刀库电气调试中的“找规律法”
摘要:刀库的调试是加工中心电气调试中的一项重要内容,对于调试过程中遇到的具体的问题,尤其是那些随机性的问题,进行详细地记录,认真地观察,透过纷繁的表面现象,找出并总结规律。“找规律法”往往可以缩小排查范围,将问题化难为易,使得问题迎刃而解。
本文列举两个例子,来说明 “找规律法” 在加工中心刀库调试中的应用。一例是 “还刀过程刀套多走问题”,另一例是 “换刀过程中数据的二次刷新问题”。
一、还刀过程刀套多走问题
1.刀库简介
链式刀库如图 1 所示,该刀库采用三相异步电动机配合计数开关进行分度定位,并采用固定式换刀模式(刀具和刀套是一一对应的,刀具号即刀套号),刀库容量为 24。ATC 的各个动作由一系列油缸驱动完成 : 机械手向左 / 向右平移油缸,单元向主轴 / 向刀库油缸,手臂伸出 / 缩回油缸,机械手正 / 反转 180°油缸。
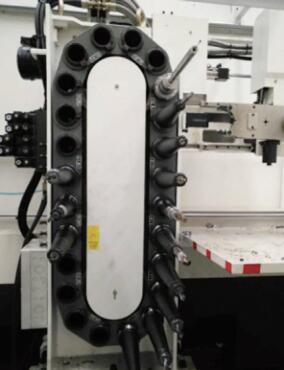
图 1 链式刀库
为了方便描述,将自动刀具交换过程分为三个部分 :
(1)备刀动作 : 刀库分度到 T 代码指定的刀具处,机械手抓完刀备用。
(2)换刀动作 : 该动作过程中,手上刀具和主轴刀具进行交换,刀库门关闭标志着换刀过程结束。
(3)还刀动作 : 该动作过程在刀库侧进行,刀库分度至手上刀号处,将手上刀具还到刀库。
2.问题规律
在 “还刀动作” 中,刀库的初始位置在 2 号刀套处,目标刀套号(即所要还的手上刀具号)为 20。刀库就近找刀套,需要从 2 号刀套处启动逆时针转动至 20 号刀套,见图 2。可是实际动作是 : 刀库逆时针转到 20 号刀套后并没有停止,而是继续转动到 18 号刀套才停止,如图 2所示。即刀库 “多转了” 2 个刀套,导致 “还刀动作” 异常中断,20 号刀具无法正常还到刀库,如图 3 所示。
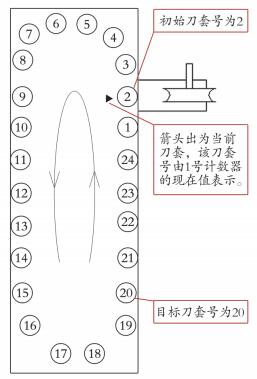
图 2 刀库转动情况
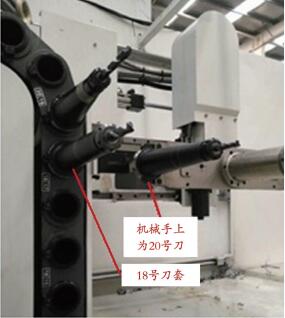
图 3 还刀中断
对问题现象进行总结,可以得出下面5条规律:
(1)刀库分度中,刀库是多转而不是少转了,并且多转的刀套数总是相同的 : 均为 2 个。
(2)分度错误均发生在“还刀动作”过程。“备刀动作” 虽然也有刀库的分度动作,但是并未遇到分度错误。
(3)每次错误,均是以 2 号刀套为起始位置,20 号刀套为目标位置,除此以外的其他刀套并没有发现类似问题。
(4)分度错误时,刀库的转动方向均为逆时针,而没有顺时针。
(5)该刀库分度错误为偶发,故障间隔时长时短,或者数小时,或者数天。
3.问题分析
既然刀库多转且多转 2 个刀套,首先想到 :刀库转动过程中,图 4 中的计数开关的脉冲信号少了两个,或者说 “丢了两个脉冲”。然而由上面 “问题规律” 中的(2)和(3)可知,“备刀动作” 中刀库分度并未见异常,并且除了 20 以外的其它刀套号的分度也未见异常,由此判断 “丢脉冲” 的猜想是站不住脚的,相关的软件和硬件线路便认为是无误的,这也就大大缩小了问题排查的范围。这里,不妨以 “逆时针转动与多转 2个刀套之间的联系” 为切入点进一步分析。
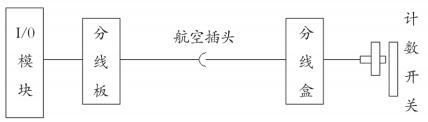
图 4 计数开关
(1)刀库的转动方向与计数器的计数方向刀库的转动方向与计数器(CTR)的计数方向是紧密相联的,相互统一的。对于该刀库——顺时针转动对应着刀套号的增加,因此,把顺时针转动时对应的计数方向处理为加计数 , 即令 UPDOWN=0。逆时针转动对应着刀套号的减小,因此,把逆时针转动时对应的计数方向处理为减计数,即令 UPDOWN=1。刀库顺时针转动时,MGCCWM=0; 刀库逆时针转动时MGCCWM=1。因此,恰好可以用MGCCWM 来表征 UPDOWN,如图 5 和表 1。
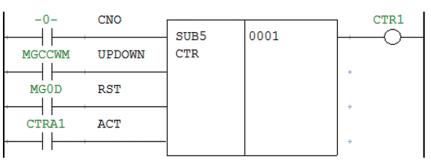
图 5 计数器功能指令
表 1 计数方向 UPDOWN
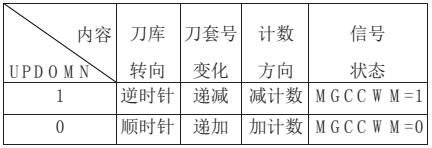
(2)关于 “2 个刀套” 的一个假设在该例中,若刀库分度正常时,计数过程为表2 中的情形Ⅰ : 计数器为减计数,由 1 连续减到19,相应地,刀套由 2 号逆时针连续转动到 20。
基于生活常识,在这里假设,在减计数的过程中,出现了一次加计数。不妨假设计数器从22 经过一次加计数变为 23,然后又恢复为正常的减计数,那么当计数器再次恢复为 22 时,刀套已经逆时针多转过了两个刀套 : 由 23 号刀套转到 21 号刀套。
这样,当整个计数过程结束时,刀库便逆时针转到了 18 号刀套,较之目标刀套号 20,显然多转了两个刀套,如表 2 中的情形Ⅱ所示。这便将“逆时针方向转动与多转2个刀套”联系起来了。
表 2 计数方向 UPDOWN
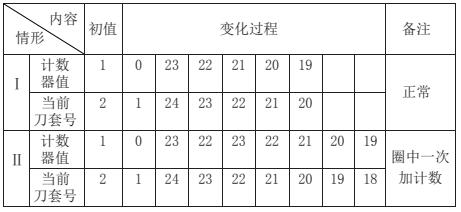
基于上述假设,考虑检查确认 : 在刀库逆时针转动过程中到底是否会存在瞬间的加计数,这就需要进一步确认两个内容 :
①在刀库逆时针转动过程中是否会出现UPDOWN=0 的情形,即 MGCCWM=0 的现象,若有,进一步确认(2)。
②在逆时针转动过程中,MGCCWM=0 时是否有计数脉冲信号 CTRA1。
(3)刀库逆时针转动过程中 MGCCWM=0的确认对问题情况进行模拟并在线诊断信号MGCCWM 的通断变化规律。发现在换刀动作中,当机械手单元向刀库侧摆动时,的确存在MGCCWM 被 “瞬间切断” 的现象,复现度极高,几乎每次换刀动作循环中都有出现。进一步顺藤摸瓜,通过研究梯形图发现 MGCCWM 的一个必要条件MROTEB会被瞬间切断,PLC如图6所示,其中 :
UTOMLS: 机械手单元在刀库侧
SIDRLS: 滑板在右侧
MGCCWM: 刀库逆时针转动 R 地址
MGCCWS: 刀库逆时针转动 Y 输出
机械手单元已经移动至刀库侧,而滑板还没有移动到右侧,导致 MROTEB 被切断,进而刀库的逆时针转动 MGCCWM 被切断,正如假设,确实出现了瞬间 MGCCWM=0 的现象。
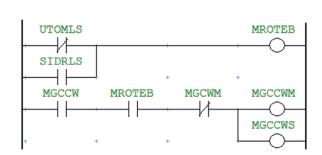
图 6 MROTEB 和 MGCCWMC
(4)在逆时针转动过程中,M G C C W M= 0 时计数脉冲信号 CTRA1 的确认这里所说的MGCCWM=0,指的就是刀库逆时针转动过程中的 Δt 时间段,如图 7 所示。
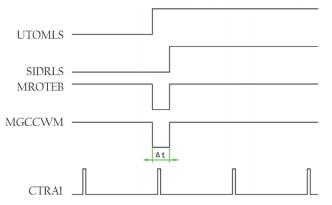
图 7 分度故障
①分度错误
在 Δt 期间,如果刀库转动的计数开关恰好被触发了一次,即产生了一个计数脉冲信号CTRA1,这种情况下,图 5 中的 ACT 信号便产生了一个上升沿,那么计数器进行一次加计数。而当滑板右移到位后,MROTEB 又恢复为 1,MGCCWM 也恢复为 1,此时,计数器 CTR1 便恢复为正常的减计数,但最终由于一次加计数而在逆时针方向上多移动了两个刀套。这里,通过 PLC 对 CTRA1 进行实时地跟踪并自锁,验证了在 Δt 期间是有计数脉冲信号CTRA1 的,如图 8 所示。还可以通过数控系统的跟踪画面对相关信号进行更加详细的监视,这里不再赘述。
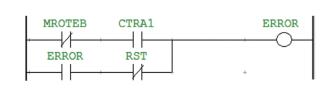
图 8 CTRA1 的自锁
再试想,在 Δt 期间,如果经历了两次计数器触发,那么刀库多转的刀套数就不是 2,而是4 个了……
②分度 “正常”
虽然在 Δt 时间段内,计数器 CTR1 为加计数类型,但是在该时间段内,如果刀库的计数开关并没有被触发,即没有产生计数脉冲信号CTRA1,这种情况下,图 5 中的 ACT 信号也就没有上升沿,那么计数器不会进行加计数。因此,计数并不会出现问题,刀库的分度动作表现为 “正常”,如图 9 所示。
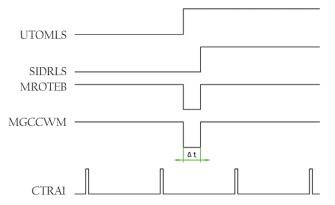
图 9 分度“正常”
基于以上分析,可知 : 问题间隔时长时短,或者数小时,或者数天,是随机的。
(5)其他现象的解释
通过观察,由于初始刀套号为 2,目标刀套号为 20,刀库逆时针转动的路径较长。在 “机械手单元向刀库侧移动” 的过程中,刀库的分度仍然没有结束,给 Δt 的出现提供了可能,即给问题情况的出现提供了可能,因而问题集中地出现在 20 号刀具的还刀动作中。
加工程序中所涉及的其他的目标刀具号对应的刀库转动路径较短,机械手单元向刀库侧动作还没有来得及执行,即 Δt 还没有来得及出现,刀库已经到达目标刀套位,因此刀库分度表现 “正常”。试想,如果使得 Δt 出现在 “机械手单元向主轴” 转动的过程中,那么分度故障就不再仅仅局限于路径较长的目标刀套了,路径较短的目标刀套也是有可能出现故障的,这里不再赘述。在 “备刀动作” 中,机械手单元向刀库侧的动作以及向主轴侧的动作均是不存在的,相应地,Δt 也就不存在,当然也就不可能出现该故障现象了,所以说,在备刀动作中,未见异常。
4.问题解决
从液压和电气两个方面着手来解决问题。
(1)液压调整
将滑板右移动作的流量略微调大,使得 Δt不再出现,相关液压动作更加协调,稳定性和可靠性随之增强,如图 10 所示。
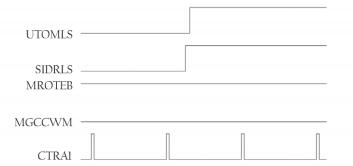
图 10 流量调整
(2)电气调整
对梯形图稍加处理,将 MGCCWM 和MGCCWS 分别写在两段梯形图中,且 MROTEB只作为刀库反转动作阀 MGCCWS 的一个必要条件,放置在刀库反转输出信号 MGCCWS 的一段中。MGCCWM 一旦接通,便不再受 MR O T EB 的控制,始终保持为 1 直至逆时针转动结束,这就完全避免了计数器的加减方向 UPDOWN 在Δt 时间段内被切断的现象,如图 11 所示。改进措施进一步提升了刀库分度动作的容错能力。经过验证,问题现象消除,问题解决。

图 11 处理完的 MGCCWM 和 MROTEB
二、换刀过程中数据的二次刷新问题
1.刀库简介
盘式刀库如图 12 所示,该刀库采用三相异步电动机配合计数开关进行分度定位,并采用随机式换刀模式(刀具号和刀套号之间并没有一一对应的关系),刀库容量为 24。刀套上(即回刀)、刀套下(即倒刀)、侧门开和侧门关均是由气动电磁阀控制,机械手旋转机构选用凸轮式机构,由三相异步电机驱动一空间凸轮装置按顺序动作。
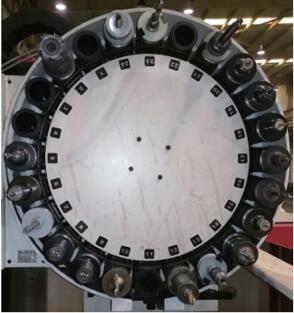
图 12 盘式刀库
2.问题规律
试切项目为钻孔加工,每加工完一个完整工件,操作者均要通过检具来检验加工尺寸是否合格,这期间,发现偶有废品出现。比如,某次检测完精度 , 通过对孔径尺寸的分析知,2号刀具和 3 号刀具发生了 “刀具对调现象” :2号刀加工了 3 号刀应该加工的孔位,3 号刀却加工了 2 号刀应该加工的孔位。后续的试验中,这种 “刀具对调现象” 又陆续地出现了,比如 :4 号和 5 号刀具,5 号和 9 号刀具。结合加工程序中刀具号的呼叫顺序,如表 3。可总结得该问题现象的规律 :发生对调的两把刀具均无一例外的为程序中“相邻的两把刀具”。问题发生的间隔时长时短,或者数小时,或者数天。
表3 加工程序中的刀号顺序
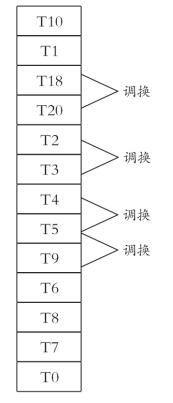
3.问题分析
刀具的 “ 对调” 现象,直观的表现为 “ 刀库分度” 错误。即执行 “T0 2 M06”,应寻找 2 号刀具并将其换到主轴上,而实际上换到主轴上的却是 3 号刀具 ; 执行 “T03M06”,应寻找 3 号刀具并将其换到主轴上,而实际上换到主轴上的却是 2 号刀具。可是 , 如果只是单纯的 “刀库分度”问题,则刀号错误应表现出很强的随机性,这无法解释问题所表现出来的 “两把刀具相邻” 这一显著特点。
刀库的分度与数据表息息相关,对数据表进行二进制数据的检索是此类型刀库分度的核心,试想,如果在刀库分度之前,数据表就已经出现了差错。那么在进行二进制数据的检索时,自然会出现错误,进而刀库分度错误,最终表现为刀具交换错误,导致加工尺寸不合格。因此有必要对数据表Ⅰ进行确认,该数据表到底是什么样子的呢?实际上,系统上显示的只有Ⅱ号工件加工结束后的当前数据表Ⅱ的内容。
(1)数据表Ⅱ
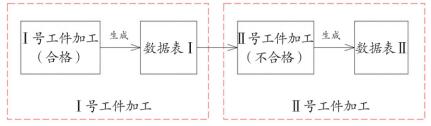
图 13
查看系统 PMC 参数中的当前数据表Ⅱ,并查看每个刀套中当前所安装的物理刀具,可得表4。正常情况下,数据表中的数据和物理刀具是“捆绑”在一起的,数据反映的即是物理刀具号。但是,表 4 却发现两处错误 :
表 4 数据表Ⅱ
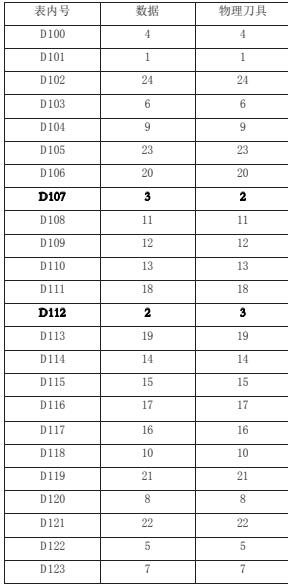
①地址 D107 的数据为 3,与 D107 对应的8 号刀套中存放的物理刀具却为 2 号刀具。②地址 D112 的数据为 2,与 D112 对应的13 号刀套中存放的物理刀具却为 3 号刀具。
(2)数据表Ⅰ
在“Ⅰ号工件加工”过程中,T2正常加工完成,执行 T3…M6, 刀库中的 T3 与主轴上的 T2 进行了物理上的交换,因此 T3 也正常加工完成。基于此,做出推测 :在此交换过程中,2 号刀具和数据表中的数据 3 “捆绑” 在了一起,3 号刀具和数据表中的数据 2 “捆绑” 在了一起。
数据表Ⅰ出现了错误,外部表现为数据表Ⅰ “没有刷新”。然而,由 PLC 逻辑关系可知,既然物理刀具的交换动作已经顺利完成,说明数据更新脉冲 PULSE 产生过,因此确认数据表Ⅰ经历过刷新。
(3)数据表Ⅰ的 2 次刷新
进一步查看 PLC 如图14 知,在ATC 电机运转的条件 M 6 6 M 中“刀库计数开关MGCLS”、“刀套下开关 POTDNLS” 和 “门开开关 SDOPLS” 均为外部开关,在 ATC 电机运转过程中,不妨假设某个开关闪烁了 1 次,那么,PULSE1 便会重来 1 次。这样,数据的刷新也再次重复一次,也就是说,数据表 1 刷新了 2 次,也就表现为 “数据没有刷新”。
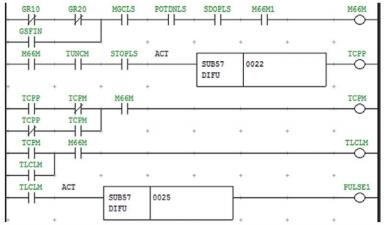
图 14 数据表刷新脉冲
其中 :
M66M:ATC 电机运转的条件
TUNCM: 松刀位
TCPM: 松刀指令
STOPLS: 停止位
SDOPLS: 门开开关
PULSE: 数据更新脉冲
4.问题解决
从机械和电气两个方面着手来进行解决。
(1)机械调整
基于 “2.3.3 数据表Ⅰ的 2 次刷新”中的分析,检查 :“ 刀库计数开关 MG C L S ” 、“刀套下开关 POTDNLS”和“刀库侧门开开关 SDOPLS”,发现 “刀库侧门开开 关SDOPLS”有松动,机械上进行调整,使之稳定可靠,避免闪烁现象。
(2)电气调整
由以上的分析可知,将 M66M 做如下的自锁处理,如图 15。这样,有效的消除了外部开关信号的闪烁干扰,提升了 ATC 动作的容错能力,因而 ATC 动作的稳定性和可靠性大大增强。经过验证,问题现象消除,问题解决。
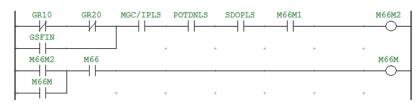
图 15 M66M 的自锁处理
三、总结与展望
对于电气调试期间出现的问题,尤其是随机性的问题,要善于从杂乱无章的信息中总结内在的固有规律,进而大大地缩小问题排查范围,具体问题具体分析,就一定能够探索出问题的根本原因,进而解决问题。两个例子在因果环节中均表现出了显著的 “蝴蝶效应”,这就需要在机床调试中多注重细节,多积累,做总结,做到举一反三,做到触类旁通。
投稿箱:
如果您有机床行业、企业相关新闻稿件发表,或进行资讯合作,欢迎联系本网编辑部, 邮箱:skjcsc@vip.sina.com
如果您有机床行业、企业相关新闻稿件发表,或进行资讯合作,欢迎联系本网编辑部, 邮箱:skjcsc@vip.sina.com
更多相关信息
- target=_blank> 3C 产品的模具制作与生产工艺略谈
- target=_blank>随动刀库的任意换刀点的控制
- target=_blank>当模具制造与工业4.0相碰撞--刀具牌号、加工方式和有助提高生产效率的数字化集成
- target=_blank>CIMT2021部分增材制造机床展品评述
- target=_blank>数控车削加工中的实用对刀方法探讨