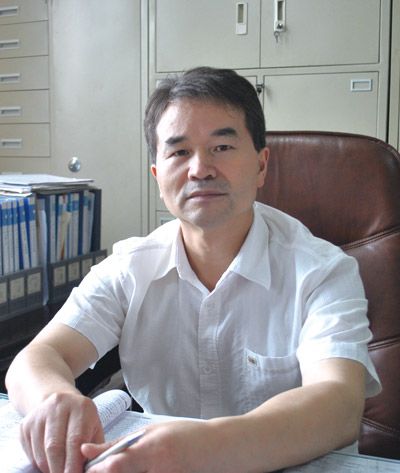
我国机床行业经过了近10 年的高速发展,特别是04国家科技重大专项实施后,各制造企业对产品进行了重新规划和全面的升级改进,的确取得了较大的进步,成功地提高了产品的可靠性和稳定性,但与世界先进机床相比,我们仍然存在较大差距,甚至存在深层次的技术问题。要解决这些问题,我认为应从以下几个方面着手:
提升设计理念
设计理念是一种工业文化,决定了产品的档次,理念跟不上,产品无论怎么做都会陷入“形似神不似”的境地。如设计的产品是二流产品,工艺能做的只是将产品做成二流产品中的一流产品。无法突破成一流产品。
(1)站在用户使用的角度进行产品设计,关注用户使用需求(质量、效率、成本)。
(2)主机和辅机同等对待。目前重主机轻辅机的现象十分普遍。机床防护、排屑、走管走线、隔热防尘、环保、宜人、可维修等常常没有得到应有的重视。
(3)机床问题都是主机制造企业的问题。不要让外配件、功能部件成为问题的借口,提高外配件的消化应用能力,正确使用、准确配置是关键。不要外配件一出问题就交给供货商。
(4)标准化、通用化、模块化设计是产品可靠性的重要保证,也是快速维修的必然发展趋势。
(5)强化设计的理论依据,尽快改变凭经验或简单地模仿设计方式。要提高设计分析手段。
提高耐心
任何技术产品都有一个逐步完善的过程,不经历长期的技术积累,则无法实现质的转变。
(1)行业导向的耐心。一个行业要想在短时间内实现质的飞越,这是不现实的,也不符合科学发展规律,机床行业作为基础更是如此。要科学地导向,不能使整个行业变得浮燥。要正视与世界机床先进企业之间的差距,要彻底消灭这种差距,不是一投入就能解决的,需要一个长期摸索、不断学习的过程,急是没有用的。
(2)企业的耐心。企业的资源是根据自身的优势配置的,也是有局限的,有限的资源只能用于有限的目标,尤其是处于社会配套不完备的情况下,过分依赖别人是无法做出精品的。由于服务领域的发展阶段不同,对产品的需求时段也不相同,此起彼伏的现象是很正常的,不能这山看着那山高,什么产品都想做,结果什么产品也做不好。同时还扰乱市场秩序,使行业步入无序和恶性的竞争状况。最终不但新产品没有成功,原有的产品优势也被削弱了。坚持有所为有所不为的产品发展原则,集中资源,做精目标产品。
(3)技术人员的耐心。技术人员需要克服急躁的情绪,冷静下来做大量扎实的基础技术工作。要从技术源头对产品进行全方位的梳理和改进,要树立品牌意识。目前在许多技术方面我们仍处于落后状态,如变形控制及补偿技术、机床刚性及抑振技术、机电联调技术、动态参数优化技术、虚拟制造技术、智能化技术等。都需要坚持长期不懈的努力和扎实的技术研究和消化应用工作。
(4)制造人员的耐心。要提升全体从业人员的精品意识,不要只对任务(甚至只对工时)负责,更重要的是对产品负责,对用户负责。要制定严格的考核和激励机制,激发员工的改善热情和精益求精的工作作风。
提高从业队伍水平
机床制造业经历了几次低迷,人才流失比较严重,形成了不同程度的技术断层,加上近些年来国外企业大量涌入,对技术人才进行了新一轮的争夺。在人才培养模式上应有新的思路,企业与大专院校和职业技能学校结对子是保持人才连续的方式。但更重要的是,应从国家战略层面提升行业的地位,给行业应有的爱护和尊重,形成良性的职业崇尚,吸引更多的人从事制造业。
企业要通过多种渠道对员工进行技术、技能培训,帮助员工快速成长。
注重细节
造成目前“形似神不似”的重要原因是各种细节未做到位。许多方面有意识,但不彻底。
工艺流程设计不细致,工艺的指导性和操作性不强(工艺方法不明确、工艺手段不完备),如装配该量化的未量化等,缺乏精细制造的认识,“差不多就行了”的想法较普遍。
提升职业敬畏,培养爱岗敬业精神和良好的工作习惯,才是注重细节的前提。
质量是产品的生命
质量是产品的生命,谁都知道,但一与生产任务冲突就不要命的做法时常发生。质量不能停留在口头上,要固化到骨子里。在质与量发生冲突时,首先强调“质”而不是“量”。
质量问题一定要消灭在制造企业内部,切不能拿用户做验证。坚持不合格产品决不允许流入下道工序。
提高从业队伍的质量诚信,树立“我做事我负责”的质量理念。
如果您有机床行业、企业相关新闻稿件发表,或进行资讯合作,欢迎联系本网编辑部, 邮箱:skjcsc@vip.sina.com