高速、高精度数控铣床电主轴结构优化及其性能研究
2016-8-25 来源:机械工程学院 作者:陈丽婷
高速、高精度电主轴静态性能的分析及其结构优化设计
3.1、高速、高精度电主轴的静态性能理论分析
在静载荷下主轴抵抗变形的能力就是高速电主轴的静态性能。高速电主轴静态性就是指主轴的静刚度。弯曲静刚度与轴向静刚度是主轴的静刚度的两种表现形式。对主轴单元而言,弯曲刚度与负荷能力及抗震性密切相关。弯曲刚度可W代表静刚度。电主轴的弯曲刚度K表示当主轴前端产生单位径向位移8时,在位移方向所需施加的力Fy6]。
电主轴单元静刚度的计算公式如下:

K一主轴系统静刚度,单位N知m:
Ff—主轴系统前端的径向力,单位N;
5—径向力作用下主轴前端位移,单位^ml。
芯轴刚度与轴承刚度能够综合反映电主轴系统的刚度。电主轴系统刚度大小会受到主轴形状、尺寸及各组成部件的加王制造精度的影响,同时轴承组预紧力、级联方式等也会影响电主轴刚度。
电主轴系统的刚度与机床的加工性能息息相关,一旦刚度达不到要求,就会使得主轴变形量过大,降低机床的加工性能,导致精度要求达不到,同时可能导致轴承不能正常运转,轴承磨损加剧严重时甚至会导致轴承失效。在对高速机床的静刚度测量研究中发现,机床变形的一半1以上部分发生在机床主轴部件处,因此,为提高机床的加工可靠性,就必须加强对主轴静刚度的研究。接下来我们运用有限元分析软件ANSYSWorkbench分析对电主轴的进行静态特性。
3.2、高速、高精度主轴系统静态特性的有限元分析
3.2.1高速、高精度主轴系统静力分析的模型简化及建模
a)构建主轴系统几何模型
电主轴单元主要由旋转件和支撑件和固定件H部分构成。旋转件主要是指芯轴、转子、轴承组内圈、滚动体等;支承件是指轴承组外圈W及滚动体与轴承内圈的点支撑;固定件就是指固定不动的壳体、定子冷却套等。在对电主轴单元的静态分析时,只有旋转件和支撑件起作用,可W忽略固定件的作用。仅对旋转件与支承件进行分析,其结果能够代表主轴系统的整体静力学性能。在进行分析之前I我们首先要对电主轴系统做如下简化:
1)将电主轴的芯轴和转子作为一个整体进斤处理,并且假设其具有相同的材料属性;
2)用弹性支撑来代表轴承径向刚度,弹性约束值用轴承径向刚度值来表示;
3)不考虑轴承组轴向刚度。最终得到电主轴系统的简化模型如图3.1所示。
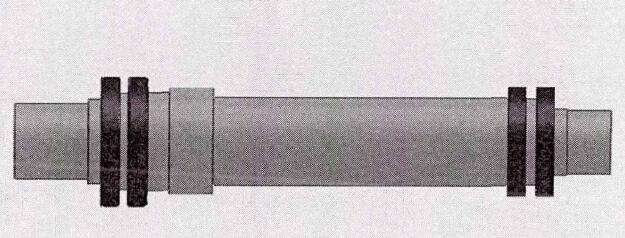
图3.1电主轴静态分析简化几何模型
b)建立电主轴有限元模型电主轴系统静态分析的有限元建模,具体步骤如下:
1)简化几何模型在DesignModeler中的建立
首先,建模可W选择DesignModeler的自体建模属性进行实体建模,也可W选择将电主轴单元已经在SolidWorks中建立好的H维模型进行导入达到建模的目的。此处,由于我们事先己经完成了H维模型在SolidWorks中的建立,只需将文件格式存储为电主轴.agd即可直接将电主轴模型导入。简化几何模型如图3.2所示。
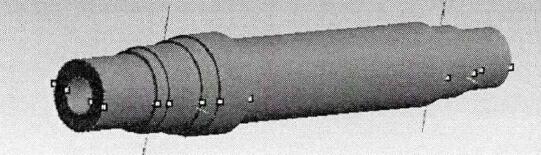
图3.2导入的几何模型
2)添加材料属性
主轴系统选用40CrNi,此材料的参数为:弹性模量E=210N/mm2,泊松比^1=03。在软件中选择模型的几何体形式为"目〇邮",然后巧开EngineeringDate窗日进行材料属性的添加,完成后返回Simula化n窗口。
3)划分几何模型的网格
双击model进入电主轴静态性能仿真分析,首先完成模型网格划分的操作。首先在"Mesh<Method"中利用过滤体rigid功能键选择主轴系统整体模型,设定网格类型为优先选择空间六面体;然后设定模型网格大小,通过在"Mesh<化ing"设定5mm为网格的划分尺寸。此后,通过单击"Mesh<GenerateMesh"即可完成网格的划分。模型共有115776个单元和169503个节点。对有限元模型进斤网格划分后如图3.3所示。
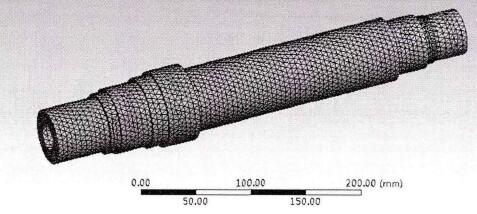
图3.3电主轴的有限元模型
3.2.2高速、高精度电主轴静态载荷的计算
锐削加工时的锐削力是电主轴主要静态外载荷。因为不同工况下钥削力的差异很大,结合VMC系列现有机床加工条件,确定锐床工况进行设定:立式钥床在統削加工时,假定采用端面粗齿硬质合金端面统刀,工件材料定为铸铁,并且采用对称锐削,根据VMC系列现有端面统刀的锐削参数选择维克特63A04R-SCMORC10-22,具体刀具参数如表3.1。下面对锭削力进行计算:
表3.1维克特63A04R-SCMORC10-22刀具参数
1)已知条件
由第二章初步确定的高速锭削电主轴的基本尺寸,设定电主轴的工况:作i定采用端面粗齿硬质合金端面就刀,工件材料定为铸铁,并旦采用对称统削。维克特63A04R-SCMORC10-22,具体刀具参数,統刀直径d0=63mm,钥刀齿数Z=4,每齿进给量3/=化22mm/Z,毎次锐削深度即背吃刀量=2mm,洗削宽度=40mm。
2)切削力计算
根据主轴系统结构进行受力初步分析,用于指导电主轴结构的静力学分析巧优化设计。在满足主轴静力分析的前提下,简化后的系统受力如图3.4和图3.5所示。
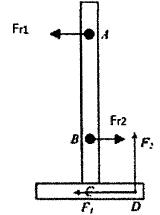
图3.4主轴系统径向简化受为图
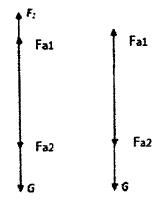
a)切削工作b)空转
图3.5轴向受力分析
切削受力点到主轴系统前支承点之间的垂直距离为115mm,CD代表刀具切削受力点到主轴系统中屯、线之间的距离为31.5mm。根据理论力学中力矩平衡得如下方程;
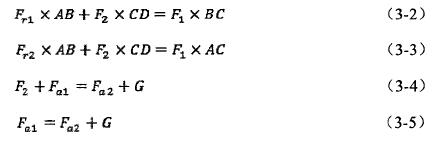
其中,frl——后轴承径向支撑力,i;2——前轴承径向支撑力,——后轴承轴向力,F。^前轴承轴向支撑为,&——切削力径向分力,&——切削力轴向分力。
由上述公式可知,若想求得主轴系统轴承组径向、轴向支撑为,需先求出切削力径向分力和切削力轴向分力。对于端面镜削加工,单个刀片的受为情况如图3.6。单位切削为是指单位切削面积上的主切削力,铸铁材料的单位切削力是1200N/rnm2。所W己知单位切削力的条件下主切削力的求解公式为口7]:

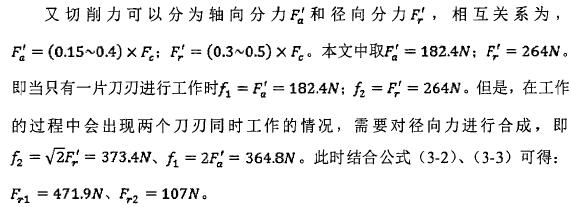

图3.6单个刀片的受力情况
由于建模时,未将刀具考虑在内,需将力换算到主轴悬伸段的端部。显然由于主轴在径向方向上受力平衡。在主轴系统悬仲段端部Fr=与1-与2=364.9。
3.2.3髙速、高精度电主轴静力分析的加载、约束及求解
本论文在对电主轴系统进行静力学分析时,主要分析其镜削力载荷,由上章节计算得到的主轴在设定工况下在主轴前端节点上所受最大径向载荷为
Ff=364.9W。
在实际工程中,轴承系统会发生非弹性形变,形变会影响机床的加工质量和主轴系统的静态特性。前面在进行模型简化时己经指出,本文用ANSYSWorkbench中的弹性约束来模拟将轴承的弹性支承,用轴承径向刚度来表示约束刚度值。
下面具体描述如何在ANSYSWorkbench的Sta化Structure功能模块中对模型进行加载、约束与求解,步骤如下:
a)施加载荷W及约束
1)施加约束
首先添加圆柱面约束于电主轴前后轴承轴段面处,选择Si5)ports>CylindricalSupport,选择过滤电主轴模型安装轴承组圆柱面,而后对圆柱面进行约束,设置两圆柱面径向和轴向自由,切向有约束。对主轴前轴承组处添加固定约束,选择Siq)ports>FixedSi5)port,选择安装前轴承组的主轴圆柱面的后端面。最后对简化的轴承组添加弹性约束,选择Si5)ports>ElasticSiq)port,过滤选择电主轴芯轴用于配合前、后轴承安装处的圆柱面。给定前圆柱面的径向刚度值为324(N/|un),后圆柱面的径向刚度值为297卿Aim)。
2)施加载荷
漆面己经计算得到了主轴的境像锐削力F,=364.9N,本论文模拟分析时将此力W集中力的形式对主轴前端进行加载施。具体操作时,选择Loads>Force,然后选择前轴端边的锭削力作用点,将载荷类型设置为Compoiients,Z轴负方向,大小为364.9W。电主轴模型添加载荷W及约束后如图3.7所示。
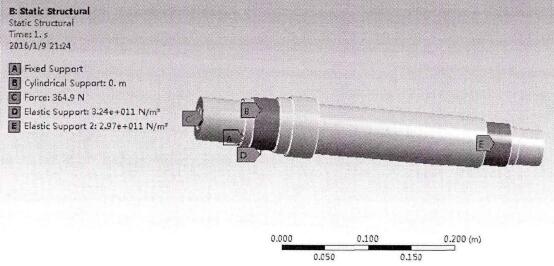
图3.7添加载荷^^^及约束后的电主轴模型
b)指定求解参数并完成求解
静力变形是电主轴静态分析的主要体现形式,所研究主轴的变形情况是静力分析必须要做的工作。经过上述加载后,选择Deforma化n>Toal>Slove,得到电主轴的静力变形。结果如图3.8所示。
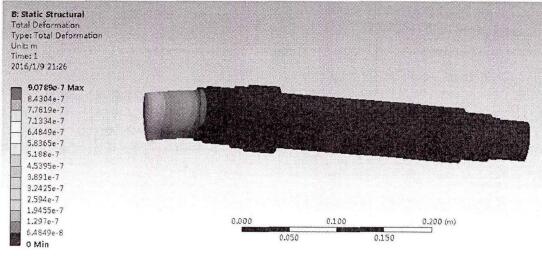
图3.8高速电主轴的静态变形图
从图3.8可W得出,电主轴在典型切削条件下,最大形变出现在主轴系统前端。最大变形量表示为6=9.0巧Xl(r7mWo.giym,其他区域所受影响都相对较小,变形量可1^忽略。由电主轴静刚度的计算公式(3-1)可得:

本论文设计目标要求电主轴静刚度不低于235W佔m,实际上电主轴的静刚度为400扣/^?11,显然电主轴的静刚度符合设计要求。
3.3、基于ANSYSWorkbench的电主轴结构优化设计
3.3.1结构优化的具体内容和优化设计
在对高速电主轴结构设计完成W后,我们可W巧步认定电主轴的总体结构、电机选择、轴承的配置W及系统的静刚度等部分已经基本达到设评目标要求。接下来主要对主轴结构参数进斤优化。
作为高速机床的核屯、部件,电主轴的性能直接决定其加工精度和生产效率。电主轴的静刚度对其性能有很大影响,它的数值大小主要受电主轴径向尺寸、电机、滚动轴承W及预加载荷的大小的影响。在进行模拟实验时,主轴前端悬伸量
(a)和前后支撑跨距(L)能够直观的反映电主轴的静刚度大小。
研究发现,在对电主轴进行结构设计时,主轴前端悬伸量越小主轴刚度值越大。而主轴支撑跨距对电主轴静刚度之间的关系属于非线性,很难通过^计算方法跨距的合理值。主轴刚度在两者之间的综合作用下变得更加难W确近年来,随着有限元法的快速发展,主轴前端悬伸量和前后支撑跨距等参数已经可W用ANSYSWorkbench进行优化。而且其优化结果与实际实验结果误差不大,能够做到对电主轴结构参数的优化。
利用ANSYSWorkbench的优化设计模块DesignXplorer对初步完成结构设计的电主轴进行优化,W电主轴前端悬伸量(a)和前后支撑跨距(L)为设计变量来提高电主轴静刚度,进而完成电主轴系统的结构优化设计8]。
3.3.2ANSYSWorkbench优化设计的基本概念
从己经有的方案中,选出最满意的设计方案,就是优化设计。在实际工程设计中,往往会遇到想要实现某一特定功能或需要多个参数达到综合性能最佳,此时通常数学学科的最优设计理论为指导,通过计算机软件(如ANSYSWorkbench)来实现。解决最优解的问题时,首先根据设计目标,建立目标函数,然后给出函数变量的取值范围,最后求解,得到最优方案8]。
3.3.3高速、高精度电主轴结构优化设计的具体步驟
通过分析可知,影响电主轴静刚度的最主要参数就是主轴前端悬伸量(a)与前后支撑跨距(L)。下面W主轴前端悬伸量(a)和前后支撑跨距(L)为设计变量,W提高电主轴静刚度为设计目标,完成电主轴的结构优化。同时还要考虑减小主轴质量,一方面节约钢材,另一方面也可W降低主轴惯性矩。也就是说,电主轴静刚度最大的问题也就是使主轴前端位移最小的问题。
ANSYSWorkbench的优化设计放在静力学有限元仿真后面进行研究,与静力学分析不同,既然是优化分析,那么优化后的主轴前端悬伸量(a)和前后支撑跨距(L)值必然与优化前有所不同,因此优化设计时主轴前端悬伸量(a)和前后支撑跨距(L)必须设置为变量,即需要参数化构建有限元模型,因此须将进行结构优化设计的电主轴前端悬伸量(a)和前后支撑跨距(L)设置为变量(a的初值是原设计值,为50mm;L受建模的限制将轴承安装轴段的长度都计算在内为305mm),这样才能用DesignXplorer功能模块进行仿真和优化设计。电主轴结构优化设计的模型与电主轴静态分析的实体模型相同,因此在电主轴的静力学分析基础上,设置目标函数,即在geometry模型选择主轴前端变形量(a)和前后支撑跨距(L)使之成为输入设计变量,如图3-9。此处需要说明,前后轴承支撑跨距选择轴承安装轴段两端面之间的距离代替。然后在结构静力学分析求解模型的结果求解栏中勾选totaldeformation中的最大结果作为输出变量,即主轴的最大型变量为输出结果,如图3.9。
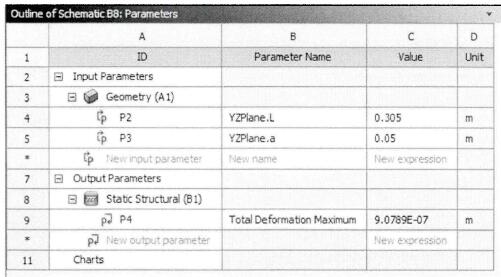
图3.9设计变量
点击进入ANSYSWorkbench的优化模块ANSYSDesignXplorer的ResponseSurface模块中,在满足电主轴结构设计要求的前提下,设置主轴前端变形量(a)和前后支撑跨距(L)变量的变化范围如图3.10(a)、(b)所示。然后对DOE功能模块中对10个设计点进行预览和更新操作,结果如图3.11。
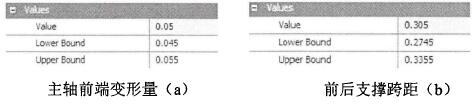
图3.10变量的变化范围
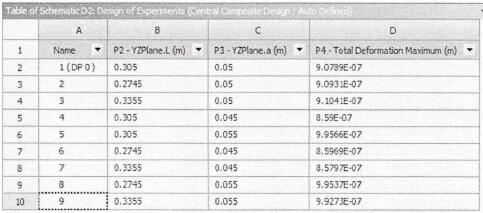
图3.11对10个设计点更新的结果
然后单击生成优化结果,得到结构优化后的方案。单击"Min/MaxSearch*"得到设计变量使得目标函数取到最大/最小值时的值,如图3.12所示。

图3.12目标函数的最值
由图3-12的优化结果可知,当主轴前端悬伸量3=45mm和前后支撑跨距L=274.8mm时,主轴前端变形量达到最小值,此时主轴整体尺寸变小,直径不变,质量也相对较小。综合各方面的因素,最终取各优化参数如表3.2所示。
表3.2主轴最优化参数
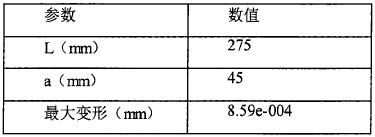
从上表可W看出,结构优化后的电主轴前端悬伸量(a)减小了5mm,前后支撑跨距(L)减少31mm,主轴前端变形量最小,大小为H=0.000859mm=0.859^m,此时,电主轴的静刚度值最大,大小增大到42日N/imi,比原值(400NAmi)提高了6%。优化后电主轴系统质量也有明显的减小。优化后的电主轴系统结构图如图3-13所示:
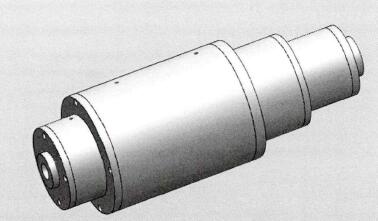
图3-13优化后的电主轴系统结构图
3.4、本章小结
本章首先对电主轴结构进行静态分析,得到静刚度值400N/^im,初步验证了电主轴结构设计的合理性。然后应用ANSYSWorkbench的优化模块ANSYSDesignXplorer对电主轴静刚度的重要影响因素;电主轴前端悬伸量(a)和前后支撑跨距(L)进行优化设计,结果使电主轴的静刚度提高6%,同时主轴质量比优化前有所减小。优化结果对电主轴静动态性能的提升意义重大。
投稿箱:
如果您有机床行业、企业相关新闻稿件发表,或进行资讯合作,欢迎联系本网编辑部, 邮箱:skjcsc@vip.sina.com
如果您有机床行业、企业相关新闻稿件发表,或进行资讯合作,欢迎联系本网编辑部, 邮箱:skjcsc@vip.sina.com
更多本专题新闻
专题点击前十
| 更多