编程方式对加工表面质量的影响分析及解决方法
摘要: 所谓数控加工程序,就是一个零件在 NC 机床上的加工顺序、刀具移动的轨迹以及加工工艺参数和辅助功能等信息,用字母代码和数字以一定的格式编写出来。根据零件的复杂程度,可根据不同的编程方式使用手动编程或自动编程。在实际数控加工应用中,为了提高工作效率,降低编程出错率、减少不必要的劳动力等情况,多数数控加工采用自动编程,但由于某一些特殊应用环境下,如模型曲面的绘图精度 , 模型在不同软件的导入导出下精度缺失 , 三维转二维图形的点、线衔接失真等因素,导致自动编程出现编程轨迹杂点或不均匀,从而导致表面质量缺陷。本文主要对此特殊应用时产生的不规则轨迹对加工表面质量的影响分析,同时对该问题提出的一种解决思路。
关键词 : 数控程序 ; 插补 ; 加工 ; 表面质量 ; 华中数控系统 ; 匀顺轨迹优化
1.引言
数控编程实际就是将二维轮廓轨迹或三维曲面造型等轨迹转化成数控系统能够识别的 G 代码,在编程中用得最多的 G 指令就是 G00 快速定位、G01 直线插补、G02 顺圆插补及 G03 逆圆插补。
所谓插补就是机床数控系统依照一定方法确定刀具运动轨迹的过程,插补是一个实时进行的数据密化的过程,不论是何种插补算法,运算原理基本相同,其作用都是根据给定的信息进行数据算,不断计算出参与插补运动的各坐标轴的进给指令,然后分别驱动各自相应的执行部件产生协调动,以使被控机械部件按理想的路线与速度移动。
对于标准的线、圆弧组成的二维轨迹,我们可采用手动编程或自动编程,通过 G0、G01、G02、G03 等插补指令来模拟轨迹路径,而对于不规则的曲线、样条、曲面造型等,就需要通过自动编程使用 G01 来逼近模拟路径轨迹,这种全由G01 直线插补逼近的轨迹俗称小线段。
自动编程的软件有很多, 如UG、ASTERCAM、北京精雕、Powermill、CAXA 等。在编制程序前,都会对模型进行处理,三维转二维轮廓轨迹,各模型图档的文件导入导出,不同的软件打开不同的模型文档都可能会存在轨迹精度缺失,或标准轮廓从新以样条构建的形式存在,从而导致软件编程时出现噪点、拐角轨迹错乱、轨迹不均匀、轨迹精度差等情况,造成加工表面质量欠缺。为了解决这些因素造成的表面质量,可以从二维三维图档处理、编程参数设定、系统算法处理三个方面进行规避。
2. 常见模型处理后的程序编程引起的特殊轨迹分析
2.1 模型在不同的软件导入导出后,提取线框编程时产生的特殊轨迹各种绘图及编程软件, 如 UG、MASTERCAM、CAD、Powermill 等, 在使用过程中经常会遇到模型之间的格式互相转换,导入导出后在不同的软件中打开进行编程,此时可能会出现模型的精度缺失,转换后得模型提取二维线框时产生曲线打断重组、样条拟合的情况,造成编程时圆弧段轨迹产生步长不一致,无规则的直线圆弧拼接的特殊轨迹。
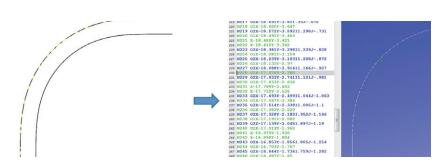
二维线框圆弧段被离散重组 离散后的曲线编程得到的程序轨迹
2.2 曲面造型时的精度与方式,造成编程时产生的特殊轨迹对曲面、拐角等进行造型时,往往由于造型时曲面精度的误差、曲面或拐角造型的方式、曲面导入导出后失真、编程的参数影响等,在自动编程时,可能会出现程序轨迹不均匀,程序插补点杂乱,参差不齐的现象。
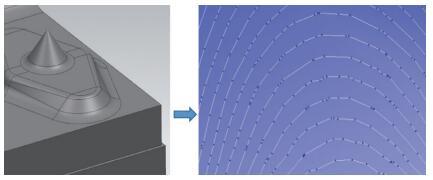
多拐角曲面造型 放大后拐角处的程序节点轨迹
2.3 编程软件及后处理造成的轨迹噪点不同的编程软件,在曲面造型时、或经过转换处理的三维模型及二维线框模型,编程设置不同的参数生成程序轨迹后,使用不同的后处理,可能程序的节点数会有明显的区别,根据现场用户不断的反馈及案例调研,噪点存在的编程轨迹居多。
例如以下几种常见形式存在的噪点。
形式 1: 轨迹折返噪点
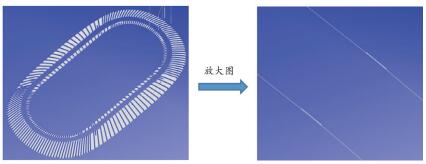
曲面编程时,由于曲面造型的失真,出现 0.01mm 以内的折返噪点
形式 2: 单轴方向噪点
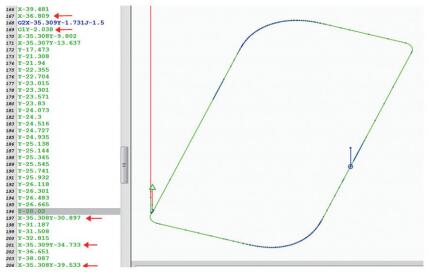
X 轴单轴移动时,出现 0.001mm 单轴反向噪点
3. 产生特殊轨迹后,对加工表面质量的影响分析
3.1 二维轮廓中的曲线打断重组、样条拟合等情况,编程时圆弧段轨迹产生步长不一致,无规则的直线圆弧拼接的特殊轨迹,在程序段中直接体现为 G1G2 的连续程序段,会造成圆弧转角处出现明显深浅不一的竖纹或波浪块状纹。
3.2 曲面精度的误差、曲面或拐角造型的方式、曲面导入导出后失真可能会出现程序轨迹节点不均匀,参差不齐,在程序段中直接体现为不规则平滑的小线段程序,会造成拐角处出现过切痕。
3.3 编程程序中出现的噪点,经常会以不同的形式出现,微小线段的折返、微小线段的单轴反向、同向轨迹中微小线段的夹角节点等,在程序段中直接体现为单节点的异常点程序,会造成表面噪点处多出单一切痕。
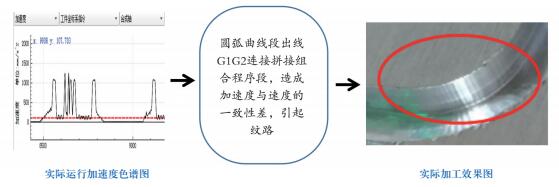
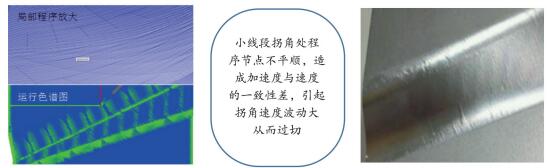
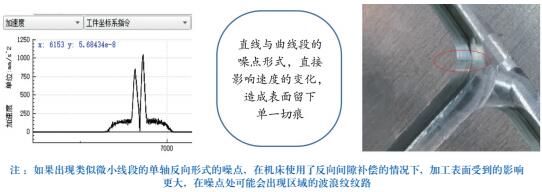
4. 对特殊轨迹造成的加工表面质量解决方法
特殊轨迹对加工表面质量的影响分析中可以看出,一般多数是编程轨迹节点不均匀,异常噪点、曲线以微小线段直线插补与圆弧插补 G1G2代码拼接的形式,从而引起速度加速度变化的一致性差,造成实际加工应用表面质量缺陷。
解决方法1:通过编程手段解决
针对曲线以微小线段直线插补与圆弧插补G1G2 代码拼接形式的程序代码,可通过编程软件参数设置进行相关设置,需要提高编程轨迹精度,进行圆弧离散编程。如 MasterCam2018、UG、第三方软件处理源程序等均可实现。
解决方法2:对模型进行补面修补重造型处理在曲面或拐角造型时,由于造型相切或位置时,设置过大的精度值,导致曲面拐角连接的平顺性存在缺陷。或者模型的导入导出等因素造成模型图素变形等情况,从而影
响编程时拐角或曲面处出现程序节点不平滑,参差不齐的情况。一般情况下,可通过一下情况进行处理,但工作量会增加。
可通过补面的方式重塑模型,对有问题部分进行局部处理 在进行曲面的相切处理时,提高相切的精度误差 导入导出的模型注意提高精度识别,如果变形产生误差时,对局部要进行重塑曲面处理 程序编程时,在不影响工件精度要求时,可适量放低轨迹的编程精度上下偏差,同时对拐角进行平顺处理注 :此方法对工作人员的技术及工作量大,要求较高,实际应用中并不常见。解决方法3:通过数控系统端的轨迹算法进行处理加工针对微直线段和圆弧段混合、线段长度极度不均匀、线段转角波动较大、噪点等轨迹缺陷,系统内部能够进行前后程序段的预读后,在误差范围内,根据程序节点的变化曲率进行轨迹节点的重新计算拟合和处理,从而控制加工轨迹及速度的一致性。
如华中数控系统的匀顺功能,能够快速有效地对上述轨迹缺陷进行匀顺光顺,在允差范围内纠正程序指令点,纠正后的指令点组成的加工轨迹与原始的加工轨迹相比,长度及转角都能均匀一致。
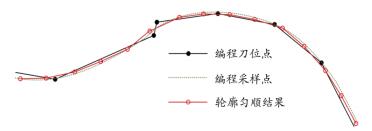
匀顺示意图
①对二维轮廓实际应用色谱图与实际加工效果的改善 :
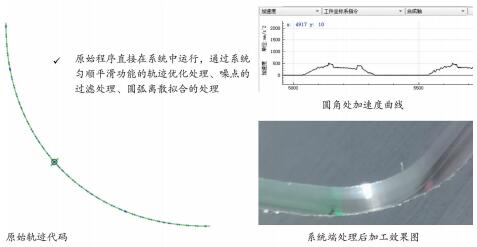
②对三维曲面拐角实际应用色谱图与实际加工效果的改善 :
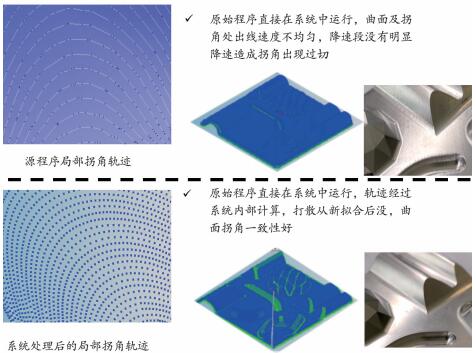
5.结语
在实际的加工应用中,不同的编程员、不同的模型处理方法、不同的编程方式,直接对程序有很大的影响,从而间接的造成实际加工中的表面质量欠缺。
不同的特殊代码程序,根据实际应用环境而定,可使用不同的处理方式。无论是手动优化、第三方软件处理、重造型、曲面拐角修补后后处理、还是通过系统的内部轨迹优化算法内部处理等,最终达到我们需要的理想加工效果。
投稿箱:
如果您有机床行业、企业相关新闻稿件发表,或进行资讯合作,欢迎联系本网编辑部, 邮箱:skjcsc@vip.sina.com
如果您有机床行业、企业相关新闻稿件发表,或进行资讯合作,欢迎联系本网编辑部, 邮箱:skjcsc@vip.sina.com
更多相关信息
- target=_blank>雷尼绍光栅产品助力打造设计“独特”的直线电机
- target=_blank> 有关精密卧式加工中心产品的研究
- target=_blank>肯纳金属的KYHK15B™材质刀片在高达58HRC的硬材料车削应用中具有更高的耐磨性和更长的刀具寿命
- target=_blank>斯凯孚、铁姆肯 , 他们轴承游隙调整的技术优势
- target=_blank>加工中心主轴拉刀机构的设计与研究