通过刀具主轴的精细运动实现高精度切削
2024-5-31 来源:- 作者:吉冈隼人
【摘要】近年来,随着产品水平的提高,对加工精度的要求也越来越严格。另外,还希望实现具有微细结构功能表面的三维曲面等更复杂的形状加工。在本研究中,为了提高铣削加工的水平,通过使刀具主轴在XY和Z轴方向微动,来减少振动误差并实现精细图案加工。具体介绍如下:在主轴头设置小型振动单元,通过反馈测量的振动信号,抑制XY平面内的误差;以及在主轴上嵌入超磁致伸缩元件,利用外部磁场进行微小定位的结构。
近年来,为了实现高附加价值的产品和器件,各产业领域对三维复杂形状的加工要求不断增加。特别是通过表面具有微细图案而表现出特殊功能的功能表面早已为人所知,被称为Bio Inspired Manufacturing(仿生制造)的生物模仿制造备受关注1)。预计未来将需要在加工三维形状的同时在其表面加工出精细图案的技术。
在表面上形成微结构的MEMS加工技术的应用正在广泛普及,很多领域都已经得到了应用。通过应用MEMS加工技术,加工单位更小,加工更精细,从而实现更高效的形状制造。但是MEMS加工技术在大多数情况下也存在应用上的限制,如受加工对象材料限制,难以适用于任意曲面形状等。另一方面,由于传统的机械加工是物理性加工,所以具有可对广泛的材料进行加工,还可制造沟槽、台阶以及三维曲面等形状的特点。在对无数细微形状的加工中,我们需要让机器按照其形状移动,这需要大量的加工时间。
本文以实现机械加工,特别是使用立铣刀铣削加工的高精度和高功能化为目标,介绍了我们研究小组正在研究的通过使刀具主轴微小位移来提高设备加工水平的相关内容。
一、 机械加工的高精度化与微驱动
1.去除加工中的母性原理
机械加工包括利用材料变形的塑性加工,去除材料的切削加工、磨削加工以及研磨加工等多种类型。本文以切削加工,特别是使用立铣刀加工,——即高精度铣削加工为对象。
如图1所示,铣削加工是利用主轴使多刃刀具高速旋转,对工件进行三维相对运动,从而削去不需要的部分,创造出所需加工形状的加工方法。因此,通过刀具主轴与工件的相对运动,可以加工出任意形状,而且与MEMS加工技术相比,可以高效地去除材料。但是,由于是通过刀具进行材料去除,两者之间的相对运动会直接反映到加工形状上,因此,当刀具或工件的任何一个运动有误差时,就会产生加工误差。也就是说,以位移为基准进行切削加工时,由于机床的运动精度会被反映到加工对象上,所以要求机器在短期和长期的时间内,保持稳定的高精度运动。这在机械加工中被称为母性原理(Copying principle),将机床和加工零件的关系比喻为亲子遗传关系。因此,在铣削加工中,用于旋转立铣刀的主轴以数千至数万转高速旋转,为了实现高精度加工,即使在这种状态下,也有必要将回转跳动和振动等降低到极限。反过来考虑,如果能够高速、高精度地控制刀具与工件的相对位移,就有可能实现高质量的切削加工。
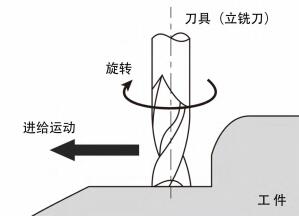
图 1 使用立铣刀进行铣削
2.主轴的旋转误差和微小驱动
机床中主轴的旋转精度是由旋转轴加工精度、所使用的轴承精度、驱动电机的转矩不稳定、装配精度、轴承润滑状态等多种因素的综合影响而决定的。因此,无论在机械设计、装配工艺以及加工过程中如何考虑条件,都很难完全抑制旋转中的误差。因此,为了实现更高的精度,在考虑上述问题的基础上,还需要对加工过程中发生的旋转引起的误差进行测量,并通过实时进行某种反馈控制来降低误差。
对于这种正在加工中的主轴,为了降低误差而进行反馈的尝试已经有很多报告。最具代表性的例子是,支撑主轴的轴承不使用一般的滚动轴承,而是采用磁轴承,通过电磁力进行非接触支撑,在抑制旋转时的摩擦和振动的同时,通过控制电磁力来实现高精度旋转。根据反馈控制系统的构成,各种特性的实现和改变都很容易,还存在与滚动轴承组合2)和与空气静压轴承组合。但由于旋转的主轴采用非接触支承,在刚性方面是不利的,因此在进行一般机械加工的加工中心等方面的应用受到限制。
二、在XY平面内主轴的微驱动
主轴旋转中的误差,如果主轴中心轴为Z轴,则有XY平面内(主轴半径方向)和Z轴方向(主轴中心轴方向)的分量。这里,着眼于XY平面内,轴方向将在第三部分中叙述。
1.旋转同步跳动和旋转异步跳动
主轴旋转过程中的误差分为旋转角度具有可重复性的周期性跳动误差(旋转同步误差,Repeatable Run-Out,以下简称RRO)和与旋转角度无关的非周期性跳动误差(Non-Repeatable Run-Out,以下简称NRRO)。利萨如图形如图2所示。例如,如果主轴存在相对于旋转的不平衡量,则会导致旋转过程中的跳动,这对应于旋转同步跳动,由于相对于旋转角度具有可重复性,所以低速旋转时,可以通过直线轴的定位进行补偿。另一方面,NRRO是旋转异步跳动,没有可重复性,补偿困难。典型的NRRO成分有滚动轴承的滚动体公转周期、保持器的平衡等。另外,虽然数值大小本身RRO>NRRO,但难以预测和补偿的NRRO无法抑制对加工表面的影响。因此,本研究以NRRO为对象。
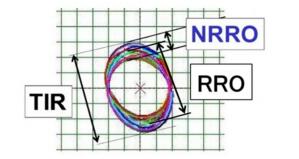
图 2 Lissajous 图形中的 RRO 和 NRRO
2. 微驱动原理及系统结构
由于伴随主轴旋转的NRRO很难事先正确预测,因此要进行实时反馈控制。图3是该系统的结构。
以市场上销售的精密加工中心为基础增加了加振系统。由于以数万转的速度旋转的主轴本身很难按照误差进行微驱动,因此在本研究中,将具有由螺旋马达驱动的板弹簧支撑质量的单元固定在主轴头部,通过调整传感器测量的误差信号的增益及相位,将误差信号反馈到马达电流中,利用质量驱动产生的反作用力对主轴头进行振动,从而进行补偿。
采用这种方式,主轴的NRRO本身没有受到抑制,但如前所述,切削加工中,刀具和工件的相对位移非常重要,因此通过连同主轴头一起进行微小位移来抑制工件或搭载工件的工作台的位移误差。
系统通过测量刀具相对于主轴头的相对位移(①)和主轴头的振动加速度(②),通过带通滤波器提取NRRO成分,调整增益和相位来进行振动反馈。另外,作为评价对象,还同时测量了装载工件的工作台到刀具的相对位移(③)。作为对主轴施加振动力的类似研究,也有在异常加工状态下的微细加工时减小振幅等例子,但与这些相比,本研究的目标在于普通加工时进一步提高精度。
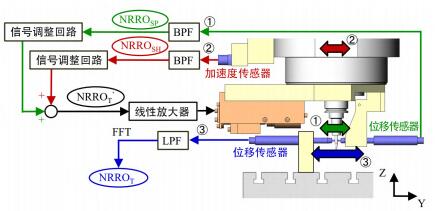
图3 基于振动的误差抑制系统的结构
3.精密加工试验的评价
为了评价所构建的系统特性,通过使用立铣刀的精密加工试验,对系统特性及加工表面进行了评价。在试验中,为了忽略RRO的影响,采用单刃金刚石立铣刀进行加工,根据反馈的有无,对NRRO成分的降低率进行了评价。图4显示了其结果。如果只使用主轴的异步振动分量(NRROSP)和主轴头的异步振动分量(NRROSH)中的任意一个作为反馈信号,有时降低效果不理想,或者相反NRRO也可能增大。另一方面,将两者合起来进行反馈时,可以确认在30,000及40,000 r/min的任何转速下均有较高的降低效果。
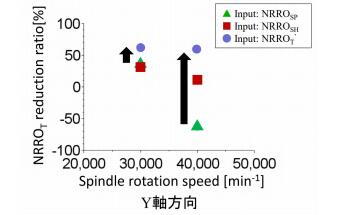
图 4 y轴方向上NRRO的减小效果
图5显示了通过非接触表面形状测量系统对实际切削的加工表面进行评价的结果。由于使用的是半径约1mm的单刃金刚石立铣刀,表面上球体的一部分凹陷应该是均匀排列的,与不加振动相比,在有加振动的情况下,可以确认深度方向的偏差减小了。综上所述,通过对加工表面的评价,确认了通过对主轴头进行反馈激振,可以降低NRRO的影响。
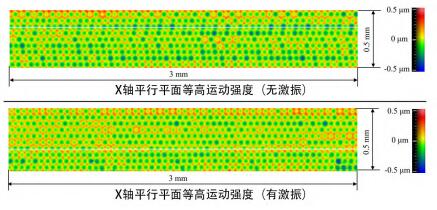
图5 基于加工面的特征测量的评价
三、 主轴轴方向的微驱动
1. 轴向的微小位移控制与概念
一般来说,机床主轴为了实现高刚性,都采用重型和大型结构,为了配合加工面上无数的微细结构,整个主轴都要进行微细驱动,导致加工速度下降,效率非常低。为了在切削加工中实现精细结构加工,必须使高速旋转的立铣刀在XY平面以外的旋转轴方向上发生微小位移。为了配合微细结构实现高响应驱动,最大限度地减小驱动质量是很重要的。也就是说,不是驱动整个主轴结构,而是包括际进行切削加工的立铣刀在内,驱动质量必须变小。这与精细定位机构中的粗微动定位机构类似。
2. 驱动原理和系统结构
在本研究中,如图6所示,在刀具支承部内部嵌入了致动器,仅局部驱动前端部分,从而使驱动的惯性质量最小化。在切削刀具不旋转的车削加工中,压电材料作为小冲程、高响应的致动器之一,早在20世纪80年代就有相关报告。但是,像铣削加工那样,为了给加工中高速旋转的主轴供电而进行配线,在技术上还存在很多问题。因此,本研究采用了用超磁致伸缩材料代替压电材料的设计。超磁致伸缩材料是一种因施加外部磁场而产生形变的功能性材料,通过合理设计的磁路,将设置在非旋转部分的励磁线圈所产生的磁场进行感应,可以非接触地施加到旋转的元件上。
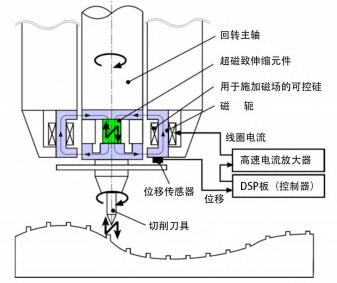
图6 对带有超磁致伸缩元件的旋转刀具的局部驱动
利用将这种超磁致伸缩材料作为致动器嵌入的主轴系统,构建了三维加工系统。图7显示了系统的整体结构。具有卧式三轴机床的结构,采用空气静压主轴水平布局,Z轴及X轴采用直线电机驱动,垂直方向的Y轴采用滚珠丝杠驱动。通过对超磁致伸缩元件施加磁场,与每个轴上的定位同步,仅在轴向上驱动刀具部分,为了提高非线性较强的超磁致伸缩元件的定位精度,嵌入环形电容位移计提供反馈控制。通过组合该刀具的轴方向微动和XYZ轴运动,通过将刀具的轴向精细运动与XYZ轴的运动相结合,可同时高效地创造三维形状和表面结构。
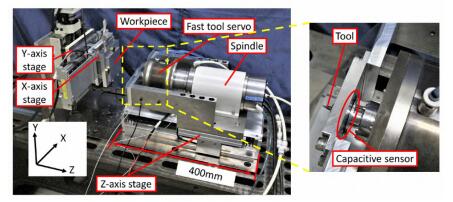
图7 构建的3D加工系统
为100 μm/s,工件材料为无氧铜。图9显示了用形状测量机测量加工后的截面的结果。当切削深度从3~0.1μm改变时,可以确认无论在哪个台阶上,加工的误差都低于目标0.05 μm。当加工台阶小于0.2 μm时,台阶形状变得模糊,这可能是由于轴向定位分辨率及进给轴的直线度问题等原因造成的。因此,加工分辨率被认为可达0.2 μm左右。
此外,通过将进给轴的运动和刀具轴方向的精细运动相结合,同时加工曲面形状和表面结构的示例如图10所示。在如图所示的加工中,利用XYZ的进给轴在球面上沿凹陷形状的轨迹运动,与该运动同步在刀具轴方向上施加微小切削量,从而在表面加工出长方形孔形凹坑形状。刀具旋转速度为15000r/ min,进给速度为5mm /s,凹坑深度为5 μm。如图所示,从加工的测量结果可以看出,加工几乎是按照指令值进行的。另外,总共加工了26个凹坑,平均深度为4.95 μm,可以确认实现了标准偏差为0.14 μm的高精度加工。
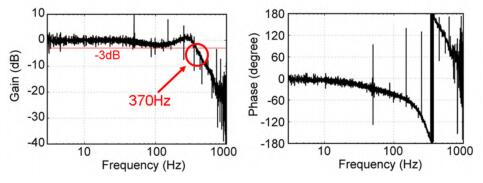
图8 刀具伺服系统的波特图
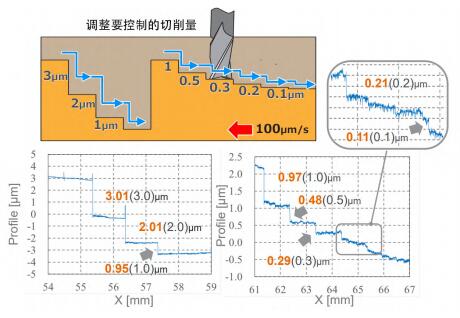
图9 微切削加工的评价
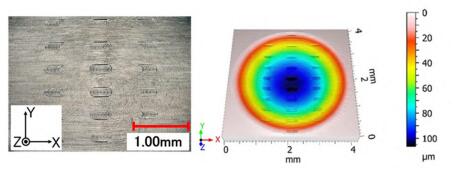
图10 同时创建曲面形状和曲面凹坑的示例
四、 结论
本文的研究是为了提高精密铣削加工的精度和质量,通过在刀具主轴上实现各个轴方向的微动功能,实现了高精度加工和精细加工。具体来说,通过将加振单元的驱动反作用力作用于主轴头上,可以减少NRRO对主轴的影响,通过在旋转主轴中嵌入了由超磁致伸缩元件组成的非接触式微动机构,并在加工过程中与进给轴的运动同步,实现了同时高效进行形状加工和纹理加工的系统。此次嵌入主轴的超磁致伸缩元件是一种功能性材料,具有与压电元件相似的特性。正如压电元件不仅可以用作致动器,还可以用作传感器一样,超磁致伸缩元件在受到外力时也会改变其磁导率。值得一提的是,此次开发的基于超磁致伸缩元件的微动机构还具有用作加工状态监测传感器的潜力,有望得到进一步发展。希望通过该系统实现接触检测功能、加工力监测功能以及位移控制和振动附加功能等在精密加工中有用的功能。
投稿箱:
如果您有机床行业、企业相关新闻稿件发表,或进行资讯合作,欢迎联系本网编辑部, 邮箱:skjcsc@vip.sina.com
如果您有机床行业、企业相关新闻稿件发表,或进行资讯合作,欢迎联系本网编辑部, 邮箱:skjcsc@vip.sina.com
更多相关信息