镍基高温合金管板深孔加工试验
2020-6-16 来源: 哈电集团(秦皇岛)重型装备有限公司 作者:王福春,王强,李伟,赵跃
摘要:针对镍基高温合金材料切削变形大、加工硬化严重,材料强度高、切削力大,导热系数小、切削温度高等加工特点,开展 BTA 深孔加工工艺试验,从钻头直径、切削转速、进给速度三方面分析了对孔加工质量的影响,并试验分析了 BTA 钻头的使用寿命。
关键词:镍基高温合金;管板;深孔;试验
压水堆核电站蒸汽发生器管板一般采取复合形式,即高强度的低合金钢母材 + 镍基堆焊层。其目的是依靠低合金钢承受工作介质的压力,使表面堆焊层起到耐受一次侧放射性流体腐蚀的作用,以及管板与换热管焊接隔离过渡作用。目前,此类复合结构的管板深孔加工工艺比较成熟。
某型号蒸汽发生器,因其运行温度高、设计压力大、工作环境恶劣,管板设计通体采用高温下具有较高强度的镍基合金锻件,且管板孔精度要求严格。管板的材料牌号为 SB-564 UNS N08810,机械性能见表 1 所列。管孔呈三角形布置,孔心距 27mm,孔深 320mm。此型管板孔的尺寸精度要严于压水堆蒸汽发生器,而且此种材质的蒸汽发生器管板在工程上属首次应用,给管板的深孔加工工艺带来了挑战。
表 1 SB-564 UNS N08810 锻件机械性能

1、镍基高温合金切削特点
镍基高温合金的常规切削具有如下特点:材料塑性好、切削变形大、加工硬化严重;材料强度高、切削力大;材料导热系数小、切削温度高、刀具磨损快。对于镍基高温合金孔的钻削,因为处于封闭或半封闭的加工状态,使得孔的表面质量、孔的尺寸和位置精度都较差。
而且,镍基高温合金锻件上的深孔多为回转体上的单孔,普遍使用卧式车床通过钻、镗的外排屑方式进行加工。但这些传统方法的加工效率低,多次定位和重复定位产生累积误差使得孔位置精度差,不适合本型蒸汽发生器管板孔加工。
2 、 试验条件
2.1 试件材料
为了更具有代表性,试验用料的材质、孔区厚度与产品管板相同,并且与产品管板具有相同的熔炼炉号、相近的锻造比和相同的热处理工艺。
2.2 加工工艺及刀具
深孔加工工艺有枪钻(外排屑)、BTA 钻(内排屑)和喷吸钻(内排屑)3 种。枪钻和 BTA 钻削工艺在核电管板深孔加工中应用较多,具有一定的经验。综合考虑管板孔的加工精度和加工效率,试验采用 BTA 加工工艺。
2.3 加工设备
试验采用进口卧式数控深孔钻,机床主要参数:X 轴(水平)行程 6500mm,Y 轴( 垂 直)行程4500mm,Z 轴(主轴水平)行程 1100mm;定位精度:X 轴 0.03mm,Y 轴 0.02mm,Z 轴 0.01mm;重复定位精度:0.01mm。
3 、试验项目及结果
3.1 钻头直径对扩孔量的影响
BTA 钻头在加工过程中,随着刀具磨损,孔径会逐渐变小。由于设计的孔径公差范围较小(0.05mm),留给 BTA 钻头直径选择的范围也很小,既要防止首孔直径超差上限,又要兼顾刀具磨损后孔径变小超下限。图 1 为 选 用 Φ19.16/19.27/19.34/19.42mm4 种 规格钻头,加工首孔直径的扩大量。从数据看,对于直径为 Φ19.42mm 的钻头,平均扩孔量在 0.035mm 左右,个别孔达到了 0.04mm;对于直径为 Φ19.16mm 的钻头,最大扩孔量达到了 0.06mm,平均扩孔量为 0.04mm。可看出,随着钻头直径的增大,加工镍基合金的扩孔量呈下降趋势。
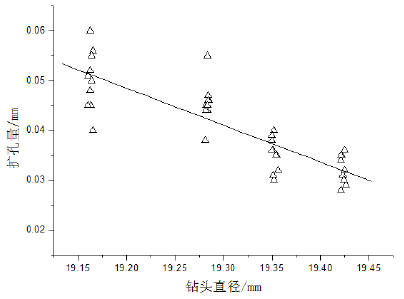
图 1 镍基合金材料扩孔量随钻头直径的变化
3.2 转速对加工精度的影响
使用 Φ19.16mm 的 BTA 钻头,采用相同进给速度、不同转速(800~1400r/min)钻孔时,除个别孔径达到Φ19.22mm 外,其余基本都在 Φ19.18~19.20mm 范围内波动,均可满足设计图纸的要求。对于本目标产品,可以认为在选定的参数范围内,转速对孔径基本无影响。但是随着转速的提高,孔壁的表面粗糙度明显变好。这是因为主轴转速较小时,部分切屑不是由切削刃直接切出,而是靠刀具挤压形成,导致孔壁质量差。
然而随着转速的增加,刀具磨损明显加剧。主要原因是,随着主轴转速的增大,切削过程中摩擦热产生的时间就会很短,热量来不及向切屑和刀具内部传导,从而导致切削温度升高,又因为镍基高温合金本身导热性能差,使得热量在切削位置积聚、刀具磨损加快。
3.3 进给速度对加工质量的影响
进给速度是影响深孔加工效率的主要因素,在上述选定的切削转速下,采用不同的进给速度进行试验。图 2 为采用大于 70mm/min 的大进给时切屑的形状,明显厚而且宽,还不易断屑。这是因为在转速一定的情况下,当进给速度增大时,切削深度会随之增大,切屑从工件上被切除后发生卷曲,由于镍基合金有较好的韧性,虽然切屑经历了冷作硬化,仍不易断屑,极易堵塞排屑通道。
图 3 为采用小于 70mm/min 的小进给时切屑的形状,虽然长但不易断屑,呈窄而薄的褶皱长条形态,能随着切削液顺畅的排出。而且切削平稳,避免了断屑时的冲击,从一定程度上还可提高钻头的耐用度。
3.4 钻头寿命试验
试验采用 4 支相同规格的钻头,按照相同的参数连续加工 40 孔,首孔孔径均为设计值的上限或者超过上限;随着打孔数量的增加,钻头磨损加重,使得孔径逐渐减小。对于尾孔,大部分孔径已经达到设计值的下限,有的已超过下限。
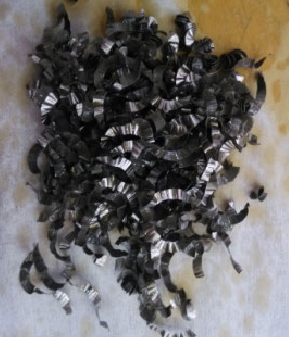
图 2 大进给时切屑形态
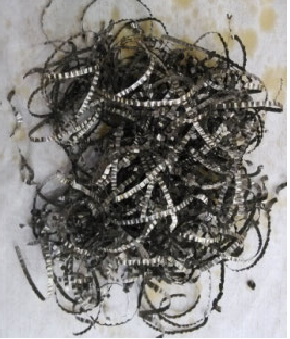
图 3 小进给时切屑形态
在 BTA 钻头的 3 个刀齿中,由于外齿线速度最大,因此外齿距离钻头中心最远处磨损最为严重。在导向条的磨损方面,第一导向条和第二导向条表面涂层颜色变化明显,其中第一导向条的颜色变化要小于第二导向条,并且第一导向条最顶端均不同程度的发生磨损,第二导向条的磨损不明显。
4 、结语
通过 BTA 钻头加工镍基高温合金管板孔的工艺试验,得到如下结论:
(1)BTA 钻头扩孔量随钻头直径的增加而减小,对于 Φ19.16~19.42mm 的钻头,最大扩孔量达到0.06mm,平均扩孔量约为 0.04mm。(2)相同进给速度时,800~1400r/min 的转速,对孔径影响不大,但随着转速提高,孔壁表面粗糙度变好。(3)相同转速时,随着进给速度的增加,切屑变厚而且不易断屑,易发生堵屑现象;采用小进给时,切屑呈窄而薄的褶皱型长条,可顺畅排出。(4)选用加工精度最佳的切削参数,连续加工 40孔时,尾孔已接近或超过孔径公差的下限,BTA 钻头的外刃及第一导向条磨损严重。
投稿箱:
如果您有机床行业、企业相关新闻稿件发表,或进行资讯合作,欢迎联系本网编辑部, 邮箱:skjcsc@vip.sina.com
如果您有机床行业、企业相关新闻稿件发表,或进行资讯合作,欢迎联系本网编辑部, 邮箱:skjcsc@vip.sina.com