一种新型奥氏体不锈钢经济实用型深孔钻削加工技术
2018-5-7 来源:九江职业技术学院 作者:张东升,牛峥,岳珊
摘要: 奥氏体不锈钢因热稳定性差、塑性大、导热率差,易出现加工硬化、切削力大、断屑困难、易粘刀、刀具易磨损等现象; 深孔加工因排屑散热困难、钻头刚性差、冷却润滑困难等原因较难加工。通过制作加长钻头刀杆,改善钻头装夹和冷却方式,采用三尖七刃群钻,合理选用进刀方式和切削用量,在普通车床上解决了单件小批量奥氏体不锈钢的深孔加工难题,经济适用。
关键词: 奥氏体不锈钢; 深孔钻; 空心轴; 加长钻套
某工厂需加工 1Cr18Ni9Ti 奥氏体不锈钢空心轴数件,零件 图 如 图 1 所 示,该 工 件 较 细 长,长 度 与 外 径 比 为20. 69,长度与孔径比则达 30,属深孔加工。在零件批量较大时一般采用价格昂贵的深孔钻专用设备和深孔钻加工,且配有专用工装夹具,考虑到该厂没有专用设备的实际情况,利用现有设备,改进钻头装夹和冷却方式,采用三尖七刃群钻,合理选用进刀方式和切削用量,较好地解决奥氏体不锈钢的深孔加工难题。
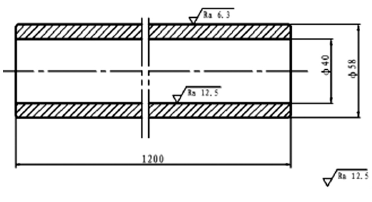
图1 1Cr18Ni9Ti 奥氏体不锈钢空心轴
1 、奥氏体不锈钢加工特点
1Cr18Ni9Ti 奥氏体不锈钢由于塑性好,加工硬化严重、难断屑、易粘刀、导热性差、切削抗力大、加工精度难控制等特点,属难加工材料。其切削特点如下:
(1) 加工硬化严重。由于 1Cr18Ni9Ti 奥氏体不锈钢中奥氏体不够稳定,在切削应力的作用下,部分奥氏体会转变为高硬度的马氏体,加工硬化层的深度超过切削深度的 1/3,硬度比加工前增加 1. 4 ~ 2. 2 倍,加工硬化层的抗拉强度σb 高达 1470 ~ 1960MPa。
(2) 切削抗力非常大。切削过程中因显著的塑性变形,加上高温时材料的粘结性,导致切屑和刀头、切屑和母材粘接在一起,加剧了摩擦,使切削抗力猛增,另有加工硬化影响,使切削抗力很大。
(3) 切削温度高。切削过程中切屑剧烈的塑性变形、工件与刀具间强烈的摩擦,使形变热和摩擦热转变为大量的切削热,使得导热系数低的不锈钢加工过程中产生极高的切削温度。
(4) 切屑难折断。奥氏体不锈钢的塑性大、韧性好,导致切屑难折断,切屑缠绕在刀具和工件上,难以清理,会刮伤已加工表面。
(5) 刀具易磨损。在高温、高压下,奥氏体不锈钢中的合金元素与刀具中其他金属元素的亲和力强,使刀具产生粘结磨损、扩散磨损。另外奥氏体不锈钢中碳化物颗粒硬度很高,会与刀头产生强烈摩擦,加剧刀具磨损。
(6) 加工精度难控制。奥氏体不锈钢的线膨胀系数大,约为碳钢的 1. 5 倍,加工时会造成工件严重的热变形,难以控制加工精度。高温高压下切屑易粘结在刀头形成积屑瘤,使工件表面粗糙度较大。
另外深孔加工因排屑、冷却、润滑困难、钻头刚性差等原因,也属于难加工项目,其特点如下:
(1) 工件加工精度低。刀杆受孔径的限制,细长、刚性差、强度低; 钻孔时易弯曲变形、偏斜; 产生振动、波纹、孔口锥度,造成工件孔中心线直线度、内孔圆度、圆柱度、端面全跳动误差,表面粗糙度低。
(2) 钻头耐用度低。钻头在封闭环境中工作,冷却液难以到达切削区,散热、润滑困难,断屑不易、排屑不畅,降低了钻头的耐用度。
(3) 加工过程难以把握。钻削时切削情况难以直接观察,只能凭经验来判断切削过程是否正常。
2 、奥氏体不锈钢加工方法
综上所述,奥氏体不锈钢深孔加工属难加工项目,大批量生产条件下,一般采用昂贵的深孔钻床、深孔钻头和专用钻孔的装置。本厂因单件小批量生产,为节省加工成本,考虑到工厂的实际条件,拟采用普通车床加工,自制加长钻头,改进冷却方法,选用合理的切削用量来加工内孔,采取的技术方案如下:
2. 1 加工前准备工作
(1) 车床和刀具准备。选用工厂自有的普通卧式车床CA6140 × 1500,准备三爪自定心卡盘、 跟刀架、 中心架、钻夹头和顶尖等附件。准备 45°和 75°YG813 硬质合金偏刀、YG813 硬质合金内孔车刀、内外螺纹车刀、中心钻、φ30mm钻头 ( 磨成三尖七刃的群钻) 、φ40mm 扩孔钻和冷却液。
(2) 改进钻头装夹方式和冷却方式。在 φ30mm 钻头和φ40mm 扩孔钻锥柄位置车出 Tr24 × 3mm 的外螺纹,中心位置钻 φ6mm 的液道孔至螺旋槽处; 在螺旋槽的位置钻切削液出口与螺旋容屑槽相通,钻杆安装在夹套中,夹套安装在车床刀架上。
(3) 刀杆准备。用经过滚压的钢管制成加长钻头的刀杆,如图 3,滚压目的是提高钻杆表面的硬度并降低粗糙度,以免钻孔时拉伤,钻杆内径加工成 φ29. 5mm,略小于钻头直径,刀杆的长度取 650mm,略大于工件总长的一半,并进行表面热处理以提高硬度和耐磨性,一端车出 Tr24 ×3mm 的内螺纹,另一端车出 M28 × 2mm 的内螺纹与切削液管接头联接。
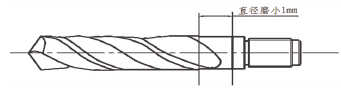
图 2 钻头柄部加工为螺纹
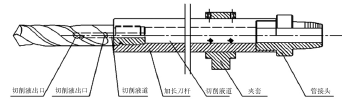
图 3 钻头安装在加长钻杆内
2. 2 加工流程
(1) 车外圆和端面,钻中心孔。将工件毛坯插入车床主轴孔内,用三爪自定心卡盘夹住右端,用 45°外圆偏刀和中心钻以 Vc = 12m/min 左右的切削速度,车端面和钻中心孔。松开卡盘抽出工件,调头夹左端,用顶尖支撑工件右端,安装好跟刀架,在工件左端加工一段研磨跟刀架托爪的外圆,以便快速研磨托爪。将大拖板移至车床尾部,把 75°偏刀刀尖移至托爪前 2 ~ 3mm,以 Vc = 45m/min、f = 0. 3mm/r、ap= 1. 5mm 左右的切削用量车削工件外圆,经多次车削将工件外圆尺寸车至要求。卸下跟刀架,安装好中心架,将工件掉头安装在三爪卡盘和中心架上。用 45°偏刀车端面,使工件总长为 1200mm,并车好余下的外圆,钻中心孔。再用60°锪钻把中心孔扩大,使大径尽可能超过 φ30mm,便于钻孔时定位,避免把孔钻偏。
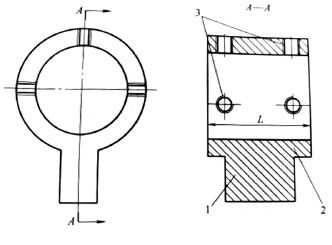
图4 加长钻头夹套
1-夹套 2-内孔 3-螺纹孔
(2) 粗加工内孔。将 φ30mm 的标准钻头安装在车床尾座上,预钻 φ30mm × 120mm 左右深的导向孔。将深孔加长钻头的刀杆装夹在专用夹套内,如图 4 所示,使钻头可在夹套内自由滑动,并伸出 300mm 左右长度,锁紧夹套上的螺栓,将刀杆安装在方刀架上。来回移动床鞍,让加长钻头在预孔内反复移动数次,调整钻杆轴心线位置确保与工件轴心线同轴。为减少加工硬化现象发生,选取 Vc = 12m/min、f= 0. 25mm / r 左右的切削用量进行钻孔。切削液通过管接头直接流入钻头的容屑槽内出液口处,直接冷却钻头。每次进给的深度达到 15mm 左右时,迅速退出钻头排屑并清除碎屑,进行润滑。钻孔时一定要记住大拖板刻度盘起点和终点的读数,下次钻孔要在上次钻孔深度前约 1mm 处开始进给,不要等钻头接触工件后再进给,避免钻尖在工件表面停留,加剧切削表面硬化,造成钻削困难,加快钻头磨损。加工中应经常保持钻头锋利,必要时增加修磨钻头次数。
(3) 扩孔。将 φ40mm 扩孔钻安装在加长钻杆上,以 Vc= 12m / min、f = 0. 3mm / r 左右的切削用量进行扩孔。必须充分利用大拖板刻度盘记数,方法同前。由于扩孔加工余量比钻孔时减小很多,可在每次钻孔 40mm 左右,退出钻头排屑并润滑。
(4) 调头扩孔。在扩孔深度达到工件长度一半后,调头对剩下的另一半孔进行扩孔,至此加工完毕。仔细测量零件尺寸精度和表面粗糙度,直到达到加工要求为止,然后卸下工件。
3 、结论
采用三尖七刃的群钻,改变钻柄的装夹方式、增加冷却液通道,自制加长钻杆,顺利加工出 1Cr18Ni9Ti 奥氏体不锈钢空心轴,保证了加工精度要求,降低了加工成本,节省了费用,对于此类不锈钢深孔的加工有一定的借鉴意义。
投稿箱:
如果您有机床行业、企业相关新闻稿件发表,或进行资讯合作,欢迎联系本网编辑部, 邮箱:skjcsc@vip.sina.com
如果您有机床行业、企业相关新闻稿件发表,或进行资讯合作,欢迎联系本网编辑部, 邮箱:skjcsc@vip.sina.com
更多相关信息