基于有限元分析的磨床床身优化设计
2018-8-21 来源:上海理工大学 机械工程学院 作者:王强,季懿栋,李志荣
[ 摘要 ] 利用有限元分析软件 ANSYS 对磨床床身模态分析,通过试验测定的模态频率与仿真值进行对比,对有限元模型进行修正,借助于 ISIGHT 软件对床身进行了单目标及多目标优化设计。仿真结果表明,单目标优化设计可将床身重量减少10.06%,多目标优化设计可将床身重量减少4.38%,且床身应力、导轨最大变形量、固有频率均有改善。
[ 关键词 ] 磨床头架;有限元分析;拓扑优化
0 、引言
磨床床身是磨床中一个非常重要的部件,起着支撑工件和连接工作台、桥板等关键零部件的作用,磨床床身的静刚度和动态特性直接影响到被加工零件的质量,并与磨床床身的整机性能有着密切关系。磨床床身的设计尺寸和布局形式,决定了其静态和动态特性的优劣,为实现磨床床身轻量化、高精度、高效率的目标,对磨床床身进行优化设计十分必要。郭春星等采用整体优化和分层优化的方法分别对床身结构进行优化设计,达到降低床身自重的目的,结果表明:分层优化技术可有效解决设计变量较多的复杂结构优化设计。曾亚平等通过对低阶固有频率和振型的研究得出床身变形特点,从而得到床身结构刚度的薄弱环节,得出优化设计方案。但以上研究都是以轻量化为单一目标,忽略了对床身应力、导轨变形量等的研究,且与实际测量值误差较大。因此,本文同时考虑床身的静态和动态特性,结合试验值对有限元模型进行修正,以轻量化为目标同时兼顾床身应力、导轨变形量等方面,通过优化床身的结构来实现轻量化的目标。
1、 床身有限元分析
1.1 床身几何建模
磨床床身是一个大型复杂结构件,由砂轮架、头架、尾座等组成。本文研究的某型号外圆磨床床身由灰铸铁铸造而成。磨床床身长 2 760 mm、宽 1 690 mm、高 580 mm。前磨床床身上有 V -平型导轨,导轨总长 2 670 mm,前磨床床身内部有 6 块横隔板,后磨床床身内部分别有 3 块横隔板和 3 块纵隔板,磨床床身底面则由 10 块垫铁支撑。为有效减少模型单元数量,从而减少计算时间,降低分析成本,提高分析效率,可对原床身模型进行简化。研究表明,在建模时去掉部分凸台、螺钉孔、圆角等对分析结果影响不大。最终建立的简化后的磨床床身的有限元模型如图1 所示。
1.2 材料属性、网格划分及边界条件设置
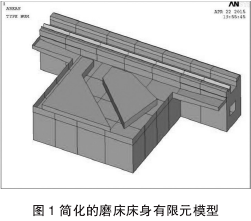
1.2.1 定义材料属性
磨床床身由铸铁 HT250 铸造而成,HT250 的密度为 7 200 kg/m3 ,弹性模量为 110 000 MPa,泊松比为 0.28,屈服强度为 250 MPa。
1.2.2 网格划分
选择合适的单元能使建模简单化。考虑到床身的薄壁结构,ANSYS 中的壳单元适合于床身的建模,因此选择 SHELL181 单元来建立床身和SOLID186 单元建立导轨。床身和导轨是两个相对独立的部分,需要通过节点耦合的方式将其耦合在一起,从而实现模拟磨床床身与导轨的连接。网格划分时,选择适当的网格大小对有限元分析非常重要,网格越细,分析出的结果越接近实验测量,但运算量及运算时间也随之上升。为了使划出的网格形状整齐,本文首先将每条线段按照每段 0.02 mm 划分成小段,然后选择自由划分,网格划分之后共生成 67 977 个单元和 83 703 个结点。
1.2.3 边界条件
床身采用 10 个地脚螺栓固定,地脚螺栓位置分布如图 2 所示,固定处限制所有自由度。
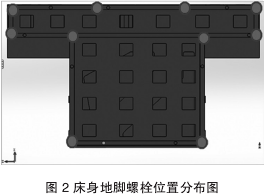
1.2.3 床身模态分析
对于磨床床身而言,模态分析非常重要,通过对机床磨床床身的模态分析,得出机床的各阶模态频率,可以避免磨床床身受载后发生共振,减小因共振带来的损失。表 1 所示为仿真得出的各阶模态频率与试验测得的各阶频率,从表 1 中可以看出仿真值与试验值误差较大,这是因为仿真时忽略了床身与地基之间的接触刚度,因此有必要对有限元模型进行修正。
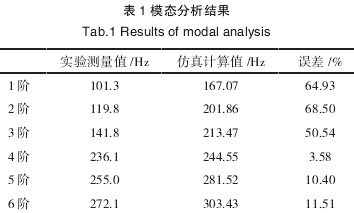
2、有限元模型修正
由于忽略床身与地基之间的接触刚度导致的仿真精度较差,本文通过弹簧单元 COMBIN14 模拟床身与地基之间的接触刚度。为确定弹簧的刚度,将模态分析得出的每一阶频率与实验测量值求差的平方求和作为目标函数。因为磨床床身电机频率大概为 50 Hz,为了避免共振,应确保第1 阶模态频率高于电机频率,所以第 1 阶频率的比重最大,需要给第 1 阶频率加权。将弹簧刚度作为设计变量,第 1 横排结合面采用弹簧型号 1,刚度为 K1;第 2 横排结合面采用弹簧型号 2,刚度为 K2;第 3 横排结合面采用弹簧型号 3,刚度为 K3。对磨床床身结构进行优化设计,其数学模型为
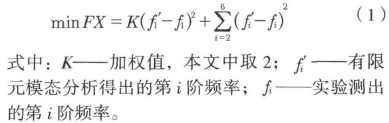
建立数学模型后,运用计算机辅助优化平台ISIGHT 进行优化求解,优化设计流程如图 3 所示。ISIGHT 针对不同的数学模型提供了很多种不同的算法,本文采用 ASA 自适应模拟退火法、MIGA 多岛遗传算法、Pointer 算法三种算法进行优化分析。
表 2 为三种优化算法计算出的各阶频率最优值与试验测量值误差的对比。将表 3 与表 1 对比可知,采用弹簧单元模拟床身和地基之间的刚度对有限元模型修正后,仿真计算出的各阶频率与试验值的误差大大减小。由于磨床床身中影响刚度最重要的因素为第 1 阶频率,应该取第 1 阶频率误差最小的算法结果,所以 MIGA 算法的结果最为合理,可将 MIGA 算法计算出的弹簧刚度用于后续的优化计算中。
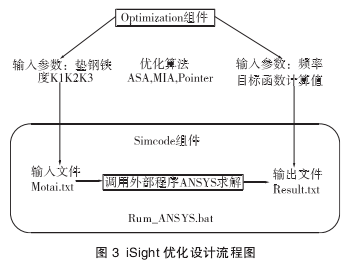
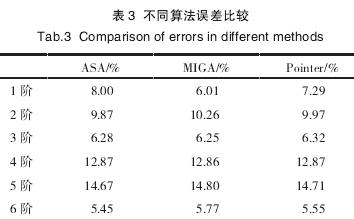
3、单目标优化设计
轻量化是对构件进行设计时,在满足使用要求的情况下,尽可能地减少材料,从而使得产品尽可能轻。在当今的产品设计中,轻量化设计和轻量化材料所起的作用越来越重要,尺寸优化是最经典的优化技术,当产品或者零部件的结构形式已经确定下来,只需要确定一些规格尺寸和参数即可。尺寸优化含有 3 种变量,分别是设计变量、状态变量以及目标变量,本文采用的是尺寸优化。
3.1 床身尺寸优化设计数学模型
如图 4 和图 5 所示,X1 为磨床床身外板的厚度。X2 为前磨床床身与后磨床床身相接筋板的厚度。X3 为磨床床身内筋板的厚度。如图 6所示,T1-T5 分别代表不同筋板到第一块筋板的距离。
综上所述,可建立如下的优化模型:
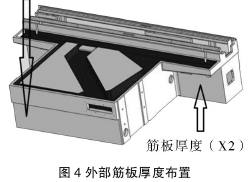
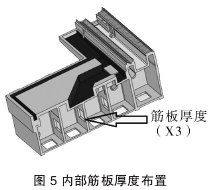
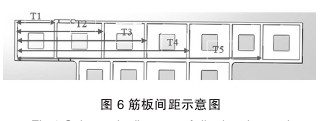
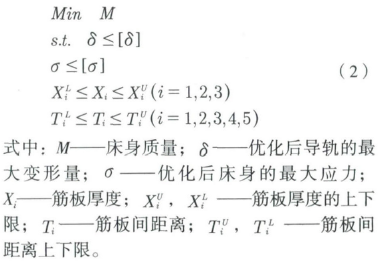
3.2 优化结果分析
图 7 为尺寸优化流程图。首先对不同参数下的有限元模型进行有限元分析,得到分析结果。通过优化算法寻优,直到满足算法设置的要求,优化求解过程结束,如果不满足则返回进行进一步求解。本文采用的优化算法是 ASA 自适应模拟退火法。
表 4 为计算得出的各设计变量的最优值及最优值与试验值的对比。从表 4 中可以看出,虽然磨床床身最大应力提高了,但是仍然在能够满足要求的范围以内,而导轨的最大变形量有所减小,精度稍微提高了一些,同时磨床床身质量减少了10%。结果表明,床身在满足要求的情况下质量减小,同时提高了加工精度。
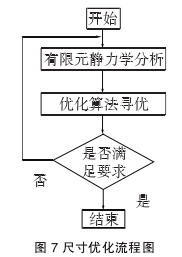
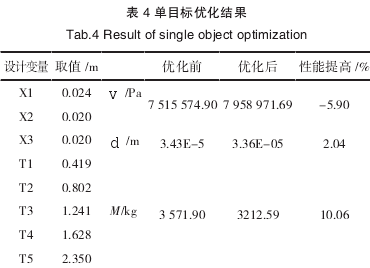
4、 床身多目标优化设计
在实验测量优化问题中,大多数存在多目标,且目标之间一般是互相冲突的。对多个子目标同时实施最优化的问题称之为多目标优化问题,又称多准则优化问题、 多性能优化问题或矢量优化问题。
4.1 床身多目标优化设计数学模型
在实验测量中,磨床床身尺寸的设计不能只考虑单方面的目标。比如为了避免磨床床身与电机发生共振,第 1 阶模态频率必须高于电动机频率。又为了保证磨床床身的精度,导轨的最大位移尽可能小。同时,磨床床身总质量也越小越好。但是以上 3 种要求是相互矛盾的,所以希望能够计算出综合考虑的最佳结果。综上所述,可建立如下的优化模型:
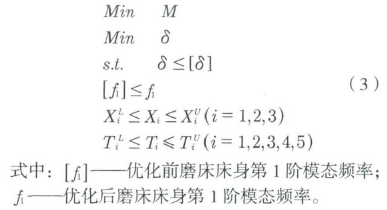
4.2 灵敏度分析
在进行多目标优化之前先进行灵敏度分析。磨床床身结构的灵敏度分析是分析结构设计变量变化对质量、变形、应力和固有频率等性能的影响。不同部位的形状和尺寸参数对结构性能的影响程度不同,即敏感程度不同。通过分析结构参数的灵敏度大小,找出最敏感的设计变量,从而进行优化设计。在 i Sight 中选择灵敏度分析模块DOE 模块进行灵敏度分析,图 8 及图 9 为各设计变量对目标函数的影响。

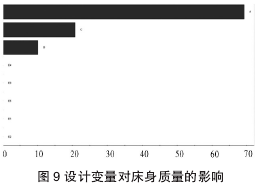
由灵敏度分析结果可知,外筋板厚度 X1 对导轨最大变形量和磨床床身总质量都是影响最大,而第 3 块筋板与基准筋板的间距 T3 几乎对两个都影响不大。对于设计变量较多的多目标优化分析灵敏度可以减少设计变量个数,同时也能够在计算结果中更加方便选取最优值。在后文分析中因为考虑到 T3 仍然对精度有影响,所以依旧设置 T3 这个设计变量。
4.3 优化结果分析
采用 NGGA 算法进行优化求解,得出的各设计变量的最优值及最优值与试验值的对比如表 5所示。从表中结果可知,优化后的磨床床身质量减小了 4%,达到了轻量化的目的,优化后的第1 阶固有频率高于优化前的第 1 阶固有频率,这将减少磨床共振的发生,且导轨最大变形量有一定程度的减小,从而保证了加工精度。
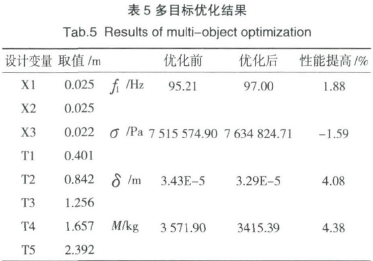
4.3 单目标与多目标优化结果对比
表 6 为单目标与多目标优化设计计算出的目标变量性能提高程度的对比。从表 6 可以看出,单目标优化得出的床身质量相对于多目标优化减轻程度更大,但是床身最大应力也伴随着较大程度的劣化。而多目标分析出的质量虽然没有单目标分析出的质量变化大,但是兼顾到其他属性,其导轨最大变形量和磨床床身最大应力相对较小。因此在实际设计生产中,可根据不同的目标选择不同的优化方法。
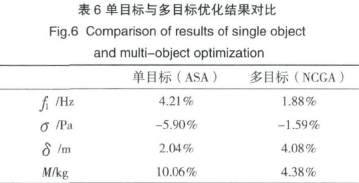
5、 结论
本文通过不同的优化算法对某磨床进行优化设计,并对优化前后的床身结构进行了动静态性能对比,得到如下结论:
(1)通过弹簧单元模拟床身和地基之间的接触刚度对有限元模型进行修正可大大提高仿真的精度;
(2)单目标优化设计相对于多目标优化设计对床身的轻量化优化效果更好,但床身应力及导轨最大变形量优化效果不如多目标优化设计。
投稿箱:
如果您有机床行业、企业相关新闻稿件发表,或进行资讯合作,欢迎联系本网编辑部, 邮箱:skjcsc@vip.sina.com
如果您有机床行业、企业相关新闻稿件发表,或进行资讯合作,欢迎联系本网编辑部, 邮箱:skjcsc@vip.sina.com
更多相关信息