C系列飞机固定器类零件数字化加工技术
2021-3-26 来源: 沈阳飞机工业(集团)有限公司 作者:锁聪
摘要:为了解决C系列飞机固定器类零件加工困难的问题,设计了一种典型的数控加工工艺。针对特殊结构,设计制造专用刀具。借助三维CAM软件,编制数控加工程序,合理制定刀具轨迹,生成数控机床专用NC代码。利用几何仿真软件,对NC代码进行仿真检查,避免撞刀、过切等意外情况的发生。最后,对典型零件进行实际的切削加工,零件的尺寸精度及外形精度均符合设计图样要求,表明了此加工工艺的可行性,为C系列飞机固定器类零件的数控加工提供了一种典型的工艺方案。
关键词:数字化加工;双曲率;T型槽;数控编程;仿真检查
0 引 言
C系列飞机固定器类零件共90余项,属舱门附件,主要用于固定密封胶条。该类零件整体结构复杂,外形为复杂双曲面,内部含带曲率T型槽结构,加工困难。此外,零件各处厚度尺寸较小,加工过程中极易发生变形,尺寸精度和型面精度均不易保证。固定器类零件虽外形结构各不相同,但T型槽截面尺寸一致,属于结构相似类零件,若找到一种稳妥可靠的加工方案,即可完成全部此类零件的加工。
1、 零件分析
固定器类零件整体数量较多,通过全尺寸分析,选出一项典型零件,包含了所有 该 类 零件的典型特征,以此零件为基础,开展工艺研究,典型零件示意图如图1所示。
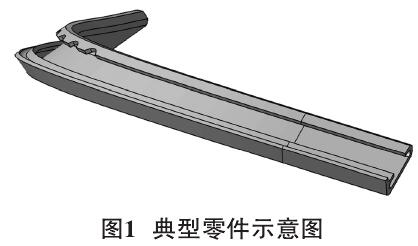
1.1 毛坯信息
零件由铝合金预拉伸板材机加而成,材料牌号为7475 T7351 ,材料厚度为1.5 in(约38.1 mm)。考虑到零件装夹及加工基准设置等多方面因素,毛坯尺寸需略大于零件尺寸,通过测量零件实际尺寸,最终确定毛坯长宽尺寸为350 mm×180 mm。毛坯材料为高强度铝合金,加工性能尚可,属于易加工材料。
1.2 典型结构特征
零件整体结构复杂,相对于平板零件,既有一定程度的弯曲,又有一定程度的扭曲,内外形均为复杂双曲面。此外,最为突出的则是其T型槽结构,一般零件的T型槽为简单直槽或单曲率T型槽,但该零件的T型槽跟随其内外形面,为复杂双曲率T型槽,这就给T型槽的加工带来了极大的挑战。虽然零件整体结构复杂,但是通过细致分析,也找到了一定规律。零件可近似看做一等截面结构,提取零件截面,沿着一条空间复杂曲线拉伸,即形成了三维几何实体,零件构成示意图如图2所示。对零件三维构成的清晰分析,也为后续的加工带来了新的思路。
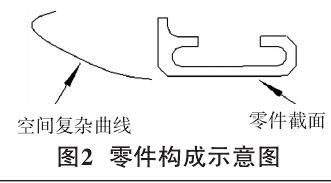
1.3 零件尺寸及精度
零件属薄壁结构,所有厚度尺寸均为1.5 mm,尺寸公差为±0.24 mm。考虑到零件的使用需求,需在T型槽内安放密封胶条,保证密封性,故其最重要的尺寸为T型槽槽口厚度,名义尺寸为3 mm,尺寸公差为±0.2 mm。此外,为了保证零件的顺利安装,对于外形曲面也有严格要求,外形曲面的面轮廓度要求为0.25 mm。
2、 加工方案
2.1 机床的选择
该零件外廓尺寸较小,对机床工作台尺寸及加工行程并无特殊要求,但其结构复杂,存在部分开角、闭角结构且角度较大,需选择一台五坐标数控机床才能完成零件的加工[1]。通过具体分析,零件加工过程中摆角最大处发生在T型槽加工过程中,A角行程需超过±50°,C角行程需超过±180°。为了保证加工的顺利进行,选择法国FOREST-LINE机床厂生产的五坐标数控加工中心加工此零件,其A角行程为±110°,C角行程为±360°,完全满足加工需求。
2.2 刀具的选择
零件的材料为高强度铝合金,故选择两齿整体硬质合金立铣刀完成加工,针对零件不同区域,选择直径大小适宜的铣刀进行加工,尽量在刀具一次装夹后完成全部工序内容,减少换刀次数,提高加工效率[2]。
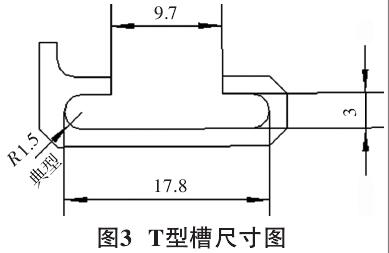
针对零件的特殊区域———T型槽,则需设计制造专用的T型刀具。专用刀具的设计需完全匹配T型槽结构,T型槽具体尺寸如图3所示。由于T型槽厚度为3 mm,底R为1.5 mm,若想完成加工,T型刀具的T型厚度与底R需与零件完全一致,而在刀具直径上,则可以比T型槽宽度17.8mm略小,这样可以分多次加工到位,减少每次加工量,保证T型槽内壁的加工质量。此外,T型槽开口宽度仅为9.7mm,还需考虑刀杆直径,避免加工过程中发生撞刀。综合以上因素,设计了一把专用T型刀具,具体的结构尺寸如图4所示,刀具直径为16 mm,刀具底R为1.5 mm,T型部分厚度为3 mm,刀具的尾部采用直柄夹持的方式,直径同样为16 mm,而在刀杆进入T型槽的部位则设置了缩颈,直径为6 mm,这种设 计 方 式 既 保 证了刀具的整体刚性,又避免了加工过程中发生刀具碰撞,可以确保专用刀具顺利完成T型槽的加工。

2.3 加工流程
零件需双面加工 ,在正式加工前需确定加工基准。将板材毛坯上下表面铣平见光,作为Z向加工基准,铣出一长一短两条直角边,作为X向和Y向加工基准。在毛坯周边布置若干压板,进行轴向压紧,压入量不宜过多,约为10 mm,避免加工过程中刀具与压板碰撞。由于压板位置均设置在毛坯周边,在一次装夹后即可完成本道工序的全部加工内容,无需窜动压板,减轻了操作人员的工作量,减少了零件生产的辅助时间。一般来讲,选择结构要素较少的一面作为第一面,优先加工,针对此零件,则选择无T型槽的一面优先加工。零件第一面为复杂双曲面,综合考量零件尺寸及加工效率,选取25R3立铣刀进行粗加工,采取轴向分层的方式,每层均匀去除余量,留余量1 mm。为了减少换刀次数,在半精加工时仍然选择此把刀具,半精加工后应保证余量均匀,为精加工做好准备。精加工时仍然无需换刀,采用定角度行切的方式,完成零件外形曲面的精加工。精加工时合理设置切削用量,保证外形曲面的加工精度及表面粗糙度符合设计要求。
第一面加工完成后,将零件翻面,进行第二面的加工,加工基准与第一面保持一致,确保双面加工零件的准确性。零件第二面虽结构较多,但仍优先加工出复杂型面,加工方式与第一面相同。然后对T型槽区域进行加工,T型槽的加工一共分两步,首先选用8R0立铣刀加工T型槽口,为后续的T型刀加工清除障碍。然后使用专用T型刀具,进行T型槽宽度的加工,宽度加工共需要3刀,第一刀从T型槽的正中间通过,左右两侧均匀留有余量,然后在左右两侧各补铣一刀,均采用顺铣的方式,完成整个T型槽的加工。最后,对零件进行切断加工,选取12R0立铣刀去除外形余量,只在零件2个端面处留有2个连接筋,厚度与零件厚度一致,待全部加工完成后,由钳工从板材毛坯上去除2个连接筋,卸下零件。
3、 数控编程
在现代化制造领域中,数控编程的软件众多,优势各有不同,怎样发挥一个软件的优势是考验一个编程人员的基本素质。在本次加工中,选用CATIA V5作为编程软件CATIA V5是航空制造业常用的一款CAM软件,其编程简单方便,数据处理能力强,针对不同的零件结构特征,可以灵活地选用不同的编程指令,完成加工。此外,该软件还具有独特的产品 (Product)/过程 (Process)/资源(Resource)模型[3],可以提供真正的协同环境,共享流程信息,是实现人员、工具、方法和资源真正集成的基础。
3.1 编程方法
在本次加工过程中,使用五坐标数控高速铣床,高速铣削不同于普通的数控加工,在许多方面都需特殊注意,在本次数控编程中使用了如下方法[4]:1)粗加工时,采用轴向分层的方式;2) 针对复杂曲面,采用定角度行切加工;3)刀具切入材料时采用斜向下刀;4)保证刀具轨迹平稳,避免机床功率突变;5) 避免加工过程中走刀方向突变;6)粗加工后设置半精加工,保证精加工时余量均匀。
3.2 T型槽区域加工程序的编制
在CATIA V5中,有专用的T型槽加工指令GrooveMilling,但其只针对简单直槽,对于复杂双曲率T型槽则束手无策。常用的方式是使用多轴轮廓加工指令Multi-Axis Flank Contouring来进行替代编程,但该指令也存在一定弊端,即在编程过程中无法使用T型刀具,只能使用立铣刀。这就使得编程人员在编程过程中使用立铣刀来近似编制刀轨,而在实际过程中使用T型刀具来加工。这种方式不但增加了编程人员的工作难度,也使得实际加工出的零件与理论存在一定偏差,极易造成质量事故。
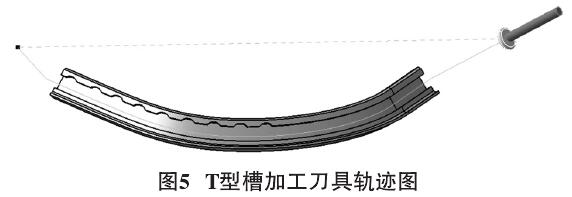
在本次编程过程中,尝试了多种不同的编程方式,经过多方比较 , 最终决定使用多轴参数线加工指令Isoparametric Machining来进行T型槽加工程序的编制[5]。不同于以往选择槽侧面对刀具轨迹进行驱动,使用该指令可以选择T型槽底面,再辅以若干引导点,实现对刀具轨迹的编制。刀轴的运动方式则选择Lead and tilt,使刀轴在加工过程中随形变化,始终保持刀具轴线与所接触曲面的法向保持一致。这种五轴联动的加工方式,可以精确地控制刀具轨迹,随形加工出整个T型槽,保持产品质量,刀具轨迹示意图如图5所示。
4、 仿真检查
VERICUT是一款专为制造业设计的数控加工仿真和优化软件[6],采用虚拟现实技术,对加工过程进行模拟,具有真实的三维实体显示效果,比传统意义上的刀路轨迹仿真更接近于实际加工情况。它可以取代传统的切削试验,真实模拟加工过程中零件、夹具、工作台、机床及刀具切削的实际情况,不仅可以对机床运动状态进行仿真,还能够对数控加工程序进行验证、优化,帮助编程人员修正编程错误,该软件已经成为提高数控加工质量的高效工具。VERICUT系统环境下实现数控加工过程的仿真,通过以下几个步骤实现[7]:1)建立数控机床模型,配置控制系统;2)建立刀具库,定义刀具类型及参数属性;3)调入毛坯模型、零件模型;4)调入NC数控程序;5)虚拟加工仿真,使用自动比对模块检查。
按照上述步骤对零件加工过程进行仿真,对数控加工程序进行切伤及残余检验,通过软件参数的设定,切伤及残余可以用不同颜色显示出来。VERICUT仿真可以使用前置程序,也可以使用后置程序,在本次仿真时使用后置程序,保证仿真程序与最终加工程序一致,避免中间环节错误导致意外情况发生。依据仿真结果,不断修改完善数控加工程序,直至没有切伤及残余发生。
5、 结 论
在本文工作中,设计了一种典型的C系列飞机固定器类零件的数控加工工艺。选取典型零件,针对其复杂双曲率T型槽结构,设计制造了专用刀具,完成特殊区域的加工。借助CATIA V5软件,巧妙运用各种指令,编制数控加工程序,生成数控机床专用NC代码。通过VERICUT软件对NC代码进行仿真,避免加工过程中意外情况的发生。最后,使用五坐标高速数控加工中心对典型零件进行了实际加工,零件的尺寸精度及外形精度均符合设计图样要求。切削结果表明,该工艺方案可以完成典型零件的数控加工,加工效果良好。考虑到固定器类零件结构相似,该类零件均可以使用此种数控加工方案完成加工。
投稿箱:
如果您有机床行业、企业相关新闻稿件发表,或进行资讯合作,欢迎联系本网编辑部, 邮箱:skjcsc@vip.sina.com
如果您有机床行业、企业相关新闻稿件发表,或进行资讯合作,欢迎联系本网编辑部, 邮箱:skjcsc@vip.sina.com
更多相关信息