立式加工中心支承系统敏感性分析及其结构设计
2018-3-23 来源:大连理工大学 机械工程学院 作者:马雅丽 冯 潇
摘要: 为了高效溯源出机床支承系统的刚性薄弱环节,提出了敏感性分析基础上面向支承系统加工精度的结构设计方法。基于敏感性分析结果,以支承系统加工精度影响明显的立柱为例进行了拓扑优化设计,提出了以静态应变能与静动组合应变能为优化目标响应的壁板与结构单元设计。在此基础上,将该机床的刀尖最大变形量作为优化设计的目标,兼顾支承系统的质量与固有频率,建立了支承系统中涉及立柱外壁板和结构单元的尺度优化设计方法。最后,立式加工中心支承系统在保证质量相对不变的条件下,对比分析了新设计方案与原方案的性能,其结果刚性提高了 5%~11%,验证了支承系统敏感性分析方法及结构设计的有效性。
关键词: 加工中心 ; 支承系统; 敏感性分析; 拓扑优化; 尺度优化
0、引言
机床结构设计方法主要通过传统设计及改进、优化设计法、仿生法以及替换传统材料等达到机床性能的最佳化,而如何将现代科学技术应用于机床的设计开发、分析评估、改进优化是当前研究机床结构设计的关键问题之一。目前机床结构优化设计的研究主要包括以下两个方面: 一方面基于有限元分析的机床结构拓扑优化,在生成的概念模型基础上进行尺寸和形貌的局部设计; 另一方面基于相关的优化算法进行外形和尺寸优化。针对机床敏感性分析来说,黄强介绍了基于多体系统理论与齐次坐标变换方法,提出了从众多机床几何误差源中识别出对加工精度影响较大的敏感性误差。程强在敏感性分析的基础上提出一种识别关键性几何误差源参数的新方法,并采用矩阵微分法计算和分析误差敏感性系数。范晋伟提出了一种基于多体系统运动学理论的机床误差敏感性分析新方法。
尽管机床的敏感性分析方面取得了长足的发展,但缺乏从机床结构设计角度出发,探究支承件位移参数与机床加工精度的关联关系。在此背景下,本文以某立式加工中心 为例,专注于该支承系统敏感性分析及其结构优化设计,从而可有效避免机床结构的盲目改进。
1、支承系统的敏感性建模与分析
机床支承系统静态性能的优劣是保证机床加工精度的基本要求。机床支承系统的敏感性分析旨在辨识各支承件位移参数对刀具和工件成形点相对其理想位置的影响程度,探究支承件位移参数与机床加工精度的关联程度。
1.1 支承系统的敏感性建模
以立式加工中心静态位移参数作为设计变量,研究各相邻支承件之间位移数学关系及其加工精度与支承件位移参数的映射关系。基于多体系统的精度建模理论,构建机床加工精度与各支承件位移间的数学模型,实现机床支承系统的敏感性分析。立式加工中心 支承结构构成及其邻接关系如图 1 所示。
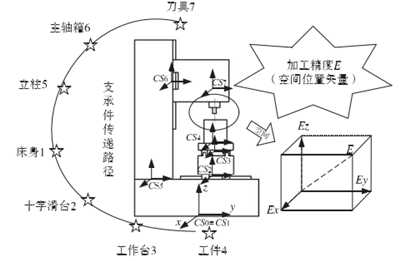
图1 立式加工中心结构构成
立式加工中心的刀具成形点与工件成形点之间的相对位置决定了机床加工精度。加工中心的支承系统建立两类坐标系: 系统坐标系 CS0 和支承件坐标系CSi( i = 1,2…7 ) 。设在初始空载条件下,两类坐标系位姿状态重合,方向与机床坐标系方向一致。切削载荷下,机床支承系统位移是由各支承件位移相互耦合作用而产生,定义位置矢量进行描述。每个支承件坐标系 i 在工作空间具有三项位置位移与转角位移参数为:
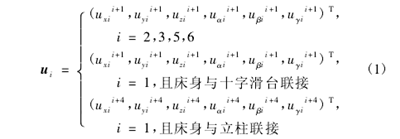
其中,uxi + 1i表示支承件坐标系 i + 1 相对于 i 的 x 向位置位移。因该立式加工中心支承系统由 7 个支承件构成,若以床身为基准,机床支承系统的位置矢量则包含 36项位置和转角位移分量,则其位置矢量为:
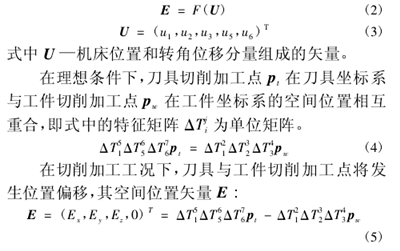
1.2 支承系统的敏感性分析
机床支承系统位移敏感性分析的目的是溯源机床的刚性薄弱环节,以通过薄弱结构的再设计提升机床静态性能及加工精度。其方法或过程是将静态整机加工精度以刀具与工件两端点的矢量差表征,分析各支承件位移参数对加工精度的效应。
根据式(5)中支承系统空间位置矢量,任意位移参数的增量所引起的机床系统空间位置变化量dE可以表达为:
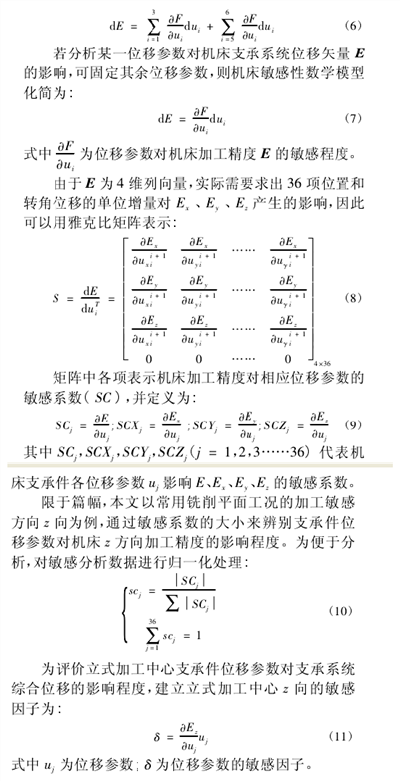
采用有限单元法分析立式加工中心整机静态性能,提取各支承件的相对位移参数代入敏感性模型,完成立式加工中心z向敏感因子分析,其结果如图2所z向敏感因子反映了该立式加工中心支承结构对:向加工精度的影响程度。分析结果表明,立柱:z向位置位移的敏感因子占全部敏感因子的35 %,而床身前部(即与十字滑台结构相连接的部分)和工作台z向位置位移的敏感因子不足2 %。基此,获得支承系统z向薄弱结构,可通过再设计进一步提高相关结构的性能。
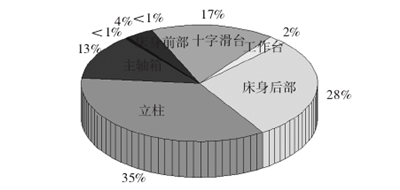
图2 立式加工中心z向敏感因子
2、支承结构的拓扑优化设计
立式加工中心的立柱主要结构由实体壁板、筋板以及镶嵌壁板上的结构单元组成。为获得最优的支承系统性能,采用以静态与动态性能多目标的结构拓扑优化技术进行结构壁板及筋板的主体结构设计;基于立柱的承载类型,选择结构单元类型;利用尺度优化方法获得主要结构参数的尺寸,从而综合提升支承件的性能。
2.1 支承结构的壁板设计
机床立柱需要经历多加工工况载荷条件,因此采用加权来分析与设计工况。根据立柱支承功能和固定型式,设置导轨、轴承座与螺钉固定连接板为非设计区域,其余部分为优化设计区域,获得具有良好综合性能的最佳传力路径,如图3所示。
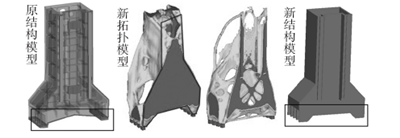
图3 立柱外壁板的基木形状
综合考虑图3动静拓扑优化获得的传力路径,设计立柱壁板的外部形状。新结构与原模型外壁板的承载路径基木一致,呈现“梯形”的结构形式,并基此确定立柱外壁板的形状尺寸。
2. 2 支承结构的结构单儿设计
支承结构的结构单元设计是将结构单元附着在相应的内壁板,防止空心薄壁结构产生颤振和刚性不足的有效措施。通过壁板内壁布置相应的结构单元把导轨引进的集中载荷转移和分散到立柱的整个截而板壁上,实现立柱的整体刚性增强。
结构单元类型的选择首先应参考拓扑优化结构中局部单元的形式,抽象并规整化;其次,根据支承结构的承载类型,以及结构单元在同尺寸下不同单元类型的力学性能,综合考虑最优的单元类型;最后,尽可能地采取对称分布有序布置结构单元,从而简化铸造结构工艺性以及热量传递能力。
立柱新结构方案如图4所示。根据拓扑优化材料分布,选择太阳型结构单元附着于后壁板相应位置处,以满足拓扑结构中力的最佳传递路径;同时参考文献结果D i7,由于菱型与米字型单元结构具有一定的相似性,并且在抗弯、扭等各项性能突出,选择性能略高的菱型单元布置在立柱导轨四周的壁板上,加强立柱悬臂部分的局部刚度,避免薄壁振动。

图4 立柱的结构单元
3、支承结构的尺度优化设计
支承结构的尺度优化设计是基于Workbench与Pro / E实现联合参数化建模与分析,采用多变量多目标优化的设计方法,在支承系统的基础上,通过结构性能最薄弱的立柱尺寸优化,选择合理的外壁板、加强筋和结构单元尺度,以满足支承系统的静动态性能。
3.1 支承结构的尺度优化目标与变量
将该机床的刀尖最大变形量作为立柱尺度优化设计的优化目标,保证在质量不变或者减小的条件下,改善支承系统的静态性能。同时,建立对称性和工艺性约束,设置优化变量中相应尺寸保持等量关系,亦可显著减小计算量。立柱优化以外壁板的前后侧、左右侧、加强筋厚度和菱型单元的宽度与高度五种尺寸作为优化变量,如图5所示。此外,对以系统模态固有频率作为衡量该立式加工中心动态性能的优化目标,分析优化变量参数与固有频率的关系。
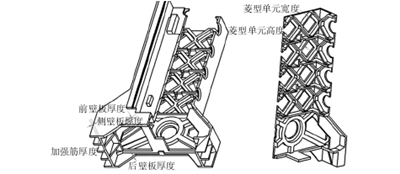
图5 立柱尺寸优化变量
3. 2 支承结构的尺度优化结果分析
根据workbench正交试验,通过响应曲而(线)来拟合设计点,研究优化变量的影响,并能够动态显示优化变量与目标参数之间的关系,确定最佳的优化变量尺寸。限于篇幅,仅列举其中的两种优化变量如图6所示,图中x、y和z分别代表加强筋厚度、菱型单元高度以及刀具的z向最大变形量。
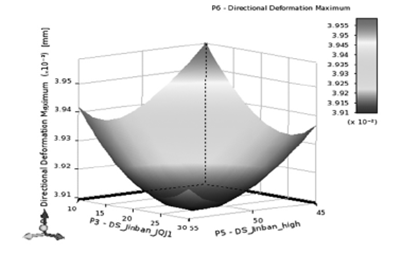
图6 优化变量的响应曲面
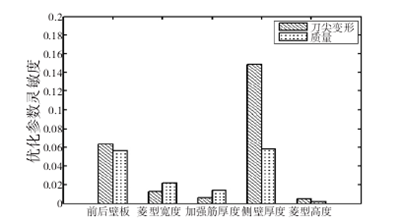
图7 优化变量的灵敏度
为了更好地明确优化变量对于优化目标的影响程度,基于workbench的灵敏度结果,衡量各优化变量的贡献程度。其中,涵盖了对模型质量和刀尖成形点位移的影响,如图7所示。当优化变量的刀尖变形灵敏度大于其质量灵敏度时,则说明该优化变量更能够满足在质量轻的前提卜,对机床刀尖变形量影响更大。图中结果显示,侧壁厚度、前后壁板厚度和菱型单元高度符合刀尖变形灵敏度大于其质量灵敏度。此外,侧壁板厚度、前后壁板厚度、菱型宽度、加强筋厚度以及菱型高度依次对于刀尖变形的影响逐渐减小。 在考虑该支承系统导致的刀尖最大变形的同时,通过Workbench立柱外壁板、加强筋以及菱型单元的正交试验设计,观察立式加工中心支承系统的固有频率,图8为模态优化过程中不同优化变量尺寸组合的固有频率结果。图中的结果表明,优化变量大小的变化对支承系统的固有频率影响较小,其固有频率变化的最大幅度不超过1. 6Hz。
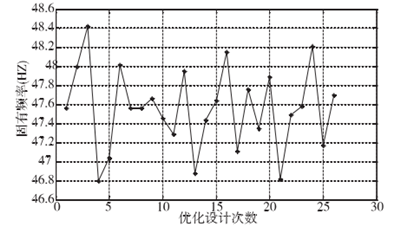
图8 模态优化分析结果
综上,立柱结构最终尺寸仅需要考虑各优化变量对支承系统刚性的影响,即刀尖的位移量。根据优化变量的灵敏度及响应曲而,将前后壁板厚度、侧壁厚度和菱型单元宽度由初始的15 mm设置为18m,28mm和12 mm菱型单元高度由40 mm增至SOmm,加强筋板宽度保持不变。
4、支承系统的性能评价
机床支承系统刚性采用刀具成形点和工件成形点之间的相对位移误差进行评价。由于工作台处变形相
对刀具成形点变形要小很多,因此,结构方案性能评价时,仅考虑刀具的位移量作为支承系统刚性的评价指标。
保证新结构方案与原方案的工况条件、约束位置、网格划分等保持一致情况下进行结构的刚性分析,结果见图9。刀具上最大位移点由53. 8μm减小至48.4μm,而最小位移点则由50.0μm减小至47.4μm其支承系统的质量3. 255t减小为3. 241t,即保证质量相对不变的条件下,立式加工中心支承系统的刚性提高了5%一11%左右。

图9 支承系统的刀具位移
5、结论
本文从机床结构设计角度出发,提出了切削载荷下支承系统的敏感性建模与分析方法,结果显示,立柱z向位置位移是该立式加工中心支承系统的薄弱环节;基于此,建立了立柱的拓扑优化与在支承系统基础上尺度优化设计方法,优化的结果显示,立柱的优化变量对机床系统固有频率的影响很小;最终在保证质量相对不变的条件下支承系统的刚性提高了5%一11%左右。
投稿箱:
如果您有机床行业、企业相关新闻稿件发表,或进行资讯合作,欢迎联系本网编辑部, 邮箱:skjcsc@vip.sina.com
如果您有机床行业、企业相关新闻稿件发表,或进行资讯合作,欢迎联系本网编辑部, 邮箱:skjcsc@vip.sina.com
更多相关信息