汽轮机转子末叶片销孔加工装置的设计与研究 (中)
2017-7-5 来源:辽宁工业大学 作者: 张晚青
3.汽轮机转子末叶片销孔加工装置的机构设计与计算
汽轮机转子末叶片销孔新型的加工装置主要由定位与夹紧装置、进给装置、传动装置、平衡装置等四部分组成,在上一章中对各部分机构的总体设计方案进行了阐述,在这一章中将继续介绍这台销孔加工装置的各个机构的具体设计方案及关键部件的计算。销孔加工装置的各个机构的具体设计方案为这台装置的可行性提供了进一步的理论依据和技术支持。
3.1 定位与夹紧装置的机构设计
新型转子末叶片锥形销孔的加工装置是将采用整个钻孔装置固定在转子上进行加工,这种加工方式称作“蚂蚁啃骨头”的加工方式。早在上世纪五六十年代,“蚂蚁啃骨头”的机械加工方式在当时得到了广泛的推崇和推广。这种加工方式就是用小型机床加工较大型零件的加工方式。在工作时,大型工件由于体积和质量较大,不易移动,故移动体积和质量都相对小的机床在大工件周围进行加工。鉴于这样的加工特点,我们常把相对小的机床叫做移动式机床。一台最小转子的质量也要十几吨,而这种新型末叶片销孔的加工装置(除平衡装置外)仅仅 60Kg 左右。因此,“蚂蚁”主要是指所谓的“积木式”机床和“移动式”机床,在本文中指的是汽轮机转子末叶片销孔的加工装置。而“骨头”则是指经铸、锻、焊接等方法处理后的大型工件,在本文中指的是汽轮机的转子[15]。
这种“蚂蚁啃骨头”的加工方式常用于指代各种“以小干大”的方法。其实,这种“以小干大”的加工方式在传统加工工艺中并不少见。在中国的明清时期,曾经就有传道士使用过这种加工方式制造天文仪器;在民国时期也出现过用小机床加工大的零件的例子;在前苏联时代也曾用移动式的“塔式机床”加工大型零件的事例。本设计中所采用的“蚂蚁啃骨头”的加工方式,不仅可以节省用于定位所需要的大量时间,而且可以解决由于精度不高带来的较大误差[16]。
本设计的定位和夹紧装置的作用是将小型的加工装置固定在待加工的大型汽轮机转子上。定位与夹紧装置的设计主要包括定位机构的设计和夹紧机构的设计两部分。
3.1.1 定位机构的设计
定位机构的设计是根据转子上的平衡孔相对位置和大小的不变进行设计的。在汽轮机的转子上分布着一级级的叶轮和隔板,但因为隔板上的汽封会存在漏汽的现象,这样就会使每一级的叶轮前后有一定的压差存在,于是就会使轴向推力有所增加。鉴于此,在每一级的叶轮上钻相同的平衡孔,可以有效的降低轴向推力的作用。因此,在汽轮机的每一级叶轮上,一般都开有大小和位置相同的平衡孔。为防止偶数个数的平衡孔对称而产生断裂,故一般叶轮上开 5 或 7 个的平衡孔。为方便加工,平衡孔在一般情况下起到定位的作用[17]。
在本设计中,运用“一面两销”的定位原理对定位机构进行设计,利用相邻的两个平衡孔用两销进行定位。通常情况下,在进行机械加工的过程中,使用频率最高的一个定位方式就是“一面两销”,即这种定位方式第一定位基准是一个基准面,另外的两个基准是垂直于这个基准面的两个销,这两个销分别是一个圆形销,一个削边销(或菱形销)。
在一面两销的定位方式中,一个销和一个面总共限制了 5 个自由度,仅有一个自由度没有被限制,即绕销旋转的自由度,假如在一面两销的定位方式中的另一个销仍然选用圆销,那么,就对两销间距离即两销连线方向的自由度多限制了一次,这样就形成了过定位[18]。一个圆柱销与一个菱形销的设计就是用于防止过定位的。故菱形销只限制了角向的选转的自由度,符合 6 点定位原则,限制了全部 6 个自由度。即一面,限制了 3 个自由度,即沿 Z 移动,绕 X 转动,绕 Y 转动,如图 3.1 所示。
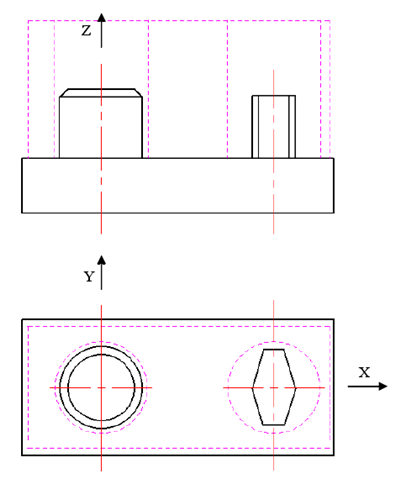
图 3.1 一面两销结构示意图
在机械加工过程中,任意的尺寸都会存在公差(或误差),而两个销的中心距不可能与两个定位孔的中心距完全一致。削边销或菱形销就是可以有效的避免由中心距的误差而造成的无法安装,并且可以限制绕 Z 向的转动。因此,圆柱销是限制 X、Y 向移动的,菱形销的长轴垂直两销孔的连心线[19]。
削边销的设计及误差分析:
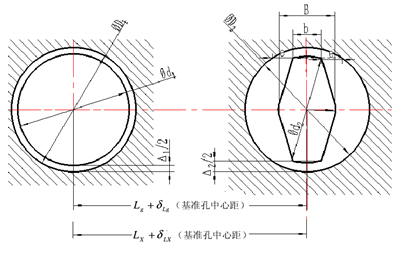
图 3.2 一面两销误差分析示意图
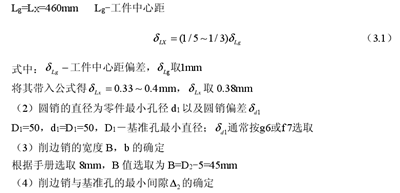
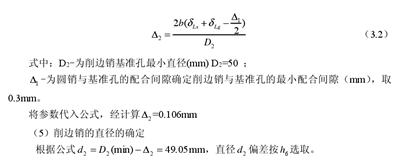
3.1.2 夹紧机构的设计
快速卡钳属于卡具的一种。在机械加工或制造过程中,通常会有将零件或物体放在恰当的位置来进行检测或加工的工序,用来把对象固定的装置,我们称为卡具。卡具也具有其广泛的含义,只要能够快速,准确,方便的固定工件,这样的装置都可以称之为卡具。在卡具这个广泛的大家庭中,属机床夹具应用最为广泛,简称夹具。
夹具通常由定位元件(确定工件在夹具中的正确位置)、夹紧装置等组成。故本设计中的汽轮机转子末叶片销孔加工装置属于机床的一种。
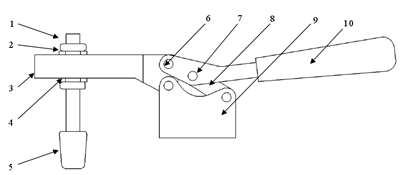
1-压杆 2-螺母 3-滑动框梁 4-调节滑块 5-压紧橡皮垫 6-铆钉 7-连接杆 8-支撑杆 9-底座 10-控制手柄
图 3.3 快速卡钳二维图
本课题中的夹紧机构是将定位好的钻孔装置完全固定到转子上,它的主要组成部件是快速卡钳和连接架。快速卡钳,又称为快速夹具。它的实质其实就是双摇杆机构,双摇杆机构属于平面连杆机构的一种,它由连杆、机架及两连架杆等四构件组成。机构中各构件互相作平面平行运动,其基本型为由四个构件和四个低副组成的平面四连杆机构(简称平面四杆机构),它是应用最广和结构最简单的机构,同时又是构成平面多杆机构的基础。平面四杆机构中,与机架相连接的运动构件称为连接架,不与机架相联的构件称为连杆。能相对机架作整周转动的连接杆称为曲柄,相对机架仅能作往复摆动的连架杆称为摇杆[20-24]。
在现实生活中,我们常巧用死点夹紧原理对元件或零件进行夹紧。当平面四杆机构中,当连杆与从动件在同一条直线时,那么这个平面连杆机构达到了死点位置。被死点位置中的平面连杆机构所压紧的工件,即使存在再大的作用力,同样没有办法把压头松开,当然破坏力除外。在本课题中的所选用的快速夹具,装夹便捷,快速,使用简单,并且灵活,节省了在装配夹具中所使用的大量时间。本文中设计的夹紧装置巧妙的运用快速卡钳,可以使新型的加工装置安装在转子上更加方便,快速,安全[25,26]。
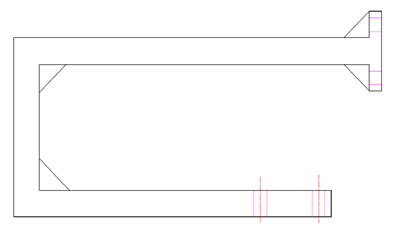
图 3.4 夹紧机构连接架
夹紧机构中的另一部件是连接架,连接架的作用是将加工装置与快速卡钳连接起来,使快速卡钳其发挥应用作用。由于连接架的两端分别由螺栓连接到加工装置和快速卡钳上,整个连接架均已悬出,且悬出面过大,而连接架自身所能承受的载荷有限,此时,在两个结合面之间设计一块加强肋,用来提高结合面的强度和刚性。
3.2 进给装置的机构设计与计算
汽轮机转子末叶片锥型销孔的新型加工装置的进给装置是为了实现 X、Y、Z 方向进给而进行设计的。其主要部件包括螺旋传动副、导轨、进给锁紧机构、滑块、连接板、锥齿轮和带座轴承等。
3.2.1 螺旋传动副的选用与计算
螺旋传动是机械传动的一种,它主要是利用螺纹牙面与螺旋旋合来实现直线运动与回转运动转换的一种传动形式[27]。
螺旋传动的分类根据工作性质的不同可分为:
(1)传力螺旋。传递动力是传力螺旋的主要工作性质的体现,即较大的轴向力和轴向运动均由较小的转矩转动产生,螺旋千斤顶和螺旋压力机就是传力螺旋的最好例证,在工作时常用低转速,间歇的工作或短时间的工作。
(2)传导螺旋。传递运动是传导螺旋的主要工作性质的体现,即传动的精度高是传导螺旋的主要特点。金属切削机床的进给螺旋是传导螺旋的常用方式,其较长且连续的工作时间,较高的工作速度,均可使工作台和刀具的直线进给得到更好的实现。
(3)调整螺旋。轧钢机轧辊的压下螺丝和冲压机的调整螺旋是调整螺旋的常用形式,其零部件间的相对位置的调整和固定是调整螺旋传动实现的目的,就像带传动中心距调整时的张紧螺旋,通常不轻易转动[28]。
本设计中根据工作性质,选用的是传导螺旋和传力螺旋,可以通过人工对手柄的旋转,使 X、Y、Z 三个方向进行进给,间歇的工作和进行精确的定位,并通过旋转手柄完成对预加工的销孔进行较好的钻削。
螺旋传动根据螺纹副摩擦性质的不同可分为:
(1)滑动螺旋
滑动螺旋摩擦系数和螺纹升程在通常情况下较小,故纵然具有很大的轴向力,但其具有很小的转矩。运用这种工作原理,前面所述的传力螺旋起到了事半功倍的传力作用,升程越小“四两拨千斤”效果就愈发的明显。
滑动螺旋传动的特点是:摩擦阻力大,传动效率低,大多数情况为 30-40%;易于自锁;磨损快,进而寿命短;结构简单,加工方便;运转平稳,然而可能有爬行的情况产生。
滑动螺纹一般可分为梯形螺纹和锯齿形螺纹。在日常生活中,我们常提到的滑动螺旋传动就是梯形螺纹传动。梯形螺纹之所以可以得到最广泛的应用,是因为锯齿形螺纹近用于单向受力的传力螺旋。然而矩形螺纹常用于要求不是很高的传动螺旋和传力螺旋。
(2)滚动螺旋
滚动螺旋,也可称为滚珠丝杠传动。在旋合螺母和螺杆的工作面上,置有适量的滚动体,多数情况下为钢珠,少数情况下为滚子,当螺母与螺杆进行转动的时候,滚动体在滚道里沿着螺纹进行滚动,使螺母与螺杆的相对运动成为滚动摩擦,使螺旋副的传动精度和传动效率得到了极大的提高。
滚动螺旋传动的特点是:摩擦阻力小,传动效率高,其传动效率至少在 90%;结构复杂,制造较难;具有传动的可逆性,即既可以把旋转运动变成直线运动,同时也可以把直线运动变成旋转运动;运转平稳,启动时无颤动,低速时不爬行;螺母和螺杆预紧后,一般能够调整到较高的定位精度和重复定位精度,其精度介于静压螺旋和滑动螺旋中间,而且可以提高轴向刚度[29-31]。
多数滚动螺旋的螺母上有滚动体返回通道,与螺纹滚道形成闭合回路,使滚动体在螺纹滚道内循环。
本课题中选用的既有滑动螺旋传动,又有滚动螺旋传动。在 Z 向进给装置的设计是在考虑其自身重力的基础上进行设计的,虽然平衡机构能够使钻孔装置处于无重状态,但为避免操作不当或操作失误所引起的加工装置在 Z 向上滑落下来的危害,所以在 Z 向将螺旋传动副设计为带自锁功能的梯形滑动螺旋传动,即梯形丝杠副。根据上述的滚动螺旋传动的特点,将 X、Y 向上设计为摩擦阻力小,传动效率高的滚动丝杠传动。
梯形丝杠螺旋副的选型与设计:
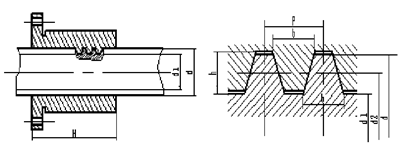
图 3.5 梯形丝杠
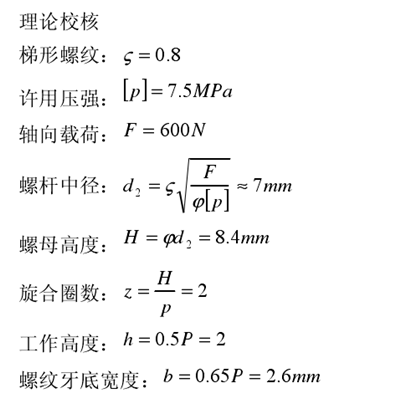

3.2.2 锥齿轮的选用与计算
齿轮是常用的机械设备的重要组成部分与基础零件。它具有传动效率高,功率范围大,使用寿命长,传动比准确,安全可靠等特点,故而成为现今诸多机械产品中不可或缺的传动部件。
(1)锥齿轮的选用
对于平行轴传动,通常多采用圆柱直齿轮或斜齿齿轮传动;对于相交轴传动,多采用直齿、斜齿或曲线齿的锥齿轮传动;对于两轴既不平行又不相交的传动(交错轴传动),可采用准双曲面齿轮传动、蜗杆传动、以及交错轴斜齿圆柱齿轮传动。根据一般尽可能选用结构简单和工艺合理的传动型式,根据本设计对传动装置的结构和动力参数的要求,Z 向进给方向选用两个直齿锥齿轮(伞形锥齿轮)来实现手柄方向的转向,这样可以使手柄的操作更加便捷[32]。
直齿圆锥齿轮主要用于相交轴传动,它的效率比较高,可达 98%,通常用于机床、汽车、拖拉机等机械中。直齿锥齿轮传动的主要特点是承载能力小,比曲线锥齿轮的轴向力小,制造和结构都比曲线锥齿轮容易。
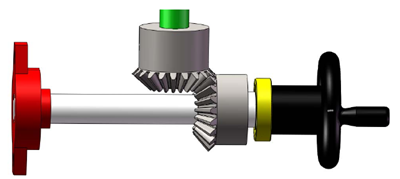
图 3.6 Z 向手轮转动结构图
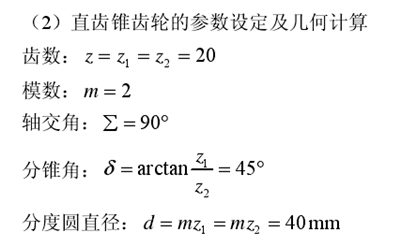
直齿锥齿轮一般用于低速传动,其齿线理论上为直线。为了补偿少量的安装误差及负载变形,实际上常在齿长方向上制有微量的鼓形。直齿锥齿轮的轴向力比曲线齿锥齿轮小,因此,有时可以用轴承来减小对安装空间的要求[33]。
3.2.3 轴承的选用
本课题进给装置中,根据不同轴承的性质,功能,及其不同轴承的特点,选用了KFL002 带座外球面轴承和深沟球轴承。
(1)带座外球面轴承的选用
本课题中的 KFL002 带座外球面轴承是将菱形座和润滑脂密封型深沟球轴承组合起来的高精度组件产品,但价格不贵。它是通过几个螺栓连接安装到 Z 向进给框架上,并且具有调心功能,同时又能够进行润滑脂的补充,它是一种使用和安装都很便捷的产品[34]。
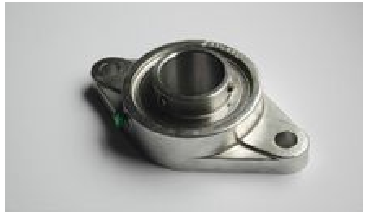
图 3.7 KFL002 带座外球面轴承
(2)深沟球轴承的选用
在本设计中,根据深沟球轴承的特点及其结构设计的需要,选用宽度为 8mm 的国标深沟球轴承。
3.2.4 连接锥齿轮的轴的设计
轴是在机械设备中的一个重要的零件,它是用来安装传动零件,并且使轴绕它的轴线转动,传递转矩或运动,并通过轴承和机架相连接。根据轴和轴线的形状和功用不同,可分为直轴,曲轴和软轴三类。
轴的结构决定于受载情况、轴上零件的布置和固定方式、轴承的类型和尺寸等条件。轴的结构,应使轴受力合理,避免或减轻应力集中,有良好的工艺性,并使轴上零件定位可靠,装拆方便。轴上零件的周向固定,可采用键、花键、销、过盈及胀紧套等连接。轴上零件的轴向固定,常用轴肩、轴环、螺母、轴端挡圈、套筒、圆锥面、锁紧挡圈、紧定螺钉和弹性挡圈等[35]。
本课题中的轴的主要作用是连接锥齿轮,使锥齿轮绕着轴线转动,来实现齿轮的传动,进而达到手柄转向的作用。轴与直齿锥齿轮之间用平键相连接,平键与轴和锥齿轮
采用过盈配合的配合方式,在轴的两端分别用一个带座外球面轴承和一个深沟球轴承连接,由于深沟球轴承与框架过盈配合,故不需要用轴肩等对其进行轴向固定。
3.2.5 导轨与滑块的选用与计算
导轨主要用来支承和引导运动部件沿着一定的轨迹运动。两个作相对运动的部件构成一对导轨副。其中,不动配合面称为固定导轨或静导轨,运动配合面称为运动导轨或动导轨。在运动导轨和固定导轨之间一般只允许有一个自由度。在本课题中,进给装置中的导轨均为直线导轨。导轨按照其摩擦性质的不同,分为两大类,一类是滑动导轨,一类是滚动导轨。
鉴于导轨的运动性能,针对于本课题设计与选用不同类别导轨时应注意以下方面:
(1)导向精度。由于本课题的运动轨迹均为直线运动,几何精度是影响导向精度的主要因素;
直线运动导轨的几何精度一般包括导轨在垂直平面、水平平面内的直线度和两条导轨面间的平行度,两导轨面间横向某长度的扭曲值;
(2)精度保持性;
(3)低速运动的平稳性;
(4)刚度的满足。
在本课题中,根据工作性质和不同类型导轨的特点,在进给装置中,将 Z 向进给的导轨设计为滑动导轨,将 X、Y 向的导轨设计为滚动导轨。
(1)Z 向进给导轨的选用
直线滑动导轨既可以是一个专门的零件,也可以在一个零件上起导向作用的部分。在 Z 向进给的机构设计中的直线滑动导轨起到导向作用。滑动导轨的运动件和承导件直接接触,其优点是结构简单,接触刚度大,缺点是磨损快,易形成自锁。
在 Z 向的进给机构中,选用 T 型导轨用来对加工装置的 T 型丝杠进行导向,以减小对丝杠的方形螺母的压力与扭矩。由于在 Z 向上,丝杠和与其配合的方形螺母作上下往复运动。如果没有导轨的导向作用,则方形螺母相当于悬臂梁的结构,对方形螺母的压力和扭矩之大可想而知。虽然在螺母两侧增加了直线滑动导轨的设计,减缓了对螺母的压力,但仍可能出现自锁现象,故需要对导轨的不自锁条件进行验证,以保证进给过程顺利安全的完成[36-38]。
滑动导轨不自锁的条件:
作用力 F 平行于导轨轴线,与轴线的距离:

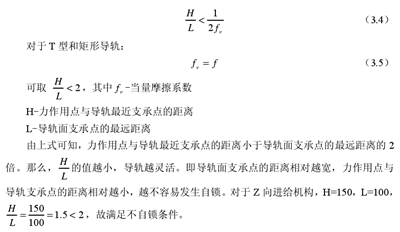
(2)X、Y 向进给导轨的选用
直线滚动导轨副是一种新型的导轨标准组件。它是由四列循环滚珠、滚珠保持架、支承滑块和带滚道的导轨等四部分组成。一般情况下,每根导轨有两个或两个以上的支承滑块。承载时,滚珠与滚道成线接触,其承载能力比点接触高很多。由于滚动元件在受力时产生弹性变形,因而可以预紧,以提高导轨副的抗冲击性能和刚度。
滚动导轨的优点是:在滚动导轨中,其动静摩擦因数的两个值相差很小,选用滚动导轨不会容易出现爬行现象,并且定位精度高,寿命长。因此,在本课题中的 XzY 方向的进给导轨,选用直线滚动导轨副中的光轴和 SBR 滑块。
SBR 直线导轨:在本课题中,选用 SBR 直线导轨,它以超高的强度和刚度,以及超低的阻力,在现实生产与生活中,得到广泛的应用。
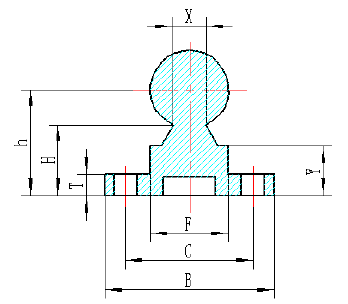
图 3.8 SBR 导轨
表 3.1 导轨尺寸参数表

3.2.6 进给锁紧机构的设计
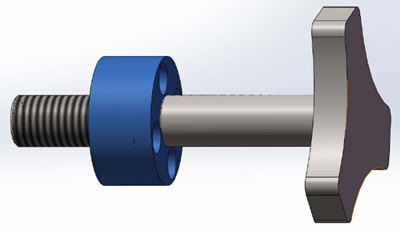
图 3.9 锁紧机构
本文中的锁紧机构主要对 Z 向和 Y 向的导轨进行锁紧,以使两个方向的进给装置进行锁紧在特定的位置停留,且停留后不会因振动或误碰手柄而产生位移,以确保钻孔精度满足加工需求,保证钻孔过程的顺利进行以及操作工人的人身安全。
进给装置的锁紧机构由带螺纹法兰和带手柄螺杆组成。Z 向的锁紧机构中,带螺纹法兰由四个沉头螺钉固定在 Z 向与 Y 向的进给连接架上。当进行 Z 向进给时,将带手柄螺杆旋松或卸下,在进给到特定位置时,将其旋进带螺纹法兰中,将螺杆通过 Z 向与Y 向的带孔连接架旋到旋不动为止,利用螺杆对导轨的挤压力,阻止 Z 向进给,达到锁紧目的。X 向的锁紧机构中,带螺纹法兰由四个沉头螺钉固定在 X 向的一个滑块上,进给到特定位置后,将螺杆旋进法兰中,将螺杆通过带孔的滑块直接旋到 X 向导轨上,直到旋不动为止,以实现对 X 向进给的锁紧。
3.3 传动装置的机构设计与计算
本文中的传动装置是由电动机、传动机构和工作机构三部分组成。这部分装置主要是通过对 X 向进给装置的移动,来对预加工孔进行钻削。电动机接上电源后,通过平键传递动力到小皮带轮上,再通过把小皮带轮和大皮带轮连接起来的皮带将动力传递给大皮带轮,再通过大皮带轮将主轴的转动传递给钻头,就这样实现了钻孔的过程。
3.3.1 传动机构的设计与计算
在本课题中,选用带传动的传动方式是因为其自身的优点:传动稳定,便于拆卸与安装,不使用润滑油等。根据本文中需要设计的传动机构功能,选用结构简单,用于平行轴传动的开口传动。
传动带选用窄 V 带进行动力传动,窄 V 带承载层为绳芯,锲角为 40°,相对高度近似为 0.9 梯形截面环形带。窄 V 带还具有摩擦系数大,工作面与轮槽粘附性好,允许包角小,传动比大,能承受较大的预紧力,传递功率大等特点[39]。
关于带传动的参数设计计算:
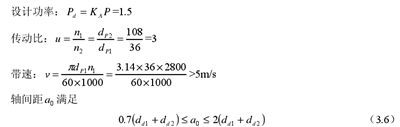
P -传递功率(kw) KA-工况系数(载荷平稳或变动微小时AK =1) 1n -小带轮转速(r/min)
2n -大带轮转速(r/min)
P1d -小带轮节径(mm)
P2d -大带轮节径(mm)
3.3.2 工作机构的工作流程及电机的选型
(1)工作机构的工作流程
电动机以每分钟 2800 转的转速将动力以 3:1 的传动比通过小皮带轮和皮带传递给大皮带轮,在大皮带轮和轴套之间用平键连接,以保证主轴转速的正常运行。在轴套的外侧的前后,存在两个铜质的外轴套,并和轴套之间保持一定的缝隙,以减小主轴运动时所产生的摩擦力。其中,两个铜质的外轴套分别通过三个铆钉固定在钻孔工装的框架上。为方便使用,钻头套是工厂内部自行加工的,它是上下半径不等的两个圆面构成的圆锥体,中间是钻头直径的通孔。在椎体直径大的一面,用车床车出大概 10mm 厚的螺纹,并切成均匀的四等分。将钻头放入钻头套后,用圆形螺母对钻头套进行预紧,以便将钻头固定在钻孔工装上[40,41]。
由于每两级叶轮之间的距离相对小,致使普通的钻床无法对末叶片销孔进行钻削。本课题中的钻孔机构就是根据转子叶轮末叶片销孔的特殊情况而设计的钻孔装置。转子中,两叶轮间的最小距离为75m,所以对于钻孔工装中框架的设计,在满足强度的前提下,尽可能薄一些,以便顺利完成整个钻孔过程。
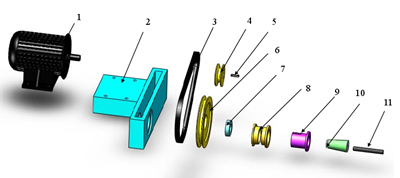
1-电机 2-框架 3-皮带 4-小皮带轮 5-键 6-大皮带轮 7-圆形螺母8-铜质外轴套 9-轴套 10-钻头套 11-钻头
图 3.10 传动装置爆炸图
钻孔过程:首先将钻头装进钻头套,再把钻头套安置到轴套内,用圆形螺母将钻头套锁紧,固定到工作机构中,注意安装后的露出的钻头长度和整个框架厚度之和要小于叶轮之间的最小距离;将传动装置的电机接上三相电源,而后钻头主轴转动,摇动 X轴手柄,使钻头对准划线后预钻孔位置,先用较小直径的钻头进行钻削,而后再用图纸要求销孔大小直径的钻头进行钻削。在钻削过程中,无法一次顺利完成整个钻削过程,将预紧钻头套的圆形螺母旋松后,用卡钳将钻头伸长到能够将叶轮钻透长度,进行第二次钻孔,直到完成通孔钻削为止。而后逐个孔进行钻削。钻削完成后,再次旋松钻头套上圆形螺母,用卡钳将钻头放到可以顺利将钻孔工装摇出的长度,将其旋出。至此完成一个钻孔周期[42,43]。
(2)电机的选型
在工厂中一般用于加工的电机均为三相交流电源。在本设计中,在电机的选用上沿用了原有的三相异步电机。选取 Y 系列 Y-90S-2 型三相异步电机,额定功率 1.5kw,电机转速 2800r/min。该电机具有结构简单,效率高,价格低,维修方便等优点。
3.4平衡装置的机构设计与计算
本课题中的平衡装置的作用是平衡掉整个装置的重力,理论上使其处于一种失重状态,使其运动平滑,操作省力,可以大大减轻劳动强度,提高工作效率。平衡装置在 Z向进给装置的方形螺母出现问题时,使其防止突然坠落,并使其处于三维空间的悬浮状态。
平衡吊夹具操作简单、方便,所以只要移动手柄工件物料即可随动。
3.4.1 平衡装置的总体设计与受力分析
本课题中平衡装置包括小型移动起重机和弹簧平衡器两部分。小型移动起重机由横梁,立柱,车轮和配重片等组成。为防止小型起重机发生侧翻,加配重片以使装置达到受力平衡。
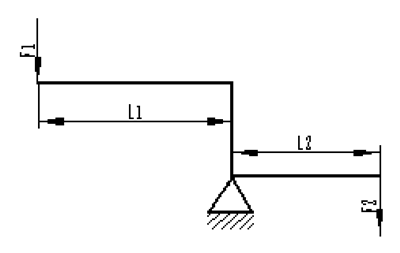
图 3.11 平衡装置受力分析图
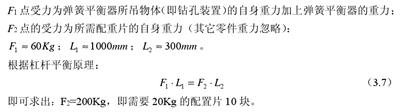
3.4.2 弹簧平衡器与葫芦的比较
弹簧平衡器的能量来自于在弹簧平衡器内部的蜗卷弹簧,蜗卷弹簧处于一种蜷缩状态,凝聚着弹性势能,使平衡器吊起的重物与弹簧的拉力相抵消,使重物悬挂在半空中。它的工作原理实际上使平衡器内的蜗卷弹簧的弹性势能与重物的重力达到平衡。这种弹簧平衡器使重物处于失重状态,大大降低了操作工人的劳动强度,提高了劳动生产效率。弹簧平衡器还可以节约空间,降低成本。
葫芦属于小型起重设备的一种,它主要是通过钢丝绳或链条,来带动取物装置运动的起重装备。葫芦主要是起到承上启下的过度作用,结构简单,易操作,但安全系数低,无保险装置。而弹簧平衡器自身存在优点是葫芦所不能及的。第一,弹簧平衡器存在保险装置,当其内部的弹性势能不足以平衡掉悬挂的重物时,其内部的弹簧会断裂,起到保险的作用;第二,弹簧平衡器能用较小的力移动重物,可以节约很多不必要的人力[44]。
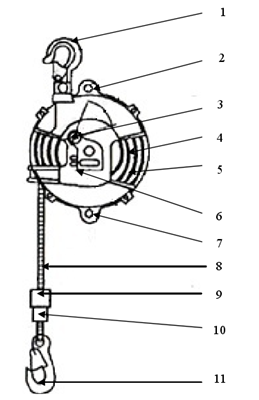
1-挂钩 2-安全孔 3-拉杆止动销 4-塔轮 5-钢丝强固定螺栓 6-调节蜗杆 7-绳拖动移动孔 8-钢丝绳 9-缓冲橡胶 10-铝管 11-吊钩
图 3.12 弹簧平衡器结构图
3.4.3 弹簧平衡器的选型
由于钻孔装置的质量在 50Kg 左右,故弹簧平衡器应选称重 60Kg 的型号,其中要考虑弹簧平衡器自身重量。
表 3.2 弹簧平衡器工作参数表

3.5 本章小结
本章对汽轮机转子末叶片销孔的加工装置的各个部分的重要机构的设计与选型进行了系统的介绍,包括固定与夹紧装置的设计,其中一面两销的定位方式的选用与说明和快速卡钳的原理及选用;进给装置的机构设计与计算,其中包括 X、Y、Z 方向螺旋传动副的选用,导轨和滑块的选用,手柄转向机构锥齿轮的选用,轴承的选用等;传动装置的机构设计与计算;平衡装置的设计与选用等。
投稿箱:
如果您有机床行业、企业相关新闻稿件发表,或进行资讯合作,欢迎联系本网编辑部, 邮箱:skjcsc@vip.sina.com
如果您有机床行业、企业相关新闻稿件发表,或进行资讯合作,欢迎联系本网编辑部, 邮箱:skjcsc@vip.sina.com
专题点击前十
| 更多