在线测量技术在精密磨床中的应用
2018-2-26 来源: 中航工业北京航空精密机械研究所 作者:张东亮,梅国平,姜新生,陈宇
[摘要] 通过为数控精密磨床装配雷尼绍测头,详细介绍了在线测量在数字控精密磨床系统的构成、工作原理、数据处理方法以及磨削实验结果,使其具备在线测量功能,实现了产品的测量、加工一体化。
[关键词] 数控磨床;在线测量;数据处理
引言
数控加工一般采用离线测量模式,工件加工完成后需要搬运到检验部门进行检验,这种测量方式工件需要重新找正、设定原点,人为因素带入一定的误差,影响测量精度;工件在搬运、装卡过程中也容易出现变形与磕碰;造成操作工人劳动强度高,生产效率低。在线测量指工件加工完成后不拆卸,通过与机床集成在一起的测量系统直接对其进行测量,检验加工是否合格,这种方式可解决离线测量中存在的各种问题有效提高加工效率。
精密磨床集成在线测量功能后,可实现工件内廓面测量成形、加工 G 代码自动编程、磨削量自动检测等功能,使数控磨床成为测量、加工一体化设备。本文介绍了实现精密磨床在线测量需解决的测量坐标系建立、工件曲面建模、工件测量加工 G 代码生成等关键技术问题,并通过磨削试验验证了精密磨床在线测量功能。
1 、在线测量精密磨床系统构成
精密数控磨床系统构成如图 1 所示,其包含 X、Y、Z 三个直线轴和 C 轴、电主轴两个旋转轴,其中 C 轴上装卡工件,通过 X 轴、Z 轴、C 轴三轴联动实现在线测量和磨削加工;电主轴上安装磨头,可以以最高 12000r/h 转速对工件进行磨削加工。
测头为雷尼绍手动旋转测头,分辨率为 0.001mm,其优越的三维测量性能与高精度光栅尺相配套,可保证产品测量的准确度。旋转测头可以克服因被加工产品长,被测空间小所带来的死区,提高测量效率。测头安装在测量杆上,信号通过数控系统快速 I/O 接口引入,以提高测量精度。测头接触工件瞬间可触发中断,数控系统通过 MEAS 命令记录当前坐标值,并记录到测量文件中。通过测量轨迹规划,可实现工件内阔面测量,测量结果作为加工 G 代码自动编程依据,通过加工前后测量结果对比可检验磨削量是否合格。
精密数控磨床为高精度机床,任何误差引入系统都将影响加工精度,本系统安装光学成像设备作为对刀系统,通过调整高精度光学镜头,可将测头和磨头在同一焦距下放大数倍,并将图像上传至上位计算机,分别记录测头和磨头中心点坐标值,找到二者之间相对位置关系,即可建立测量坐标系和加工坐标系。上位计算机采用高配置工作站,完成测量轨迹规划、测量 G 代码自动编程、测量结果曲面拟合、加工 G代码自动编程、加工结果校验等大数据计算处理工作,同时提供人机交互界面,实现加工参数设定,加工 G 代码仿真执行,操作记录等功能。
840D 数控系统执行测量和加工 G 代码,通过多轴插补运动实现工件的测量和磨削加工。
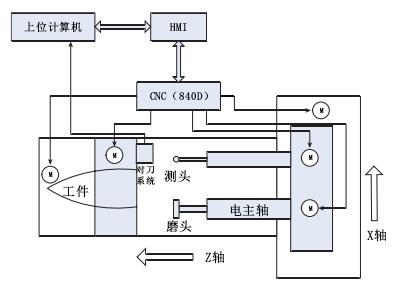
图1 精密数控磨床系统构成示意图
2、测量、加工坐标系建立
工件测量和加工都是基于工件母线曲线方程,其原点位于工件顶部,所以进行加工前需建立以该原点为基准的测量坐标系 G54、加工坐标系 G55。精密磨床光学对刀系统如图 2 所示,通过固定在磨床上的基准块和光学成像系统,找到测头和磨头与工件坐标原点之间相对位移,进而建立测量坐标系、加工坐标系。
① 在安装基准块时准确测量其 X、Y、Z 三个方向与工作坐标原点的坐标差值,并通过销钉将其固定在床身上,确保二者坐标差值固定不变。
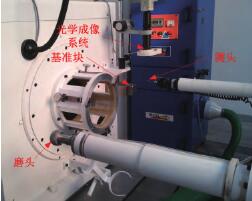
图2 精密数控磨床光学对刀系统图
② 测头测量基准块 X、Y、Z 三个端面,数控系统自动记录测头中心点坐标值,通过与基准块坐标差值计算,得到测头相对于工件坐标原点位移,在数控系统中设置坐标偏移值,建立测量坐标系 G54。
③ 通过光学成像系统找到测头中心点与磨头中心点 X 向、Z 向坐标差值,通过与测量坐标差值计算,得到磨头相对于工件坐标原点位移,在数控系统中设置坐标偏移值,建立加工坐标系 G55。
3 、数据处理方法及加工 G 代码生成
精密数控磨床通过对工件上分散点的测量得到点云数据,运用最小二乘法进行母线方向及圆周方向两维曲线拟合,得到被测工件回转体曲面。依此为基础,结合刀具(磨头)自身特点,根据加工参数自动生成加工 G 代码,保证加工精度。加工完成后可对加工区域再次进行测量,验证加工效果,检测加工误差,若误差超出了要求,可对未达标区域进行再加工,直到满足加工要求。
对工件内廓面精密测量和修磨加工是数控磨床两大最基本功能,数据处理是将测量和加工联系起来的桥梁,同时也是按要求精密修磨的关键。
数据处理的任务是将测量的数据进行曲面建模,建立加工基面,在此基础上根据加工去除量和刀具轨迹规划生成加工 G 代码,完成对工件的修磨加工。曲面数字化修磨数据处理流程如图 3 所示:
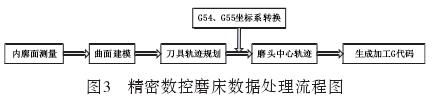
图3 精密数控磨床数据处理流程图
① 内廓面测量
对工件加工区域进行测量的过程如下:测头沿一条母线按等步长采集测量数据完毕后,工件沿圆周方向等间距旋转,使测头沿另一条母线采集数据,重复上述过程,依次遍及整个测量区域。
② 曲面建模
对工件内廓面进行测量之后得到一系列离散数据点,根据工件加工工艺要求,找到所有测量点中距离内表面理论点最高的一个点,以这个点位基准勾勒出距理论内表面等距的一个虚拟曲面,然后在此基础上根据各点的去处量自动生成加工 G 代码。
针对工件在圆周方向上的圆度已达到较高精度且加工区域在母线上曲率变化较平缓这一特点,采用最小二乘法曲线拟合的方法,即根据测量数据点,求出一个
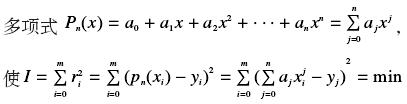
将每条测量母线的X坐标与Z坐标进行三次多项式曲线拟合,根据母线方向拟合曲线的数据将圆周方向的 X 坐标与 C 坐标进行三次多项式曲面拟合,两个方向的拟合曲线即组成了工作基面;然后根据磨削去除量再沿着工件基面的法线方向计算出加工基面。以拟合加工基面方程为基准并依据工艺参数以及测头和磨头半径在法向方向上进行半径补偿,就可以得到磨头中心坐标曲面。最终根据加工精度计算母线方向加工步距和圆周方向加工步距,规划刀具轨迹,构成加工基面的型值点集合,生成加工 G 代码。
③刀具轨迹规划
精密磨床采用螺旋线形的环切刀具轨迹遍历内廓形,加工过程中磨头在工件内由里向外,先控制磨头伸到工件的靠顶端处第一个螺旋环第一个节点处,通过控制工件在 C 向旋转和磨头 X、Z 向微动,三轴联动来完成第一圈修磨;第一圈的终点即为第二圈的起点,同样由工件旋转和磨头微动三轴联动完成第二周的加工,依次完成对整个内廓面的修磨。
4 、数控磨床磨削加工试验
在线测量数控磨床在加工完成后可通过测量系统验证加工精度:将加工区域内每条测量母线加工前后的测量结果相减,得到各条母线加工值,如图 4 所示:
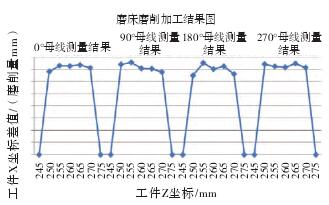
图4 精密数控磨床加工结果数据图
加工范围:Z 向(工件母线方向)30mm,坐标范围245~275mm;磨削量:0.07mm,即工件母线的 X 向(磨削进给方向)磨削前后坐标差值;圆周采样步距:90°,即在圆周方向每隔 90° 取一条母线进行测量,共采集 4 条母线数据(0°,90°,180°,270°);母线采样步距:5mm,即沿母线 Z 向每隔 5mm 采集数据,每条母线上得到 7 个数据;图 4 横坐标为 4 条母线的 Z 坐标;图 4 纵坐标为加工前、后测量点 X 坐标的差值,即磨削去除量;每条母线上方的角度值表示该条母线在圆周方向的位置。
可以看出,工件内表面的磨削是以近似相等的去处量进行的,误差控制在 ±0.01mm 以内,该误差影响因素包括:①雷尼绍旋转测头 0.006mm 测量精度;②直线轴 0.007mm 定位精度;③对刀系统误差、装卡误差等。
5 、结论
在线测量技术应用到精密数控磨床中,实现了产品的测量、建模、加工一体化,节省了工件搬运、重复装卡的工时,提高了产品测量、加工精度,经实际应用其加工精度能控制在 ±0.01mm 以内,同时该设备降低了工人劳动强度,显著提高了生产效率。可以预见,在线测量技术在数控机床中的广泛应用会成为发展趋势。
投稿箱:
如果您有机床行业、企业相关新闻稿件发表,或进行资讯合作,欢迎联系本网编辑部, 邮箱:skjcsc@vip.sina.com
如果您有机床行业、企业相关新闻稿件发表,或进行资讯合作,欢迎联系本网编辑部, 邮箱:skjcsc@vip.sina.com