期断裂失效形式基本上为疲劳断裂:
(2)连杆轴颈、主轴颈与曲柄圆周相接的圆角位置是曲轴所受应力最大的位置。因为过渡圆半径较小(一般要求为6 mm)且加工及处理都比较麻烦.导致应力集中现象明显,容易产生裂纹源;
(3)油孔位置也是曲轴的薄弱位置。开口的加工质量、形状及尺寸都直接影响曲轴的疲劳强度。若加工或维修时处理不好。留下了刀痕或其他缺陷,会带来应力集中。导致疲劳裂纹的生成:
(4)曲轴原材料的氢元素含量对后续工艺及各项性能有直接影响。若原材料里氢含量高于2 ppm,就会大大增加曲轴的脆性.极易导致曲轴发生早期断裂失效
(5)曲轴在淬火后冷却不够及时和充分,会产生大量的铁素体和上贝氏体,导致曲轴强度、硬度和冲击韧性等各项静态性能大大降低.更会使曲轴的抗疲劳强度等各项动态性能大幅降低:
(6)曲轴正火时不够充分或温度过高,会使形成的奥氏体晶粒大小不一。且晶界平直.还会生成具有方向性的上贝氏体和铁素体,使曲轴的各项性能变差;
(7)锻造曲轴时若在圆角位置遗留了折叠层,就极易导致曲轴在这些位置开裂,甚至断裂:
(8)圆角位置的机械加工质量直接影响曲轴的疲劳强度。若曲轴在生产或者大修的磨削处理时,在这些位置遗留了加工刀痕.就会带来严重的应力集中,大幅降低曲轴的疲劳寿命。
投稿箱:
如果您有机床行业、企业相关新闻稿件发表,或进行资讯合作,欢迎联系本网编辑部, 邮箱:skjcsc@vip.sina.com
如果您有机床行业、企业相关新闻稿件发表,或进行资讯合作,欢迎联系本网编辑部, 邮箱:skjcsc@vip.sina.com
更多相关信息
- target=_blank>基于粒子均衡的移动传感器网络覆盖控制研究
- target=_blank> 毂帽鳍的节能机理分析
- target=_blank> 航空发动机内部损伤智能诊断系统研制
- target=_blank>世界级冲压车间技术
- target=_blank>发动机火花塞的使用与维护
新闻资讯
| 更多
- target=_blank>MB2120B型数控内圆磨床电主轴变频器的改造
- target=_blank>【雷尼绍】RESOLUTE™与MELSERVO-J5强强组合,实现更快速、精确、可靠的运动控制
- target=_blank>NSK开发低摩擦轮毂单元轴承 可增加电动汽车续航里程
- target=_blank>T68卧式镗床进给系统的数字化改造
- target=_blank>AGV+协作机器人在零件数控机床加工上下料中的应用
- target=_blank>2020年7月高端装备制造业、工业机器人,行业运行简述
- target=_blank>浅谈线切割机床中走丝与慢走丝
- target=_blank>ANCA整体PCD铣刀 —— 提高生产效率带来新的发展机遇
- target=_blank>伊斯卡,不止专注于金属加工
- target=_blank>EMAG成功收购Scherer Feinbau(舍勒公司),极大扩展了公司产品范围以及客户群体