加工中心可靠性维修周期的研究
2018-5-17 来源:转载 作者:张丽萍,李业农,赵建杰
摘要: 为了建立加工中心的最佳维修周期与有效度之间的数学模型,以确定最佳维修周期,通过对立式加工中心常见故障的类型及原因分析,建立了平均故障率与规定考察时间之间的关系曲线,分析出了加工中心的平均故障率随着时间的增加而逐渐增大,建立了预防性维修即事前维修与事后维修的可靠性维修间隔时间模型; 基于平均故障率函数为递增函数,按有效度为最大时可求出最佳维修周期,并通过实例,运用可靠度函数的数值积分方法,计算出了加工中心的最佳维修周期。研究结果表明,所建立的计算方法为数控机床的最佳维修周期的确定提供了一种有效途径。
关键词: 加工中心; 可靠性; 平均故障率; 维修; 有效度; 预防性维修周期
0、 引言
某中小规格的立式加工中心,其 x、y、z 轴的行程分别为 600 mm、400 mm、500 mm。它的主传动采用主轴电动机,同步齿形带结构,三向导轨均采用高速化滚珠丝杠,其传动噪声低。该型加工中心的可靠性不仅与其自身的结构设计、制造、装配等因素有关,还与其加工条件、生产环境和操作工人的技术水平等因素有关。该加工中心结构和工作条件的复杂性导致其故障模式多样性,使其故障的演变过程有其一定的规律性,其可维修性也是衡量该产品质量好坏的一个关键指标。
由该加工中心的子系统或零部件引发的故障,经过修理后能够使故障排除,并恢复到正常工作的状态,所以该加工中心是一个可修复系统。由于故障发生的部位不同,产生的原因和程度不同,维修人员及使用的维修设备不同,加工中心的修复时间是一个随机变量,修复质量的高低也影响着加工中心的可靠性水平。
在工程应用领域,可靠性和维修性结合起来被称为可修复系统的广义可靠度。可修复系统可靠性特征量主要是首次平均无故障工作时间和平均无故障工作时间、平均修复时间、修复率和系统的有效度。可维修性是设备本身的一个性能,它包含于产品的可靠性设计中。
如何能合理地确定加工中心的最佳维修周期,给加工中心提供良好的维修,可以改善、维持或提高加工中心正常工作状态,能够最大地发挥加工中心的工作能力,这是笔者所要研究解决的问题。
本研究通过建立加工中心的最值维修周期与有效度之间的数学模型,以确定最值维修周期。
1、 加工中心常见故障分析
该型立式加工中心常见的故障可分为机械系统故障和电气系统故障。机械系统故障主要有主传动系统故障、进给运动系统故障、刀具自动交换装置故障、液压及润滑系统故障、排屑系统故障等等,这类故障主要发生在数控机床主机的各运动的执行机构上,如主运动系统的主轴、各坐标轴方向的进给运动、自动换刀装置中的刀库及机械手、等等。
对于机械系统故障,一般可通过精心保养和维护来降低故障发生的频率。当故障发生以后,小故障可通过精心调整来解决。对于已磨损或已损坏的零部件,须通过更换零部件的办法来排除故障。
电气系统故障通常分“强电”故障和“弱电”故障。“强电”故障主要指电动机、接触器、继电器、熔断器、行程开关等电器元件及电路方面的故障。“弱电”故障主要指 CRT 显示器、CNC 装置、伺服单元、输入输出装置等方面出现的故障。这部分故障又可分为软件故障和硬件故障,软件故障主要有加工程序出错、运算或动作出错等; 硬件故障主要有集成电路芯片、接插件以及外部连接组件等故障。
2 、发生故障的概率模型
加工中心的可靠度函数 R( t) 值是随着使用时间的增加而逐渐降低的,而发生故障的概率侧是随着使用时间的增加而逐渐增加的。故障率 λ( t) 是指使用到某时间尚未发生故障的设备在该时刻后单位时间内发生故障的概率,λ( t) 是一条件概率。由于按定义计算 λ( t) 是比较困难的,常用平均故障率的观察值予以替代,平均故障率的观察值是指数控机床在规定的考察时间内,故障发生的次数与累积工作时间之比,其数学表达式为:
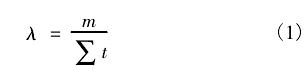
式中: λ— 平均故障率的观察值; m— 在规定的考察时间内,数控机床发生故障的次数; ∑t— 在规定的考察时间内,数控机床累积的工作时间。
通过较长时间对多台该型号加工中心的观察与统计,得到平均故障率 λ 与规定的考察时间 t 的曲线如图1 所示。
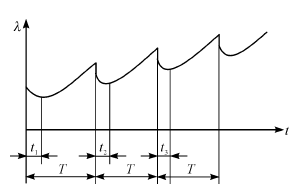
图 1 平均故障率 λ 与规定的考察时间 t 的曲线
如图 1 所示,对应于 t1为加工中心的跑合阶段,由于元器件和材质的缺陷、各零部件间的调整不当、加工质量等原因引发的早期故障,平均故障率 λ 呈较快的下降趋势。对新投入使用的数控机床,使故障减少的有效途径是加强跑合阶段的使用和维护管理,严格执行有关的跑合规定,可有效提高其使用寿命。
然后,加工中心进入正常工作阶段,随着数控系统故障、电气系统故障和零部件的疲劳、磨损、腐蚀及蠕变等典型损伤的积累,引起操作系统失灵和运动部件的爬行、抖动,至使加工中心的加工精度下降。此时,平均故障率 λ 逐渐增大,如图 1 中 T 阶段所示。加工中心工作到 T 阶段,平均故障率 λ 增大,此时应对加工中心进行预防性维修。要对存在故障隐患的零部件进行维修,还要对相的部位进行预防性处理,以使其保持良好的工作状态。
在维修过程中,零部件的工作位置可能会发生改变,应通过反复调试,使其达到正常的工作状态。第一次维修后,加工中心的功能得到恢复或部分恢复,平均故障率 λ 下降,维修后的t2阶段,由于维修导致各零部件间的重新装配,新更换零部件的材质和元器件缺陷等原因引发维修后的早期故障,同样会使该阶段的平均故障率 λ 较高,但呈较快的下降趋势( 如图 1 所示) ,加工中心再次进入正常工作阶段,重复上述的过程。加工中心工作到第二个 T 阶段,平均故障率 λ 增大,须再次对加工中心再次进行预防性维修。
上述讨论的平均故障率是用以表征加工中心总体可靠性的数量指标,它着重表述的是加工中心平均故率的变化情况。
3、 可靠性维修周期的确定
在加工中心工作过程中,不仅工作可靠性,而且各项加工精度和经济指标都会随着工作时间的增加而逐渐下降。因此,生产企业要重视对加工中心各项加工精度和经济指标的变化规律的研究,适时对加工中心进行预防性维修,以保证其加工精度达到要求。
在加工中心的维修实践中,故障发生后进行修理,即事后维修,其在经济上或技术上付出的代价,往往要大于预防性维修。其原因是由于故障发生的随机性,如在工作过程中突然发生的故障,还可能会引发相关的从属故障,所造成的损失往往会更大,维修所付出的代价往往会更高。由此看来,预防性维修的好处是不言而喻的。当故障率随工作时间的增加而增加时,适时地采取预防维修措施,可有效地抑制加工中心的工作状况恶化,维持或恢复其完好工作状况。为使加工中心的维修工作在预防方针指导下,做到技术与经济相结合,很重要的一点就是确定其维护和修理的具体时刻,即何时维修最优的问题。一种有效的做法是按加工中心的有效度达到最大的原则来确定最佳维修周期。
对于加工中心这类可维修产品,由于无故障工作与故障停机是交替发生的两种状态,为此用 X( t) 表示在 t 时刻的状态,即:
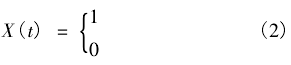
式中: 1— 设备在 t 时刻处于无故障工作状态,0— 设备在 t 时刻处于故障停机状态。现以图 1 为例,当加工中心工作到 T 时刻,实施预防性维修,所用维修时间为 tp,修复后投入工作。如果工作到 T1(T1≤ T) 时刻就发生故障,须事后维修,事后维修的时间为 tc,修复后再工作至 T2,且 T = T1+T2,再进行预防性维修,其可靠性维修间隔时间如图 2 所示。有效度 A 是指可维修产品在规定的条件下使用,在规定的条件下修复,在规定的时间具有或维持其规定功能处于正常状态的概率。在某个规定的时间区间内,有效度 A 可表示为:
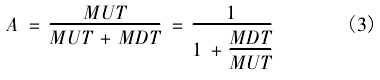
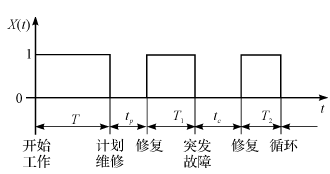
图 2 可靠性维修间隔时间
式中: MUT——— 加工中心的平均可工作时间( Mean UpTime) ,MDT——— 加 工 中 心 的 平 均 不 可 工 作 时 间( Mean Down Time) 。加工中心的平均不可工作时间 MDT 由平均预防性维修时间 tp和平均事后维修时间 tc的加权求和得出,即:
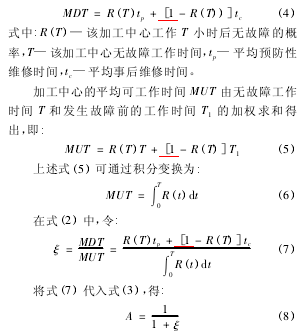
在式( 8) 中,当 ξ 值为最小时,有效度 A 有最大值。
由于图 1 所示平均故障率函数为递增函数,故可按有效度 A 为最大时求出最佳维修周期 T。
如图 1 所示的案例中,平均预防性维修时间tp=4h,平均事后维修时间 tc= 9 h,加工中心的可靠度R( t) 曲线如图 3 所示。
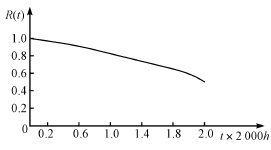
图 3 加工中心的可靠度 R( t) 曲线
根据式( 6) ,通过数值积分可求出与 t 相对应的 ξ值( 图解如图 4 所示) ,其计算结果如表 1 所示。
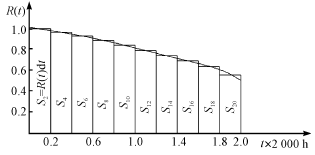
图 4 可靠度函数积分式图解
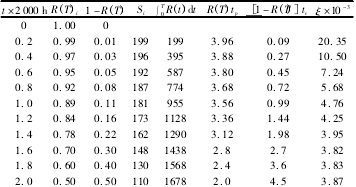
表 1 数值积分计算表
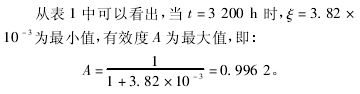
与最大有效度 A 对应的时间 T = 3 200 h 就是最佳维修周期。加工中心需要通过维护和修理来维持和恢复其完好工作状况,若其发生故障或性能下降,可通过维修加以恢复,缩短其不能工作的时间,使其具有较高的有效度。
4、 结束语
本研究通过对某型立式加工中心常见故障的类型及原因分析,揭示平均故障率与规定的考察时间之间的变化规律。对于加工中心这类可维修产品,其平均故障率随工作时间的增加而增加,如果适时地采取预防维修措施,可有效地维持或恢复其完好工作状况。基于可靠性理论,根据预防性维修即事前维修与事后维修的维修间隔时间模型,按有效度最大的原则可计算加工中心的最佳维修周期,这对提高数控机床的维修水平有一定的实践意义.下一步要深入研究加工中心的定期维护保养策略,尤其是关键部件的故障危害度,以提高加工中心可靠度维修保养的水平。
来源:南通职业大学 机械工程学院,南通科技投资集团股份有限公司
投稿箱:
如果您有机床行业、企业相关新闻稿件发表,或进行资讯合作,欢迎联系本网编辑部, 邮箱:skjcsc@vip.sina.com
如果您有机床行业、企业相关新闻稿件发表,或进行资讯合作,欢迎联系本网编辑部, 邮箱:skjcsc@vip.sina.com