TF2000 型数控不落轮镟床刀具补偿调整方案研究
2024-7-23 来源:- 作者:-
摘要:针对 TF2000 型数控不落轮镟床刀具补偿调整需要结合数据反复试验效率低下的问题,通过反复试验提出以加工后不同轮形结果为依据进行刀具补偿调整的方案。总结了 10 种不同轮形结果应采取的刀具补偿的调整方案,优化了刀具补偿调整方案,提高了轮对加工效率和精度。
关键词:数控不落轮镟床;刀具补偿;电客车;踏面镟修
数控不落轮镟床是地铁车辆段中常见的工艺设备,主要承担电客车轮对的测量及镟修工作。TF2000 型数控不落轮镟床是一种高性能专用数控机床,主要适用于各类型机车车辆在不解编、不落架的条件下,对日常运营过程中轮对踏面、轮缘的磨损和擦伤进行修复,恢复轮对踏面技术状态[1]。
1、TF2000 型数控不落轮镟床刀具系统
TF2000 型数控不落轮镟床刀具系统采用刀架对称布置方案,每侧刀架均由刀座、刀片、以及固定块组成。刀架是刀具系统的基础,刀座、刀片均固定在刀架上。刀架固定在测向机构上,实现了刀具加工坐标系与测量坐标系的统一。镟床共配置 4 枚刀具,采用垂直刀和水平刀结合加工的方式,通过楔形螺丝与刀片固定块相互作用固定在刀座上。T1 刀(水平刀)负责镟修车轮踏面、倒角及轮缘外侧面,T2 刀(垂直刀)负责镟修车轮的轮缘顶点与轮缘内侧面[2]。T1 刀和 T2 刀具有互换性。
2、TF2000 型数控不落轮镟床轮的加工坐标系
为便于加工根据轮对踏面的技术标准要求建立了加工坐标系 G55。G55 与机床原始坐标系的对应情况见图 1。实线代表刀具的加工轨迹,M 点为机床的坐标系原点;P 点为加工坐标系原点的位置。虚线段 G55X 和 G55Z 分别表示 P 点与 M 点之间的偏移量,即加工坐标系相对于机床坐标系偏移量。
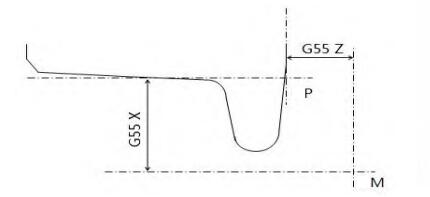
图 1 TF2000 型数控不落轮镟床程序工件坐标系示意图
3、TF2000 型数控不落轮镟床轮的加工轨迹
如图 2,轮对在踏面基点位置与轨道进行接触,由于塑性变形在以基点位置附近形成一个凹陷区;轮缘外侧与轨道在转弯时相互作用,轮缘厚度减小轮缘高度增加,需通过镟修恢复轮对踏面形状。镟床加工程序按照《TBT449-2003 机车车辆车轮轮缘踏面外形》[4]中 LM 磨耗型轮对踏面轮廓
进行编制,加工时严格按照 LM 磨耗型轮对踏面轮廓进行加工,确保修复完成的轮形符合标准要求。
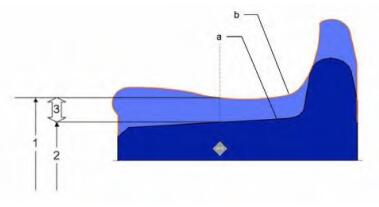
图 2 轮对廓形加工前后对比图
4、TF2000 型数控不落轮镟床刀具补偿调整方案
由于镟修程序中的刀位点都是按照 LM 型车轮踏面尺廓进行编写的,刀具的运动轨迹未考虑到不同尺寸刀具的刀位点[3],因此加工精度收到刀具尺寸影响较大。当刀具更换、磨损时需通过镟床标定结果对刀具补偿进行调整。加工过程中作业人员只能以经验和反复试验确定刀补数据。这种方式需要多次试验,效率低且误差率高。经试验研究发现,以镟床加工原理结合加工后轮对踏面形状,采取相应刀补措施可以提高刀具调整精度,节约刀具调整时间,增加工作效率。
4.1 加工后踏面轮廓正确,直径过大
如图 3 所示,加工后轮对踏面的轮廓符合要求,直径与目标直径相比过大。这种情况说明刀具在 X 方向的切削深度不够,导致轮对踏面 X 方向上的切削量过小。针对这种情况需要适当减小 T1刀和 T2 刀 X 方向的刀具补偿,从而满足切削要求。
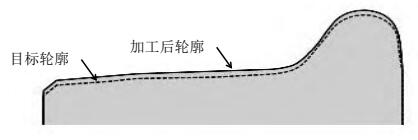
图 3 踏面轮廓正确,直径过大示意图
4.2 加工后踏面轮廓正确,直径过小
如图 4 所示,加工后轮对踏面的轮廓符合要求,直径与目标直径相比过小。这种情况说明刀具在 X 方向的切削深度过多,导致轮对踏面 X 方向上的切削量过大。针对这种情况需要增大 T1 刀和T2 刀 X 方向的刀具补偿,从而满足切削要求。
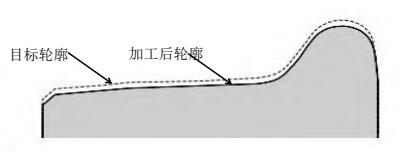
图 4 踏面轮廓正确,直径过小示意图
4.3 加工后踏面轮廓错误,轮缘背面过大
如图 5 所示,加工后轮缘背面过大,轮缘顶点到轮缘内侧面 X 方向上高于车轮踏面、倒角轮缘外侧面,轮缘顶端出现台阶。这种情况说明 T1 刀切削量正常,T2 刀在轮缘顶点到轮缘内侧面 X 方向的切削深度不足,致使在 T1 刀与 T2 刀交接处产生台阶。针对这种情况需要减小 T2 刀 X 方向的
刀具补偿,从而满足切削精度的要求。
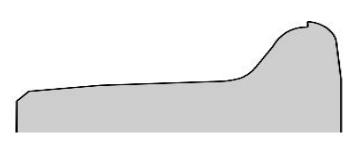
图 5 踏面轮廓错误,轮缘背面过大示意图
4.4 加工后踏面轮廓错误,轮缘背面过切
如图 6 所示,加工后轮缘背面过切,车轮踏面、倒角及轮缘外侧面 X 方向上高于轮缘顶点到轮缘内侧面,轮缘顶端出现台阶。这种情况说明 T1 刀的切削量正常,T2 刀在轮缘顶点到轮缘内侧面X 方向的切削深度过多,致使在 T1 刀与 T2 刀交接处产生台阶。针对这种情况需要增加 T2 刀 X 方
向的刀具补偿,从而满足切削要求。
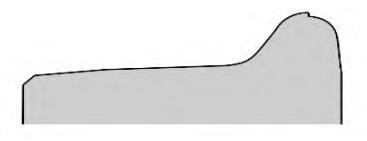
图 6 踏面轮廓错误,轮缘背面过切示意图
4.5 加工后踏面轮廓错误,直径过小
如图 7 所示,加工后踏面直径过小车轮踏面、倒角及轮缘外侧面 X 方向上低于轮缘顶点到轮缘内侧面,轮缘顶端出现台阶。这种情况说明 T2 刀的切削量正常,T1 刀在车轮踏面、倒角及轮缘外侧面 X 方向的切削深度过多,致使在 T1 刀与 T2 刀交接处产生台阶。针对这种情况需要增加 T1 刀 X
方向的刀具补偿,从而满足切削要求。
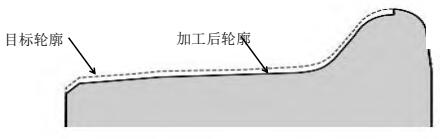
图 7 踏面轮廓错误,直径过小示意图
4.6 加工后踏面轮廓错误,直径过大
如图 8 所示,加工后踏面直径过大,车轮踏面、倒角及轮缘外侧面 X 方向上高于轮缘顶点到轮缘内侧面,轮缘顶端出现台阶。出现这种情况说明 T2 刀的切削量正常,T1 刀在车轮踏面、倒角及轮缘外侧面 X 方向的切削深度不足,致使在 T1 刀与 T2 刀的交接处产生台阶。针对这种情况需要减
小 T1 刀 X 方向的刀具补偿,从而满足切削精度的要求。
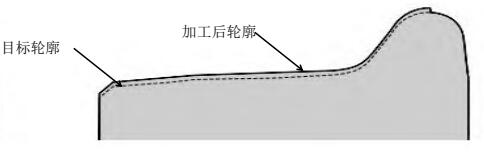
图 8 踏面轮廓错误,直径过大示意图
4.7 加工后踏面轮廓错误,踏面轮缘厚度过宽
如图 9 所示,加工后踏面轮缘厚度过宽,轮对 QR 值低于 7。这种情况说明 T2 刀的切削量正常,T1 刀在车轮踏面、倒角及轮缘外侧面 Z 方向的切削深度不足,致使踏面轮缘厚度过宽,轮对 QR 值超限。针对这种情况需增加 T1 刀 Z 方向的刀具补偿,从而满足切削精度的要求。
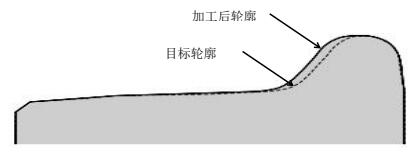
图 9 面轮缘厚度过宽示意图
4.8 加工后踏面轮廓错误,踏面轮缘厚度过窄
如图 10 所示,加工后踏面轮缘厚度过窄,轮对 QR 值高于 11。这种情况说明 T2 刀的切削量正常,T1 刀在车轮踏面、倒角及轮缘外侧面 Z 方向的切削深度过深,致使踏面轮缘厚度过窄,轮对QR 值超限。针对这种情况需减小 T1 刀 Z 方向的刀具补偿,从而满足切削精度的要求。
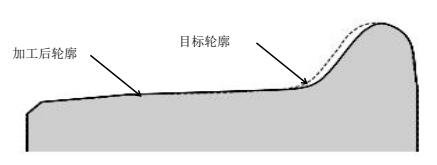
图 10 轮缘厚度过窄示意图
4.9 加工后踏面轮廓错误,轮缘内侧厚度过宽
如图 11 所示,加工后轮缘内侧厚度过宽,轮缘内侧与轮缘顶端之间过渡不圆滑。这种情况说明T1 刀的切削量正常,T2 刀在轮缘内侧面 Z 方向上的切削深度过小,致使轮缘内侧厚度过宽。针对这种情况需减少 T2 刀在 Z 方向的刀具补偿,从而满足切削精度的要求。

图 11 轮缘内侧厚度过宽示意图 图 12 轮缘内侧厚度过窄示意图
4.10 加工后踏面轮廓错误,轮缘内侧厚度过窄
如图 12 所示,加工后轮缘内侧厚度过窄,轮缘内侧与轮缘顶端之间过渡不圆滑。这种情况说明 T1 刀的切削量正常,T2 刀在轮缘内侧面 Z 方向上的切削深度过大,致使轮缘内侧厚度过窄。针对这种情况需增加 T2 刀在 Z 方向的刀具补偿,从而满足切削精度的要求。
5、总结
针对 TF2000 型数控不落轮镟床刀具补偿调整困难,依赖人员经验的问题,以加工后不同轮形结果为依据结合机床加工原理,总结出一套行使有效的刀具补偿调整方案。经实验优化后的刀具补偿调整方案可节约换刀可节时间 15 min。后续计划在此研究基础上,进一步深入研究刀具补偿量与切削次数、切削量的关系,以期制定出效率、精准度更高的刀具调整方案。
作者:王岩1 张淑敏 2
来源:石家庄市轨道交通集团有限责任公司 1 石家庄铁路职业技术学院 2
投稿箱:
如果您有机床行业、企业相关新闻稿件发表,或进行资讯合作,欢迎联系本网编辑部, 邮箱:skjcsc@vip.sina.com
如果您有机床行业、企业相关新闻稿件发表,或进行资讯合作,欢迎联系本网编辑部, 邮箱:skjcsc@vip.sina.com