车铣复合加工中心主轴结构的有限元分析
2022-5-30 来源:齐齐哈尔工程学院 作者:谢伟东
摘要: 车铣复合加工中心主轴是系统结构中的关键性零件,机床在运行过程中会受到不同程度的切削力,想要防止机床变形问题的发生率,需要通过科学的结构设置保证机床的刚度,当承受较大的切削力时,依然保有较高的加工精度,降低自激振动问题的发生。采用有限元分析技术创建系统模型,通过车铣复合加工中心主轴结构的设计调整,对主轴刚度进行分析验算,车铣复合加工中心主要包括单元技术、机床整机技术,其中主轴单元属于单元技术的重要环节。车铣复合加工中心主轴(电主轴)结构的有限元分析,主要研究目的是提高机床运行的稳定性,保证加工精度和主轴刚度。
关键词:车铣复合加工中心;主轴结构;有限元分析
0 引言
车铣复合加工中心主轴结构包括:主轴电机、主轴和轴承等部分,主轴作为机床的核心部件,其结构性能对在整台机床的运行稳定性有着重要影响,想要全面提高切削速度、保证机械加工精度,就需要建立有限元分析模型,分析主轴结构性能。主轴结构设计中的技术手段相互制约,解决速度与刚度之间的矛盾,借助有限元分析法的便利性和灵活性,对车铣复合加工主轴结构进行分析,通常情况下安装两个主轴,实现在不停车状态下的自动对接转移,自动化完成绝大部分的工件加工工作,提高加工效率。
1、车铣复合加工中心主轴结构
1.1 车铣复合加工中心主轴结构
结合轴承结构的主要特点,车铣复合加工中心主轴通常 只存在径向刚度,简化处理后发现径向压缩弹簧。车铣复合加工中心主轴简化后的力学模型分析过程中,可以有选择的忽略轴承刚度与转速、负荷之间的关系,假设轴承的刚度为标准常数进行后续的有限元分析工作,这一过程中省略了工作人员的计算量,结合主轴结构类型,主要采用滚动轴承,省略阻力因素分析并不会对最终的分析结果产生影响。如图1所示,简化主轴刚度细节部位进行整体显示。
1.1.1 轴壳
在进行主轴结构分析的过程中,轴壳作为主要部件之间,其尺寸与位置会对主轴设计精度产生影响,通过安装过程的查看,设计人员将轴承座孔安装到轴壳上,在进行电机定子安装的过程中,需要保持一端处于开放状态。一些大型的主轴结构中,为了安装便利,会在轴壳两端设计的过程中采用开放型设计原理,提高主轴的运行速度,保证运行功率,其中转子直径要高于轴承外径,实现对机床装配精度的控制,后轴承安装区域提供无间隙配合。
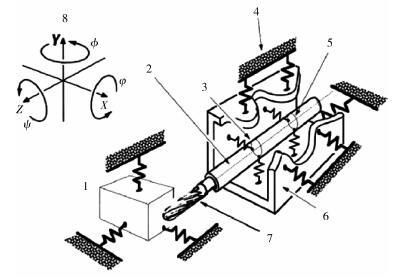
图1 车铣复合加工中心主轴简化后的力学模型
1.1.2 转轴
转轴属于主轴的重要回转体,转轴的实际精度会对主轴的整体精度产生影响,采用的转轴对形位公差、尺寸精度有着高质量要求,转轴在高速运转的过程中,受到偏心质量的影响产生不规则振动,无法保证机床动态性能的稳定性,需要借助有限元测试转轴的动平衡,在测试的过程中一部分转轴上的零件要同时接受动平衡测试。
1.1.3 轴承
精密轴承作为主轴的核心支承部件,其尺寸、位置和功能会对主轴最高转速产生影响,因此在主轴结构设计的过程中,需要选择高速性能、动负荷承载强以及发热量小的精度轴承,其中常见的类型有:动静压轴承、磁浮轴承等。
1.2 主轴电机有限元分析
1.2.1 电机的有限元仿真
在进行主轴电机有限元分析的过程中,采用仿真处理的方式,主要的计算对象是电路、磁路,以此为基础,通过 Ansoft中的 RM xprt模块进行电机结构选择,参与到电磁设计分析的过程中,计算软件仿真建模数据。将已经完成的电机模型信息输入到二维瞬态场。加载几何模型的同时进行模型材料定义,分别设定电机主从边界条件,采用网格划分的形式得到各项信息,转子受力过程中对气隙网格具有一定的敏感性,因此,在得到的最小气隙处分别设置了多层网格,计算出主轴电机电磁转矩,了解主轴电机的电流变化流程。
1.2.2 二维电机瞬态分析
将已经构建完成的仿真模型输入到 Maxwell2D 瞬态场,利用数据分析软件定义电机内部的主材料、设定精准度的边界条件,合理添加激励源,做好网格划分处理。如图2所示,计算磁链在经过转子齿面时的疏密程度,分析转子齿部尺寸对最终分析结果的影响,并结合呈现的数据效果图示,得出转子电阻与转子齿部尺寸的关系,保证漏抗与加工速度相契合。在主轴电机结构设计的过程中满足机床运行速度范围内的功率、扭矩需求,全面提高转子旋转阶段强度。
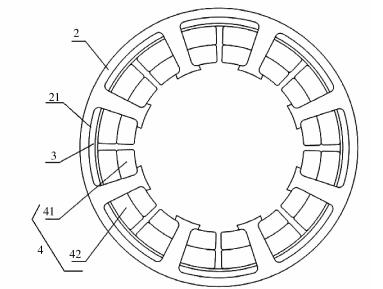
图2 双层绕组
1.3 主轴电机绕组设计
主轴电机的定子绕组为励磁绕组,在主轴结构设计的过程中电机绕组设计质量会影响到主轴动力性能,车铣复合加工中心主轴电机绕组设计过程中采用单层绕组,需要在每个槽放置线圈边。单层绕组的线圈槽数量较少,实现对槽面积的综合利用,绕组的断口接线长度有限,无法随意进行节距调整,绕组的端部交叠安装,具有较高的稳定性。在进行绕组类型选择的过程中,要结合主轴结构特点进行综合考量,车铣复合加工中心主轴的定子槽较浅,主要采用双层绕组,在嵌线阶段会遇到很多问题,绕组的散热性能较差,但双层绕组的应用能够降低高次谐波损耗。
1.4 电机定子绕组的有限元分析
1.4.1 有限元模型的建立
车铣复合加工中心主轴定子绕组为三相12/8极结构SITM,结合SRM定转子外径与内径的数据信息,对定转子极弧系数、气隙等数据进行调整,选择合适的零件尺寸完成主轴结构设计与安装,在计算机数据系统中生成了几何模型进行有限元分析,从机床控制接口输入几何模型,利用瞬态模块完成二维时步有限元计算。通过计算机软件定义外加电路,分别建立功率变换器分析模型、驱动电路分析模型,彼此之间相互验证形成仿真体系。
1.4.2 三角形单元网格剖分
定子绕组有限元分析的前提是电机模型的建立,定义运动边界的限制条件,通过有限元算法分析的时间步长,了解电机系统网格的划分情况。Maxwen能够自动剖分有限元网格,在实际分析计算过程中,当计算精度无法满足分析需求时,需要借助手工操作的方式,全面提高气隙区域的网格密度。三角形单元网格剖分形式的运用,划分过程十分仔细,网格的剖分精度较高,但需要机器保持高运行时长。在进行磁场能量集中、磁场变化快的气隙区域,要确保网格划分的精细程度,提高计算精度的同时,完成磁场变化不明显的电机区域网格划分。有限元计算需要具备理想的边界条件(磁通平行边界),在进行绕组激励源输入的过程中,要通过外电路完成输入,建立SRM 驱动电路分析模型。
2、有限元分析车铣复合加工中心主轴结构
2.1 有限元分析的主要流程
想要保证系统运行的稳定性、分析结果的准确性,就需要结合车铣复合加工中心主轴的实际构成情况,建立三维实体模型,在此基础上进行静态分析,适当地对主轴增加约束力和载荷重量,根据有限元模型显示的各项数据信息,在 ANSYSY 里求解,分析机床主轴的广义特征。
通过合理计算得到车铣复合加工中心主轴的有限元节点,分析有限元模型坐标系中产生的变形情况和移动情况,借助表格与色度图的显示形式,向计算人员展示设备与零件的位移数值与扭转变形的程度。分析多个节点的变形强弱,对主轴运行阶段承受的应力大小进行计算,同时得到车铣复合加工中心主轴应力的主要受力点,分析多个节点的位移变化,将得到的数值代入到径向刚度计算公 式:Kr=F/W ,完成车铣复合加工中心主轴刚 度计算。
2.1.1 主轴部件有限元模型
车铣复合加工中心主轴普遍为阶梯空心轴,在进行主轴部件动态、静态设计的过程中,需要利用有限元分析软件(ANSYS)对主轴部件的工作情况进行分析,根据运行时期工件的具体表现,制定主轴部件有限元模型,对分析流程进行分割。一般情况下,车铣复合加工中心主轴部件构成,需要前后两套角与陶瓷球轴承建立支撑关系,保证前轴承的固定状态,能够完成承受径向载荷、双向轴向载荷,后轴承在定向阶段会产生轻微的位移,在进行主轴工作热伸长的补偿处理阶段,前后轴承在完成定位转移的同时,将盈套固定在主轴区间。电机转子改变键联接的状态,转移到前后轴承之间,转矩的传递工作需要借助压配合的摩擦力完成。
主轴部件建模的过程中,需要通过有限元分析 AN-SYS,计算简化处理后实体模型的具体尺寸,生成关键节点,在得到的截面上进行平面单元设计,主要采用手工划分网格离散的处理形式,将带网格的截面转化为带网格的物体。结合现有的主轴约束条件,参考主轴结构设计的实际情况,进行科学的有限元分析,计算得到主轴的载荷条件,分析车铣复合加工中心主轴的铣削力。
2.1.2 特定结构的振动特征分析
特定结构的振动特征分析指的是主轴结构的固有频率以及振型,采用模态分析的形式进行主轴结构故障诊查,通过得到的固有频率值分析了解主轴结构的整体刚度,分析结论:固有频率越大、结构刚度越大。分析主轴结构故障产生的主要原因,将机床振动形式分为自由振动、被动振动和自激振动三种,机床振动可能造成刀具位移,影响工件的运行速度,无法保证工件的加工精度,最终的机床加工精度、效率不理想的后果。建立有限元分析模型计算机床固有频率,是保证机床整体性能的主要手段。
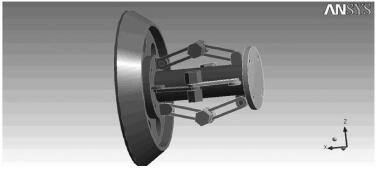
图3 ANSYS中主轴部件模型
2.2 车铣复合加工中心主轴结构特点
2.2.1 主轴结构静态分析
通过有限元分析技术对车铣复合加工中心主轴结构特点进行了解,静态分析首先需要了解主轴变化前后所产生的位移矢量,分析车铣复合加工中心主轴变形的主要区域,变形问题主要出现在主轴的前端部位,这是因为主轴前端作为主要受力点。与之相反后主轴端的变形问题并不严重,通过调查分析表明,车铣复合加工中心主轴的受力点所产生的应力最大,随着坐标的移动,应力也逐渐向主轴后端移动。
2.2.2 主轴结构模态分析
采用三维实体模态分析法,对车铣复合加工中心主轴的运行状态进行观察,主要的分析内容是,机床高速铣头的固有振动频率,以此作为依据了解振动特性与响应特性,无阻尼自由振动实验得到车铣复合加工中心主轴的固有振动特性,如表 1 所示,在检验固有频率的同时,分析振动的主要类型以及振动过程中产生的应力数值。车铣复合加工中心主轴运行的过程中,通过交变循环产生应力作用到主轴,产生生产疲劳,对内部设备和工件造成不同程度的破坏。因此,需要制定出合理的解决方案提高主轴结构强度,借助模态分析法计算出主轴的固有频率与临界转速,通过数据调整在有效转速 < 临界转速的状态下重新定位,避免对共振区域造成损耗,全面提高主轴设计成效。
表1 电主轴的固有振动频率和振型
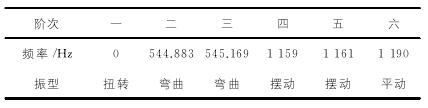
2.3 主轴结构铣削静刚度分析
铣削静刚度分析的主要目的是,了解机器在运行过程中,各项数据是否满足机床精度加工标准,在车铣复合加工中心主轴的静刚度分析阶段,结合静载荷、位移比值,通过模型演示,利用极端公式分析主轴刚度。车铣复合加工中心主轴结构中主轴箱前端呈现出六角外形,倾斜分布加强筋对主轴载荷进行分解,当主轴箱的头部呈现出矩形,主轴孔壁会与板壁之间相切,同时在另外一侧设置加强筋作为支撑,主轴载荷分解转移到左壁、两处加强筋上。选择合适形状的对角筋,能够全面提高主轴箱的弯曲刚度,降低立柱发生变形的概率,如表 2 所示,在主轴结构设计阶段,通过有限元分析得到主轴刚度的极差变化,降低主轴面内弯曲问题的发生。
表2 主轴刚度的极差分析表
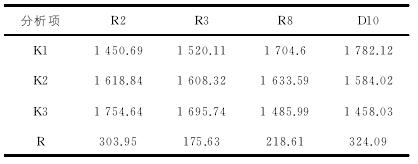
总结:在车铣复合加工中心主轴结构问题解决的过程中,需要通过有限元分析得到准确的主轴端变形动态演示,在有 ANSYS软件中以动画播放的形式表现出来,并做好视频、数据记录找到危险截面的所处区域,显示出临近受力点的轴肩区域工作情况,通过轴有限元模型完成2D、3D 的主轴模态分析,为车铣复合加工中心主轴结构设计提供精准的参考数据,作为设计修改的基础。
投稿箱:
如果您有机床行业、企业相关新闻稿件发表,或进行资讯合作,欢迎联系本网编辑部, 邮箱:skjcsc@vip.sina.com
如果您有机床行业、企业相关新闻稿件发表,或进行资讯合作,欢迎联系本网编辑部, 邮箱:skjcsc@vip.sina.com
更多相关信息