典型车钩体数控加工工艺研究
2022-4-2 来源: 常州中车铁马科技实业有限公司 作者:袁礼彬
摘要:针对动车组车钩体加工过程中的工艺难点,从数控加工程序编制、专用成形刀具设计、深孔钻技术应用等方面,提出了三个关键的工艺举措,为提升实物质量和制造效率提供了完善的技术保证。
关键词:数控程序 形成刀具 深孔钻
引言
钩缓装置是动车组车辆中最基本的部件之一,其安装于动车组车辆车体的两端处,起到连接车辆、缓冲车辆的纵向力、提高列车舒适性的作用[1]。从制造工艺实践角度来看,钩体(如图 1)加工的核心问题是如何确保钩体凸锥、凹腔、连挂面、连挂组成钩舌及主轴安装部位、主风管组成安装部位、电器连接器安装部位、气动解钩组成安装部位及钩尾连接卡环处的尺寸精度、位置精度,以便使动车组可以长期稳定地完成连挂、通风制动、信号传递及解钩等功能。
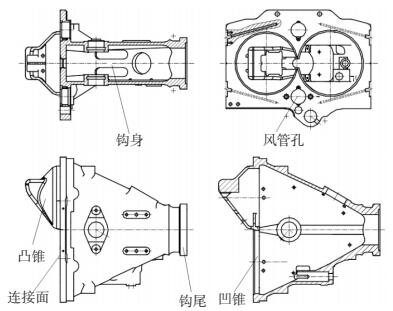
图 1 典型车钩体简图
本文作者在总结实践的基础上,对钩体数控加工三个关键瓶颈工艺进行了探索,来实现钩体加工过程的优化。
1、钩舌盘圆柱销安装孔加工专用反刮刀及数控程序
为满足卧加适应钩体钩舌盘圆柱销孔两内侧面(如图 2)的加工要求,设计并制作了专用反刮刀具[2]。反刮刀具体结构设计如图 3 所示,该反刮刀主要由刀本体、刮刀片、锁紧螺钉组成。其主要特性是刀本体的尾侧是侧压直柄,刀本体中段为联接轴,在联接杆的头部设置与其垂直的刀片座,刀柄、联接轴、刀片座构成一体化联接,反刮刀片由锁紧螺钉装配于刀片座。反刮刀片选择住友公司制造的特制菱形刀片,此刀片具备优良的抗震效果,能连续承受切削过程中的抗崩性。联接轴由不同轴圆形体组建,其外形与椭圆相似。该专用刀具前部直径尺寸为 48 mm,联接轴直径为 45 mm,两部分径向尺寸都不大于所需通过的钩舌盘圆柱销孔直径 Φ50 mm,从结构设计上保证了当该反刮刀具对钩舌盘圆柱孔两内侧面切削时,刀具径向尺寸大于所要切削部位的长度,而该反刮刀在进刀或退刀时避免与内孔表面干涉,同时最大限度地提升刀轴的刚性。
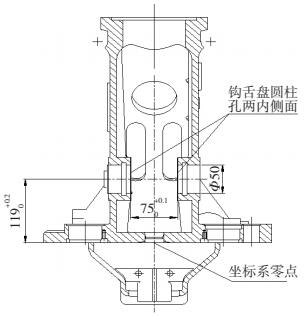
图 2 钩舌盘圆柱销安装孔简图
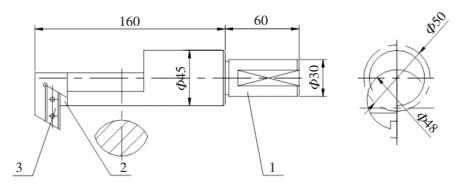
1—刀本体;2—联接轴;3—反刮刀片;4—刀片座;5—锁紧螺钉
图 3 反刮刀具结构简图(单位:mm)
加工时,首先按制造规程要求钻出通孔 Φ50mm,卧加按数控程序自动更换反刮刀具,机床主轴定向,反刮刀中心按照对应于 Φ50 mm 轴线坐标(-119,0)定位(如下页图 4-1),依事前准备的加工程序,在确保反刮刀各部位与通孔不发生干涉的条件下,以G00 设定速度通过 Φ50mm孔(见下页图 4-2),同时使反刮刀刀头在同一水平方向偏移 25 mm,使反刮刀轴线与圆柱销孔中心重合(如图 4-3),反刮刀在按程序设定的加工条件以反方向工进的方式对内侧面反刮切削(如图 4-4)。反刮动作完成后,按与前面相反的方向路径退出,到此,单侧孔的内侧面的切削循环动作完成。另一侧圆柱销通孔内侧面的切削过程与此完全相同。
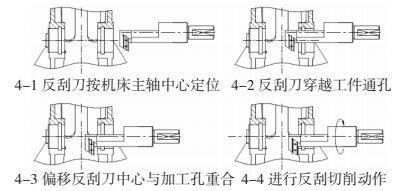
图 4 专用反刮刀加工圆柱销安装孔
制定切削程序时,以钩体图上联接面与钩体中心轴线的交汇处为零点设定工作坐标系,使用绝对值方式设定程序,则圆柱孔两内侧面反刮程序如下:G91G30Y0Z0(回机床参考点,同时做好换刀准备);
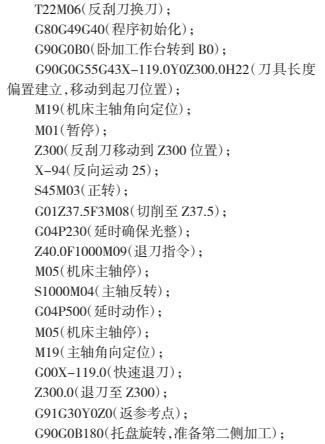
反刮刀的成功设计,较好地攻克了数控机床通用刀具难以解决的反刮难题,实现了在卧加上车钩体通孔内侧面反刮切削数控加工。实际表明,这种反刮刀较好地适应内端面加工,相比于数控机床常规的反刮工艺,明显地提升了制造质量和切削效率,有着较强的可靠性和使用性。
2、钩体钩尾内凹槽成形面铣削加工
钩体钩尾的作用是用于连接牵引杆或压溃管,是车钩模块化结构设计的重要特征。鉴于钩尾外表面内凹槽的结构特征(如图 5),传统的加工方法是采用立式数控车床车削加工,但考虑到公司缺少相应的加工设备,采用发外加工手段,一则加长工艺流程,二则影响影响生产效率。经过对比分析,考虑在卧式加工中心上采用成形刀具进行加工。
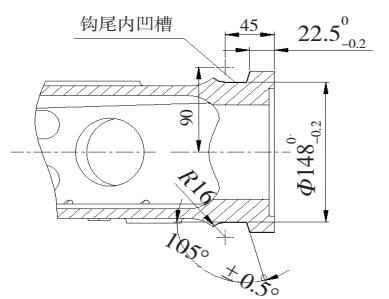
图 5 钩体钩尾内凹槽外形(单位:mm)
针对钩尾内凹槽的结构特征,技术人员设计了相应的专用焊接式成形铣刀,一方面考虑凹槽尺寸较大,粗加工采用一种成形铣刀,会增加切削阻力,引起刀具振动,减少铣刀使用寿命,因此把凹槽的粗加工分成两个部位,并设计二种形状的成形铣刀(如图 6 和图 7)。凹槽的精铣则采用一把整体形成铣刀(如图 8)粗铣后留有合适的加工余量,一次成形铣削,加工效率,表面质量高。
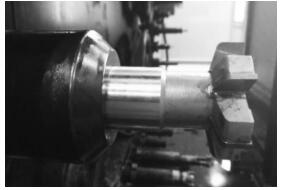
图 6 加工凹槽右段粗铣刀
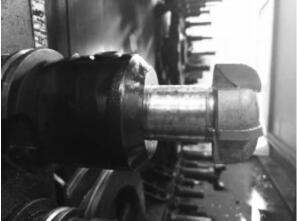
图 7 加工凹槽左端粗铣刀
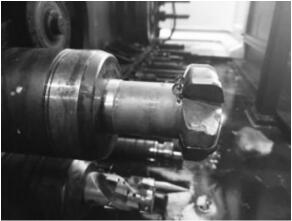
图 8 加工凹槽精铣刀
采用成形铣刀进行凹槽机加工,有两个优点,即实用性强,和钩体连接面在一次安装中加工,无需再设计专用立车夹具,在卧式加工中心上采用铣削加工,简化夹具,加工成本低;能确保钩体的切削精度和表面粗糙度,使用该切削方法,在铣削加工过程中切削量在刀具中部处最大,刀具两端处最小,这种切削量分布特性使得切削力主要汇集在刀具切削刃中间部位,刀具所承受切削扭矩会相对减弱,因此铣削过程会相对平稳。整个铣切过程最后采用整硬刀具,也有效地减少因零件二次粗切削部位之间对接误差,提升零件切削精度和表面粗糙度。
3、钩体加热带深孔加工
钩体加热带孔孔径 Φ6.5 mm,孔深 173 mm,长径比为 26,属于典型的深孔特征(如图 9),必须研究如何解决并满足图样设计的质量要求和提升制造效率。按照传统的工艺方法一般选择深孔钻机床进行加工,考虑到公司内部缺少深孔机床,因此考虑探索在卧式加工中心进行深孔加工[3]。这就要求技术人员研究如何从刀具着手解决该深孔加工技术难题。经过调研对比,多次验证,选择德国钴领公司生产的枪钻(如图 10)。
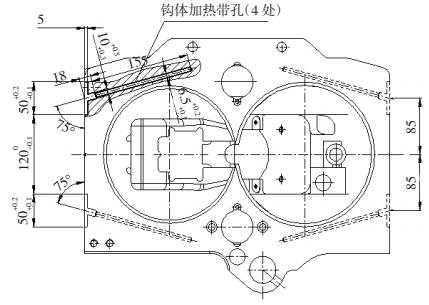
图 9 钩体前端面深孔尺寸分布
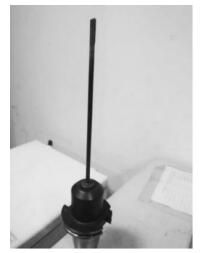
图 10 枪钻实物
本公司卧加的是日本森精机公司制造,型号为FH8000,因深孔加工的考虑,特地增大中心出水水泵,以保证加工压力,借助于卧式加工中心的回转工作台的分度功能,一次装夹,能加工 4 个方向的深孔。具体加工过程如下:
1)深孔引导孔的加工:钻头选择顶角 140°的精密钻头,以保证引导孔顶角比枪钻顶角大。引导孔加工深度设定为 20 mm,其钻头直径比枪钻大0.02~0.05 mm。
2) 枪钻切削参数的选择:枪钻首先以转速为120 r/min,进给速度为 220 mm/min,以低转速快进给地进入引导孔,进入引导孔 2/3 处后,打开切削液并提高切削速度到正常值,经过工艺人员现场多次试加工验证,比较适宜的切削参数是转速为 3 000r/min,进给速度为 230 mm/min,一次性加工至预定深度可不退刀。
3)加工达到图样要求的深度后,关闭冷却液,降低转速并快速退出枪钻至孔口。
在数控加工中心上使用枪钻进行深孔加工,能有效保证钩体深孔的尺寸精度及表面粗糙度;选用合适枪钻可大大提高机床主轴转速及刀具进刀速率;同时枪钻加工过程中刀具排屑更加顺畅,枪钻头部冷却更充分,充分延长了刀具使用寿命,因而使深孔加工取得较高的加工效率。
4、结论
车钩体结构特点决定了其加工难度,在整个加工过程中,我们重点解决了以下几个难点:
1)卧加专用反刮刀具的设计,顺利地解决了数控机床普通刀具无法无法完成的反刮加工难题,实现了在卧加上车钩体通孔内侧面反刮切削数控加工;
2)采用成形铣刀进行凹槽机加工,解决了和钩体连接面在一次安装中加工,无需立车加工,简化了加工流程,提高了生产效率;
3)探索了在卧式加工中心进行深孔加工的工艺,为同类产品提供了有益的借鉴。
投稿箱:
如果您有机床行业、企业相关新闻稿件发表,或进行资讯合作,欢迎联系本网编辑部, 邮箱:skjcsc@vip.sina.com
如果您有机床行业、企业相关新闻稿件发表,或进行资讯合作,欢迎联系本网编辑部, 邮箱:skjcsc@vip.sina.com