变速器壳体的工艺研究及效率提升
2022-11-2 来源:陕西法士特齿轮有限责任公司 作者:李洛锋
因市场原因,某变速器壳体初始设计产能较低,在汽车市场持续增长的情况下,其设计产能已显不足。为了抢占市场先机,因追加投资周期长,从产品设计、工艺开发、生产制造等方面对生产线进行优化,提升该零件的生产效率。
一. 改进前的情况说明
法士特齿轮有限责任公司的一种壳体设计兼容了变速器壳体、离合器壳体的功能,该零件设计复杂,加工内容多,工序设置较长,导致存在以下问题 :
1)个别工序的加工内容较多,节拍过长,与其他设备不能平衡。
2)生产线存在摇臂钻,影响操作人员的劳动力释放。
3)人员数量与设备数量的配比不合理,影响产线的能力。
二. 原因分析
通过对产品的设计、工艺开发、生产加工等方面的分析,发现原有工艺存在较多问题,具体如下 :
1)不合理设计,增加工艺难度及加工节拍,影响产能。
2)工艺思路较为落后,存在手动操作设备,操作人员的有效时间不能释放,影响其他设备的开动时间,降低整条生产线的设备利用率。
3)刀具的应用及加工参数的设置不够合理。
三. 改进措施的研究与应用
1. 产品设计
针对图样中存在的设计问题,与设计者沟通,对产品图样的设计进行合理化改进,示例如下 :某孔孔径要求 φA(H9),经查该孔无需如此精度,通过设计变更将尺寸改为自由公差,改进后效果见表 1。
表 1 某孔加工工艺改进
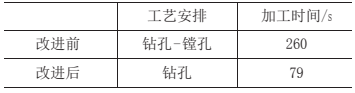
2. 工艺排布合理化
原工艺的工序冗长,部分工序使用摇臂钻,操作者的劳动强度较大。
主要通过以下工作完成工艺精简 :
(1)通过定制刀具实现工序缩减 锪孔工序由摇臂钻加工合并至立式加工中心加工,提升了加工质量,降低了操作者的劳动强度,并实现工艺精简。
(2)通过工艺改进减少工序该壳体需安装一种钢套,通过工艺试验并设计安装夹具,实现工序精简,具体对比见表 2,夹具实物如图 1 所示。
表 2 工序改进前后对比
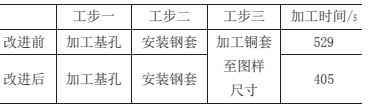
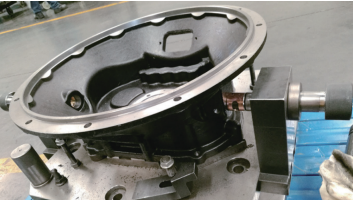
图 1 夹具
(3)角度头的应用 斜面上的螺纹孔由摇臂钻加工(见图2)改为立式加工中心加工(见图3)。
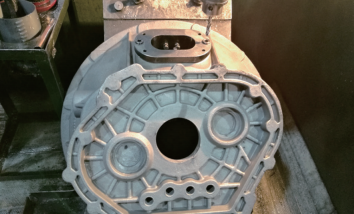
图 2 摇臂钻加工螺纹孔
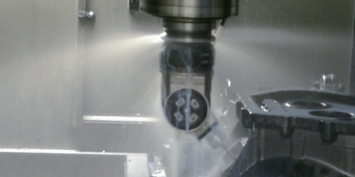
图 3 立式加工中心加工螺纹孔
(4)工艺调整压缩工序 通过设计液压夹具,调整加工内容,将两序加工内容合并为一序,为瓶颈工序省出一台立加,提升了该线产出,具体见表 3。
表 3 工艺调整改进
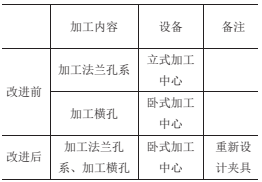
通过以上工艺排布的合理化改进,使该生产线的工序简化,具体见表 4,且为瓶颈工序增加一台设备,大幅提升了整线的加工效率。
表 4 生产线改进前后工序对比
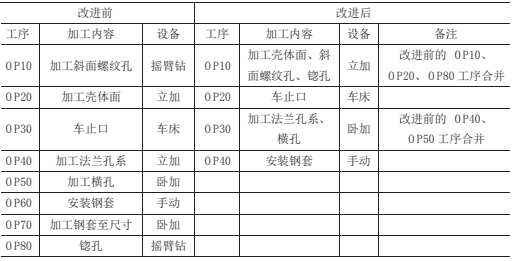
3. 新刀具的应用
1)原工艺某孔使用国产钻头,进给为 250mm/min,使用进口钻头后,进给为 900mm/min,切削效率提升 3 倍多。
2)新概念铣刀的应用。某品牌铣刀改变了传统铣削方式及理念,大幅提升加工效率 ; 较传统刀具减少了刀片的使用数量,并大幅提升了刀片寿命,成本大幅降低。切削参数及加工时间见表 5。
表 5 更换刀具前后效果对比
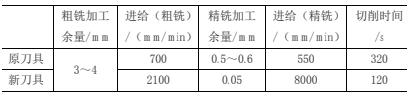
4. 刀具数量优化
在机械加工过程中,每多一个动作,则切削效率会受到影响,为此,需从刀具数量方面进行优化。
1)原工艺对孔口倒角均使用倒角刀加工,使用复合刀具取消倒角刀,加工时间可优化约2min。
2)原图样要求油孔为 φC,将该孔与螺纹孔的底孔统一,则在加工时少使用一把刀具。
5. 程序优化
1)利用现有刀具进行试验,确定其合理的切削参数区间,对现有镗刀、钻头、丝锥等常规刀具进行优化(见图 4)。
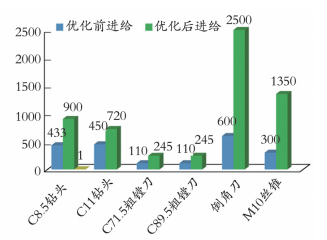
图 4 刀具进给优化前后对比
2)对程序中的刀具行走路径进行优化,并对刀具安全距离由原程序的 15mm 减少为3mm,有效减少刀具的无效运动距离。
3)原程序使用 G83 深孔循环加工某孔,通过更换刀具及调整机床切削液的压力,使用钻孔循环 G81 加工。
四. 改进的效果
1. 效率提升成果
通过以上改进,瓶颈工序的加工节拍(含加工和装夹时间)由原工艺的 20min/ 件缩短至10min/ 件,将该生产线的产能由 1.8 万件 / 年提升至 3.6 万件 / 年,大幅提高了该线的生产能力。各个改进点对效率的贡献比率如图 5 所示。
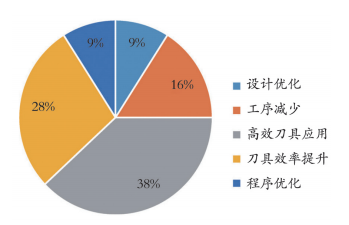
图 5 效率提升成果
2. 成本降低成果
该生产线整体投资为 800 余万元,按照 10年折旧计算,平均每年折旧 80 万元。
(1)设备折旧成本 改进前单件设备折旧 :80 万元/1.8万件=44.4元/件;改进后单件设备折旧:80万元 /3.6 万件 =22.2 元 / 件。单件设备折旧成本节约 :44.4 -22.2 =22.2 元 / 件。
(2)人员成本 改进前单件人工成本 :(8万元/人×6 人)/1.8万件 =33.3(元/件); 改进后单件人工成本:(10万元 /人×6 人)/3.6 万 件=16.7(元/件)。单件人工成本节约 :33.3 -16.7=16.6(元 / 件)。
(3)刀具成本 根据刀具对比试验,所得刀具成本节约 1.63 元 / 件。
单件成本节约22.2+16.6+1.63 =40.43(元/件)。
五. 结语
该变速器壳体生产线的工艺改进,有效地解决了设计产能不足的问题。既为公司节省了一笔可观的投资,又及时抢占了市场高速增长的桥头堡,为公司发展战略夯实了基础。
投稿箱:
如果您有机床行业、企业相关新闻稿件发表,或进行资讯合作,欢迎联系本网编辑部, 邮箱:skjcsc@vip.sina.com
如果您有机床行业、企业相关新闻稿件发表,或进行资讯合作,欢迎联系本网编辑部, 邮箱:skjcsc@vip.sina.com