TC4 钛合金深孔钻削试验研究与机理分析
2020-6-12 来源: 上海海交通大学 上海航天精密机械 作者:陈杰 胡蒙 郭国强 孙程成 明伟伟 等
摘要 :TC4 钛合金深孔钻削过程中钻削温度高、排屑路径长,加剧刀具磨损,影响深孔加工质量和精度。为制定可用于实际生产的钛合金深孔钻削加工参数,开展 TC4 钛合金深孔枪钻加工试验。试验结果表明,钻削温度受钻削速度影响较大,进给量的影响不显著;孔径和圆度随着钻削速度的增加而增大,同轴度随着切削速度增加而先增大后减小;孔的表面粗糙度随着钻削参数的增加而增大,且大参数下深孔表面质量进一步恶化;各组试验加工硬化层在30μm 左右,且随着钻削速度增加,切屑挤压变形严重。综合分析后制定的干切削条件下 TC4 钛合金深孔枪钻的钻削速度为 20m/min,进给量为 0.08mm/r。
关键词: 枪钻;深孔;钻削机理;加工质量;TC4 钛合金
钛合金比强度高、比刚度高、耐腐蚀、抗疲劳性能好,能在超低温和超高温、高应力、强腐蚀环境下稳定工作,广泛应用于航空航天领域[1]。在航空、航天器中的仪器仪表、传感器、舵骨架、航空发动机等部件制造过程中,常要求加工高精度和高质量的复杂深孔结构[2-3]。深孔长径比大,加工时处于封闭或半封闭状态,刀具切削情况无法直接观察,难以准确监控刀具状态;排屑路径长且不易排出,易造成已加工表面划伤及刀具崩刃;切削散热困难,热量累积产生高温;加工工艺系统刚性差,易产生振动[4]。因此与普通孔相比,深孔加工难度大。目前国内外一些学者进行了相关研究。
Zhang 等[5]研究了铸铁深孔加工表面质量、亚表层变形与加工条件之间的关系,以及 BTA 深孔钻削机理,提出钻削参数和钻削机理共同决定表面完整性。Zhang等[6]通过试验和有限元仿真,提出了铬镍铁合金枪钻过程中枪钻钻尖偏移不一致对深孔直线度偏差影响的理论原因。Kuzu 等[7]利用有限元和反传热法建立了微量润滑条件下的蠕墨铸铁深孔钻削热模型,并通过试验验
证了模型的可靠性。
枪钻是一种单刃切削自导向外排屑深孔钻头[8]。深孔加工时高压冷却液通过钻杆 V 形通道液体将热量带走,并利用冷却液压力排屑,且在钻头外径安装有导向条,从而保证刀具的正确导向[9]。枪钻系统有效提高深孔钻削的断屑排屑性能、冷却润滑效果、制孔精度和质量,广泛应用于小直径孔加工[10-11]。由于 TC4 钛合金弹性模量和热导率较低,钻削过程产生大量的热[12],且深孔钻削的封闭环境限制热量散发,导致钻削温度随钻削深度的增加持续增大。过高的温度会加速刀具磨损,降低孔加工精度,产生加工变质层,生成残余应力。因此需要了解 TC4 钛合金枪钻过程中加工参数对钻削温度的影响规律和加工机理,为工艺参数制定提供可靠依据。
因此,为制定满足精度和质量要求的 TC4 钛合金深孔加工工艺,开展了 TC4 钛合金深孔枪钻试验,研究钛合金深孔钻削成屑机理,分析钻削速度和进给量对钻削温度、深孔尺寸精度和表面质量的影响规律,综合分析之后给出一组应用于实际生产过程的加工参数。
1、枪钻深孔钻削试验
1.1 工件材料与刀具
试验采用锻 TC4 钛合金,工件尺寸为500mm×200mm×30mm,材 料 常 温 下 的 抗 拉 强 度为 1000MPa,400℃下的抗拉强度为 550MPa,硬度为360HV,弹性模量为 120GPa。图 1 所示为 TC4 钛合金的金相组织和元素成分。其中白色的为密排六方结构的 α 相,黑色的为体心立方结构的 β 相。
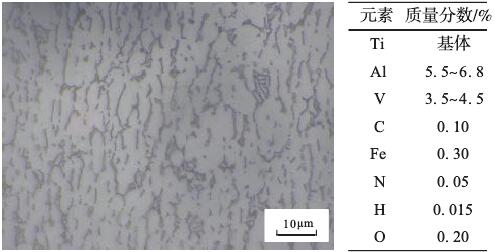
图1 TC4钛合金的金相组织和元素成分
使用德国钴领公司的 EB80-5641 型枪钻。枪钻的刀尖材料为硬质合金,涂层为 CVD-TiCN,刀杆材料为高速钢,刀杆和刀尖之间采用焊接连接。枪钻直径为7mm,钻尖长度为 48mm,钻尖加刀杆长度为 370mm,最深可加工长径比为 40 的深孔。钻尖几何参数如表 1 所示。为了减小深孔钻削时的轴向跳动,提高加工系统的刚度,在加工深孔之前先加工引导孔。使用山特维克可乐满公司的 R846-0700-30-A1A 1220 型硬质合金麻花钻加工引导孔,涂层为 PVD-(Ti, Al)N,直径为 7mm,顶尖角为 140°。
1.2 试验设备
试验在 HAAS 公司的 EC-1600 卧式加工中心上进行。该机床工作台范围为 1626mm×1270mm×813mm;最大转速为 6000r/min;定位精度为 0.01mm。深孔加工过程中温度对刀具的影响至关重要。
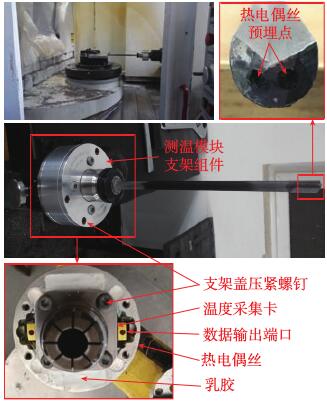
图2 枪钻试验装置及在线测温系统
表1 钻尖几何参数

本次试验采用枪钻内冷孔埋热电偶丝的方式在线测量深孔钻削过程中的温度。在线测温系统如图 2 所示,包括测温模块支架组件和温度监测系统。测温模块支架组件设置于钻削刀柄上,温度监测系统 ( 包含温度采集卡 ) 安装在该测温模块支架组件之中。热电偶丝线连接到测温模块支架组件中的采集系统,温度采集卡对温度进行实时监测,试验结束后,打开支架组件,通过数据线将采集系统中的数据传输到计算机中完成数据的输出与可视化。深孔钻削过程中共有两个热电偶丝同时采集温度信号,保证结果的准确性和可重复性。测温模块支架组件的结构 ( 包括温度采集卡、支架盖压紧螺钉等 ) 呈对称分布,且整体采用高强度铝合金材料制作,以尽可能减小偏心质量。在线测量系统搭建完成后,进行动平衡测试,根据试验结果通过增减某一位置的乳胶来平衡微小的偏心,以保证钻头高速旋转时的动平衡。
1.3 试验方案
在加工深孔之前先加工引导孔,引导孔直径为7mm,钻削深度为 10mm,转速为 1800r/min,进给量为0.08mm/r。
表2 枪钻试验参数
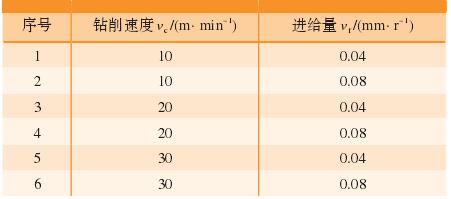
枪钻深孔钻削试验采用全因素试验,钻削参数如表 2 所示。钻削深度为 94mm,为 12 倍径。由于枪钻内冷孔预埋热电偶丝,无法进行内冷,因此采用压力为20bar 的外冷。试验过程中,对枪钻钻尖的钻削温度进行实时测量。试验结束后,采用航天精密机械研究所的C10TA0101DH/TP 型三坐标仪检测孔的加工精度。之后将深孔剖开,在距孔口 30mm、60mm 和 90mm 3 处进行制样,对孔的表面加工质量进行分析。并对已加工表面和切屑进行金相分析和扫描电镜分析。
2 、试验结果分析
2.1 枪钻深孔钻削温度
如图 3 所示,在各组参数下,钻尖温度随着钻孔深度的增加都逐渐上升。随着钻削速度增加,钻尖温度显著上升。钻削速度的提高导致材料的去除率提高,而钻削速度的提高又使钻削力减少,钻削过程中产生的能量大量转移到钻削热上,从而使钻尖温度显著上升。钛合金加工过程中,刀具温度过高会降低刀具的强度,加快刀具的磨损,特别是在深孔加工中,过高的温度很容易导致刀具的失效。为保证硬质合金刀具的耐用度,应当将钻削速度控制在 20m/min 以下。同时,随着进给量的增加,钻尖温度略有上升,但不显著。因此,在实际钻削过程中,可以采取低钻削速度,高进给量的方式提高钻削效率。
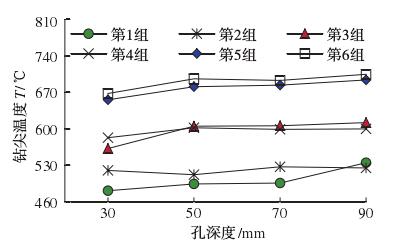
图3 钻尖温度变化图
2.2 深孔加工精度
深孔直径是工艺过程最需要控制的指标,影响到轴孔之间的配合。使用三坐标测量仪分别测量距孔口30mm、50mm、70mm 和 90mm 位置处的直径。如图 4所示,所有孔径都偏大,这是由于深孔加工刚性较弱,枪钻径向跳动引起的。在同一个孔内,深孔直径呈现出先增大后减小的趋势,深孔加工过程中的整体刚性随着钻削深度加深而逐渐增大,因此孔径有一定的减少,但区别不大。从图 4 中数据可以看出,随着钻削速度的增大,孔径有明显的增大的趋势,这与加工温度有关,温度的升高导致钻尖强度降低,跳动增大。而进给量的变化对孔径的影响不大。图 4 还给出了各组参数下的深孔圆度变化规律。孔的圆度随孔深度的增加而增加。随着钻削速度的增加,孔的圆度相应增加,进给量对圆度影响不大,但在 20m/min 的钻削速度下,0.08mm/r 的进给比 0.04mm/r 产生的圆度更大。
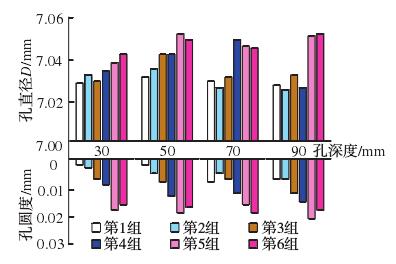
图4 深孔直径和圆度变化规律图
图 5 为各组参数下深孔同轴度 ( 以引导孔为基准 )的变化规律。各组试验的同轴度均处于 0.01~0.02mm之间。加工参数对同轴度的影响并不明显,但参数增大,同轴度还是有一定程度的升高。第 3 组试验的同轴度结果最为理想。因此,从加工精度分析,钻削速度为20m/min 下的试验结果较为理想。
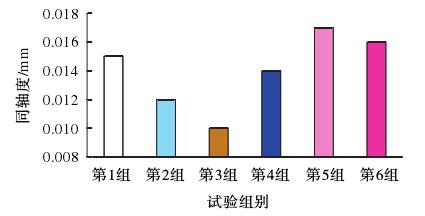
图5 深孔同轴度变化规律图
2.3 深孔加工表面质量
图 6 所示为各组试验的粗糙度变化规律图。前 3组试验粗糙度都比较小,处于 0.4~0.5μm 之间。后 3 组试验由于加工参数的增大,粗糙度明显增加,这与加工过程中刀具的状态有着密切的联系。从图 3 中可以看出,后 3 组数据刀尖温度较高,较高的温度影响刀具的韧性,加剧刀具的磨损,因此加工后的粗糙度越来越大。同一个孔内,粗糙度也越来越大,这是由于枪钻深孔加工时排屑不畅,切屑没有及时排出,会对加工表面有划伤和破坏,从而导致粗糙度的增大。
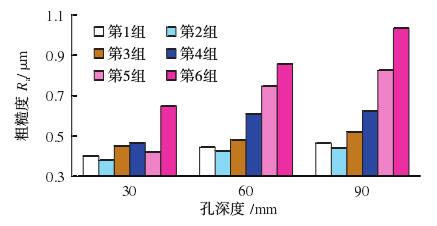
图6 深孔粗糙度变化规律
图 7 是第 2 组试验在孔深 30mm 和 90mm 处的扫描电镜(放大 200 倍)和能谱分析图。孔深 30mm 处,加工表面较为平整,无明显的缺陷。孔深 90mm 处,加工表面存在一些粘结物和切屑的划痕。对黏结物 A 点进行能谱分析,检测出 Ti、Al、V 元素和少量的 O 元素。从能谱分析可以看出切削过程中有少量的钛合金黏结在已加工表面,并有一定程度的氧化,这说明在加工到90mm 处时,刀尖的温度已经非常高,达到钛合金氧化的条件。加工表面几处切屑的划痕也说明,当加工深度较大时,枪钻的排屑不够流畅,未能及时排出的切屑对已加工表面形成了一定的划伤。可见,随着深孔加工深度的增加,切削温度升高,加工难度增加,加工表面质量也逐渐恶化。
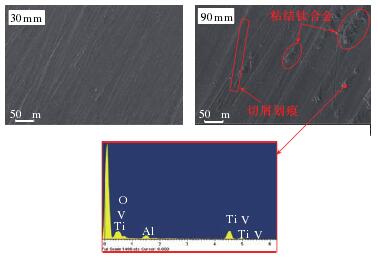
图7 第2组试验已加工表面形貌及能谱分析
2.4 深孔加工表面硬化
图 8 所示为第 1 组和第 6 组试验在孔深 90mm 处的金相图。两组加工表面的晶粒都发生沿钻削进给方向的扭曲延伸,造成加工硬化。表明钛合金深孔钻削表面塑性变形非常明显。第 6 组的孔加工表面还有 1 层厚度为 5μm 左右的白色相变层。说明该组钻削参数下的钻削温度达到了钛合金的相变温度,α 相已经转变为 β 相。
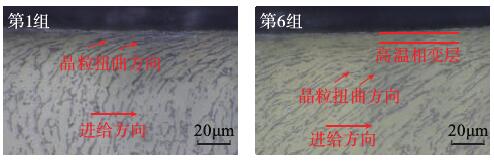
图8 孔深90mm处金相组织
在孔深 90mm 处,距离已加工表面 5μm、15μm、25μm、35μm、50μm、70μm 处检测硬度。图 9 为各组试验距离已加工表面不同距离的硬度变化曲线。其中未加工工件硬度为 360HV。可以看出每组试验条件下的深孔表面都有不同程度的加工硬化。随着钻削速度的提高,加工硬化更明显。由于第 5 组和第 6 组的试验参数大,钻削温度高,深孔已加工表面的晶粒扭曲延伸最显著,所以加工硬化最严重。从图 8 第 6 组孔深90mm 处的金相组织可以看出,第 6 组试验参数下的深孔已加工表面发生相变,产生的 β 相的硬度比 α 相小,所以在距离加工表面 5μm 处,第 6 组试验参数下的表面硬度反而略低。曲线图表明,各组试验在孔深 90mm处的表面硬化层厚度为 30μm 左右,超过 30μm 后硬度趋于工件材料原本的硬度值。
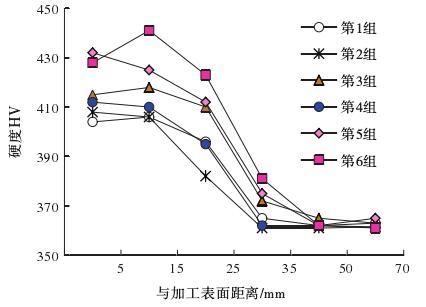
图9 各组试验加工硬化曲线
2.5 深孔加工切屑形态
图 10 为进给量 0.04mm/r 时不同钻削速度下的切屑形态。随着钻削速度增加,切屑由长螺旋卷曲状变化为短带状,且切屑中挤压部分越来越多,材料的去除由剪切转换为挤压,并且在 30m/min 下,切屑由崩碎状排出。在钻削速度较低时,容易形成螺旋卷曲状切屑,屑系数大,随着钻削速度提高,切屑转变为短带状和锥状切屑,当速度进一步提高时,切屑断裂容易,形成崩碎状切屑,同时也说明在加工过程中刀具冲击频率高,刀尖发生严重的磨损,影响加工过程的稳定性。
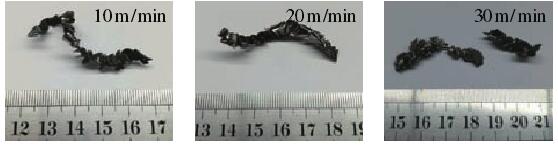
图10 不同切削速度下的切屑形态(进给量为0.04mm/r)
图 11 为第 6 组试验沿厚度方向的切屑金相图。由于热软化作用超过应变硬化,形成绝热剪切带,进而形成锯齿状切屑。图中绝热剪切带从锯齿的齿谷一直延伸到切屑和刀具接触面。在与刀具接触面表层,可以看到晶粒有一定程度的扭曲,图中标出了扭曲方向,即切屑流动方向,说明切削区温度较高,导致晶粒扭曲,发生塑性流动滑移,最终形成了加工硬化。
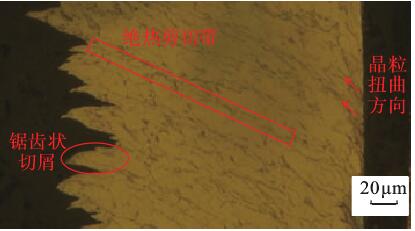
图11 第6组试验切屑金相
图 12 所示为第 6 组试验切屑的微观形貌图。因为高温、高应变率下切屑受到刀具和工件的严重挤压,所以切屑没有卷曲规律,挤压严重,卷曲半径极小。将局部区域放大 200 倍后,能清楚看到在切屑的自由面有沟壑状的锯齿,这也与图 11 相对应。
图12 第6组试验切屑微观形貌图
通过 TC4 深孔钻削机理分析,当钻削速度为 20m/min 时,加工表面硬化在可接受范围,切屑挤压变形程度适中,在排屑过程中对已加工表面损伤小,适合深孔钻削加工。进给量对钻削温度的影响较小,比较不同进给量对应的深孔加工精度,兼顾加工效率,在满足设计要求的前提下,选择进给量为 0.08mm/r。
3 、 结论
本文通过 TC4 钛合金深孔枪钻全因素试验,研究了钛合金深孔钻削成屑机理,分析钻削速度和进给量对钻削温度和深孔质量的影响规律。试验结果表明:
(1)钻削速度对 TC4 钛合金深孔钻削温度影响较大,对进给量的影响不明显。
(2)孔直径随着钻削深度的增加而先增大后减小,随着钻削速度的增加而增大。
(3)孔的表面粗糙度随着钻削速度和进给量的增加而增大,在大钻削参数条件下,深孔已加工表面有钛合金黏结物且有切屑划伤痕迹。
(4)每组试验都存在不同程度的加工硬化,加工硬化层厚度在 30μm 左右。
(5)随着钻削参数的增加,切屑挤压变形趋于严重。
综合分析试验结果,在干切削条件下,钻削速度为20m/min、进给量为 0.08mm/r 的深孔质量最优,满足实际加工需求。
投稿箱:
如果您有机床行业、企业相关新闻稿件发表,或进行资讯合作,欢迎联系本网编辑部, 邮箱:skjcsc@vip.sina.com
如果您有机床行业、企业相关新闻稿件发表,或进行资讯合作,欢迎联系本网编辑部, 邮箱:skjcsc@vip.sina.com