高速、高精度数控铣床电主轴结构优化及其性能研究
2016-8-29 来源:机械工程学院 作者:-
本章对电主轴的热态性能加W分析,由于电主轴在商速运转过程中会发生大量的热量,如果这些热量得不到很好的发散,主轴系统就会在这些热量的作用下温升,进而主轴系统受热引起热变形,直接影响被加工件的表面质量,严重时甚至会导致主轴系统失效。因此,本文希望电主轴温升能够控制在最小值,温度梯度尽量能够对称均匀分布。在对电主轴的结构设计完成么后,展开电主轴热态特性的研究工作,对提高电主轴加工特性W及加工精度具有重要的意义[62]
5.1高速、离精度电主轴的热源分析和计算
研究表明:电主轴系统的两个主要的热量来源就是内置电机发热和主轴前后高速角接触球轴承组的发热。
5.1.1髙速、高精度电主轴电机的发热分析与升算
内置电机输入功率在转化为有效输出的同时伴随着功率的损耗,功率损耗W热量的形式散发,电动机发热就是从这些功率损耗转化而来。通常包括机械损耗、磁损耗、铜损耗和附加损耗,由于附加损耗占比一般在1% ̄5%,一般不做计算。
a)主轴机械损耗
高速旋转的转子零部件跟环境气体会产生摩擦,该摩擦引起的损耗就是机械损耗。该损耗主要产生于转子两端与空气、转子外表面与定、转子配合间隙内气体之间的摩擦力。下面计算这些机械摩擦损耗,方法如下式:
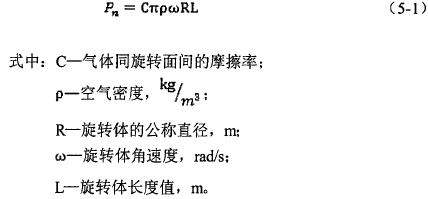
b)主轴磁损耗
铁忘被周期性反复磁化使得电机定予和转子内因磯滞和锅流会产生磁损耗。静磁化、旋转磁化和循环磁化都属于反复磁化。依据相关研究结果,本论文所涉及的反复磁化就属于循环磁化,在循环磁化时,通常单位质量材料的损耗经验公式为:
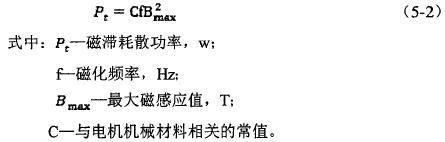
可W依据转差率计算转子铁忘的转散,但是该功率太小可W忽略。下面仅对满流损耗进行计算:
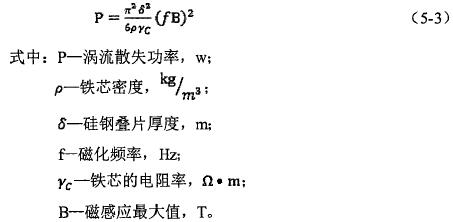
C)主轴铜损耗
在同步电机中,铜损耗是由于交变电流通过定子与转子线圈绕组,绕组材料自身电阻率引发的常态电阻热损耗。损耗方程为:
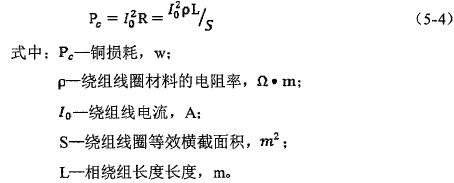
佛罗里达大学Jordan教授W额定功率37.3kw的标准电机为研巧对象[63],研巧结果表明,电机损耗包括机械损耗、铜损耗、磁损耗和附加损耗,其损耗占比如下表5.1:
表5.1电机各种损耗占比

故依据Jordan的研究取功率因素0.8,那么电动机的额定功率损耗为5.7kW,并且根据广州数控设备有限公司陈楚兴、邵国安和广州工业大学黄开胜利用ANSOFT电机快速设计软件伤真可知[641,电机在额定转速到最高转速之间可W做恒功率变速。根据上海交通大学郭舟平李藉智[65]运用NASTRAN对电主轴系统进巧主轴各个转速下的热稳态分析的研究结果也表明;在额定功率W下,主轴的转速对主轴系统定子发热的影响很大,当达到主轴的额定功率后,定子的发热随转速的变化影响不大。
高速旋转的电机会产生大量的热量,研究表明送些热量的1/3是由电机转子产生,另外2/3由电机定子产生。假设这些热量损耗全部转化为电机发热。电机的额定功率为28kW,经计算可W得到;转子产热量为1.9kW,定子产热量为3.8kW。
5.1.2高速电主轴轴承的发热分析与计算
角接触球轴承组是高速电主轴系统内部的另一个重要热源,高速旋转条件下,角接触球轴承为点接触,轴承滚动体与内外圈之间存在滚动阻力,使得两者么间摩擦剧烈,产生大量的摩擦热。研究表明,高速角接触球轴承的发热随摩擦力矩的增大发热量越多。根据Pakngren关于滚动轴承摩擦力矩的推导公式,轴承的摩擦力矩M包含两部分[66]:轴承与润滑油粘性间产生的摩擦力矩M0(N’m);与负荷作用所产生的摩擦力矩而(N’m)。计算公式如下:
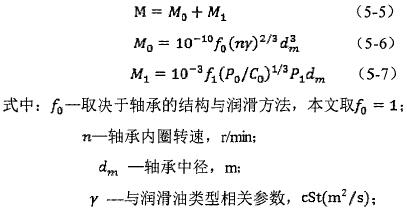
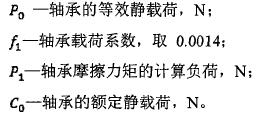
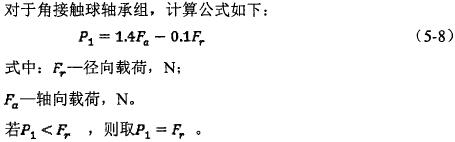
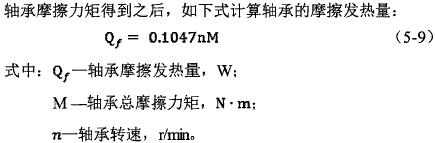
论文中轴承组采用46号润淆油作为润滑剂,结合前后轴承组的各项参数,依据式(5-5) ̄(5-9),计算可得到,电主轴在额定功率不同转速下恒J力率变速时,前后轴承组摩擦发热量如下表5.2所示:
表5.2各转速下前后轴承的摩擦发热量

5.3窩速电主轴的热载荷热生成率的计算
电主轴热载荷主要包含W下两部分;电机发热和轴承的发热。下面分别对其热生成率进行计算,电机的热生成率包括电机定及转子的热生成率;轴承的热生成率包含前轴承组和后轴承组的热生成率。计算热生成率q的公式如下:
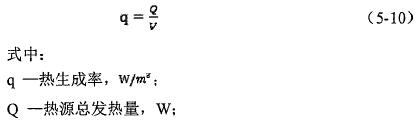
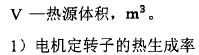
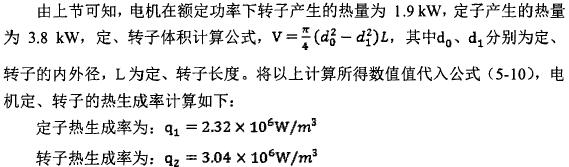
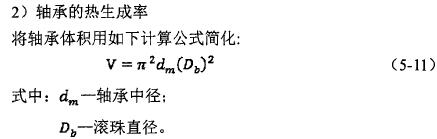
前面通过计算已经得到了轴承组的摩擦发热量,同时将上式(5-11)汁算所得轴承体积参数代入公式(5-10),电主轴在额定功率,额定转速、最高转速及15000ipm转速下前后轴承的热生成率计算得到如表5.3所示:
表5.3各转速稳定条件下前后轴承的热生成率

5.2高速电主轴热边界条件的确定
依据美国普渡大学bossmanns和中国学者吴玉厚[67]的研究,高速电主轴系统的传热主要为轴承润滑系统中轴承与润滑油气么间的对流换热,电机定子与定子冷却液间的对流换热,电动机转子端面与空气之间的对流换热,电机定转子间气隙间的对流换热,电主轴外壳与外界空气的对流换热。还有各零部件之间的福射,但是由于辖射热量相对较小,忽略不计。本论文在研究的过程中发现还要考虑主轴系统的传热:髙速电主轴巧轴空必处内表面与空气的对流换热W及系统旋转外表面与空气之间的对流换热。
5.2.1电机定子与定子冷却液之间的对流换热
该对流换热主要是通过定子与定子循环冷却液冷之间热交换实现的。螺旋槽内的冷却液通过持续不断的循环对流实现换热。冷却液的流态、温度和螺旋槽的几何尺寸都会影响该系数的具体值。
电机定子与冷却液间的热交换属于管道内的稳流体强迫对流换热。强迫对流热交换系数计算公式如下:


假定电主轴在各个转速阶段,冷却液的供应量都不变,则电主轴与冷却水之间的对流换热系数不因主轴转速的改变而改变。
5.2.2电机转子端部与空气间的传热
电机转子热传递分为H部分,其中一部分直接传递给主轴,另一部分通过定转子之间的气隙传给了定子,其余由转子端部传递到周围的空气中。研究表明,当电主轴在高速旋转时,转子端部传递到周围的空气中的那部分热量占比最大,可通过下式进行计算转子端部与空气间的热交换系数:

式中:
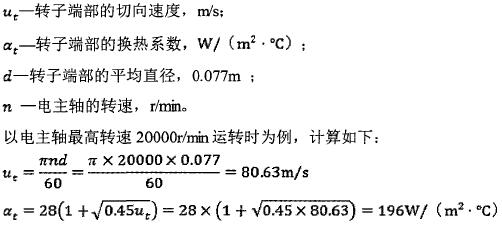
然后分别计算电主轴在额定转速、最高转速及15000rpm转速时,电机转子端部与空气间的传热系数如表5.4;
表5.4电机转子端部与空气间的传热系数

5.2.3髙速电主轴系统外壳面与外界空气的对流换热
为了保证机床的加工精度,主轴系统内部热源产生热量需要散发出去,工作一段时间后,主轴系统整体都会有温升。此时电主轴系统外壳表面温度会比周围环境高。也就是说,部分热量会通过电主轴外壳传递到周围的空气中,其余部分经由电主轴向外界空气的福射传热。该种传热方式被称为复合传热。假设环境温度为定值,复合传热的换热系数可W用下式来表示:
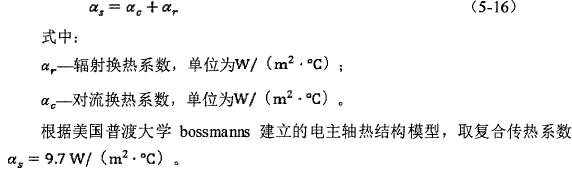
5.2.4高速电主轴系统运动外表面与外界空气的对流换热
电主轴运动外表面与周围空气的换热类似于电化转子端部的传热,可按公式(5-14)计算换热系数用,按公式(5-15)计算主轴的平均速度。主轴运动外表面的平巧直径值3?1为0.046m。根据公式 添加字1 可W计算得到电主轴运动外表面在额定转速、最高转速及ISOOOrpm转速下与周围空气的换热系数如下表5.5所示:
表5.5电主轴运动外表面各个转速下与周围空气的换热系数

5.2.5高速电主轴内部与空气的对流换热
主轴内部运动表面与空气间的对流换热与电机转子端部的传热类型相同,可根据式(5-14)、(5-15)进行计算,取主轴内部平均直径(1?^为0.025m,根据公式 添加 字2 计算得到电主轴运动内表面在额定转速、最高转速及15000ipm转速下与周围空气的换热系数如下表5.6所示:
表5.6电主轴运动内表面各个转速下与周围空气的换热系数

5.2.6轴承与油-气润滑系统的对流换热
主轴轴承的润滑和冷却采用较为先进的油气润滑方法,直接向轴承润滑区域内射入高速的油气混合物,W达到对轴承润滑与冷却的目的。但是实际上,由于漉合物中油量比较少的缘故,真正起到冷却作用的是压缩空气。气流在轴承中的平均流速和气流流过轴承的面积都会对轴承与压缩空气的对流换热系数产生影响。气流流过主轴轴承内外滚道的轴向流动面积用A表示,计算公式如下:
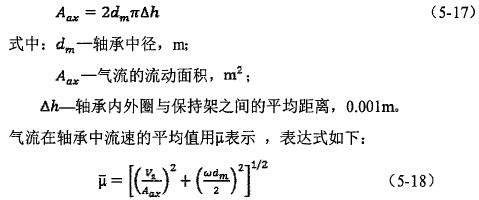
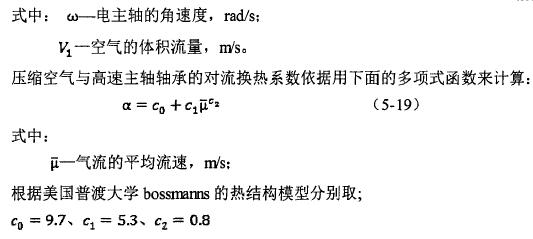
本论文中,假定轴承在各个转速下工作时轴承油气涧滑的供应量不变,取V1=124Xl(T3m3/s,然后结合轴承中径大小,根据式(5-11)、(5-)可Wi十算出前后轴承气流的平均流速。最后根据式(5-13),可W计算得到在主轴额定转速、最高转速及ISOOOrpm转速下前轴承与压缩空气的对流换热系数如表5.7所示;在主轴额定转速、最高转速及15000rpm转速下后轴承与压缩空气的对流换热系数如表5.8所示:
表5.7主轴各转速下前轴承与压缩空气的对流换热系数

表5.8主轴各转速下后轴承与压缩空气的对流换热系数

5.2.7定转子气隙间的对流换热系数
高速电主轴和环境么间的换热主要是对流换热,转速为20000r/min为例进行计算,由努赛尔方程可得到主轴定转子间气息对流换热系数计算式;
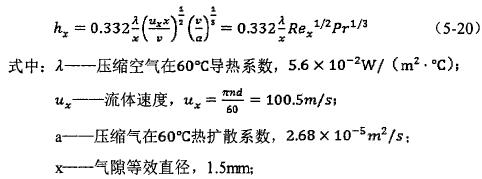
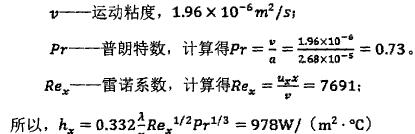
电主轴在额定转速、最商转速及ISOOOrpm转速下定转子气隙间对流换热系数如下表5.9所示:
表5.9电主轴各转速下定转子气隙间对流换热系数

5.3高速、高精度电主轴的稳态热分析
5.3.1髙速、髙精度电主轴热分析模型的简化及有限元建模
a)高速电主轴热分析模型的简化
本文在对电主轴热态特性模拟分析之前,首先模拟了电主轴在高速运行状态下热源的发热情况,然后充分利用ANSYSWorkbench分析的巨大优势,对电主轴装配体模型进行热态分析。在不影响分析结果的前提下,对系统热态模型进行简化:
1)用厚壁圆筒来代表电主轴定、转子热源体,并且设定其为稳定热分布;
2)与电主轴热分析关系不大的部件不参与热分析模型的构建,去掉拉刀系统和后支座;
3)忽略不影响热分析的螺钉、通气、通油孔等细小结构。
简化完成后的,对简化后的高速电主轴热态分析模型进行H维实体模型的建立。建立电主轴装配体时,首先利用专业的H维实体建模软件So虹Works对热态模型进行建模,保存为.igs格式之后可直接导入ANSYSworkbench进行分析求解。图5.1是在SolkiWorks中建立的高速电主轴热分析銜化模型的剖视图。
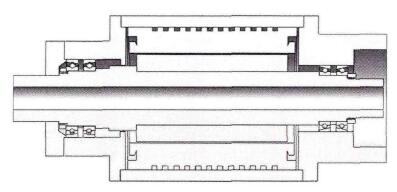
图5.1电主轴简化模型的剖视图
b)高速电主轴热分析有限元模型的建立
首先选择分析类型为Steady-StateThermal,然后将在SolidWorks中建立的电主轴热分析简化模型导入到ANSYSWorkbench热分析仿真模块中,如图5.2所示。
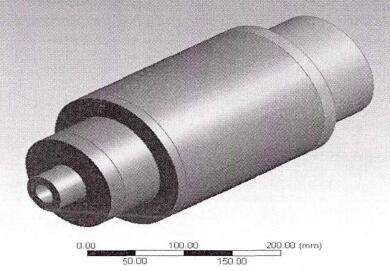
图5.2导入的电主轴模型
然后在EngineeringDa化中设置电主轴各主耍零部件的材料信息,在稳态热分析中,唯一需耍的材料属性就是导热系数,取导热系数为60.5w/m-k。接下来双击进入Model,对装配体中的接触部分进行接触设置,ANSYSWorkbench能够自动识别并且建立各种连接部件之间的接触关系,在此采用默认的固定设置。最后进行网格划分,对分析模型设定网格大小为5mm,设定自动网格划分。至此网格划分完成,为了清楚地表达主轴系统内部结构的网格划分,需要对模型进行剖切处理,是电主轴热分析有限元模型的半剖切图如图5.3所示。
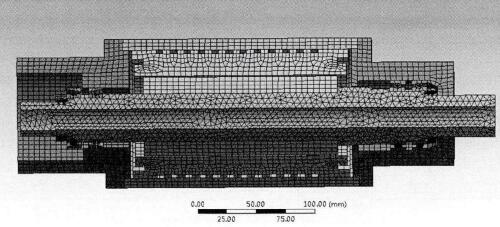
图5.3电主轴热分析有限元模型的剖切图
5.3.2施加高速电主轴热分析的热载荷及边界条件
在ANSYSWorkbench稳态热分析模块"Steady-StateThermal"中,首先分析电主轴在最高转速、额定功率条件下的热态特性,将前面5.1节中计算得到的'主轴最高转速时的前后轴承和电机定转子的热生成率作为热载荷;然后对5.2节中分析得到的电主轴热边界条件进行加载到有限元模型上,同时设置环境温度为22°C,加载条件汇总如下表5.10。最终得到载衙加载后的分布如图5.4:
表5.10最高转速时电主轴的热载荷及边界条件汇总
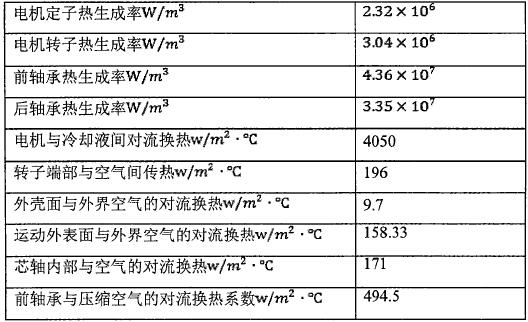
表5.10最高转速时电主轴的热载荷及边界条件汇总(续)

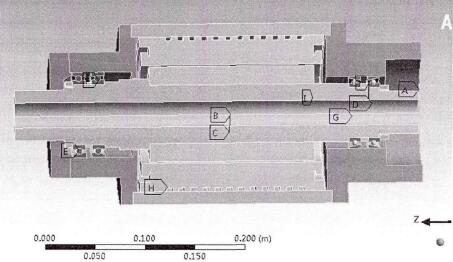
图5.4添加生热率W及热边界条件的电主轴模型
5.3.3求解并分析高速、高精度电主轴稳态热分析的后处理结果
在ANSYSWorkbench稳态热分析模块"Steady-Sl;a化Thermal"中,设定求解选项为"Temperature",最终得到主轴系统在额定功率最高转速n=20000i-/min时的稳态温度场分布图如图5.5所示。
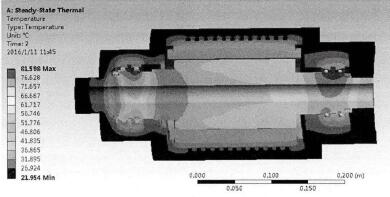
图5.5电主轴转速20000r/min时的稳态温度场分布
由上图可W看出,电机额定功率最高转速下工作时,整个主轴系统最高温升,出现在抽承肉圈处,温升达到巧.5nC。此时电机定子由于冷却液的循环>#站作用,温升相对较低,定子的最高温升仅为巧。C左右,出现在靠近转子处。相巧于定子电机转子温升相对较高,最窩温度为44。{:左右,整体来讲此时电机转子温升很不W均匀,靠近后轴承处温升更为严重。这是由于后轴承处传递来的热量更多,再加上转子本身在发热,转子的散热条件又不好,导致转子整体温升较高。由上图显示知此时电主轴的温度梯度分布很不均匀,导致主轴系统因温升导致的热变形也不均匀,严重影响主轴的加工精度。
重复5.3.2加载步驟,对热态模型添加主轴转速为15000r/min时的电机及轴承生热率W及热边界条件,得到主轴转速为15000r/miti时的稳态温度场分布如下5.6;
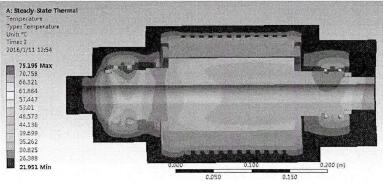
图5.6主轴转速ISQOOr/min财的稳态温度场分布
由上图可W看出,相较于最高转速时的温升情况,电主轴整体温升有所降低,尤其是主轴轴承内圈处,温升为57.2°C。此时电机定子由于冷却液的循环冷却作用,温升相对较低,定子的最高温升仅为22°C左右,出现在靠近转子处。相较于定子电机转子温升依然相对较高,而且由最高转速时的44°C提升到了46°C左右。主要是由于,转子本身发热不变,虽然从轴承处传导的热量有所减少,但是转子散热系数随转速的降低而下降,转子散热条件变得更差,导致转子整体温升更高。此时温升梯度相较于最高转速时反而变得均匀一些。
再次重复5.3.2加载步骤,对热态模型添加主轴额定转速时的电机及轴承生热率及热边界条件,得到主轴额定转速时的稳态温度场分布如下5.7:
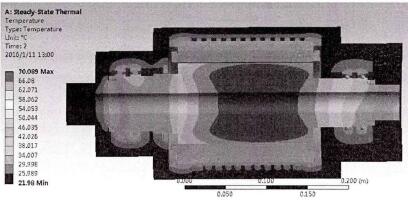
图5.7电主轴转速9700r/min时的稳态温度场分布
由图5.7明显可W看出,电机额定功率额定转速下工作时,电主轴系统温升主要集中在电机转子处,主要是由于此时转子处的散热条件变得更差。此时主轴系统整体来讲,主轴定子、前后轴承处温升都比转子处要低很多。温度分布云图相比较于最高转速时的情况相差很多。而且电机额定功率额定转速更接近于主轴系统实际工作情况。
5.3.4稳态温度结果的分析
目前研究者们普遍认为电主轴额定功率、最高转速的条件是电主轴发热最为严重的工况,因此对电主轴稳态热态性能的分析大都仅分析电主轴系统在额定功率最高转速时发热情况。但是电主轴一般情况下不会在最高转速下工作,在实际生产中,电主轴更《工作在额定转速左右,因此对电主轴额定转速时的稳态热性能的分析显然更为重要。本文对电主轴系统在额定功率额定转速、最高转速和15000r/min的中间转速多工况下,对电主轴进行了热态性能分析。分析结果表明,电主轴系统在额定转速下的稳态温度分布云图与最高转速时得到的稳态热分布云图有很大的差异,电主轴系统在额定功率额定转速下,转子处温升相对非常严重,系统整体温度梯度差异很大,由温升引起的变形很不均匀。
5.4改善高速、高精度电主轴热态性能的主要措施
本文増加电主轴额定转速W及中间速度段的热态性能分析,由分析可知,点主轴系统在不同转速状态下热态分布是有很大区别的,这样可|^>1帮助我们有针对性的提出不同转速时的热态性能改善措施。具体改善措施主要有下列四个方面:
(1)首先,不论在任何转速阶段,都应尽可能降低电主轴单元的发热量,应该想尽办法减少电机和轴承的发热量。具体的方法如下:由于同步电II*一般比异步电机功耗小,因此尽量选择同步电机;由于陶瓷球轴承发热量更少:^^可レッ考虑用其代替目前使广为使用的钢轴承,还可W合理改变轴承沮的预紧力大小来减小主轴系统轴承巧的摩擦发热量。
(2)减少电主轴系统的热位移。电主轴系统在受热条件下会产生热位移,热位移不均衡会引起额外的加工误差,因此需要对热位移进行补偿,还有电主轴系统本身的对称性也是热位移对称性的一个影响因素,应尽量保证系统对称工整。
(3)加强散热,降低系统温升。在电主轴系统中,可控的散热措施在于冷却液和海合涧滑油气处,因此可W通过控制冷却液的流量加强电机定子的散热,还可W通过改善压缩混合油气的状态W改善轴承沮的冷却效果。
(4)改善温度梯度,主轴系统温升不均匀必然导致各个零部件的温升变形量不同,进而引起主轴动不平衡,降低加工精度。因此根据W上分析结果,在最高转速时,适当增大前后轴承处的油气流量;而在额定转速时,主轴温升最大处在电机转子处,可W通过在电机安装处的巧轴空处焊接散热管道来改善电主轴转子处的散热情况,散热管道内通循环冷却水。如此可尽量是主轴的发热均衡,减少湿升变形引起的主轴系统动不平衡。
5.5本章小结
本章首先就主轴系统的主要热源W及内部传热机制进斤了详细的分析,并计算了各部分热生成率和所有可能的热边界条件。然后对进行了简化,并在利用ANSYSWorkbench的稳态热分析模块对简化了电主轴的热分析模型进行稳态热分析,论文就电主轴系统在额定功率、不同转速条件下的稳态热性能进行了分析,得到了电主轴在额定转速、15000r/min和最高转速20000r/min时的温度分布图。结果表明,在不同转速下,电主轴系统的热态特性各不相同。最后根据分析结果,有针对性的提出了改善电主轴热态性能的措施。
投稿箱:
如果您有机床行业、企业相关新闻稿件发表,或进行资讯合作,欢迎联系本网编辑部, 邮箱:skjcsc@vip.sina.com
如果您有机床行业、企业相关新闻稿件发表,或进行资讯合作,欢迎联系本网编辑部, 邮箱:skjcsc@vip.sina.com
更多本专题新闻
专题点击前十
| 更多