基于动态特性分析的机床主轴装配故障诊断硏究(中)
2017-7-13 来源:北京交通大学 作者:李凯旋
3.主轴箱测试系统的构建
本论文主要针对VCL850的主轴箱区域装配问题开展研巧。需要构建相应的测试系统对主轴箱区域的信号进行采集、保存、离线处理、分析,进而确定主轴箱区域存在何种类型的装配故障问题。因此本章重点介绍测试系统的总体结构设计、硬件的选用L义及软件的功能特点H方面的内容。
3.1测试系统的总体方案设计
针对主轴箱区域,需要检测的内容包括;主轴箱相关区域的振动信号,主轴运行时的轴屯、轨迹等。因此需要满足如下要求;
(1)可从满足机床工作频率范围内的数据精确采集。
(2)可同时采集多组、不同的信号类型。
加速度传感器主要测试VCL850主轴箱区域(径向、轴向)附近的振动信号,电锅流位移传感器主要测试主轴运行状态下的轴也轨迹,光电传感器用于标定键相信号,激光位移传感器用于测试主轴运行状态下的径向跳动量。
测试系统的总体方案设计如图3-1所示。
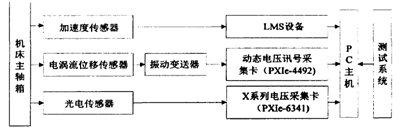
图3-1測试系统的总体方案设计
3.2测试系统的巧件选型
选择满足测试要求的硬件是满试系统的物理基础,选择的硬件直接影巧到測试的结果,因此必须选择合理的測试硬件,
(1)传感器的选用
1)本论文选用PCB公司生产的35A16型的压电加速度传感器,内置1C放大器,将传统的压电加速度传感器与电荷放大器集于一体,能够直接记录、方便与采集设备进行连接,简化了测试系统,提高了测试的精度与可靠性,同时它具有较高的信噪比,传感器体积较小,同时在检测范围内具有良好的线性特性,实物图及巧主要参数指标如表3-1所示。
表3-1加速度传感器主要参数指标
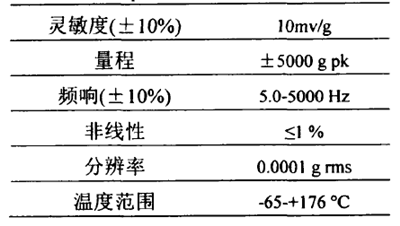
2)电渦流位移传感器传感器采用bently公司的3300XL11mm型产品,与振动变送器一并使用:电祸流传感器用于检测被测金属导体与探头端面之间静态和动态的相对位移的变化检测到的振动信号,振动变送器负责将振动信号按照比例变送成4至20mA信号。能够连续准确的采集到转子在运行状态下的多种参数指标,例如主轴运巧状态下的径向跳动豊、轴向位置W及振幅。实物图及其主要参数指标如表3-2所示。
表3-2电锅流位移传感器主要参数指标
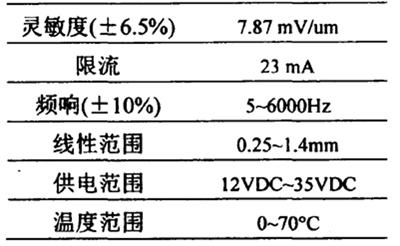
3)光电传感器与PXIe-6341电压采藥卡配合,W转子持定位置作为标记,获得高低电平信号与电祸流位移传感器相互配合,得到相位信息。
数据采集系统
本论文主要利用NIPXIe ̄4492、NIPXIe-6341数据采集卡和LMS数据采集系统完成信号的采集工作。
1) NI PXIe>4492是一款专为声音和振动应用而巧计的高精度数据采集模块。最高采样率可达204.8KHZ,可携带8通道4X InfiniBand连接器与BNC型接头传感器连接。实物图及其主要参数指标如表3-3所示。
表3-3 PXIE-4492主要参巧指标
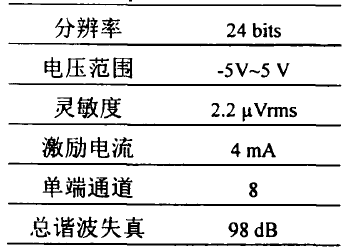
2) NI化Ie-6341具备4路32位计数器/定时器,可高级定时和触发,配有NI-STC3定时和同步技术,针对PWM、编码器、频率、事件计数等功能均能满足需求。实物團及其主耍参数指标如表3-4所示。
表3-4 PXIE-6341主要参数指标
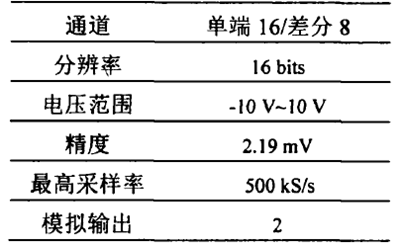
引本课题采用LMS公司的LMS数据采集设备,如图3-2所示。LMS数据采集设备专业用于对噪声、振动、声学和疲劳耐久性能测试,利用LMS数据采集设备对实验对象的输入输出信号巧行采策分析,巧现对未知巧障源位置的有效识别。
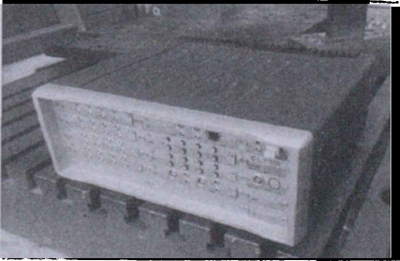
图3-2LMS数据采染设备
3.3测试系统的软件总体设计
本论文采用的是美国国家仪器(N1)公司研制开发的LabVIEW软件进行编程设计。这种閱形化编辑语言便于上手,使用这种语言编程时,辖本上不写程序代码.取而代之的是流程图或框图。同BASIC和C-样,LabVIEW也是一套通用的编程系统,内部配置可完成任何编程任务的庞大函数库。它广泛的应用于测试测量、控制、仿真、快速开发、跨平台运行等各个领域。
本论文通过LabVIEW软件将本论文的研巧内容设计成不同的功能模块,主要包括:加速度信号的测试和位移信号的测试。其中两个领域里面又由不同的子模块构成。具体包括;原始数据的采集、滤波、隔直、频谱分析、轴屯、轨迹测试、数据保存、故障识别等功能。软件测试系统的功能模块如图3-3所示。
A.加速度测试模块
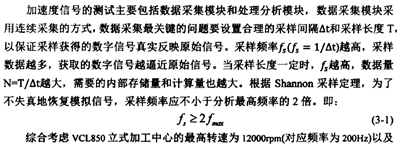
NIPXIe-4492最离采样率可达204.8KS/S两方面因素,设置采样率40%Hz,采样数4096。
加速度传感器共有6个采集数据通道,首先通过数据采集模块将原始数据写入计算机,然后通过数据分流,分配到单数据分析模块,进行时频域分析,也可对特定频率的信号幅值进行监测。由于选用连续采集的方式,程序始终处于while循环状态,.需要LabVIEW软件的生产者-消费者模式对循环数据实时输出,保存。也可在离线状态下对数据进巧处理分析。加速度信号的程悼框图如图3-4所示。
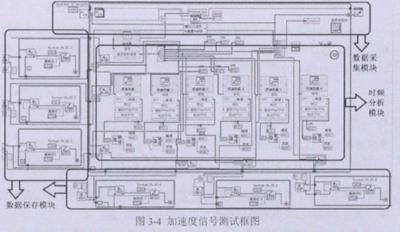
B.位移测试系统
位移测试系统主要将电祸流传感器测得的信号进行采集、处理、分析。其数据采集模块、处理分析模块同加速度测试系统,由于两路电锅流传感器同时采集且互成90度角,需要对这两路信号合成,实时显示主轴运行状态下的轴也轨迹。由于整个测试界面比较复杂,下面主耍介绍几个模块:(1)相关滤波W:带滤波信号为带有谐波、直流偏置(C)、随机噪声(7^(0)等成分的复杂信号y的,表示为;
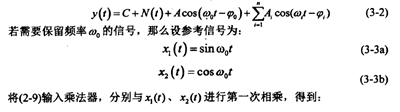


相关滤波器的程序巧图如圈3-5所示。
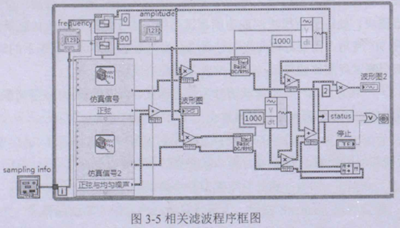
(2)相位测量
本论文可根据多重相关法和FFT分析法对相位进行测量。多重相关法可L:A有效消除随机噪声对主信号的影响,设两组含随机噪声的两路信号为x(f)、y(<)表达式为:
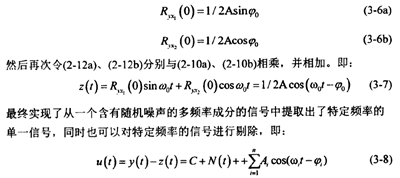
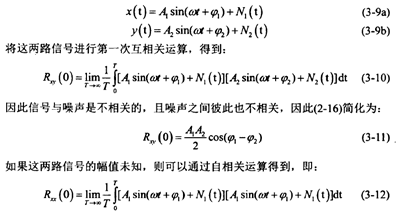
利用多重相关的方法,可w更有效的去除外界噪声干扰,综合考虑本论文采用二重相关法测试电锅流位移传感器与光电传感器测得的信号相位差,程序框图如图3-6所示:
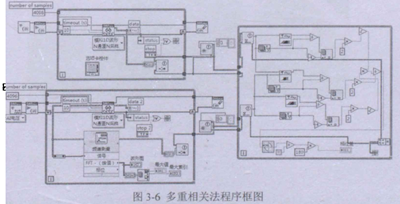
利用X、Y两向电祸流位移传感器和光电传感器测试对主轴的轴必轨迹进行检测,轴‘6轨迹测试的流程酬图3-7所示。
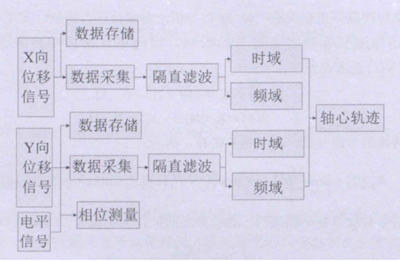
图3-7轴屯、轨迹測试的流程困
3.5本章小结
本辜苗先介绍了机床主轴箱区域常化的几种主要的装配故障类型,产生这几种故障的机理和对应的信号将征,为接下来的机床主轴箱医域检测、故障类型的判别提供了理论依据;其次介绍了对主轴箱区域进行捡测之前选用的硬件设备和相关技术参数,利用LabVIEW设计了主轴箱区域的检测系统和主耍的功能模块,为接T来的信号检测做好准备。
4.主轴箱装配故障的模拟实验
第二章主要针对主轴箱区域可能存在何种类型的装配故障及其内在机理进行了分析研巧,第H章就围绕主轴箱区域构建的测试系统进行了详细介绍。为了更好的对主轴箱区域的装配故障类型进行判断,需要在实验室开展针对性的模拟实验,观察不同的装配故障类型在时域、频域、轴也轨迹等表现什么样的信号特征。方便后续去机床现场进行信号测试时提供一定的数据参考。因此本章针对主轴箱区域几种主要的装配故障类型开展了相关的模拟实验。
如图4-1为转子实验台,由模拟台调速器控制转速大小。可通过对转子实验台上的不同部件进行人为的装配调整,模拟实际工况的不同类型的装配故障。图中可看到,利用第H章选用的硬件和构建的测试系统对转子实验台进巧检测分析。两个电祸流位移传感器互相垂直,测试转子在运动状态下的径向跳动量;光电传感器在标记位置确定基准相位:光电传感器照射到标记位置时为高电平,其他位置为低电平。
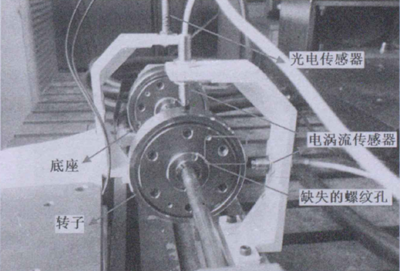
图4-1转子实验台
4.1动不平衡实验
图4-1的转子某部位存在缺失螺钉,模拟动不平衡。模拟台调速器将调整转子L的转速,800巧m左右的转速为例,得到的信号特征如图4-2所示。
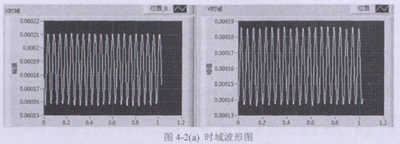
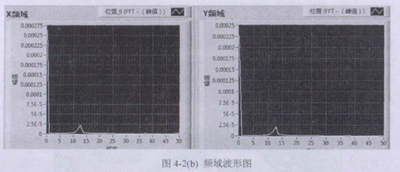
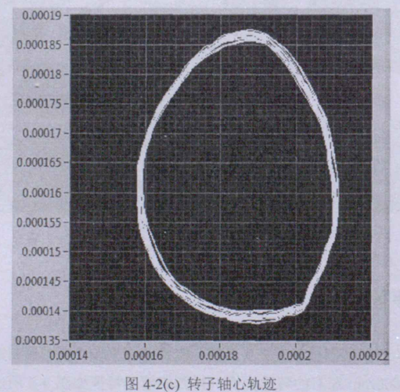
适然存在直流分量,但不影响信号特征。两个电锅流传感器的相位基本稳定在57°和150°左右,证明动不平衡位置与基准相位呈57°左右夹角,两个电巧流传感器互成93。夹角。动不平巧的信号特征主要表现为:
(1)在转子径向测得的频谱图上,频谱能量集中在基频(转子转速对应的频率),转速频率成分有突出的峰值;
(巧转速频率的数倍于基频的频谱幅值很低,时域上的波形接近于正弦波,且基频对应的幅值随转速的升高而变大,相位比较稳定。
(2)由于转轴在各个方向上的支承刚度存在差别,转子不平衡表现在x、y方向的幅值也不同,转子的轴屯、轨迹接近于楠圆形。
4.2不对中故障实验
将转子实验台的一端底座用垫片垫离造成两端底座商低不平,使转子与转轴形成一定夹角,模拟不对中问题。利用模拟台调速器调节转速,WnOOrpm左右
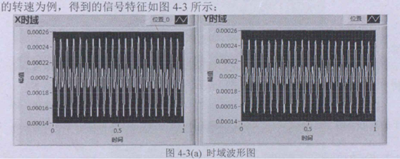
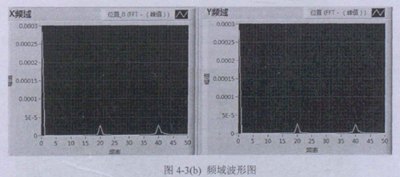
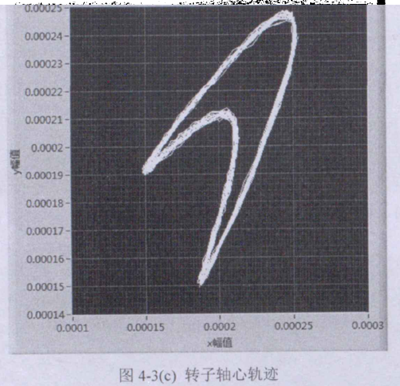
可L义管到转子不对中时,运转状态下的—倍频幅值明显,轴屯、轨迹呈香蕉形。综合本实验及文献可知,转子不对中引起的故障主耍信号特征为",iwi:3
(1)若对振动信号进巧频谱分析,其频谱成分主要W—倍频和二倍频为主转子不对中的程度越严重,二倍频的幅频特性越明显,其至超过一倍频。
(2)从转子径向检测其信号,其两个方向的时域波形类似崎变的正弦波。转子的轴屯、轨迹呈香蕉形I当二倍频的幅值更加明显时,其轴'。轨迹呈8字形。
4.3松动故障实验
使底座的螺巧略为松动,模拟松动故障。将模拟台调速器调到较低的巧速,L:A600巧m为例,为了更加便于观察,对信号采取直流分量隔离的措施。测得的信号特征如圓4-4所示:
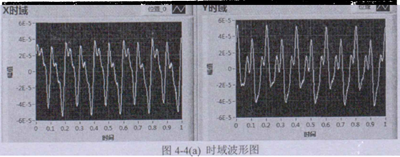
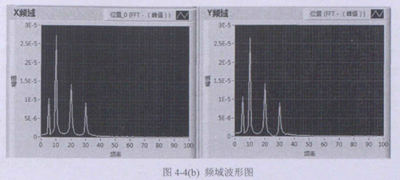
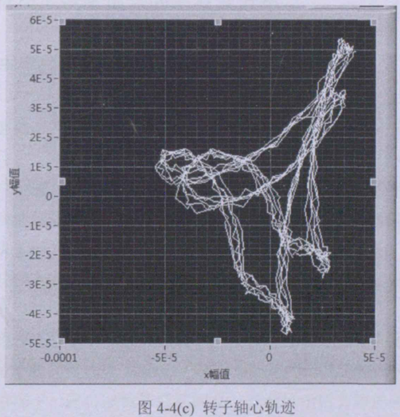
综合本次实验及文献调研得出旋转机械的松动故障其信号特征表现为IWI:
(1)对振动信号进行频谱分析时,产生松动的对应方向与其他方向的频谱信息差异很大:产生松动的方向除了基频信号、出现了更多的倍频,甚至分数倍频,松动方向的振动越强烈、高频信息越丰富;其他方向的频谱信息较少。
(2)松动使得机械结构的结合面出现间隙,机械系统表现出非线性特征。出现松动故掩的转子其轴也轨迹更加混乱、重也漂移。
4.4本章小结
棉棚转f自验自壯科日駐獅劍日雜类麵浦織验,分别获得了动不平衡、角度不对中、松动三种故障在工作状态下的时频域及轴也轨迹的信号特征,可W得出初步结论:动不平衡故障与基频相关轴屯、轨迹表现为楠圆;角度不对中故障与基频二倍频相关轴屯、轨迹表现为香蕉形或外八字形,松动故障的频域特征较为复杂,轴屯、轨迹无规律。为接下来对工作现场的主轴箱区域的信号采集及分析提供了数据支持。
5主轴箱区域的信号采集及分析
通过就不同类型的装配故障进行模拟实验,对不同类型装配故障所表现的信号特征有了一定的认识和了解,本章主要针对机床现场,对运行状态下的主轴箱区域的信号进行采集及分析,主要包括;加速度传感器位置如何确定、加速度信号的采集分析、主轴运行状态下径向位移信号、轴屯、轨迹的采集分析、故障类型的识别判定等。
5.1机床主轴箱加速度信号的采集及分析
5.1.1加速度传感器位置的确定
加速度传感器对故障产生时伴随的振动信号十分敏感,因此需要采集时域内主轴箱的振动信号,iU便用于后续的分析研巧。如何利用有限的传感器放置在主轴箱的最佳测试位置,便于后续的检测与分析,这是一个命题,模态试验分析领域称之为:响应点优化布置IW。本论文借鉴模态试验中常用的模态动能法和有效独立法,为解决实际工况下传感器优化布置的问题提供一种思路。
模态动能法|M1(MKE)W测得的模态动能最大为目标来选择传感器的位置进而提高结构动态响应测量。有效独立法1^]巧1)在模态动能法的基础上每个传感器测点对模态向量线性独立的贡献最大为目标,逐步删除有效独立向量具有最小值的节点,与此同时不断优化改进Fisher矩阵,最终达到的效果使感兴趣的模态振型在较少测点的情况下,尽可能保持线性独立,在測试中用有限的传感器获取最大的模态信息。
本文结合上述两种方法,应用于机床主轴箱区域,在工作频率下实现对传感器的优化布置,将不同頻率下对应的工作变形认定为不同阶模态振型,利用有限的传感器实现对不同频率下主轴箱最大形变区域的有效识别。
对于振动系统:系统振动具有动能(T)和势能(U),可表示为:
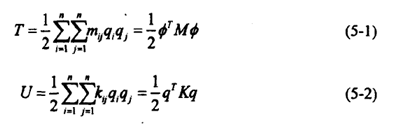
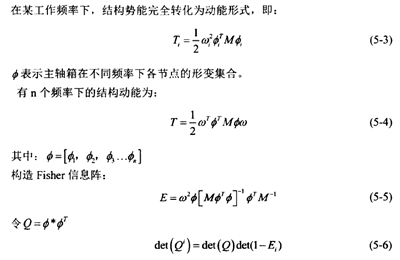
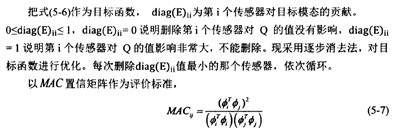
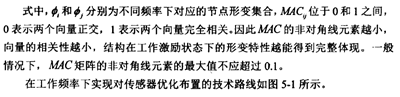
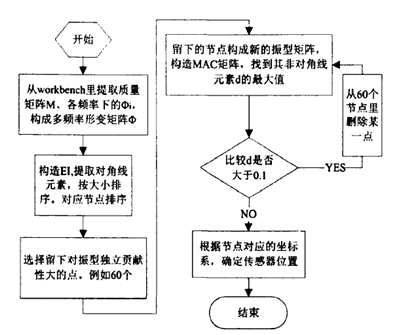
图5-1传感器优化布置的巧术路线
主轴箱在空转状态进行测试,受到的外界激励较弱,主要受到主轴自身转动产生的离屯、力作用,利用ANSYSWorkbench对主轴箱区域进行仿真分析,模拟实际工况,如图5-2所示。ANSYSWorkbench作为线性分析软件,外界激励的变化不会改变主轴箱区域的应力分布情况,轴箱区域的动态应力、应变幅值只会等比例的发生改变。因此对主轴箱区域施加的边界条件为:四端固定约束,主轴附近受到离屯、力矩设定为lOOON.mm,经过网格划分;53769个节点。
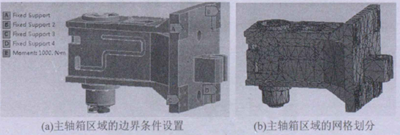
图5-2主轴箱仿真模型
主轴一般的工作转速为3600?9600rpm,对应频率区间为60 ̄120Hz,主轴箱在实际工作状态下,不同频率点对应的工作变形是不同的,称之为工作变形分析(ODS),利用有限的传感器实现对不同频率下最大形变位置的有效识别。这与利用有限的传感器实现对不同模态振型的有效识别有着共同之处。由于机床的工作频率区间在60~160HZ,因此本论文的分析频率点分别为60、80、100、120、140160Hz,表5-1分别为60、80、100、120、140、160Hz 下的形变。
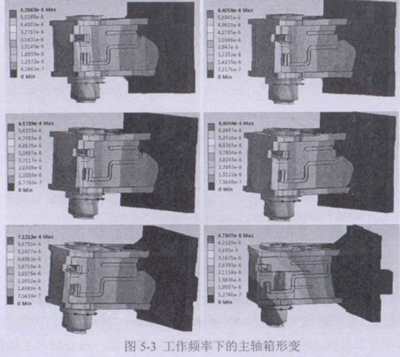
假设经过有限元网格划分后的节点均可作为传感器布置的位置,即所有节点布置加速度传感器,得到的mac矩阵值如表5-2所示:
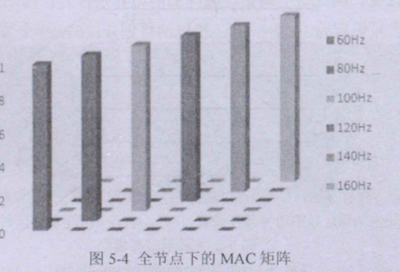
由此可见利用MAC矩阵作为评价齒数,在全节点下的非对角线最大元素仅为8.01E-05,完全对工作频率下的主轴箱形变实现了有效识别。
由于存在53769个节点,首先从ANSYSWorkbench中筛除没有形变的节点,主要分布在与固定约束靠近的区域,图5-3中的蓝色区域。这样节省了大量的计算时间。利用MATLAB软件对节点逐步消减,由图4-2可知,60个节点之前,明5-:5)式作为评价南数,60个节点之后L;|(5-7)为评价函数。传感器的求解走势如图5-5所示:从3800个节点到60个节点,再从60个节点到1个节点两个阶段。横坐标为节点数,纵坐标为MAC矩阵非对角线最大元素值。
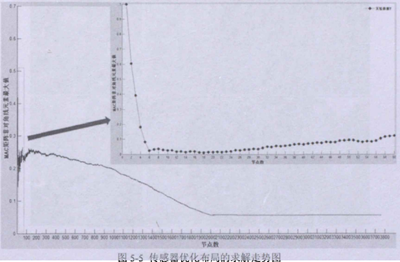
由图5-3可知,在剰余6个节点(即传感器数目为6个)的时候,既经济又能巧兼顾识别各个频率下最大形变效果。剩余数目为30时,在主轴箱区域的节点分布如图5-6所示。
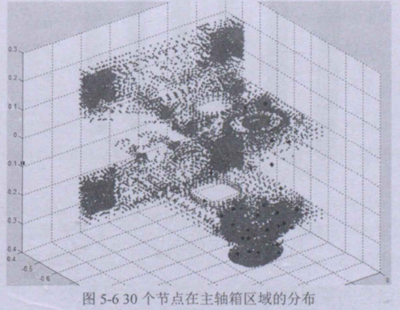
可贈到:有的节点在主轴箱的内部,实际上传感器是没办法放置的,经过排除,齡6个节点分布在主轴箱上、中、下、底、左、右六个位置,誦5-7 所示。

剩余六个节点位置的MAC矩阵如图5-8所示。非对角线元素最大值为化081576,主轴箱在各频率对应下的形变能够得到有效识别,满足要求。
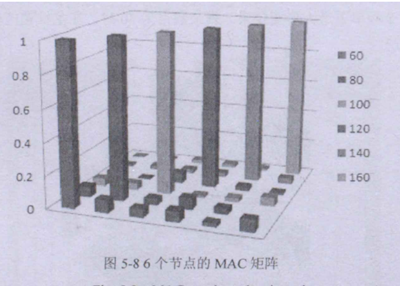
5.1.2加速度信号的采集与分析
本次实验レッ南通化床某台存在故障但未发现原因的VCL850立式加工中屯、为对象,首先在化床开启的状态下对主轴箱区域的振动信号进行检测及分析,由于主轴的转速区间为48?12000rpm,拟定W600rpm为一间隔,从60(K9600rpm测试主轴箱区域的振动情况。测试现场如图5-9所示。
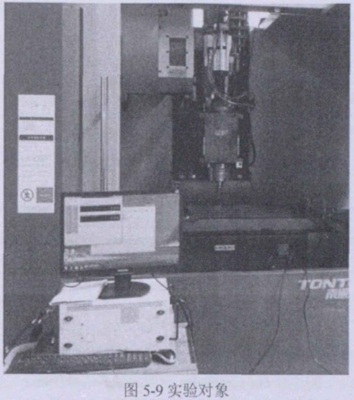
在主轴空转之前对冷却循环液开启前后的测试数据进行了分析,在六个部位观察频域图,发现未产生明显变化,只在高频区间产生了影响。说明:冷却循环液对主轴箱区域的影响不大。主轴箱中部的测试数据为例,如图5-10所示。
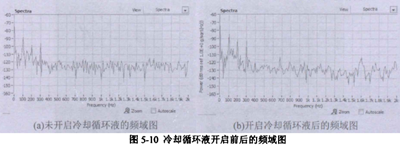
利用H向加速度传感器,可W同时检测主轴在不同转速下的轴向和径向的振动情况。现;^^主轴前端为例,观察主轴在600?8400rpm之间的时频域圍:在0?3600巧111区间,(^^?(18(分贝)表征其幅值,虽然从1800巧〇1开始,主轴转速对应频率的幅值开始突出,但其轴向、径向的振动特征与其他频域幅值相差不大,幅值的数量级在le-6级。主轴在径向的振动特征与轴向比较,幅值更小,数量级在5e-7级,W轴向信号特征为代表如图5-11所示。
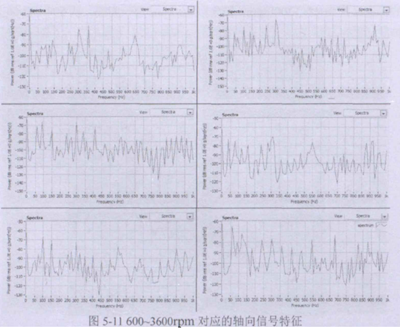
从4200rpm开始,信号特征变得明盈,主要表现为一倍频二倍频。W主轴前端上部为例,分别4200rpm、7800rpm为例观察时频域围。化图5-12所示,左列为时域信号,右列对应频域信号。
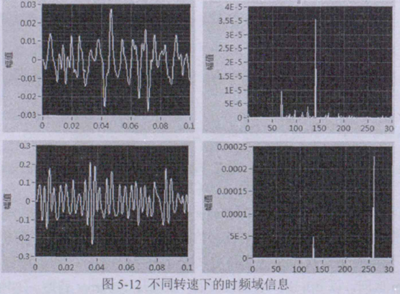
利用MATLAB将K面将主轴上中下底左右六个部位巧不同转速下的轴向、径向幅值进行对比(横坐标为转速,纵坐标为幅值,蓝线为轴向,红线为径向)如图5-13所示。可以发现轴向的振动信号明显强于径向。
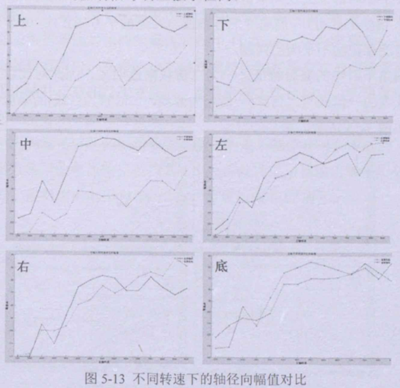
对比主轴箱区域上中底左右(线条颜色分别为黑绿红蓝紫)五个部位的轴向、径向幅值,如图5-14所示。可发现轴向的信号随转速变化的振动趋势基本一致,径向的信号随转速变化的振动趋势却差异很大。
(1)轴向在上中底左右五个部位的幅值走向基本一致,上中下部和底、左右侧的幅值成平行关系,这是由于主轴箱在底端、左两端、前端的壁厚各不相同,因此测得的信号强弱也会不同。
(2)径向在上中底左右五个部位的幅值走向出现差异。左右侧的幅值基本fc成稳步上升态势,上中下的幅值随转速呈无规则的变化。主轴巧电机通过同步内齿带轮连接,可能由于带轮张紧力的作用,导致主轴局部受力(主轴顶部)过大,因此分布在转子不同部位的径向幅值产生差异。
(3)由(2-1)式可知,加速度信号幅值与转速的平方成正比,由图5-14可知,主轴区域可能存在动不平衡的问题。由于偏角不对中的显著特征之一为二倍频幅值明显,因此对比上中底左四个部位为代表的一倍频与二倍頻(一倍频为蓝线,二倍频为红线)的幅值也能印证上述结论,如图5-15所示。
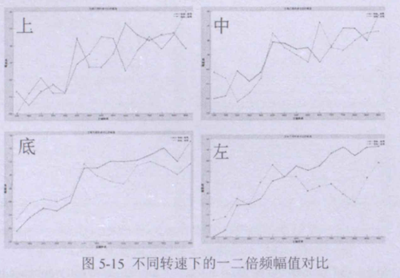
为了进行验证由加速度化睡器测试分析得出的结论,下面针对主轴运斤状态下的轴屯、轨迹进斤测试、分析。
5.2机床主轴的轴心轨迹测试
W同样的加工中屯、为实验对象,对其主轴运行状态下(600巧m?8400rpm区间)的轴屯、轨迹进行检测,观察其轴也轨迹的变化情况。轴‘心轨迹实验现场如图5-16所示。
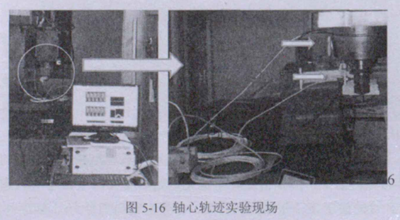
实验注意事项:
(1)传感器的安装:两个电祸流传感器彼此要尽量保证90度,由于电祸流传感器探头据测试对象的测量区间在0.41?2mm,因此既要保证安装距离在规定量程范围内,又要防止主轴开启时剧階到探头,造成传感器损坏。
(2)由于主轴开启后和每次变速后,都会引起工作台振动,必须在将传感器放置在一个有足够重的质量块。
(3)由于电锅流传感器经振动变送器输出的电压幅值在15.6V,而PXIe-4492数据采集卡的电压输出范围为±5V,因此在变送器输出端采用分压电阻的方式,使得输出电压为3VW内。原理如图5-17所示。

图5-17分压电阻图
在1200?8400 rpm区间,检测主轴的轴心轨迹,采样率为4096Hz.采样数为4096,其时域频域随着转速的改变基频、倍频亦发生改变,但轴屯、轨迹基本保持一致,W3000rpm、7800rpm 为代表,图5-18(a)为3000rpm的时域图、图5-18(b)3000rpm的频域图、图5-18((:)为3000巧111的轴屯、轨迹图;
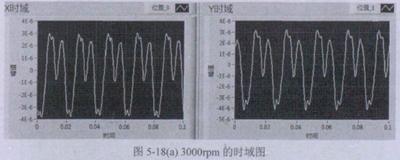
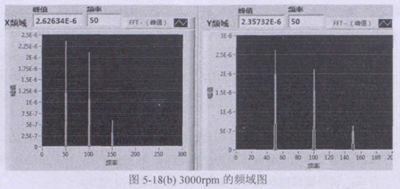

图5-18(c)的左侧为滤波后的轴屯、轨迹图,图5-18(c)的左侧为滤波后的轴必轨迹阐,滤波采用己特沃兹滤波器型低迪滤波器,截止频率为500Hz。图5-19(a)为7800rpm的时域图、图5-l%b)7800rpm的频域图、图5-19似为7800rpm的轴屯、轨迹留,低转速下的轴也轨迹较高转速的轴也轨迹更为清晰,但总体均为外8字形,主耍由一倍频、二倍频构成,也出现了H倍频,这与偏角不对中的信号特征描述是一致的,同时也印证了加速度信号测试后得出的结论:
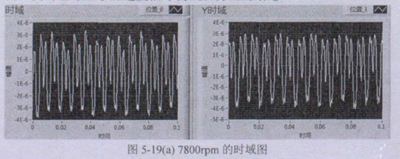
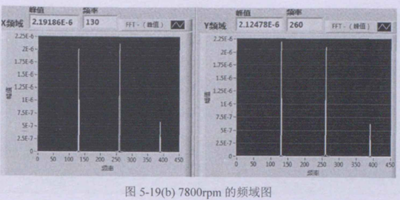
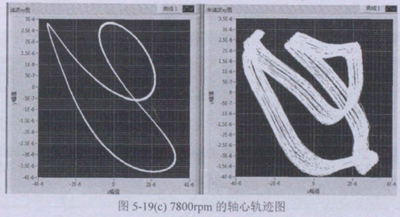
针对上述实验对象的实验结果,现对某台正常使用的机床主轴轴必轨迹进斤测试,观察其轴必轨迹。如图5-20所示。
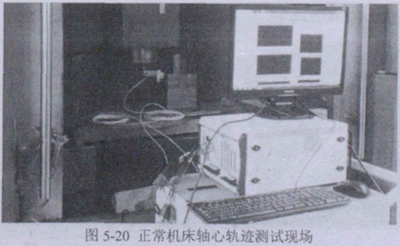
在4200rpm下,采用相关滤波器对采集的数据进行处理后的时域波形如图5-21(a)所示,频域波形如图5-2l(b)所巧,滤波前后的轴屯、轨迹如图5-21(c)所示(主要滤掉5〇Hz的交流电源频率)。
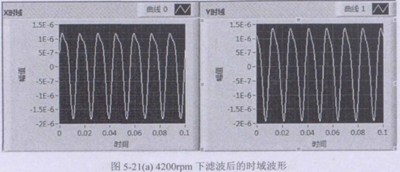
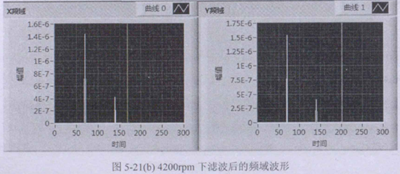
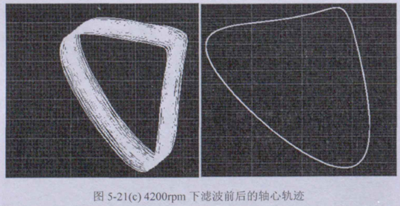
对比两姐数据,可发现:
(1)虽然本次实验对象工作状态下的主轴依旧存在二倍频,但与未调试机床的实验数据相比,幅值并不明显。最大信号为基频信号,轴必轨迹为类圆形。
(2)未调试机床的信号幅值在l5^lm左右,测得的可正常使用的机床信号幅值在如m左右,从这个角度也可看出,未调试机床的主轴径向跳动过大。
(3)由(2-1)可知,动不平衡的表征为基频信号的振幅与转速的平方成正比,从两次实验对象的数据看,基频的振幅均稳定在一定范围内,因此主轴不存在动不平衡问题。
图5-22为VCL850主轴在1200?9600rpm范围的基频相位信息。可看出基频对应的相位信息并不稳定,也说明了主轴与刀柄安装位置不存在明显的动不平衡问题。
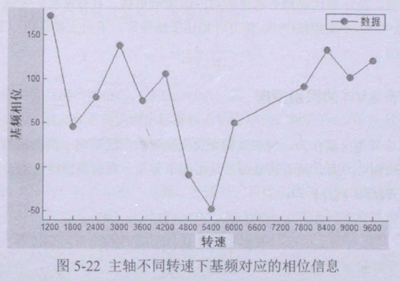
5.3基于轴心轨迹的故障类型识别方法
轴屯、轨迹是旋转机械的重要信号表征形式,目前轴屯、轨迹的形状识别作为判断设备故障的重要依据,在旋转机械(包括水电机组)的状态监测与故障诊断中得到一定应用IW1。通过轴屯、轨迹对应的图形形状的识别,可进一步分析设备振动的原因,得到故障征兆,及时采取措施防止机械巧障进一步恶化。长期的理论和实践研究已经确立了几种典型的机械故睹模式及其转子轴屯、轨迹形状的对应关系,几种常见的轴必轨迹图形及其故障原因见表5-1。
表5-1常见的轴必轨迹图形及其故巧原因

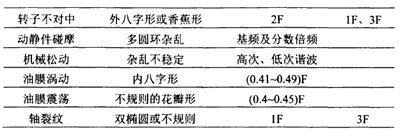
对轴屯、轨迹的识别本质上就是对二维图像的识别,主要包括特征提取、分类识别两个方面。特征提取是从轴也轨迹中提取能反应轴也轨迹本原的、重要特性的特征向量,能尽量代表轴屯、轨迹所对应的图形形状。目前常用的特征提取方法有SVD法IMW、不变矩法170-"1、傅立叶描述子法等等。下面主要介绍一下SVD法和不变矩法。
5.3.1基于SVD的识别原理
矩阵奇异值分解作为一种有效的正交变换目前广泛应用于数据压缩、信号处理、模式识别等方面。轴也轨迹图形是由两个垂直方向的波形信号组合而成。离散化设为乂(0、7(0,艮P:


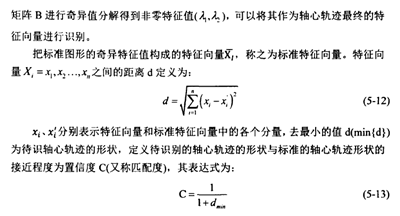
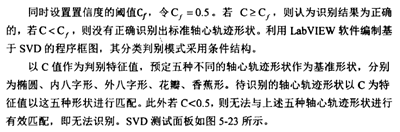
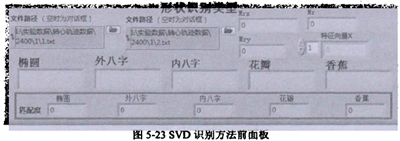
5.3.2基于不变矩的识别原理
不变矩法于1962年由Hu提出,并运用代数方法证明了其不变性,随后许多学者对不变矩进行了较深入的理论与实际应用的研究,不变矩的理论得到了逐步完善,在模式识别与图形处理等领域获得了较为广泛的应用ini。定义在平面上的二维函数/〇c,:V),它的p+q阶混合原点矩定义为:
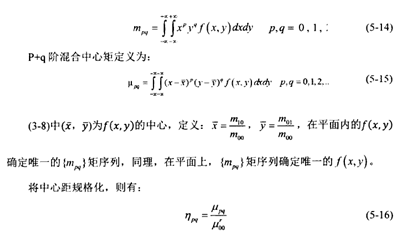
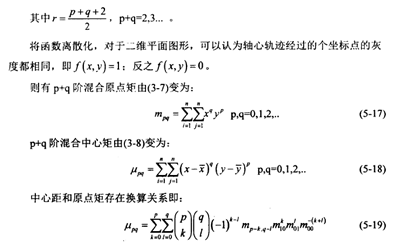
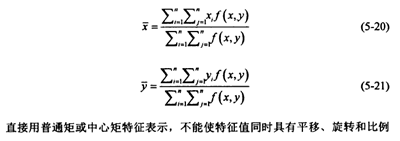
不变矩的特性。若利用归一化的中也矩,则特征不仅具有平移不变性,还具有比例不变性。这样,可L义利用归一化的中屯、矩的线性组合,达到待识别的图形具有平移、旋转、比例不变性的特征。HuMK利用代数不变量理论构造了韦个不变矩函数式。
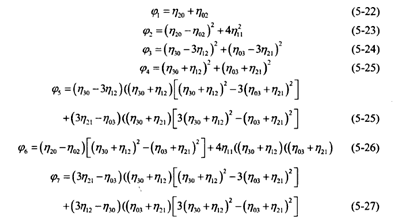
通过反复实验发现:七个函数在离散情况下对尺度缩放是敏感的,而且经过定性分析变化原因从之前的推到可tA得出W下结论:若图形尺度变化因子为P,则变化后的矩函数与原画数的关系为:
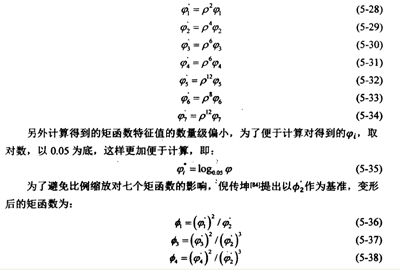
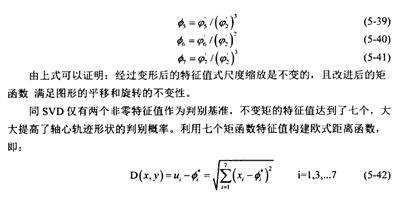
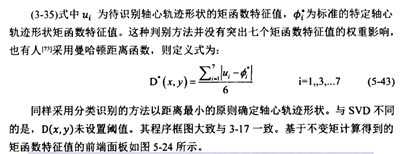
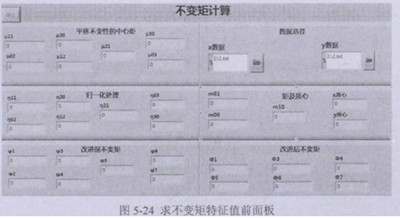
5.3.3VCL850主轴的轴心轨迹识别
利用LabV旧W软件编制几组不同的标准轴屯、轨迹形状,此作为不同主要的装配故障类型的轴屯、轨迹图形基准,同样利用LabVIEW通过基于SVD和不变两种方法对实验测得的轴也轨迹进行识别方法。相互垂直的信号表达式分别为x(t)和y(t),其表达式为;

利用LabVlEW软件根据(3-3如式设计得到不同形状的轴屯、轨迹合成信号五种不同类型的轴也轨迹形状:滿圆、外八字形、内八字形、花瓣形、香蕉形。如图5-25所示
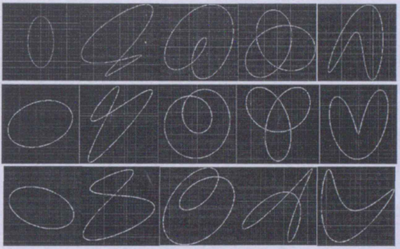
图5-25不同的轴心轨迹形状
每种类型的轴屯、轨迹形状求解H组,排除偶然因素的干扰,为后续的SVD法、不变矩法提供评价标准。
利用SVD法对VCL850立式加工中心测得的轴屯、轨迹形状进行识别,得到外八字形的识别结果,滤波前后的轴屯、轨迹识别结果如图5J6所示。
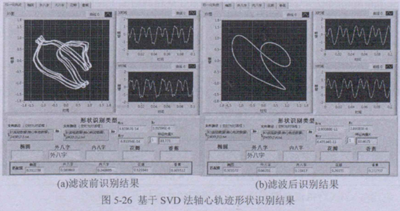
滤波前后形状置信度(匹配度)参数如下表5-2,表5-3所示:
表5-2未滤波的形状置信度参数

表5-3滤波后的形状置信度参数

由结果可UJ?看出基于SVD法实现了轴屯、轨迹形状的有效识别。但由于SVD法的特征值维数较低,待识别形状的置信度参数较低,针对局部变化敏感的轴屯、轨迹形状,此种方法的识别率更会降低。
基于不变矩法对图5-25的五种不同轴屯、轨迹的形状进斤矩函数计算,同时每种类型的轴屯、轨迹形状的函数值求平均,得到的毛个特征值如表5-4所示;
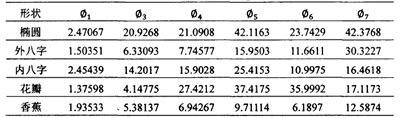
对实验测得的轴屯、轨迹形状进行矩函数计算得到的屯个特征值如表5-5所示:

利用(5-42)式对待识别图形进行计算得到的数据如表5-6所示。
表5-6基于(5>42)式的识别结果

利用(3-37)式对待识别图形进行计算得到的数据如表5-7所示。
表5-7基于(5-43巧的识别结果

由两种判别方式均可W得到正确的结果,但是内八字形和香蕉形的数据产生了很大的变化,从处理的数据结果发现使用(5-42)式作为分类识别过程中的判别依据较为合理。
将SVD法和不变矩法相结合,对轴必轨迹的形状进行判定:
1)当SVD法与不变矩法的判定结果一致时,认定判定结果正确。
2)当SVD法与不变矩法的判定结果不一致时,认定判定结果失效。
这样将同时考虑了两种方法,提高轴必轨迹形状识别的正确率。
由于表征轴屯、轨迹形状的特征值达到了七个,因此基于不变矩法识别的正确率较SVD法要更加明显,但基于不变矩法,即使同样形状,得到的特征值也是存在差异的。本论文结合两种方法对轴也、轨迹进行识别,提髙了识别的正确率。
5.4本章小结
本章在前面章节的基础上,利用构建的测试系统对主轴箱区域的振动信号进行了测试,有下成果:
(1)结合模态动能法与有效独立法,将应用于模态试验中的传感器优化布置问题运用到工作激励状态下的传感器优化布置问题上,提出了在工作激励下解决传感器优化布置问题的一种方法。
(2)对采集的信号通过分析发现:主轴箱区域的振动信号与主轴转速密切相关,基频、二倍频信号明显,属于不对中的故障特征,主轴区域的径向幅值随转速成正相关关系,属于动不平巧的故障恃征。
(3)对主轴轴也轨迹进行了在线测试,发现基频、二倍频信号十分突出,运行状态下的主轴轴也轨迹呈外八字形,符合角度不对中的故障特征,测试对象在不同转速下的基频相位并不稳定,说明主轴与刀柄安装位置不存在明显的动不平衡问题。
(4)利用SVD法和不变矩法W轴屯、轨迹作为故障的评价指标进行识别,并利用LabV W编写相关程序,基于两种方法对測得的实验数据进行了识别判定。最后将两种方法的优势结合起来,提髙轴也轨迹形状识别的正确。
投稿箱:
如果您有机床行业、企业相关新闻稿件发表,或进行资讯合作,欢迎联系本网编辑部, 邮箱:skjcsc@vip.sina.com
如果您有机床行业、企业相关新闻稿件发表,或进行资讯合作,欢迎联系本网编辑部, 邮箱:skjcsc@vip.sina.com
更多本专题新闻