枪钻低频轴向振动钻孔的有限元分析
2018-5-15 来源:转载 作者:房嘉赓,苗鸿宾,沈兴全
摘要: 为了使枪钻在加工过程中减小钻削力,运用有限元分析软件 Deform-3D 动态模拟出枪钻钻头低频轴向振动钻削过程。根据枪钻钻头轴向振动钻削的断屑经验公式确定切削参数; 建立了加工过程的有限元模型,并动态模拟了轴向振动钻削加工过程和普通加工过程,结合这两种加工过程中刀具所受的轴向力和扭矩变化情况进行了分析; 最后将两种加工情况进行对比。结果表明: 振动钻削能够显著地降低钻削中产生的轴向力和扭矩,减小钻头的磨损,延长钻头的寿命。
关键词: 振动钻削; 有限元; 轴向力; 扭矩
0 、前言
钻削力是金属钻削加工过程中一个重要的物理现象,它的大小直接影响着钻头的寿命和磨损情况,同时也与钻削热产生的多少密切相关。而深孔钻削加工是金属钻削领域里最重要也是应用最广泛的一项关键技术,由于深孔钻削是在一个封闭的环境内完成的,加工条件受被加工孔径、孔深的限制,加工时所用的刀具刚度小,加工过程中产生的钻削力又很大,尤其是钻削力中的轴向力和扭矩会严重磨损刀具,降低刀具的使用寿命。在保证加工质量的前提下,尽量减小钻削轴向力与扭矩是专家和学者最为关注的焦点,王慧东对高锰钢钻削加工进行仿真与实验研究;张秋丽利用 Matlab 分析了枪钻钻削力的数学模型,分析了钻削参数对钻削力的关系曲线; 闫鹏飞应用有限元软件建立了普通麻花钻的加工仿真模型,研究了切削用量对轴向力与扭矩的影响; 上述的研究成果只分析了切削参数对轴向力和扭矩的影响,除了考虑切削加工参数的影响因素外,在切削方法上的探索也很重要,目前国内外都在重点研究一种更合理、更新颖的孔加工方法,就是振动钻削。振动钻削是日本学者隈部淳一郎首先提出的,随后美国学者 W HAN-SEN 又对低频振动钻削进行了研究,提出了低频振动钻削的概念和方法。迄今为止,受实验设备等客观条件的限制,振动钻削的实验不可能任意改变参数值,所以运用计算机软件进行仿真分析是必不可少的,国内学者李德军,王磊,马利杰等基于有限元法对振动钻削的分析都是针对麻花钻钻头,有关深孔刀具的枪钻钻头振动钻削的有限元分析尚待进一步深入。因此,本文作者建立了枪钻钻头的三维模型,通过有限元分析软件 Deform-3D,采用振动钻削中工艺效果明显、易于实现的轴向振动,以 45 号钢材料为加工对象,对枪钻钻头轴向振动钻削过程进行动态模拟仿真并且分析加工中产生的钻削轴向力及扭矩,再与相同钻削参数情况下的普通钻削形成对比,揭示出振动钻削在深孔加工中的优势。
1、 轴向振动钻削特性分析
振动钻削是振动切削技术的一个分支,是建立在振动理论和切削理论基础上的一种新颖的特殊加工方法,与普通钻削的最根本区别是在钻削的过程中通过振动装置,使钻头和工件之间产生周期性的接触和分离,从而改变钻削规律。按频率上分为低频振动钻削、中频振动钻削和高频振动钻削,按振动方式分为轴向振动、扭转振动和复合振动钻削。
1. 1 建立枪钻钻头轴向振动钻削的运动方程
文中采用的振动频率为 40 Hz,属于低频振动钻削,振动方式为轴向方向的振动。图 1 所示为钻头作轴向振动及进给运动,工件作回转运动的情形,钻削深孔时,在钻杆后端附加一轴向振动装置,此时常用机械式激振方式实现低频振动,可以方便地使钻头实现轴向振动。
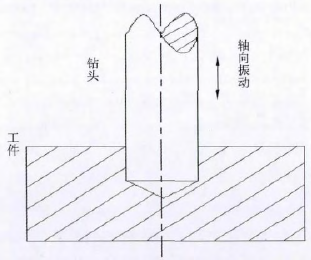
图1 轴向振动钻削示意图
根据图 1 和轴向振动钻削机制建立轴向振动钻削数学模型,则振动钻削时刀刃上任一点在轴线方向的位移表达式 ( 设钻头向下进给方向为正) 为

将式(1)对t进行求一阶导数,得到刀刃上任一点在轴线方向上的速度,即进给速度表达式为:
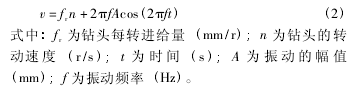
上述两式的第二项即是轴向振动运动方程,由轴向振动系统实现。
1. 2 振动参数与钻削参数的确定
为了形成有利于排屑的短切屑,实现钻削过程中的可靠断屑,根据枪钻的低频振动断屑机制,振动参数和钻削参数应满足下式:
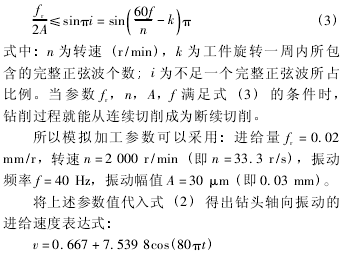
2 、建立枪钻钻头振动钻削的有限元模型
2. 1 枪钻钻头及被加工工件三维模型的建立
因为 Deform-3D 软件的建模功能很简单,不具备复杂几何建模功能,所以枪钻钻头的模型需要通过CAD 软件 PRO / E 进行几何建模,表1列出了工件和枪钻钻头的主要参数,利用这些参数进行刀具和工件的三维建模,将建立好的钻头模型文件类型保存为(. STL 格式,然后导入到 Deform-3D 软件中。
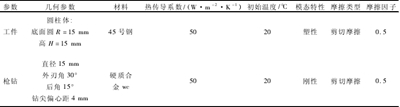
表 1 工件和刀具的特性
2. 2 前处理及边界条件的设置
首先在 Simulation 中设置时间步数为 1 000,每10 步一保存, 选择 With Time Increment 设 定值为0. 001 s。Mesh Windows 网格划分中设置工件网格单元数为 30 000,然后在钻削部分再进行单元局部细化,在 Boundary Conditions 里 设置边界条件,选择Velocity 将工件的 x、y、z 轴方向速度固定,钻头的振动进给速度导入到 Movement 中的 Speed value,形成的进给速度曲线如图2所示,呈余弦曲线状,并在Rotation 定义角速度为 33. 3 r / s。最后在 Inter-Object物体关系设定中定义摩擦类型和摩擦因子。所有设置完成后点击Check,检查没有设置错误或者遗漏,点击Generate 生成 DB 文件,进行保存,最终模型如图3 所示。对于普通钻削过程的模拟设置,只将钻头 Speed value 中的振动进给速度去掉,改为恒定不变的进给速度 0. 667 mm/s,其他设置与前面振动钻削的过程保持一致。退出前处理过程,点击 Run 进行钻削模拟计算。
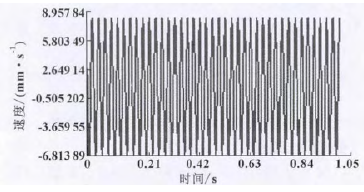
图 2 枪钻轴向振动进给速度曲线
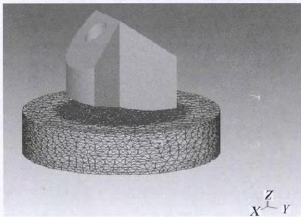
图 3 前处理后的枪钻钻削有限元模型
3 、模拟仿真的结果分析
模拟时间会很长,待模拟完毕后,点击 Post Pro-cessor 中的 Deform-3D Post,即可打开后处理界面,任意时间步的钻削情况都可以很直观地看到,图4就是第 800 步的钻削情况。
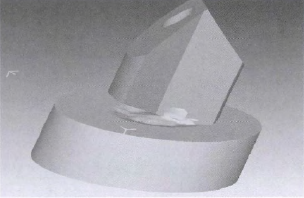
图 4 枪钻轴向振动钻削第 800 步
3. 1 扭矩分析
后处理中选择 Graph 选项,即可得到诸如应力、钻头所受的 X,Y,Z 方向的轴向力以及扭矩等数据的变化曲线,图5和图6分别是枪钻钻头在轴向振动钻削和普通钻削加工中扭矩随时间的变化曲线。从图中可以看出随着钻削深度的增加,两种情况下扭矩值呈上升趋势,但通过观察,当枪钻钻削时间前 0. 9 s时,普通钻削情况的最大扭矩值达到了14 000N·mm左右, 而振动钻削最大扭矩值是 10 000N·mm左右,相同时间内,普通钻削扭矩上升幅度要更大,明显的比较出,在其他加工条件相同的情况下,轴向振动钻削要比普通钻削时钻头所受的扭矩要小。
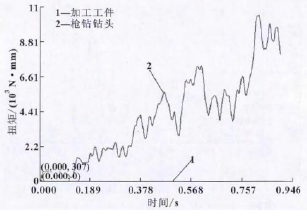
图 5 轴向振动钻削实时扭矩图
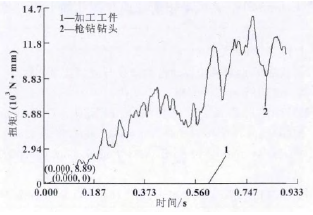
图 6 普通钻削实时扭矩图
3. 2 轴向力分析
图7和图8分别是两种情况下的实时轴向力图,两幅曲线图显示,当钻头与加工工件接触后,轴向力都随之增大,但在枪钻钻削前0. 9 s 时间内,普通钻削产生的轴向力最大达到400 N,平均轴向力在180 ~ 200 N 之间,文中取 190 N,而振动钻削情况下最大轴向力是 250 N,平均轴向力在 90 ~ 110 N 之间,文中取 100 N。振动钻削最大轴向力下降了 37. 5% ,平均轴向力下降了约 47. 4% ,经过观察和计算发现振动钻削情况下的轴向力会大幅度减小。
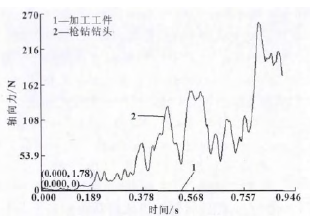
图7 轴向振动钻削实时轴向力图
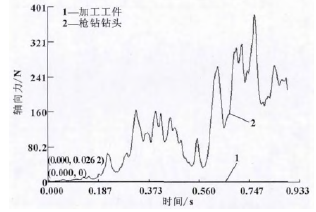
图8 普通钻削实时轴向力图
4 、结束语
基于有限元的离散思想,运用有限元动态模拟软件 Deform-3D,将振动切削理论与深孔加工刀具枪钻相结合,建立了枪钻振动钻削过程和普通钻削过程的有限元模型,通过对枪钻在两种不同加工情况下的钻削模拟仿真,获得了两种情况下产生的轴向力与扭矩,对比得出结论,在深孔加工中,枪钻的低频轴向振动钻削可以有效地降低钻削过程中所产生的钻削扭矩及轴向力,能够更好地减小钻头的磨损,减缓刀具的变形,延长枪钻的使用寿命,所以振动钻削是钻削深孔加工的一种重要且有效的加工方法,并且运用有限元分析的结果,可以为以后研究枪钻轴向振动钻削力的经验公式得到理论基础。
来源:中北大学机械与动力工程学院. 山西省深孔加工工程技术研究中心
投稿箱:
如果您有机床行业、企业相关新闻稿件发表,或进行资讯合作,欢迎联系本网编辑部, 邮箱:skjcsc@vip.sina.com
如果您有机床行业、企业相关新闻稿件发表,或进行资讯合作,欢迎联系本网编辑部, 邮箱:skjcsc@vip.sina.com
更多相关信息