摘 要 随着经济发展及科技水平的提高,硬岩掘进机、盾构机、反井钻机、巷道掘进机等机械在地下工程施工中得到了空前发展,机械破岩试验成为地下工程施工机械不可或缺的一个试验手段,以指导地下工程施工机械设计和施工。文章介绍了北京工业大学自主研制的机械破岩试验平台,该试验平台的设计制造综合考虑了高地应力、刀盘旋转和多个刀具同时破岩等工况,也考虑到不同破岩机械不同类型刀具破岩试验,还能在岩样箱中考虑到不同的岩体结构,可以真实模拟不同机械刀具的现场施工工况。试验平台由机械系统、液压系统、自动控制系统和数据采集系统组成。试验平台制作完成后,进行了多个不同工况的验证试验,达到了原定的设计要求。
关键词 机械破岩试验平台 高地应力 旋转 刀具 岩体结构
1 、引 言
21世纪是隧道及地下空间大发展的年代[1]。随着经济的发展及科技水平的提高,地下空间的开挖手段也越来越成熟和多样,如硬岩掘进机(TunnelBoring Machine)、盾构机(Shield Tunnelling Machine)、反井钻机(Raise Boring Bachine)、巷道掘进机(RoadHeader)等机械在地下工程施工中得到了广泛的应用。
施工机械的成功应用主要受以下四方面制约:地质条件、设备的选型与配置、机械运行参数和施工管理方案。其中地质条件是既定不变的,不受人为因素影响,但设备的选型与配置、机械运行参数的选择和施工管理系统的完善都是可控的。对机器进行合理地选型与设计并在施工中控制合适的运行参数是一大难题,且面临着许多的问题[2~5]。随着地下工程的蓬勃发展,机械破岩试验已成为地下工程施工机械不可或缺的一个手段,用以指导地下工程施工机械设计和施工。岩石线性切割试验可以较真实地模拟TBM滚刀破岩,在过去30多年中被广泛应用,可以通过此试验选择适合相应地质条件的 TBM,并预测机器运行参数和掘进速度,再通过实际工程中的实时反馈不断进行施工参数优化,最后根据TBM掘进情况对相应的施工管理方案进行完善,从而更高效地进行施工和管理。目前,国际上有三台线性试验机,分别在美国科罗拉多矿业学院、土耳其伊期坦布尔理工大学(Istanbul Techni cal University)和韩国施工技术研究所(Institute ofConstruction Technology in Korea)。
线性滚刀破岩试验最早由科罗拉多矿业学院提出并付诸实践,其试验机可以控制滚刀间距、贯入度等变量,并且岩石试样为大块原状岩样(1 100 mm× 800mm×600 mm),可以避免由尺寸效应带来的误差[6]。韩国施工技术研究所的线性试验机是基于科罗拉多矿业学院试验机而设计的,但在结构和试验操作上均有所改进,如试样盒、传感器等方面,而且在试验中还增加了新的测量技术,如利用摄影测量法和ShapeMetrix 3D三维评价软件对试验过程中产生的岩屑的体积进行准确的测量[7,8]。
土耳其伊期坦布尔理工大学的试验机与科罗拉多矿业学院试验机在功能上基本一样[9]。通过此试验机也解决了大量的机械设计与工程施工问题。上述三台线性试验机从本质上说没有太大差别,仅能用一把滚刀、刮刀或刀齿进行线性破岩试验,且受其框架刚度限制,当滚刀力过大时,存在侵入深度测不准的问题。另外,美国及土耳其的试验机还存在岩样固定较为麻烦的问题,韩国的试验机吸取了前二台试验机的经验,对岩样箱作了改进,使之得到很好的解决。
由于国内岩石隧道掘进机开挖案例越来越多,对机械破岩试验机及其试验也更加重视,最近已有两台试验机研制成功。其中一台为盾构及掘进技术国家重点实验室拥有,该试验机是回转式滚刀破岩机,其可放最大试样直径为 2 000 mm,厚度为 300mm,可以安装 1~3 个刀座,以及直径为 19 英寸(483 mm)的盘形滚刀。其加载方式为轴向主动力加载,最大荷载可达1 000 kN。该试验机安装了声发射传感器,可进行岩样破裂声学全频谱监测[10]。中南大学的试验机也属于回转式试验机。该试验机的加载方式为主动加载方式,最大推力为1 000kN,刀盘上最多可以安装六把刀具,其刀具包括滚刀和切刀两种,滚刀直径为 8.5 英寸(216 mm)。
通过三向力传感器可以实时监测破岩荷载[11]。
国内的两台试验机均为旋转试样方式破岩,岩样均为圆盘形,岩样不易切割成形,安装不易。另外,滚刀加载方式均为主动加载,在试验过程中需获得侵入深度和作用力两个参数。中南大学试验台滚刀及其它尺寸采用 1∶2 缩小比进行设计,不是足尺试验。
随着经济的发展,基础设施的建设,如水利、铁路、公路隧道工程向着更长、更深发展,各种开挖机械大量运用到地下工程建设中。如已经建成的秦岭铁路TBM隧道[12]、锦屏二级水电站引水隧洞[3]、正在规划的南水北调西线工程隧洞[13、列奇堡高速铁路隧道[14]、圣哥达高速铁路隧道[15]等,其埋深都超过1 500 m,地应力对掘进机开挖的影响非常显巨,包括开挖速度及滚刀的异常磨损等。简单的滚刀线性破岩试验或转动破岩试验已无法满足多种工况、多种开挖工具的模拟。由北京工业大学自主研制的机械破岩试验平台吸取了已有试验机的优点,强化了其原有试验能力,增加了多种复杂工况的模拟功能。
2 、试验平台设计思路及关键参数确定
机械破岩试验平台考虑的施工机械包括掘进机、反井钻机、铰孔钻机、盾构机、巷道掘进机等施工机械的施工。它需要模拟施工的刀具有单刃滚刀、双刃滚刀、镶齿滚刀、刮刀及不同类型齿刀的破岩过程。它需要模拟的地质条件有不同类型的岩石或岩体结构、地应力。由于需要考虑以上因素及其组合对机械破岩的影响,其设计的关键因素包括试验组合的最大推力、最大扭矩、最大地应力、岩石或岩体试验箱的大小、实现线性和旋转破岩功能。
本机械破岩试验平台设定的独立变量有:试样的岩石类型或岩体结构类型、地应力大小、刀具切割方式、刀具贯入度。需测定的参数包括:刀具三向作用力、切割系数、比能、岩石碎屑分布及形状。常变量有刀具切割间距、切割顺序、切割速度。
2.1 试样尺寸参数
试样的尺寸决定试样箱的尺寸,试样箱的大小也基本上决定了纵向平移小车、横向平移小车的长度和宽度,进而决定了底部框架的长度和宽度,所以试样的尺寸选择对整个机械破岩试验平台的尺寸设计至关重要。在试样尺寸的选择上,最主要的考虑是试样尺寸对破岩试验结果的影响。
Cho(2010)用三维动态压裂方法对滚刀破岩进行数值模拟,研究了试样尺寸对滚刀破岩试验中比能的影响[7,8],并得出试样的尺寸只要能满足长度100 mm、宽度 100 mm、高度 30 mm 即可。Gong 等(2006)应用UDEC计算了节理对滚刀破岩的影响,滚刀破岩产生的竖向裂纹能直接到达节理间距为200mm 的节理面,而节理间距达到 500 mm 时,节理对滚刀破岩影响不大[18]。因此,为了观察试验时产生的竖向裂缝的扩展情况及影响区域,模拟不同节理间距对破岩的影响,试样的高度最少要取500 mm。在实际的试验过程中,不可能只对试样进行一次切割,而是需要在不同的刀间距和贯入度组合下对试样进行多次切割破岩试验,而且为了消除端部效应,切割时要在边缘预留一定的空间,最靠边上的切槽数据也是要排除的。所以实际试验中选取试样的尺寸会远远大于上面所说的尺寸。另外,从试验的经济性和操作性上考虑,也要求尽可能地用一块试样做尽量多的试验。从国外已做过的线性试验看:其所采用的试样一般长度在 1 000 mm 左右,宽度在700 mm左右,厚度则在300~500 mm之间,故在本试验平台的设计中,以此值为参考,确定试样的最大尺寸为1 000 mm×1 000 mm×600 mm。
2.2 推力参数
试验时作用于刀具上的三向力(尤其是竖向力)的大小决定了机械破岩试验平台整体框架的设计刚度,直接影响到框架材料及参数选取,同时也决定了三向传感器、导轨及滑块等的选取。
在地下工程掘进机械中,TBM 所需推力较大,故以TBM 为标准设计试验机最大推力。TBM 破岩是利用刀具对岩石的压入,形成压碎区,在滚刀之间出现拉破坏而产生岩片。刀具推力的大小与岩石的抗压强度有极大的关系。目前 TBM 已有在岩石单轴抗压强度达到 420 MPa 的硬岩中成功施工的案例。对盘形滚刀来说,现在正在向着越来越大的直径发展,其可承受的荷载也越来越高[16]。目前已经推出有 21 英寸的盘形滚刀,它将能承受更高的荷载。
由Gertsch[6]等(2007)在线性试验机上用直径17英寸的常截面滚刀对单轴抗压强度为158 MPa的花岗岩进行破岩试验,以及Jung-Woo Cho[7,8]等(2013)在线性试验机上用直径17英寸的常截面滚刀对单轴抗压强度为209 MPa的花岗岩进行破岩试验所得出的试验数据可以看出,滚刀最大竖向力与平均竖向力之比约为 2。掘进机的滚刀受力设计为平均力,其破岩时力的瞬时波动可能达到2倍左右。在本机械破岩试验平台的设计中,考虑了两把刀具同时破岩的工况,还要为以后使用更大的刀具、三把以上的刀具同时作用留下空间,还考虑施加围压后,刀具破岩推力会更大,并考虑有一定的安全储备,故此试验平台的设计推力为2 000 kN,使其具有足够的刚度。
2.3 围压参数
试验平台的围压系统是为了模拟地应力工况,试验时施加的围压大小取决于实际工程中的地应力。试验中由推力油缸对试样施加围压,故对试样所加围压的大小一方面决定了推力油缸液压系统参数的选取;另一方面,试验时承受推力油缸反作用力的是围压试样盒,所以初始应力的大小也决定了试样盒的设计强度和刚度。
高地应力是一个相对的概念,中科院孙广忠教授(1993)[17]就曾指出,强烈构造作用地区,地应力与岩体强度有关;轻缓构造作用地区,岩体内储存的地应力大小与岩石弹性模量直接有关,即弹性模量大的岩体内地应力高,弹性模量小的岩体内地应力低。
目前,应用地应力值与岩石或岩体强度之比来判断地应力状态的划分方法得到较多数人的认可。工程实践中大多将大于20 MPa的硬质岩体内的初始应力称为高地应力。考虑到本试验平台将来要用于模拟高地应力区的TBM施工,在设计中按照这样的标准对围压油缸进行设计:当试样盒中放入的试样尺寸为1 000 mm×1 000 mm×600 mm时,液压油缸可以对其施加20 MPa的围压。这样,当减小试样尺寸时,则可对其施更高的围压。
2.4 线性破岩与旋转破岩功能
线性破岩是最简单有效的试验破岩方式,已经广泛用于地下工程施工机械破岩等领域的研究。它可以近似模拟实际工程中刀具以较大半径旋转破岩的情况。但是当旋转破岩半径较小时,线性试验就无法真实地模拟其破岩情况。本机械破岩试验平台保留了传统线性试验机的所有功能,并增加了旋转破岩这一更加符合实际工况的功能。
旋转破岩与直线破岩到底有多大差异,尤其对于镶齿滚刀来讲可能差异性更大,但由于之前的试验设备没有此项能力,没有对此进行深入研究。为了更加真实地模拟一些地下掘进机械的旋转掘进方式,此试验平台实现了这一功能。要在同一平台上实现直线与旋转破岩功能,这也是本试验平台的一个难点。最终通过在同一平台上,设计一个旋转试样台来解决这一问题。旋转试样台主要包括旋转试样盒及与其配套的机械装置和液压系统。试验时由液压系统带动试样盒进行旋转,使作用在试样上方的刀具以圆周运动的方式对其进行切割破岩,以模拟机械施工过程中刀盘上刀具的旋转切割破岩过程。
3 、机械破岩平台的组成
机械破岩平台破岩方式设计有卧式和立式两种。卧式破岩是破岩刀具与岩石试样水平布置,破岩工作面(或称之为掌子面)处于竖直平面。这样可以更加真实地模拟掘进机械破岩状况,在重力作用下,岩屑产生后可以自由掉落,便于搜集岩屑。但是此方式给岩石的吊装及固定带来极大困难,且由于岩石较重,试样箱的旋转以及支撑较为困难,所以只能刀具旋转;但是由于水平方向加载力过大给机械机构设计带来一定的困难,并使其占地面积成倍增加。而立式结构和驱动相对简单,由于机器主要受力方向转换为竖向,机器底部与地梁连成一体,所以只需考虑机器上部的刚度,节省了材料,岩样箱、刀具及刀座更换或调整简单方便,控制量测装置布设更加容易,占地面积较小,且实验完毕后可以查看岩屑在掌子面的分布情况。从节约成本和实现其基本功能的角度出发,选择立式破岩方式的设计方案,如图1所示。
图1 机械破岩试验平台的几何模型
3.1 机械系统
机械系统是试验平台的主体,构成了试验平台的外形,同时也是液压系统的载体。机械部分主要包括一个大型的钢结构框架、移动平车、移动滑轨组件、调模机构(图2)、刀架组件、直线导轨和试样盒(图3,图4)。调模机构的设计比较独特,它是在注塑机调模装置的基础上稍加改造而成,通过大齿轮带动四个小齿轮转动,并与四根导向杆上的螺纹咬合,可以使模板精确地上下移动,达到预定坐标后锁死,从而可以精确设定刀具的竖向切入深度。图3、图4显示了两个岩样箱差异,一个可以加围压,一个可以转动;试样都是块状的,易于切割成形,易于按装到试样箱中。平移试样靠液压方式固定,旋转试样靠机械方式固定。
3.2 液压系统
液压系统是整个试验平台的动力系统,提供验时所需要的动力和压力,系统主要包括液压站、液压油缸及配套的软管试验中按指令完成一系列的动作。
图2 调模机构
图3 围压试样盒
图4 旋转试样盒及旋转装置
机械破岩试验平台的液压系统是通过四组油缸和液压马达完成四个基本动作:控制移动平车的横向及纵向位移;控制围压试样盒中对试样施加的围压;控制旋转试样盒的转动及转速。液压系统的主要参数见表1。
表1 液压系统的主要参数
3.3 自动控制系统
试验平台的自动控制系统采用西门子 PLC 系统,主要由流量控制、加载控制、位移控制、温度及液面控制系统组成。
控制系统集成在控制台上,具有可视化的人机界面,如图5所示。试验时可以在人机界面中直接设定各种试验流程、加载压力、加载流量、加载时间等,可以直接输入预设的试样盒及刀具的位移坐标,控制其达到预设位移。试样盒位移精度达到1 mm,刀具位移精度达到 0.1 mm。人机界面在试验过程中会给予操作者各类提示,以防在操作过程中出错。它能够显示刀具瞬时力、三向力随时间变化曲线、试样箱“X”、“Y”(前后左右)方向位移曲线、岩石及刀具位移坐标、油液位状态、各手动油阀的开关状态、辅泵的运转状态、各电磁阀的通电状态并可在油温超高或超低、油路堵塞时报警。其上还有一些控制按钮,如控制旋转试样盒旋转方向的“旋转顺”、“旋转逆”按钮,其旋转速度可以设定为0~8 rpm,以及用于岩石试样装卸的“手动按钮”以及泵站的启停按钮等。
图5 控制面板
另外,控制系统有自动与手动两种测试方式:当采用自动方式时,试验员操纵泵站,计算机发出测试指令,控制相应的元件,自动完成测试及记录,并打印出试验报表和试验曲线;手动测试时则由人工测试及记录。系统加载压力比例控制亦可以采用手动调节和计算机控制调节两种方式进行控制。
3.4 数据采集系统
试验平台的数据采集系统硬件由工控机(计算机)、传感器、信号调理装置及输入-输出接口组成,在试验过程中重点需要监控并准确采集以下参数:
(1)作用于刀具上的三个方向的力。此力为被动力,由刀具上方固定的三轴向负载传感器进行测量,是本试验中最为重要的参数;
(2)横向推力油缸推动横向移动平车时,平车的位移;
(3)纵向推力油缸恒速或恒压推动纵向移动平车时,平车的位移和速度;
(4)旋转试验盒中液压马达的扭矩和转速;
(5)当用围压试验装置进行试验时,围压试验装置中液压油缸的压力;
(6)调模机构的竖向位移。
另外还有一些参数并不是数据采集系统能够采集到的,如试验时刀具切割下的岩屑的体积、块度及破碎角等,这些参数则需要试验人员在试验过程中或试验结束后测量或者计算获得。
最终的机械破岩试验平台整体效果如图 6 所示。
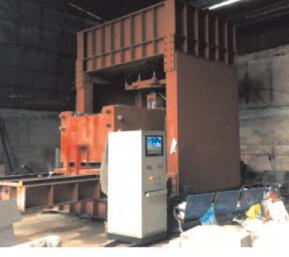
图6 机械破岩试验平台整体效果
4 、试验机能力验证
4.1 常规线性破岩试验
本试验为盘形滚刀破岩试验,所用滚刀直径为17 英寸(432 mm),设定刀间距为 80 mm,侵入深度1 mm,岩石试样为甘肃北山花岗岩,单轴抗压强度为105.6 MPa,试样尺寸为1 000 mm×1 000 mm×600 mm;所用试样箱为围压试样箱,其中围压设为0.5 MPa,用于固定岩石;三向力传感器数据采集频率选择为100次/s。
试验时,三向力传感器采集的力为瞬时波动力。图 7 为盘形滚刀以贯入度 1 mm、刀间距为 80mm 切割岩石时的累计破岩效果图,滚刀三向力随时间变化如图8、图9所示,其法向力、滚动力及侧向力的波动变化很好地反映了岩片的产生规律,大岩片的产生就是侧向力的变化点。其平均法向力为126.2 kN,平均滚动力为4.1 kN。
图7 盘形滚刀线性破岩效果
图8 盘形滚刀法向力和时间关系曲线
图9 盘形滚刀滚动力、侧向力和时间关系曲线
4.2 围压条件下滚刀破岩试验
围压试验的其它条件与常规线性试验相同,岩石试样尺寸为1 000 mm×1 000 mm×600 mm。设定围压大小X方向P=10 MPa,Y方向P=15 MPa。滚刀直径为 17 英寸(432 mm),设定刀间距为 80 mm,侵入深度1 mm。图10为盘形滚刀在设定围压条件下切割岩石时的破岩效果,岩面更为平整。三向力随时间变化曲线如图11、图12所示,其平均法向力为182.2 kN,平均滚动力5.2 kN,其法向力的变化幅度比没有围压时要小,但其平均法向力受到围压作用而增大,反映了围压效应。
图10 围压条件下盘形滚刀线性破岩效果图
图11 盘形滚刀法向力和时间关系曲线
4.3 旋转破岩试验
在试验平台上实现了镶齿滚刀破岩试验,所用镶齿滚刀直径为12英寸(304.8 mm),试验中贯入度为1mm,旋转半径为310 mm。岩石试样尺寸为1 000 mm×1 000 mm×600 mm,为北山花岗岩。所用试样箱为旋转试样箱。将滚刀以固定的贯入度直线切入岩石,待岩石旋转中心与滚刀相对公转中心对准时,开始旋转破岩。在试验中记录镶齿滚刀三向力并计算其比能。针对该岩石试样分析了贯入度对法向力、滚动力和比能的影响,以及对比分析未处理岩面和已处理岩面的破岩力和破岩效果。
图12 盘形滚刀滚动力、侧向力与时间关系曲线
图13为镶齿滚刀破岩效果图,镶齿滚刀破岩形成的岩片比较小,岩粉较多。镶齿滚刀三向力随时间变化如图14、图15所示,镶齿滚刀的法向力波动很小,滚动力、侧向力随着岩片的产生而波动,平均滚动力为5.3 kN,但其侧向力由于破岩面为锥形面不能相互抵消,为一个方向的力,这与盘形滚刀破岩是不同的。
图13 镶齿滚刀破岩效果
通过以上试验数据可知,滚刀破岩时滚刀三向力是一种波动力,并在一定范围内波动。镶齿滚刀力的波动范围相对于盘形滚刀较小,这和其破岩机理有密切关系。常规线性破岩试验盘形滚刀三向力均比围压工况下盘形滚刀三向力小。这反映了当地应力较大时,盘形滚刀侵入相同的深度,其所需盘形滚刀三向力较大。
通过常规线性破岩试验、围压破岩试验以及旋转方式破岩试验,得到了一些刀具破岩的重要数据,以及在工地难以看到的破岩现象,验证了该机械破岩平台各项功能的可靠性与实用性。它成为目前完成工况最多、实用性最强、模拟实际工程最接近真实的机械破岩平台。
图14 镶齿滚刀法向力和时间关系曲线
图15 镶齿滚刀滚动力、侧向力与时间关系曲线
5 、结 论
通过对已有机械破岩试验平台的调研与功能分析,综合目前隧道机械开挖的工况,在原有线性滚刀破岩试验机的基础上,增加了大尺寸多滚刀破岩功能、围压功能、旋转破岩功能。试验平台的承载能力、试验的刀具类型、破岩工况得到大幅度的提高。岩样箱的设计考虑到了岩体的结构及滚刀破岩裂纹扩展规律对试样的要求,并考虑到试样装卸的方
便。试验平台由机械系统、液压系统、自动控制系统及数据采集系统组成。试验平台研制完成后,进行了线性切割试验、围压条件下线性切割试验、镶齿滚刀旋转破岩试验,获得了可靠的数据和实验现象,验证了机械破岩试验平台的各项功能。
目前该平台的试验能力、试验工况、自动控制与测量水平均优于国内外同类型破岩试验机,成为全球第一台新型的多功能试验平台。由于它可以真实全面模拟破岩机械刀具的现场施工状况,故用之研究刀具破岩机理,可以准确有效地指导实际工程中破岩机械的选型、设计、优化施工参数及进行掘进施工预测,为地下工程机械开挖服务。
如果您有机床行业、企业相关新闻稿件发表,或进行资讯合作,欢迎联系本网编辑部, 邮箱:skjcsc@vip.sina.com