电火花线切割是一种直线电极的展成加工方法, 因为它使模具(尤其是复杂的模具) 加工工序简化、生产周期缩短, 而倍受人们的欢迎, 被广泛地应用于模具制造行业。数控电火花线切割机床利用电蚀加工原理, 采用金属导线( 钼丝)作为工具电极切割工件, 其主要用于切割淬火钢、硬质合金等特殊金属材料, 加工一般金属切削机床难以加工的细缝槽或形状复杂的零件, 在模具行业应用广泛。影响数控电火花线切割机床加工精度的因素主要有偏移量、取件位置、切割路线、起点、装夹与定位及引入、切出、超切、回退程序等。
1 反向间隙补偿量的测量
( 1)将磁性表座吸在X、Y 台面上, 将千分表夹在表座上, 移动X轴, 使千分表探头与线架下臂接触, 表的探头方向与X轴平行, 同时与X、Y台面平行。
( 2)移动X轴, 使表针指向千分表量程的1/3左右处;
( 3)在主菜单下F5(人工)菜单中按F2选择单步子菜单, 在单步菜单中, 按F6功能键选择步长为+ 100Lm, 按F1使X轴正方向移100Lm, 记取千分表上的读数X1, 再按F1使X轴正方向再移动100Lm, 记取千分表上的读数X2, 按键选择步长为100Lm, 按F1 移动X轴, 记取千分表上的读数X3, 这样将X= X3- X1即得到X 轴的补量。
( 4) 用同样方法测出Y轴的补偿量Y;
( 5) 在主菜单下按下F4(设置) 键, 进入设置功能子菜单, 按F2进入间隙设定子菜单, 分别按F1, F2, 按提示输入补偿量X、Y, 设入的补偿量以绝对值略小于测得值为宜, 如测得X轴为- 1. 5Lm 输入- 1Lm;
( 6) 反复( 1) ~ ( 5) 操作, 使测得补偿量值为最小, 注意, 再次测得的补偿量输入时应与上次的补偿量相加, 如系统已显示齿补量为3Lm, 又测得为- 1Lm, 则应输入2Lm 。
2 确定钼丝偏移量
编程时首先要确定钼丝中心运动轨迹与切割轨迹之间的偏移量, 如图1示,f=d/2+ z, 式中: d为钼丝直径; z为单边放电间隙。放电间隙与工件材料、结构、走丝速度、钼丝张紧情况、导轮的运行状态、工作液种类、供液情况和清洁程度、脉冲电源等因素有关。偏移量的准确与否将直接影响工件加工的尺寸精度。一般可根据脉冲电源参数与放电间隔的关系的基本规律估算出放电间隙[1] 。如DK7725e机床采用快走丝, 在加工电压等于60~ 80V 时, z= 0. 01~0. 02mm。对加工精度要求较高的工件, 此时多采用试切工件的方法来检测
3 保证加工表面粗糙度的措施
( 1)根据线切割工作的特点, 钼丝需要频繁地换向来进行加工, 钼丝在换向的瞬间会造成其松紧不一, 钼丝张力不均匀, 从而引起钼丝振动, 直接影响加工表面粗糙度, 所以应尽量减少钼丝运动的换向次数。在加工条件不变的情况下, 加大钼丝的有效工作长度, 可减少钼丝的换向次数,减少钼丝的抖动, 促进加工过程的稳定, 提高加工表面质量。
( 2)脉冲电源是影响加工表面粗糙度的重要因素, 脉冲电源采用矩形波脉冲, 因为它的脉冲宽度和脉冲间隔均连续可调, 不易受各种因素干扰, 所以减少单个脉冲能量,可改善表面粗糙度[2] 。影响单个脉冲能量的因素有脉冲宽度、功放管个数、功放管峰值电流, 所以减小脉冲宽度、减小峰值电流, 可改善加工表面粗糙度, 然而, 减小脉冲宽度,生产效率大幅度下降, 不可用; 减小功放管峰值电流, 生产效率也会下降, 但影响程度比脉冲宽度小, 因此, 减小功放管峰值电流, 适当增大脉冲宽度, 调节合适的脉冲间隔, 这样, 既可提高生产效率, 又可获得较低的加工表面粗糙度。
( 3)进给速度要适当。DK7725e线切割机床的加工进给速度分为0~ 10共10档, 速度从慢到快, 进给速度过低会降低进给效率, 过高会引起短路频繁甚至烧丝。经试验并总结, 当系统的加工电流达到加工电源短路电流的75%~ 80%时, 屏幕显示步进频率S大致恒定(不包括运丝电机换向时间) , 控制面板上电压表指针稳定, 加工进给速度比较恰当[ 3] 。
4 正确选择切割路线
切割路线应有利于保证工件在切割过程中的刚度和避开应力变形影响, 如图2所示, 模块装夹固定其左边, 图2是从五角星凸模右侧, 按箭头所示方向切割, 由于坯料两侧的连接材料很快被割断, 左侧工件刚性很差, 难以抵抗应力而变形, 使得五角星凸模尺寸精度产生较大误差, 若改用图3所示路线进行切割, 则模坯产生变形, 从而保证了五角星凸模的尺寸精度。
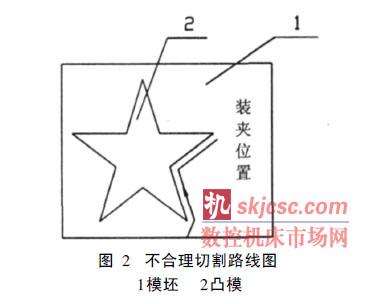
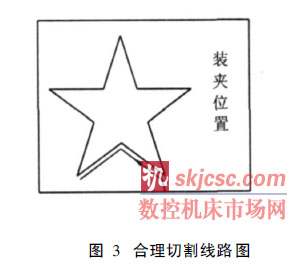
5 结论
通过DK7725e型线切割机床的加工实践, 总结出设定方向间隙补偿量、精确确定钼丝偏移量、正确调整加工参数、正确选择切割路线, 保证工件的加工精度。
如果您有机床行业、企业相关新闻稿件发表,或进行资讯合作,欢迎联系本网编辑部, 邮箱:skjcsc@vip.sina.com