超精密车床主轴回转误差测试系统的研究
2016-12-14 来源:哈尔滨工业大学 作者:王世良
第 3 章
径向运动误差分离及实验研究
本章以三点法误差分离算法为基础,提出径向误差测量实验除噪、滤波、同步运动误差的提取和三点法误差分离算法的频域连续性处理方法,减少测量信号在时域频域中的变换计算。利用之前搭建的回转误差测试系统对超精密车床主轴回转误差进行实际测量实验和数据分析。本章还从超精密车床固定方向刀具加工工件表面成形角度,分析一阶谐波去除依据。
3.1 径向运动误差分析
3.1.1 最小二乘偏心对径向运动误差的不可分离性
本节将分析传感器测量值在频域中的解析构成,并分析最小二乘圆心对径向回转误差的不可分离性。下面首先讨论回转是理想轴,测试件表面轮廓不是理想圆的情况传感器的测量值。图 3-1 中曲线为测试工件某一截面的实际轮廓,O 为截面的最小二乘圆心,由于安装偏心使得测试工件最小二乘圆心 O 与回转轴心 O?有偏差 e。
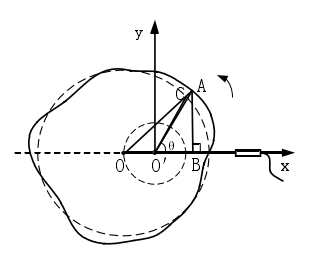
图 3-1 实际表面轮廓传感器测量
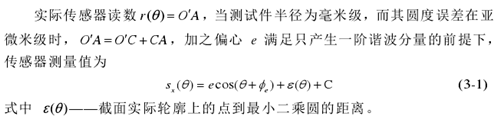
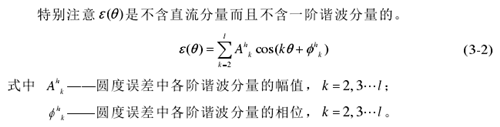
由式(3-2)可知,非理想截面时,建立在回转轴心处的测量坐标系(之后还会介绍坐标系不建在回转轴心处)中,x 轴方向的传感器读数为最小二乘圆心在 x 轴方向上的运动轨迹。如果截面平面内布置两个传感器,则可以测出最小二乘圆心在平面内的运动轨迹。
安装偏心,通常指的是人为安装测试件到回转轴时产生的偏心。但是即便不安装测试工件,直接对主轴某一截面进行测量,实际情况下此截面的最小二乘圆心和其回转轴心也基本不会重合。故定义此处最小二乘圆心与瞬时回转中心的偏差为最小二乘偏心。这个最小二乘偏心与之前讨论的安装偏心并无本质区别,只是最小二乘偏心比安装偏心小很多罢了,所以将安装偏心归到最小二乘偏心概念中。最小二乘偏心满足一定条件时,只产生一阶谐波分量,并引入到传感器测量值中。
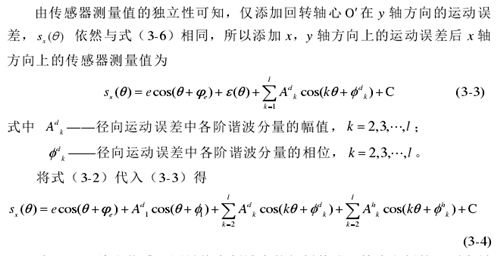
式(3-4)给出传感器测量值在频域中的解析构成,等式右侧第一项为最小二乘偏心运动,第二项为回转轴的一阶谐波运动,第三项为回转轴的二阶及以上谐波运动,前三项的值指的都是最小二乘圆心运动在传感器轴线方向上的分量。第四项为被测截面实际轮廓上的点到最小二乘圆的距离(注意此项不含直流分量和一阶谐波分量),实际上也是截面转动时在传感器轴线方向上的轮廓上的点到最小二乘圆的距离,组后一项为直流分量。除去直流分量所有项之和为最小二乘圆心的运动与圆度误差的叠加。
下面将从传感器测量值在频域中的解析构成结合三点法误差分离算法分析最小二乘偏心对径向运动误差的不可分离性:
在三点法误差分离过程中,因权函数 G(1) ?0 ,抑制一阶谐波,使传感器中的一阶谐波量没有分开。分离出的圆度误差不含一阶谐波分量,即(3-2)式。传感器测量值中的一阶谐波分量全部归到主轴回转误差运动中,从(3-4)式可知归到主轴回转运动误差中的一阶谐波分量就包含最小二乘圆心的偏心运动,这个偏心运动量影响了主轴回转误差的分离精度。
从式(3-4)中去掉圆度误差项和直流分量项即为三点法得到的回转运动误差,其中第一项与第二项是最小二乘偏心运动量和回转误差一阶谐波分量。因为二者都是一阶谐波,其和亦为一阶谐波。显然一二项的合成是唯一的,而若已知合成项,其分解不唯一,所以最小二乘偏心运动与回转轴的一阶谐波运动是不可分的。
如果在测量试验中人为安装测试件进行测量,则最小二乘偏心量相对于回转误差会很大,严重影响回转误差的分离结果,即便是直接对回转轴截面直接测量,回转误差中依然包含了最小二乘偏心量,只不过相对于安装偏心量小些罢了。
鉴于最小二乘偏心对径向运动误差的不可分离性,由两种处理方式得到回转轴回转误差:一是保留一阶谐波分量,缺点是回转误差中包含了最小二乘圆心的偏心运动量;二是去掉一阶谐波分量,缺点是回转误差中损失了回转轴的一阶谐波分量。如果用安装测试件进行测量时,要去掉一阶谐波分量,因为此时最小二乘偏心运动量相对于回转误差太大,如保留一阶谐波分量,分离出的回转误差将严重失真。
下面讨论一阶谐波分量如何处理的问题:
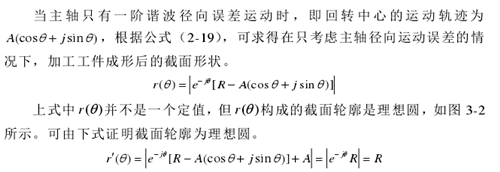
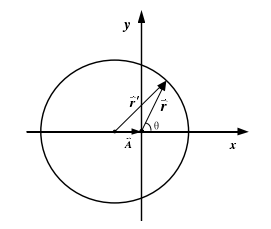
图 3-2 主轴具有一阶谐波误差运动固定方向刀具加工工件成形
至此可得出结论:超精密车床主轴径向一阶谐波误差运动不影响固定方向刀具加工工件截面形状轮廓,所以从加工工件的角度来讲超精密车床主轴径向运动误差中的一阶谐波分量可不予以考虑。综合上述信息,利用三点法误差分离测量主轴的径向回转误差可以不计一阶谐波分量的影响,故在在误差分离之前可以将信号中的一阶谐波分量直接去掉。
3.1.2 同步误差和异步误差的频域提取
在分析同步和异步运动误差之前先来看一下一种常用的误差分离方法——集合平均。集合平均是对同一误差信号进行 N 次采样,然后对这 N 次采样的数据按点位求平均值。
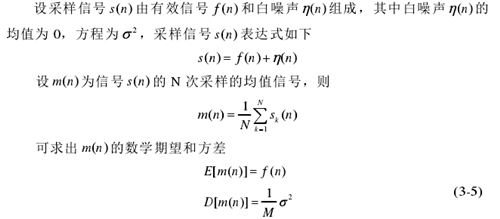
可见对信号做集合平均处理有抑制随机噪音的作用。
所谓的同步误差就是回转轴的多转采样数据的均值,异步误差是从每转采样数据中减掉同步误差[45],如图 3-3。主轴的回转误差运动实际上不是周期性的,对于超精密车床,其主轴的回转精度很高,每转的回转误差运动基本保持一致。由此计算出的同步误差可以视作主轴的回转运动误差。

提取同步误差的作用是从主轴的回转运动采集信号中提取周期性回转运动感误差,作为误差分离的基础信号。另外,同步误差的提取同于对信号做了集合平均,所以对信号中的随机噪声也有一定的抑制作用。
同步运动误差是多转数据对应点位的均值,所以要求每转的采集信号是严格的等角度采样,否则均化后的结果将失真。
以上讨论了从时域角度提取主轴的同步运动误差,并可知提取同步运动误差不但提取了主轴的周期性的高回转精度运动误差,还具有集合平均的效果,降低低阶噪声的影响。下面讨论从频域中提取同步和异步运动误差:
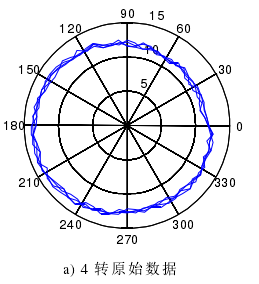
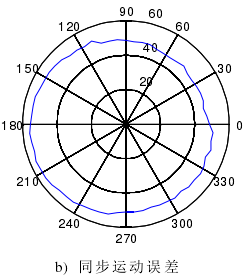
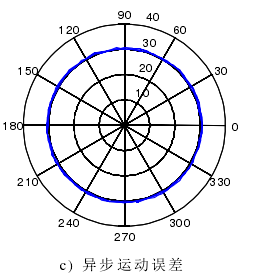
图 3-3 Maltab 仿真传感器的 4 转数据及同步、异步运动误差时域图
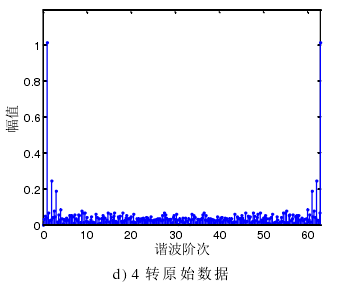
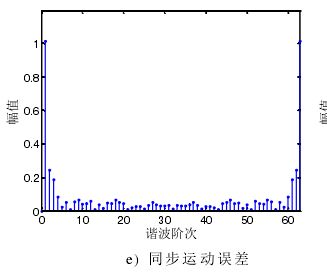
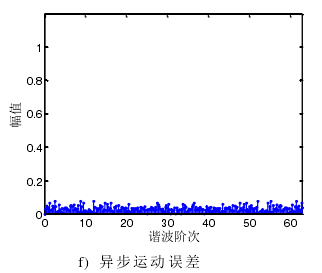
图 3-4 Maltab 仿真传感器的 4 转数据及同步异步运动误差频域图
对一个传感器的 4 转数据(每转 64 个点)进行傅里叶变换,整数倍谐波阶次对应的是同步运动误差的谐波成分,如图 3-4 e)所示;小数倍谐波阶次对应的是异步运动误差的谐波成分,如图 3-4 f)所示。已知这个结论,从频域中提取整数倍谐波分量成分,即是主轴的同步运动误差。
3.1.3 径向运动误差数据的频域连续性处理
本节将综合除噪、滤波、提取同步运动误差和三点法误差分离在频域中进行连续处理,即从传感器原始电压时域信号开始,上述步骤全部在频域中处理,不在时域中提取同步运动误差,减少信号在时域频域中的转化计算。图 3-5 是频域连续性处理与一般方法对比图,从图中可以看出,频域连续性处理减少了时域信号和频域信号之间的转换次数,即可以减少额外的计算量。频域连续性处理的关键即是 3.1.2 节中讲述的从频域中提取主轴的同步运动误差,在这个环节中可以减少时域频域的转换计算。
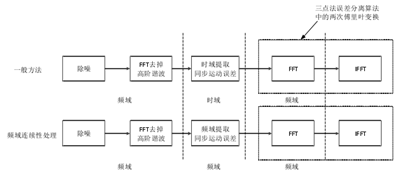
图 3-5 频域连续性处理与一般方法对比图
以下将详细展开频域连续性处理的各个环节,首先讨论滤波。在采集模拟信号之前,通常要对此信号进行抗混叠滤波。所谓的抗混叠滤波[47],即是设置滤波器的截止频率为有用信号的最高频率,将高于截止频率的成分从信号中去除。抗混叠滤波的作用是在采样之前将高频无用频率成分去掉,防止在之后的采样过程中将高频干扰信号采样成低频成分,出现频率混叠现象,造成采集信号的失真。
抗混叠滤波是在模拟信号进行数字化采集之前由硬件实现的,另一种方法是通过软件滤波的方式实现数据采集的抗混叠作用。具体操作是直接进行模拟信号的数据采集,但是要求采样频率应为高于高频干扰成分频率的至少两倍以上。采集得到的数据再进行数字滤波,将高于有用信号的最高频率的成分去掉。如果采样频率仅仅设置为高于有用信号的最高频率的两倍以上,那么高频干扰成分会在采样过程中错误的采样为低频成分,在以后的处理中,再也无法用数字滤波器滤除了。图 3-6 为防止频率混叠的两种方法:
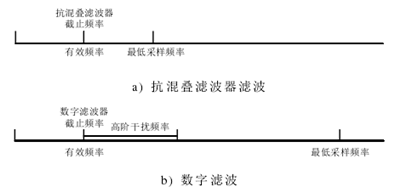
图 3-6 抗混叠滤波和数字滤波比较

表 3-1 抗混叠滤波和数字滤波区别

由图 3-6 和表 3-1 可见,采用数字滤波的优点是采集系统中不用加入抗混叠滤波器硬件,缺点是由于采样频率较高,增加了 A/D 转化的成本以及后期的数据处理运算量。
对采样后的数据,要将信号中的高阶成分去掉。根据 ISO 标准,工件的圆度误差多为低频信号,当被测件的圆度误差的谐波阶次大于 22~45 阶后,通常就归于零件的表面质量如波纹度、表面粗糙度等,如图 3-7。从超精密车床加工的角度来讲,其加工的零件的轮廓误差的主要来源是主轴的回转运动误差。工件的表面形状误差的主要来源于主轴的低阶回转运动误差,工件的表面质量如波纹度、表面粗糙度误差主要来源于主轴的高阶回转运动误差。本论文对主轴回转运动误差的测量目的主要是为后期提高加工工件表面形状误差做准备,所以分离主轴回转运动误差与分离圆度形状保留同样的谐波阶次即可。论文中将保留误差信号的低 50 阶信号,将高于 50 阶的信号全部除掉。
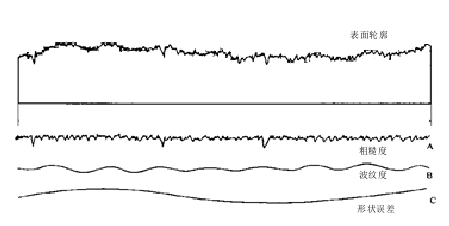
图 3-7 工件表面轮廓成分组成
具体除掉采集信号高阶信号的做法是:首先对采集信号做傅里叶变换,将相应的高阶项及对称项置零,然后在做反傅里叶变换得到滤掉高阶成分的信号。这种数字滤波方式可以将信号中给定的高阶成分全部滤掉,带通内的谐波成分全部保留而且没有任何衰减。
综合以上分析,图 3-8 给出径向运动误差频域连续性处理的详细数据处理过程。
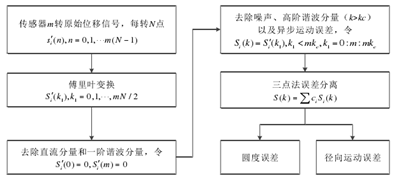
图 3-8 径向回转误差频域连续性数据处理流程
3.1.4 主轴回转精度的评价
最小二乘圆法对评价圆度误差最常用的方法,对于主轴径向误差运动的评价可以参照圆度误差评价,采用最小二乘圆评价。利用最小二乘法,找出实际轮廓的理想圆,使得轮廓上各等分点沿径向到圆周距离的平方和最小,这个理想圆即为最小二乘圆,其圆心为最小二乘圆心,如图 3-9 所示。
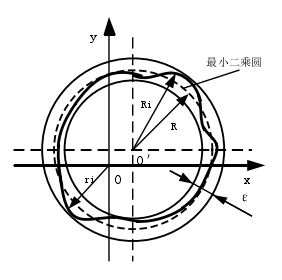
图 3-9 最小二乘法确定理想圆圆心
最小二乘圆的圆心 O'?坐标 (a,b),半径为 R,则
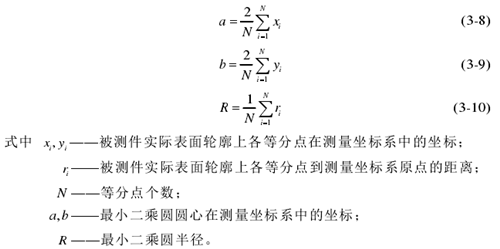
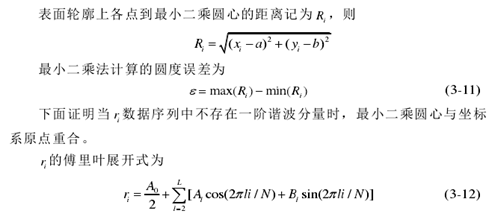
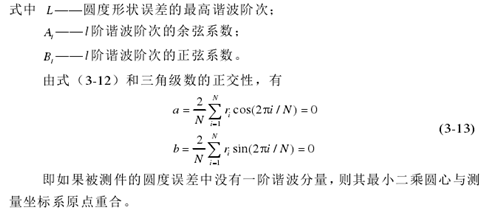
3.2 径向运动误差测量实验及分析
3.2.1 传感器安装角位置的确定
在满足 G(k)≠0(k=0,2,3,4…N)的条件下,即除三点法原理性一阶谐波抑制以外,保证其他谐波成分不被抑制,p1、p2有很多组,文献[50]给出确定三点法传感器最佳角位置的方法。圆度误差各阶谐波分量的误差传递系数Q(k) 的计算方法如下:

式中ɑ (k),β(k)——分别为权函数G(k)的实部和虚部。
Q(k) 包含由传感器自身精度(如传感器的非线性,灵敏度系数误差及随机噪声等)和传感器安装误差(安装间隔偏差,传感器测量轴线偏斜等)对分离出的圆度误差的第 k 阶谐波分量引入的误差系数。
为增大圆度误差分离精度,应该减小圆度误差的各阶谐波分量的传递误差,其中一种方法是使 Q(k)的最大值最小。本课题据此设定传感器安装位置N=128,p0=0,p1=17,p2=32,其权函数如图 3-10 所示。
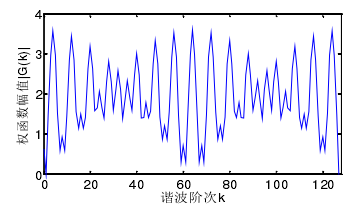
图 3-10 N=128,p0=0, p1=17,p2=32 时的权函数图
3.2.2 测试工件选取及安装偏差消除
通常在主轴回转运动误差测量试验中会采用标准球或标准棒作为被测试件,如图 3-11,通过对被测试件的运动的测量来主轴的回转运动误差。标准球和标准棒各有各的优缺点,标准球的优点是可以用位移传感器通过扫描的方式精确的找到球赤道位置,可用于调整传感器位置使所有传感器共赤道平面安装;标准棒可以提供更多的测量截面,而且相同精度的标准棒相对于标准球的价格会低一些。
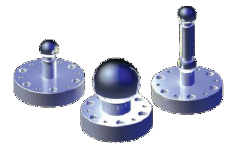
图 3-11 标准球
虽然高质量标准球或标准棒的截面圆度误差可以控制在 25 nm 以下,但是对于超精密车床,十几纳米或是几十纳米的圆度误差相对于主轴回转运动误差来说还是不可以忽略,依然要在数据处理中将圆度误差分离出去。
另外,人工装夹被测试件到超精密车床时一定会带来安装偏心及安装倾角的问题。安装偏心一方面导致测量信号混入较大的一阶谐波分量,通常会比其他阶次谐波分量大出几个量级;另一方面较大的安装偏心会使测量到的位移分布在一个较大的范围,传感器非线性误差带来的影响会增大。虽然传感器的非线性误差影响非常之小,但是对于精密测量来说,我们要考虑到每一个细节问题。标准测试件的安装倾角偏差也是一个很大的影响因素,很小的安装倾角也会导致被测试件末端截面产生较大的偏心运动。
综合以上分析,即便是采购高质量的标准球或是标准棒,对于超精密车床主轴回转运动误差不可忽略,那么我们可以放宽对标准测试件圆度误差的精度级别的限制。对于本试验来讲,最合理的方法既是利用机床本身加工圆柱体工件作为被测试件,在不拆卸状态下接着进行主轴回转运动误差的测量试验。这种做法合理的原因有:
(1)虽然目前实验室超精密车床还无法加工出圆度误差在 25 nm 以下的柱体或是球体,但是其加工的工件的圆度误差和主轴的回转运动误差处在同一个数量级(加工工件的圆度误差的最主要来源是机床主轴的回转运动误差),不会影响误差精度;
(2)消除人工装夹标准测试件带来的安装偏心和安装倾角误差,可以更精确地分离主轴回转运动误差。
(3)加工圆柱体工件要比球形工件更为简单,而且精度要更高,可以节约购买标准球或是标准棒的试验成本。
3.2.3 位移传感器初始间隙的安装要求
位移传感器的安装初始间隙对测量试验也有一定的影响,下面对此进行讨论:
capa NCDT6300 传感器线性度≤0.2%FSO,即在满量程 50 μm 的情况下传感器的精度不会超过 100 nm。通常超精密车床主轴误差运动在几纳米到几百纳米之间,而且传感器在小量程测量时的线性度要好于满量程线性度,所以如果传感器在 500 nm 的测量范围内,其测量精度可以控制到 1 nm 以下。
传感器满量程线性度不超过 0.2%,但是在量程内不同范围内的非线性误差是不一样的。为了保证更严格的测量数据,在进行实际测量试验时,多个位移传感器测头到被测试件的初始安装间隙尽量保持在相同的数据范围内,尽量减少传感器非线性误差带来的影响。
3.2.4 径向误差测量试验方案
超精密车床径向回转误差运动包含径向 x,y 两个自由度方向上的运动,从算法角度上来说,利用三点法误差分离技术,可以从数据中将主轴的径向两个自由度的误差运动提取出来。径向误差测量装置系统图如图 3-12 所示,实际实验装置如图 3-13 所示。
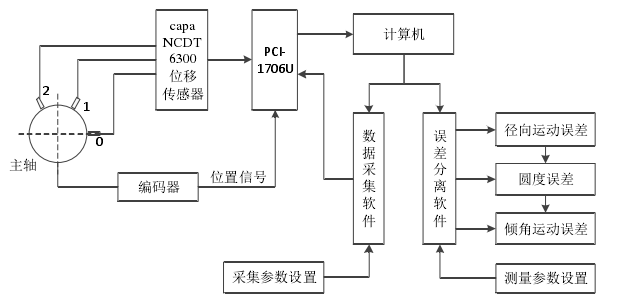
图 3-12 测量装置系统图
在进行数据采集的过程中,通常为等时间采样。但是为了消除主轴转动时的速度波动对采样角位置的影响,采取等角度采样,即每隔一个相同的角度进行一次数据采集。保证等角采样的方法是利用旋转编码器,利用编码器发出的脉冲信号触发采样。编码器保证等角度采样一是三点法误差分离算法的要求,二是在求同步误差时,非等角度采样均化后将使同步运动误差失真。
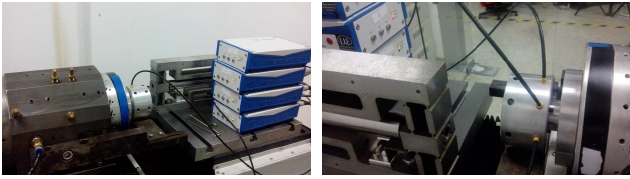
图 3-13 三点法实际测量试验传感器布置
3.2.5 径向运动误差分离实验数据处理
三点法误差分离是通过布置垂直于轴线的同一个截面上的三个位移传感器进行测量的,在算法上要进过两次傅里叶变换,得到将主轴的圆度误差和主轴两个自由度上的径向运动误差分离开来。下面将介绍三点法频域误差分离试验的具体分离过程。
我们在最终计算时采用的每转采集 128 点进行误差分离,为保证有效地去除采集信号中的高频成分,减小频率混叠带来的影响,在原始电压采集过程中将提高采样频率,每转采样点为 768 点。图 3-14 是三个传感器采集主轴在转速为 1000 r/min,采样频率设置为 1280 Hz,转动 20 转的原始电压数据。
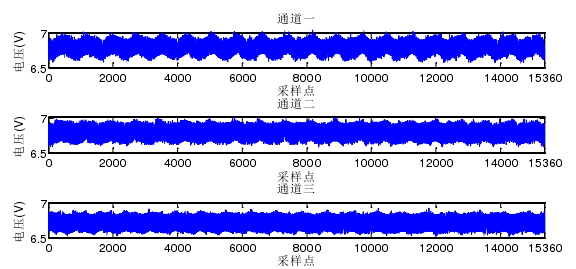
图 3-14 三个传感器采集的 20 转原始电压读数
从上图可以看出,各传感器的原始电压信号噪音成分还是很高的。先将传感器电压信号根据公式(2-20)转化为位移信号,这是一个简单的线性变换。然后对 20 转的数据进行傅里叶变换,对直流分量、一阶谐波分量和高于50 阶谐波分量傅里叶变换项置零去掉上述成分。图 3-15 为 0 号传感器 20 转采样信号去掉直流分量、一阶谐波分量和 50 阶以上谐波分量后的频谱图。
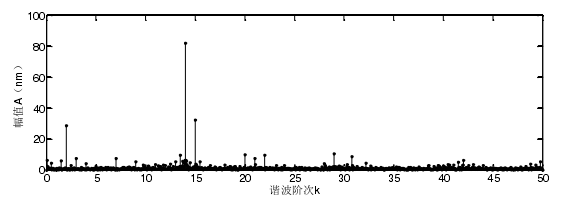
图 3-15 传感器 0 滤掉直流分量、一阶和 50 阶以上谐波分量后的谐波图
根据 3.1.2 节讲述的从频域中提取整数倍谐波阶次分量,即可得到超精密车床主轴回转误差运动中的径向同步运动误差,其谐波成分如图 3-16 所示。
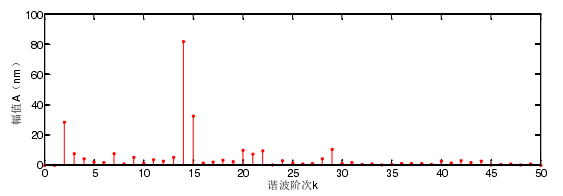
图 3-16 主轴在传感器 0 轴线方向上的同步运动误差谐波图
图 3-17 为图 3-15 和图 3-16 中信号的时域极坐标图,此处给出其时域图形,为的是直观地显示主轴的在传感器 0 方向上的运动误差。
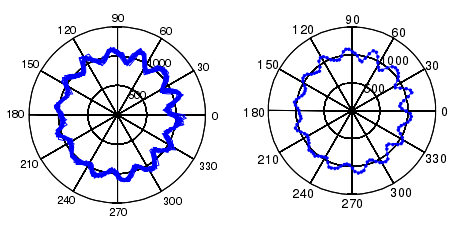
图 3-17 传感器 0 的 20 转数据及同步运动误差
以上是在频域中去掉直流分量、一阶谐波分量、50 阶以上谐波分量以及在频域中提取同步运动误差的过程。其中提取同步运动误差的过程中不仅提取了主轴回转误差运动中的周期性运动,而且还对信号起集合平均作用,进一步抑制低频噪声。
图 3-18 给出三个位移同步运动误差信号的谐波图,此信号中包含被测试件的圆度误差和主轴径向运动误差,是三点法误差分离的基础数据。
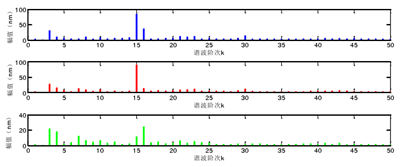
图 3-18 三个传感器的同步运动误差谐波图
基于三个传感的同步运动误差利用三点法频域误差分离技术进行圆度误差和主轴径向回转误差的分离,分离结果如图 3-19 所示。
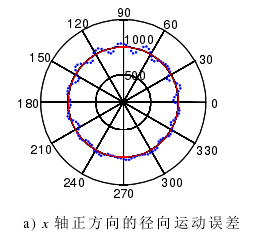
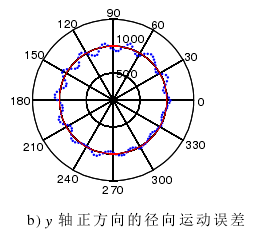
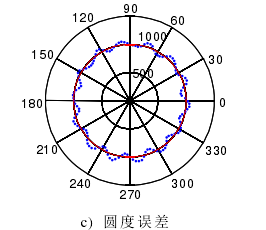
图 3-19 误差分离后的径向运动误差和圆度误差
3.2.6 主轴转速对径向运动误差的影响
前几节分析的是主轴在 n=1000 r/min 的转速下进行的径向误差测量试验,主轴在不同的转速条件下,其径向运动误差是不同的。本节的内容主要研究主轴的不同转速下进行测量试验,分析其径向运动误差和转速的关系。表 3-2是主轴在不同转速下,根据 3.1.4 节讲述的最小二乘圆方法评价的圆度误差和主轴径向运动误差。图 3-20 给出径向运动误差在不用转速下的曲线图。
表 3-2 转速对主轴径向运动误差的影响
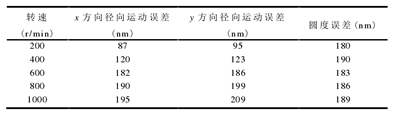
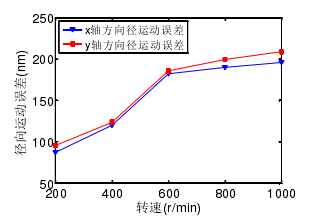
图 3-20 主轴在不同转速条件下的径向运动误差
从上表和图中可以看出主轴在不同的转速下,从测量数据中分离出的圆度误差基本保持一致,但 x 和 y 方向的主轴径向运动误差随着转速的降低而减小。当转速降到 600 r/min 时,其径向回转运动误差迅速降低;当转速在200 r/min 以下时主轴的径向运动误差在 100 nm 以内。
图 3-21 中给出主轴转速在 1000 r/min,600 r/min 和 200 r/min 时,误差分离的具体数据极坐标图形。从图中可以直观地看出,不同转速下分离的圆度误差图形基本一致,而随着主轴转速的下降其
x 轴方向的径向运动误差不断的减小。需要注意的是不同转速下分离出的图像在相位上有些差别。
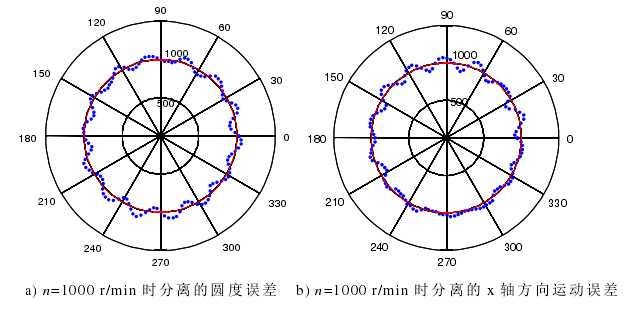
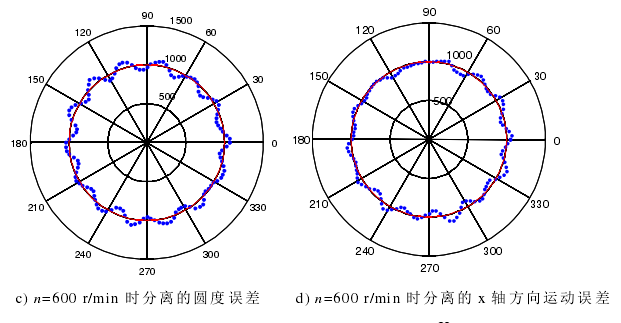
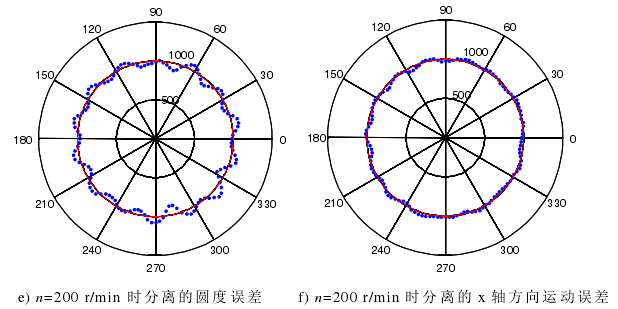
图 3-21 主轴在不同转速下分离出的圆度误差和 x 轴方向的径向运动误差
3.3 本章小结
本章以三点法误差分离算法为基础,借助从频域中提取同步运动误差原理,将实际测量实验中的除噪、滤波和同步运动误差的提取整合全部在频域中处理。而且频域连续处理可以一直延伸到三点法误差分离算法中,即将三点法中的部分计算统一整合到频域处理。通过统一多个步骤在频域中的连续处理,减少了测量信号在时域频域中的变换计算。从超精密车床固定方向刀具加工工件表面成形角度,利用之前建立的运动学模型分析了一阶谐波分量对工件表面成形无影响,为测量实验中去掉一阶谐波分量提供理论依据。针对超精密车床进行径向运动误差测量实验,并分析主轴不同转速下的回转误差精度。
投稿箱:
如果您有机床行业、企业相关新闻稿件发表,或进行资讯合作,欢迎联系本网编辑部, 邮箱:skjcsc@vip.sina.com
如果您有机床行业、企业相关新闻稿件发表,或进行资讯合作,欢迎联系本网编辑部, 邮箱:skjcsc@vip.sina.com
更多本专题新闻
专题点击前十
| 更多