摇臂钻床主轴控制系统设计
2022-6-10 来源: 湖南潇湘技师学院、湖南九嶷职业技术学院 作者:申运
摘要:本文设计采用变频器对摇臂钻床的主轴进行改造,在零件加工过程中可实现一键换速操作,节约了操作时间提高了加工效率。通过对水泵厂摇臂钻床设备进行改造,获得良好的使用效果,有很强的实用价值。
关键词:变频器;控制系统设计;可调电位器
湖南永盛泵业有限公司购买了沈阳中谊 Z3040 型摇臂钻床对水泵的泵体及端盖进行钻孔与攻丝加工。使用一段时间后出现主轴变速箱内齿轮出现频繁打齿的现象,且每次更换新的齿轮后工作不到一个月时间就出现损坏的情况。受永盛泵业有限公司委托,由电工技能大师工作室负责对该机床进行改造设计。就主轴频繁打齿问题进行探索并解决了主轴频繁打齿故障。
1、企业对该摇臂钻床主轴变速方式提出的要求
(1)对该钻床改造后仍能满足基本的钻孔、攻丝要求。
(2)解决主轴变速箱频繁打齿的问题。
(3)解决加工过程中的快速换挡问题,方便转速调整且操作简单。
(4)需要配置有主轴速度显示功能。
2、摇臂钻床主轴箱齿轮损坏原因分析
查阅相关资料摇臂钻床主轴箱齿轮损坏的主要原因有:齿轮质量不佳,进行过大负荷钻削,及主轴未停稳就进行换挡操作。了解到操作人员的工资是以计件的方式计算,通过仔细观察操作员操作过程,发现操作员每次在钻孔与攻丝切换时需要进行换挡操作;且机器未停稳就开始操作换挡手柄进行换挡。工人为了提高加工数量在进行攻丝时选择高速攻丝,操作员在丝锥的四分之一处缠绕铜线来限制螺纹的深度。通过观察铜线与工件的距离来停车,当铜丝快接近工件时立刻改变主轴的方向实现退刀。
在排除齿轮质量不佳、与过大负荷钻削等原因后。主轴箱齿轮损坏的原因可以锁定为:机器未停稳就进行换档操作导致齿轮打齿,最关键的是在攻丝操作时对主轴进行频繁快速正反转操作导致主轴箱齿轮冲击过大、齿轮负荷过重导致主轴箱齿轮损坏。
3、Z3050摇臂钻床主轴控制系统设计
3.1 解决频繁打齿的办法
操作工操作主轴换向的速度非常快,尤其是在对盲孔进行攻丝的阶段主轴由正转到反转切换的速度非常快;齿轮箱内部有很明显的齿轮冲击声音。齿轮在换向的时候负荷非常重,按此思路去探索问题的解决办法。
在空车状态我们尝试在换向的时候刻意先让主轴完全停止下来,再改变主轴的方向。发现主轴齿轮箱内部的异响变弱。解决问题的重点就是在换向的时候让主轴以制动的方式停机。
变频器既能实现主轴电机的无极调速,也能实现有“档位”的变速。设置变频器加、减速时间可实现电机平稳地加减速与停车,从而可减小电机在快速换向时对主轴箱的冲击。最终选用变频器来驱动主轴电机,解决主轴频繁打齿的问题。
3.2 根据工艺要求确立主轴控制方法
在与操作者及工厂技术人员沟通后得知:根据工序此台设备在加工零件时需要先钻孔然后在钻好孔的基础上再进行攻丝。在钻孔与攻丝的的过程中需要切换机械档位操作麻烦。希望能够只进行一次装夹,通过更换钻头及丝锥实现钻孔与攻丝。在钻孔与攻丝的切换过程中能实现快速换挡。
控制方法是选定主轴机械档位的某一档位进行加工,采用变频器对电机进行调速实现主轴速度的变化。从而解决在同一道工序中不用机械换挡的方式进行泵体零件钻孔与攻丝加工。
3.3 主轴变频控制系统设计
根据工艺要求,在钻孔与攻丝的过程中需要主轴变速 1 次,那么我们在改进的时候第一时间想到的是高、低速档位控制。高速用于钻孔、低速用于攻丝。并且还预留一电位器供其他零件加工时可以在变速范围内调整任意转速。摇臂钻床主轴变频控制系统电路图如图 1。
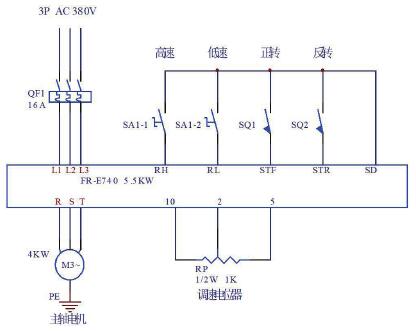
图 1:Z3050 摇臂钻床主轴变频控制系统原理图
3.3.1 钻孔与攻丝速度一键切换
图 1 中,采用三菱 FR-E740 4k W 变频器为主轴电机的调速控制器,通过三档旋钮开关选择主轴高、低转速。当旋钮开关打至左边 SA1-1 接通,变频器高速旋转;当旋钮开关打至右边 SA1-2 接通,变频器控制电机低速旋转。当旋钮开关处在中间位置时则变频器的高、低速度输入信号均断开,变频器的速度受可调电位器控制。变频器频率源的选择与旋钮开关位置对应表见表 1。
表 1:变速旋钮位置与变频器频率源选择
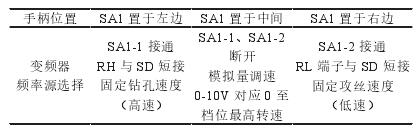
当主轴换向操作手柄打至左边 SQ1 接通变频器端子 SD 与 STF接通变频器控制电机正向转,当主轴方向手柄打至右边 SQ2 变频器端子 SD 与 STR 接通变频器控制电机反向旋转。
3.3.2 主轴无极调速

图 2:转速显示仪表
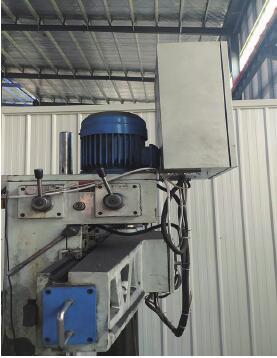
图 3:控制电箱安装位置图
因变频器设置为外部多段速控制模式时,高低速端子信号权限高于模拟量输入。所以当三档旋钮 SA1 打至中间位置,高速与低速端子输入信号均断开。变频器的频率高低受模拟量输入端子电位高低控制,模拟量输入电位越高则电机转速越高反之则越低。此种方式适合工艺过程中需要调整转速的场合,通过调整调速电位器RP1 可控制主轴转速在零至档位最高转速之间进行调整。实现了主轴的无极调速。同时由于变速旋钮 SA1 在中间位置变频器转速信号就默认受模拟量控制,可在加工过程中设置任意转速也为一档位。
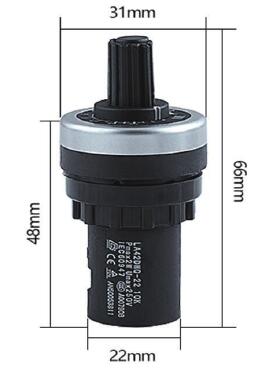
图4 可调点位器
通过变频器多段速控制可对摇臂钻床主轴转速进行有“档位”变速,并实现转速一键切换。模拟量调速可实现转速连续变化,实现了主轴的无极调速增强了主轴加工的适用性。此种方案让一键换速与无极调速并存,让操作变得更加灵活。
4、主轴转速显示功能设计
4.1 主轴转速检测装置
为了在零件加工时选择合适的转速,增加了速度检测与指示装置。考虑便于安装,选择了 NJK-5002C NPN 三线常开型霍尔传感器为速度检测装置,并配置 90 度安装支架。
5.2 调试
(1)将变频器置于外部控制模式先采用可调电位器对主轴进行调速,配合操作员的经验,将主轴调至某转速范围内,并记录高速的频率。在进行低速攻牙加工时调整电位器至某较低转速,记录变频器的运行频率。
确定高低速频率后将高速频率和低速频率的参数全部写入变频器。
(2)变频器高、低速参数调整。在加工零件时多次测试最后确定钻孔速度为高速频率 50Hz1攻丝速度为低速频率 20Hz。根据现场测试将频率整定在此范围可以获得较好的加工效果。
(3)变频器加速时间与减速时间设定。配合操作人员反复测试,确定变频器,加速时间 1S,减速时间 0.5S。
(4)最高频率设定。因该电机的最高工作频率是 50Hz 因此将变频器的参数整定在 50Hz。
(5)电子限流保护参数设定。查看电动机的铭牌发现其额定电流为 7.3A,因此我们将变频器参数整定在 7.5A。
(6)转速测试。对基本参数进行整定及基本功能进行调试后对转速显示功能进行测试。通过改变高、低速档位并与其他档位进行组合对转速进行记录如表 2 所示。
表 2
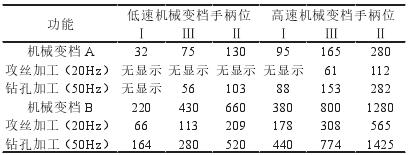
经过测试,转速表有死区当机械变档打至某些低速档位时,机械主轴转速显示为零。在操作员处获得以往经验数据,选择了变速箱高低速手柄打至高速位置,机械变档选择 B 位、Ⅲ档位置。钻孔转速为 774r/min,攻丝速度为
308r/min。
6、使用效果
(1)通过 2 年时间的考验,采用变频器对主轴进行控制后主轴箱内齿轮未见损坏。
(2)使用变频器对主轴进行控制实现了钻孔与攻丝加工在不进行机械变档的方式下进行转速的一键切换,通过一次装夹实现零件的钻孔与攻丝加工,提升了加工效率。使设备的操作变得简单。
(3)因机械档位改变后主轴转速调速范围发生变化,通过加装速度显示仪表可实时地显示摇臂钻床主轴的转速,方便用户选择合适的转速进行零件加工。
(4)改进后机床操作人员需要一段时间适应机床的性能,同时加工的工艺过程需要再次监测。
(5)缺点是:主轴转速显示检测有死区:在主轴实际转速低于 30r/min 时主轴速度显示器显示数值为零。加工过程中当主轴向下移动后磁铁超出传感器检测范围主轴转速显示为零,主轴转速表无法显示实际钻削转速。在钻孔与攻丝加工时加工的深度还未能实
现孔深度自动控制,这也是后续研究设计的方向。
通过长时间的测试验证设计方案可靠有效,改进后的钻床工作稳定性高、操作便捷、故障率低,提升了加工效率。根据工艺要求设计多种速度组合选择,可在相关行业与领域进行推广。
投稿箱:
如果您有机床行业、企业相关新闻稿件发表,或进行资讯合作,欢迎联系本网编辑部, 邮箱:skjcsc@vip.sina.com
如果您有机床行业、企业相关新闻稿件发表,或进行资讯合作,欢迎联系本网编辑部, 邮箱:skjcsc@vip.sina.com