力臂调节器薄壁套筒螺旋导程槽加工改进
2019-6-24 来源:中航工业贵阳万江航空机电有限公司 作者:汪奎
摘要:分析了薄壁套筒零件外圆螺旋槽的建模和加工方法。通过UG软件与四轴联动加工中心的完美结合,为类似零件的数控加工提供了新的路径与技巧。
1. 产品结构和加工难点
图1所示产品为全晶体力臂调节器,主要功能是调节飞机机翼的水平平衡,用于多种机型的歼击机和其他机种。组成产品的零部件及元器件中,薄壁套筒(见图1b)是一个重要件,它装在产品内部,不外露。其外圆上的三处螺旋导程角是加工中的难点。
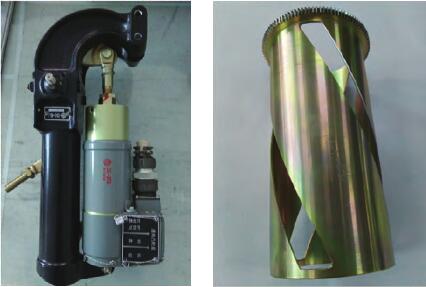
图1 全晶体化力臂调节器
图2 所示为该套筒的外形 尺寸 , 其结构特点是 : ①零件壁薄 , 最薄处尺寸仅为0 . 925 mm 。②外圆上沿 120 °方向均匀分布 3 处螺旋槽 , 槽宽为(10±0.008)m m,螺旋槽的 导 程 角 是 26 °± 5 ′ , 根部R0.5 mm ,表面粗糙度值R a =0.4 μ m 。③薄壁外圆一端要插齿,模数m=0.5,齿数z=108,压力角α=20°,齿顶高系数ha*=1,径向间隙系数c*=0.2,精度等级6h(GB 2363—2005)。④零件材料为30Cr Mn Si A(GJB 2609 — 1996 ),热处理硬度 41~45H R C,表面处理镀铬5~8μm。
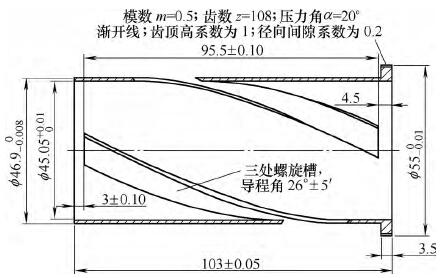
图2 薄壁套筒外形尺寸
薄壁套筒的加工难点为:①薄壁件刚性较差,加工过程中产生的振动导致表面质量差,产生变形,不好保证精度。②薄壁件在外圆上插齿,插齿过程中产生的范成运动、切削运动和进给运动容易导致零件变形,齿轮精度不好保证,尤其是齿形误差易受影响。③材料为30Cr Mn Si A,属于中碳钢,有较高的综合机械性能,且热处理硬度较高,加工中刀具磨损严重,生产效率受到影响。
2. 传统加工方法及缺点
传统的加工方法是做专用夹具在普通铣床上加工,图3所示为专用铣床夹具,其加工原理是:把零件定位在夹具上并夹紧,手工摇动夹具手柄,带动夹具的丝杠传动,零件的运动有两种,在转动的同时向前移动,套筒上的每一点都在进行螺旋转动。在每个完整的螺旋槽加工过程中,刀具只是固定地转动,不进行坐标移动。
传统加工的缺点为:①质量不稳定。螺旋槽的宽度尺寸取决于刀具的直径,刀具直径不合格或在加工过程中发生磨损会影响槽宽精度尺寸,加工中产生的颤动容易导致表面质量差。采用传统的加工方法,尺寸精度最好只能达到±0.02m m,表面粗糙度值R a=1.6~3.2μm,要达到最终设计要求,只能采用手工研磨抛光的方法。②刀具磨损严重。由于零件材料为30Cr Mn Si A淬火中碳结构钢,加工中刀具磨损严重,每加工8~12件零件就需更换刀具。由于刀具的直径直接决定了槽宽的尺寸,通用刀具很难达到加工要求,这就需要准备大量的专用刀具,不但刀具制造成本高,而且给管理和库存带来很大的麻烦。③废品率和超差品率高。传统加工的废品率每批次约5 % ~ 8 % ,超差品率 1 2 % 。废品率造成了较大的质量损失,超差品率造成了较高的返工成本,一旦尺寸超差,只能通过钳工抛光的方式进行返工,加工效率低,返工成本高 , 每返工 1 件需要20m i n,增加了制造成本(小时费用率)。
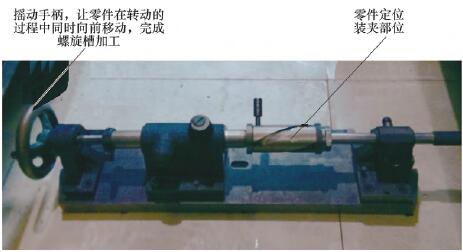
图3 传统加工专用铣床夹具
3. 毛坯类型和设备选择
薄壁零件具有质量轻 、节约材料和结构凑的优良特 点 。 为了提高材料利用率 , 零件外形尺寸为f 55mm /f 45.05m m×103m m,毛坯采用管状材料 , 尺寸为f 58mm /f40mm×105mm,材料利用率约55.6%。设备选择CNC系统为Mazak的四轴联动加工中心FJV-250(见图4),主要是考虑到该机床加工范围较大,内部功能较强,摒弃传统铣床夹具的加工方式,通过一次装夹自动走刀实现三处螺旋槽的加工,此外,该设备还具有如下特点:①加工的适应性强、灵活性好,能加工轮廓形状比较复杂或难以控制尺寸的零件,如本例中薄壁槽宽(10±0.008)m m 。②能用数学模型描述复杂的曲线零件及三维空间的曲面类零件,如本例中的三处空间螺旋槽的角向尺寸26°±5′。③加精度高,加工质量稳定,尺寸一致性好以及减轻操作者的劳动强度,可以有效避免本例中刀具磨损后的槽返工周期及返工成本。
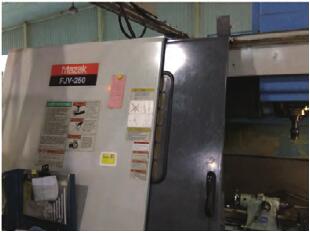
图4 四轴联动加工中心
4. 模型的建立
齿槽宽三维模型的建立是比较关键的,也是UG编程中比较生僻的环节,对初学编程的人员来说有一定的难度。特别是缠绕曲线和扫掠成形,更是三维模型建立的难点和重点。
(1)螺旋槽宽边界线段的形成和缠绕曲线。坐标原点移至端面截面的最顶点,在XOY平面内沿X 向画一条26°线并派生直线,生成宽度为10mm的两条槽宽边界线段。U G软件插入→来自曲线集的曲线→缠绕/展开曲线。选择曲线:两条槽宽边界线段(见图5上面两条曲线);选择面:圆柱体外圆柱面;指定平面:X O Y 平面(两线段所在平面),确定并生成两条沿圆柱体的缠绕曲线(见图5下面两条曲线)。
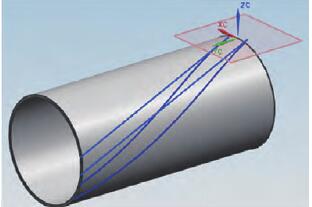
图5 槽宽边界线段的形成和缠绕曲线
(2)螺旋槽轮廓界面的建立及模型的形成。首先,要画出扫掠界面。在端面顶点沿垂直于边界线段构成的平面内画对称矩形界面,矩形的宽度为槽宽1 0 m m ,宽度方向只需保证高出圆柱顶面和低于内孔顶面即可(便于扫掠后进行布尔运算)。其次,UG模型界面中插入/扫掠/扫掠→截面选择曲线:端面界面框;引导线选择曲线:选择一条缠绕线;定位方法:选择另一条曲线/点另一条缠绕线,确定并形成螺旋槽实体轮廓(见图6)。
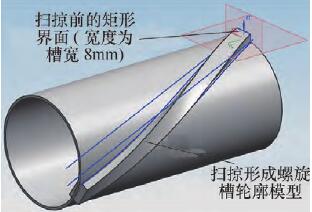
图6 螺旋槽轮廓界面的建立及模型的形成
(3)阵列螺旋槽轮廓模型并布尔运算形成螺旋槽。首先在端面截面均布阵列三处螺旋槽轮廓模型。用实例几何体指令,类型选择旋转,选择对象:点已生成的缠绕体;指定矢量:-XC(将坐标原点移动到端面中心,沿轴线方向的坐标);指定点:端面中心点;角度120°、副本数2。布尔运算中的求差方法形成三处螺旋槽,再运用建模、裁剪及布尔运算补全其他部位(见图7)。5. 刀具的选配刀具的选配主要考虑通用化和降成本。①普通A型f4mm钻钻中心孔,目的是为后续刀具进行引导,防止刀具偏移,保证下刀点对整个外圆的对称度。在加工中,刀具刚开始受工件力的影响很大,容易发生偏移,导致钻孔时孔的误差较大,达不到设计要求公差范围或起不到良好的引导作用,用A4中心钻先预打一个小孔或凹槽,钻头的头部沿着此小孔或凹槽钻下去,保证四周受力均匀,减少误差。②普通f 6mm钻头钻孔,目的是在螺旋槽圆柱体外圆的最高点部分钻出一个空间区域,为后续立铣刀粗加工创造出下刀的均匀受力空间区域。③通用立铣刀f 8mm粗铣槽,槽的最终尺寸是10mm,留2mm余量(单边1mm)进行最后精铣。④通用立铣刀f 3mm沿螺旋槽内壁四周走一圈,精加工至最终尺寸。通过引导→钻引导空间区域→粗加工→精加工步骤和精加工中移动轨迹的闭路循环,完全可用通用铣刀代替专用刀具,既降低了成本,也避免了刀具损耗带来的加工和返工困扰。
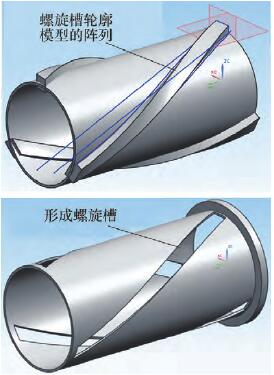
图7 布尔运算形成螺旋槽并补全其他部位
6. 程序的优化
在保证质量的前提条件下,追求高效率和避免动作浪费是企业生产改善的追求方向,本程序只需建立4个操作即可完成整个螺旋槽的加工。
(1)中心钻引导操作(用钻孔操作“DRILLING”)。这个操作的注意点是:防止中心钻断裂。中心钻一般由高速钢材料制成,钻孔部位直径比较小,实际加工中易折断(数控加工过程中折断是不易被发现的),加工中要加润滑液,利于切屑的排出,保证通畅不被卡住或折断。进给速度150m m/m i n,主轴转速2 500r/min,切削速度200mm/min,逼近速度2 000mm/min,进刀速度1000mm/min,移刀速度3 000mm/min。
(2)钻出引导空间区域操作
(用钻孔操作“DRILLING”)。
本操作很简单 , 其目的就是在铣刀下刀点钻出一个f 6 mm孔的空间区域 , 保证铣削 力度均匀 。 进给速度 2 0 mm /min ,主轴转速 2500 r / min ,切削速度 250mm / mi n , 逼近速度2 000m m/m i n,进刀速度 1000 mm / min 、 移刀速度4000mm/min。
(3)粗加工操作(用型腔铣“CAVITY_MILL”)。加工出整个螺旋槽的外形形状,留少许余量最后成形。主轴转速5 500r/m i n,切削速度1 800m m/m i n,逼近速度3 000mm/min,进刀速度800mm/min,第一刀切削速度800m m/m i n,移刀速度5000m m/min。
( 4)精加工操作(用平面铣“PLANAR_MILL”)。沿封闭的螺旋槽四周精加工一圈,完成整个螺旋槽的最终形状尺寸要求。主轴转速6000r/min,切削速度2500mm/min,逼近速度3000 mm / min , 进刀速度 1 200m m/min,第一刀切削速度 1200 mm / min , 移刀速度 5000mm/min。
程序的编制因个人的编程风格和习惯不同,没有一个标准模式。以上操作中的切削参数不是唯一的,仅供参考。
7. 加工结果
尺寸精度分布区域表
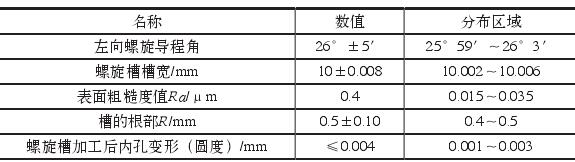
经过多年的加工,零件质量稳定,尺寸参数在规定的公差区间合理分布(见附表),外观质量美观,可靠地解决了薄壁类套筒零件螺旋导程槽的加工和质量问题,为该类零件的加工提供了新的方法和技巧。该类零件无论是军用、民用还是应用于其他领域,都很普遍。
8. 结语
该零件批量大 , 经多年的加工验证,其尺寸精度、表面粗糙度、几何误差、生产效率和装配性能在传统的基础上都得到很大的提升。对操作者的要求也不高,只需具备金属切削加工基础知识(如刀具材料、切削数据和冷却方式等)和了解CNC数控系统的构成和工作方式(如调试、刀补及程序调用等),即可自行建模、自行编程和自行加工。
投稿箱:
如果您有机床行业、企业相关新闻稿件发表,或进行资讯合作,欢迎联系本网编辑部, 邮箱:skjcsc@vip.sina.com
如果您有机床行业、企业相关新闻稿件发表,或进行资讯合作,欢迎联系本网编辑部, 邮箱:skjcsc@vip.sina.com
更多相关信息