核电冷却泵泵体五轴数控加工工艺研究
2021-1-13 来源: 云南机电职业技术学院校企合作办公室实训 作者:孙建明,黄晓明,朱兰,杨晓春,刘春美
摘要: 核电冷却泵泵体是主回路系统中三大核心部件之一,泵体的制造加工精度对整体设备的运行安全有直接影响。为提高泵体的加工精度,提出用五轴数控加工工艺加工泵体。分析泵体特征,应用尺寸中差建模,并设计专用夹具。基于遗传算法,研究加工工艺及方法,应用五轴联动数控加工中心完成核电冷却泵泵体加工。解决了圆柱倒扣面、90°弯管管道、薄壁件等加工难题。
关键词: 核电冷却泵; 夹具设计; 中差建模; 五轴联动
0 、前言
核电冷却泵泵体是主回路系统中三大核心部件之一,也是核岛中的一级安全部件。泵在主回路系统中所起的作用相当于人体内的心脏,泵体负责将主回路的冷却剂完成热循环,在反应堆输出功率之前加热反应堆装置。泵体内部管道必须衔接光顺,以保证冷却剂高效完成热循环。
泵体的制造加工精度直接影响整个设备的运行安全。传统的铸造技术很难满足核电冷却泵泵体的使用功能要求,五轴数控加工技术在提高泵体内部管道表面质量及精度方面具有很大的优势。五轴加工的主要优势:
( 1) 通过调整刀轴矢量避免刀具、主轴与工件及工装发生碰撞干涉; ( 2) 刀具相对于加工工件的位置可以灵活调整,保证刀具切削时处于最佳姿态,有效提高工件的表面质量。因此,五轴数控加工技术主要应用在航空、航天、水利水电、船舶、军工等领域的核心产品制造。
1 、泵体分析
泵体工程图如图 1 所示,泵体主要由泵心、90°弯管、支撑体组成。泵心呈 R150 mm 倒扣面,管道壁厚为 5 mm,并且要求管道内壁衔接光顺、无明显接痕,管道外壁 R4 倒角面光顺。
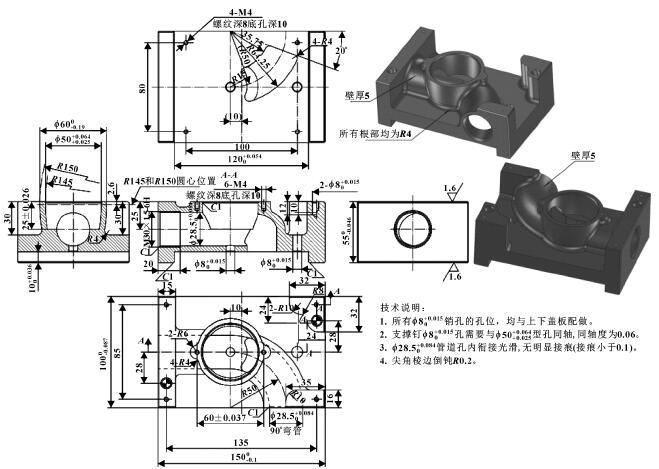
图 1 核电冷却泵泵体工程图
加工难点:( 1) R150 圆柱倒扣面,加工时需合理调整刀轴的角度及刀具切削姿态,才能保证加工完成的倒扣曲面表面质量及精度符合设计要求。( 2) 管道壁厚仅为 5 mm,要求设计合理的加工工艺方案,保证薄壁加工不变形。( 3) 90°弯管内壁要求衔接光顺,内外壁曲面呈均匀壁厚管道状,应用 3+2 轴、4+1 轴任意摆动刀轴均无法满足弯管内壁衔接光顺的设计要求,必须应用五轴五联动加工工艺技术才能满足加工设计要求。
2 、中差建模
按照设计人员的习惯建模方式,建模时都以对零尺寸建模,至于实际加工精度是否能够满足设计图纸要求,主要取决于操作机床的工人能否依经验调整刀具半径补偿值。随着现代技术不断发展,机床生产厂家生产的数控机床定位精度已达到 0. 02 ~ 0. 05 mm级,发达国家生产的机床定位精度能够达到 0. 005mm 级,机床控制系统也越来越先进。通过控制系统的补偿,在刀具未磨损的情况下加工出来的产品都能够达到图纸要求。
编程工程师只需严格按照中差建模及编程,机床运行加工一次,零件尺寸就能达到图纸要求。
例如文中冷却泵泵体尺寸 60+0-0. 19,如果建模时不计算尺寸中差,还是按对零尺寸建模,加工完成的零件尺寸偏大,操作机床的工人需反复修改刀具半径补偿值并运行机床再加工,直到零件尺寸符合图纸要求为止,这种做法费时费力耗能,并且容易出错。故中差建模是保证产品零件尺寸精度的关键。

3 、夹具设计
五轴联动加工时,工作台 A、C 轴都要转动,当A 轴摆动角度大于等于 90° 时,工作台与主轴容易发生碰撞。为了避免此类事故发生,工件装夹时应抬高装夹位置,需要设计五轴专用夹具来实现。根据EMCO LM600 五轴联动加工中心工作台直径、主轴直径,设计夹具。夹具安装在工作台中心,充分利用五轴联动机床的行程,同时保证 A 轴摆动角度大于等于 90°位置时,主轴与转台保持一定的安全距离。
工件装夹示意图如图 2,L 代表 A 转台直径,L1代表最小安全间隙,L2代表主轴半径,H1代表三爪卡盘高度,H2代表夹具高度。经分析可得 H2计算公式。

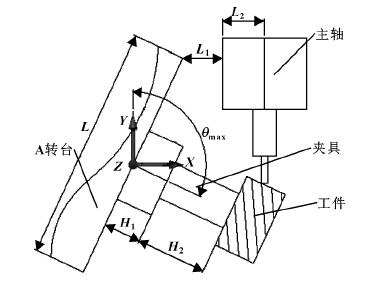
图 2 装夹示意图
为了方便装夹及拆卸工件,设计如图 3 所示的夹具,夹具上 3×8. 2 的通孔用于 M8 螺栓锁紧工件。
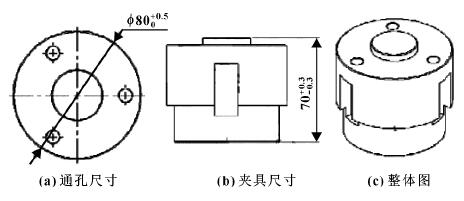
图 3 夹具设计图样
4 、加工工艺方案
4. 1 基于遗传算法优化加工工艺
核电冷却泵泵体加工有多种加工工序,一种加工工序有多个加工策略,一个加工策略又有多个加工参数。例如: 加工 28. 5+0. 084+0弯管外管面工序有 4 种:
( 1) 先把外管面粗加工、精加工到尺寸,然后再粗加工、精加工内管道; ( 2) 先粗加工、精加工内管道,再粗加工、精加工外管面; ( 3) 先粗加工外管面,然后粗加工内管道,再精加工外管面,最后精加工内管道; ( 4) 先粗加工内管道,然后粗加工外管面,再精加工内管道,最后精加工外管面。
精加工外管面时可以应用 Power Mill 最佳等高精加工策略,也可以应用 Power Mill3D 偏置精加工策略。加工工艺包括 8 个关键参数: 加工工序、加工策略、切深 ap、切宽 ae、主轴转速 S、进给量 F、加工时间、表面粗糙度。应用遗传算法优化加工工艺,既能保证加工精度和表面质量又能缩短加工时间。遗传算法优化加工工艺流程如图 4 所示。
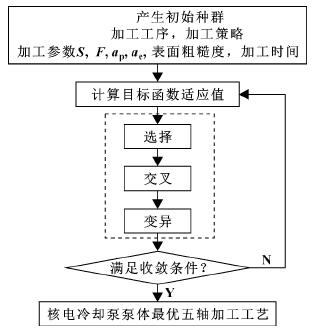
图 4 遗传算法最优解流程图
4. 2 加工策略
4. 2. 1 刀具选择
选择合适的刀具材料和刀具类型不仅可以提高加工效率,而且能够保证零件的加工精度。刀具的选择可遵循以下原则:
( 1) 粗加工时在尺寸允许条件下尽量采用大直径刀具,提高生产效率,降低刀耗。
( 2) 在保证产品零件尺寸的情况下,为使刀具有足够的刚度,其悬伸长度应尽可能短。核电冷却泵泵体毛坯材料为 2AL2,属于易加工材料。在综合考虑核电冷却泵泵体的形状、材料等各个方面的因素后所选刀具的参数如表 1 所示。
表 1 选用刀具参数
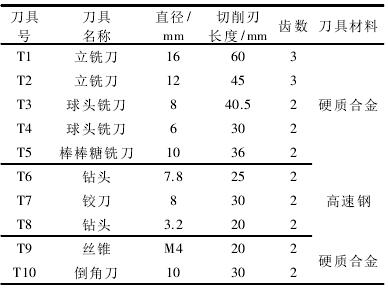
4. 2. 2 关键重要工序过程
( 1) R150 倒扣型腔及弯管外管面半精加工粗加工后外管面留有大量台阶余量,如图 5 所示。
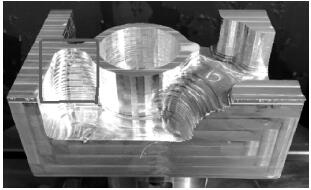
图 5 泵体外管面粗加工成品
如果直接精加工,精加工余量大并且不均匀,加工后的外管面表面质量较差。应将外管面大部分余量除去后再进行精加工,去除大部分余量可以应用模型残留区域清除策略,也可以应用最佳等高精加工策略,还可以应用等高精加工策略。应用遗传算法优化加工工艺后采用等高精加工策略。优化后的刀路轨迹如图 6 所示,提刀 301 次,加工时间 24 min4 s。
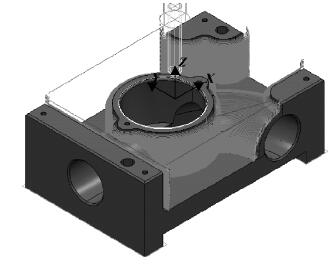
图 6 优化后的刀路轨迹
没有优化前的刀路轨迹如图 7 所示,提刀 781 次,加工时间 50 min23 s。
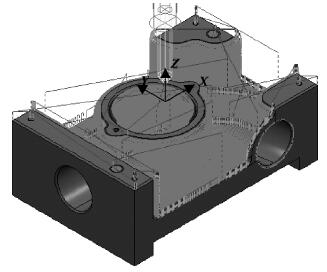
图 7 优化前的刀路轨迹
( 2) 内管道粗加工
为了保证内管道衔接光顺,外管面粗加工后加工内管道。如果外管面精加工完成后再加工内管道,内管道加工时工件会产生振动,导致内部管道面产生振纹,表面不光顺。粗加工内部管道面应用 Power-Mill2016 等高精加工策略从两端分别加工,比应用常规的模型区域清除策略开粗加工节省时间 23 min50 s,减少提刀 89 次。
( 3) 内管道半精加工应用
Power Mill2016 管道加工策略半精加工内管道,其刀路轨迹计算有 2 种方式:
①只需设置中心参考线,根据参考线的变化截取管道,完成刀路轨迹的计算,这种方式适合截面变化规律的管道; ②需要设置中心参考线、管道上下面坐标系,根据上下坐标系确定加工范围,用平行等距的方式截取管道,中心参考线作为刀轴的倾斜曲线,从而计算刀路轨迹,这种方式适合截面变化不规律的管道。此次加工的管道呈90°,总长为 115 mm,通过刀路轨迹计算,测得有效切削刃 95 mm 才能完成该管道加工,查阅山高刀具样本,最长的棒棒糖铣刀有效切削刃为 60 mm。由此可知,想用一个加工策略完成整个管道加工是不可行的。仔细分析内部管道面,有 65 mm 管道面是直管道面,应用 3+2 轴就能把该部分加工完成,为了保证内部管道面衔接光顺、无明显接刀痕,计算直管加工深度 W,W = 65-25+6+0. 5= 46. 5 mm。加工部位及
刀路轨迹如图 8 所示。
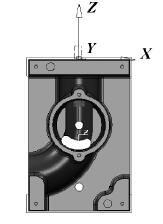
图 8 3+2 直管加工刀路轨迹
另一端长度为 64. 25 mm 的弯管面应用 3+2 轴定轴加工,应用管道粗加工策略配合直径 10 mm 的棒棒糖铣刀加工内管道弯管部位。中心参考线从管面到型腔中心位置,轴向余量为0. 35 mm, 行距为 3 mm, 下切步距为 0. 3 mm, 刀轴方向为自动,倾斜角度为 15°,顺序自末端均匀螺旋方式,快进高度为几何形体安全区域方框,打开自动碰撞模块,夹持间隙为 0. 5 mm
,刀柄间隙为 0. 5 mm。刀路轨迹、中心参考线、加工位置如图9 所示。
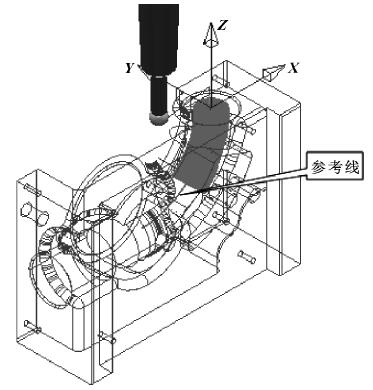
图 9 弯管加工参考线及刀路轨迹
( 4) 内管道精加工
内管道加工的精度影响到核电冷却泵主回路系统冷却剂的热循环效率,加工精度至关重要。长 46. 5mm 直管道面加工应用等高精加工策略加工,3 + 2 轴定轴加工方法,最小下切步距为
0. 9 mm,螺旋下刀方式。
弯管部精加工有 2 种精加工策略:
①管道插铣精加工策略,适合加工管道内部截面变化的管道; 管道螺旋精加工策略,适合加工管道内部截面一致的管道。文中加工的内部管道面属于截面一致的管道,应用管道螺旋精加工策略加工,行距为 5 mm、下切步距为 0. 3 mm、合并点为 60,提刀高度开始为 10mm,重叠为 8 mm,提刀高度为 0. 3 mm,打开自动碰撞 模 块,夹 持 间 隙 为 0. 5 mm,刀柄间隙为 0. 5mm,刀轴方向为自动,快进高度为几何形体安全区域方框,切入切出延伸移动方式,距离为 1. 5 mm。
( 5) 外管面精加工外管面精加工有 3 种加工策略:
①平行精加工策略; ②3D 偏置精加工策略; ③最佳等高精加工策略。平行精加工策略计算刀路轨迹的原理是计算出 2D 刀路,然后沿着 Z 轴方向投影到曲面上,采用该策略计算的刀路轨迹有一个弊端,如果加工的曲面较陡,投影到该区域的刀路就稀疏,加工出来的曲面不光滑,刀路轨迹如图 10 所示; 等高精加工策略计算刀路轨迹的原理是根据设定的下切步距把曲面按照层切方式分割,得到曲面加工刀路
。
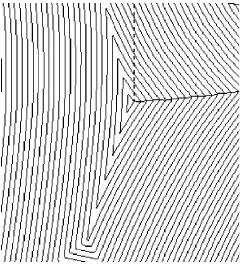
图 10 平行精加工刀路轨迹局部截图
该策略计算生成的刀路轨迹只能按照 U、V 方向排列,不能按照弯管的弯曲率均匀生成刀路轨迹,存在多处零点切削,加工后的管面也不光滑; 3D 偏置精加工策略计算刀路轨迹的原理是根据曲面的法向线投影计算,计算生成的刀路轨迹无论是陡曲面还是平缓曲面行距均一致。设置参考线及参考线方向后,可以按照参考线方向计算生成刀路轨迹,这样生成的刀路轨迹能有效减少刀具零点切削问题,加工出来的曲面表面质量较好,刀路轨迹及参考线如图 11 所示。
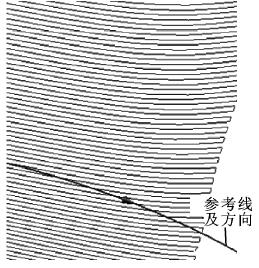
图 11 3D 偏置精加工刀路轨迹及参考局部截图
( 6) 底部 R4 倒角精加工中心型腔两侧 R4 倒角呈倒扣负角面,需要旋转工件把负角转化为正角才能加工。
文中加工方法是通过新建编程坐标系来控制工件旋转的方向及角度,复制 G54 坐标系得到 G54-1 坐标系,该坐标系绕 X 轴旋转 30°得到编程坐标系。加工 R4 倒角负角面应用清角精加工策略,按照默认的加工策略计算生成的刀路轨迹像缝衣服一样加工倒角面,如图 12 所示。
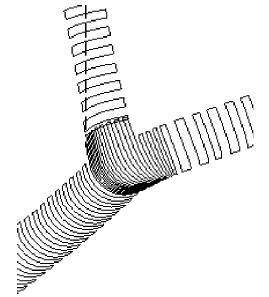
图 12 缝衣式刀路
加工出来的倒角面不光顺,有一道一道的接刀痕。为了倒角面光顺,应改变刀路轨迹的加工方向,通过把清角精加工策略中的方式设置为自动方式,重新计算生成的刀路轨迹沿着倒角面平滑走刀,如图 13 所示。
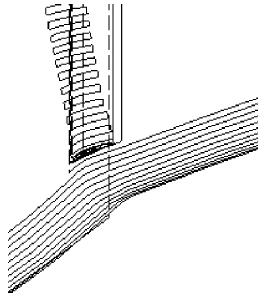
图 13 光顺式刀路
泵体左右两侧支撑体 R4 倒角面应用原 G54 坐标系编程,加工存在 2 个弊端: ①刀具悬伸长; ②刀杆擦到已加工面。刀具伸出夹持刀柄的长度要大于 30 mm,刀具伸出长度过长,切削时刀具会振动并存在让刀现象。切削过程加工倒角特征的刀具直径只有 6 mm,直径为 6 mm 的球体铣刀有效切削刃只有 18 mm,刀杆会把已加工表面擦伤。
为了避免上述弊端,加工两侧支撑体时均要旋转工作,让刀具和刀杆与侧面呈5° ~ 10°角度,如图 14 所示。
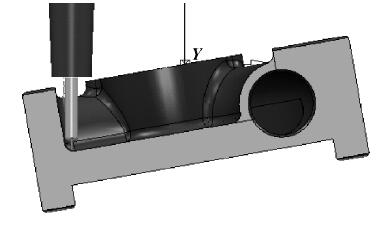
图 14 刀具与侧面夹角示意图
4. 2. 3 关键工艺参数
根据工序过程,分析零件各加工区域几何特征,结合加工过程,应用遗传算法得到最佳工艺参数,如表 2 所示。
表 2 加工工序及关键工艺参数
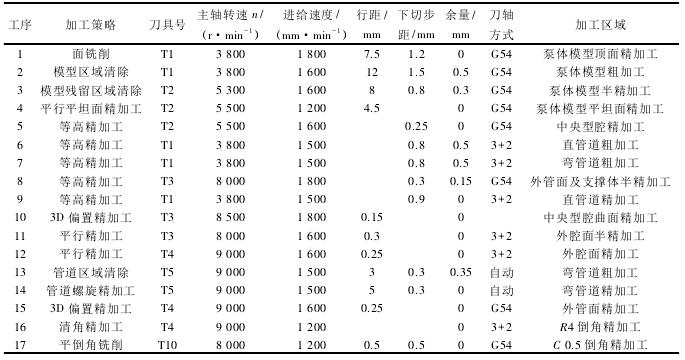
5 、五轴联动加工
5. 1 装夹方式
用三爪卡盘夹持夹具,然后用螺钉固定待加工的毛坯,如图 15 所示。卡盘用 4 块压板压紧在工作台上,卡盘压紧固定前装夹圆柱度小于等于 0. 005mm 的环规,用百分表校正三爪卡盘与机床工作台轴心线 同轴度,调整三爪卡 盘位 置,保 证 同 轴 度 在0. 02 mm 跳动范围之内,如图 16 所示。
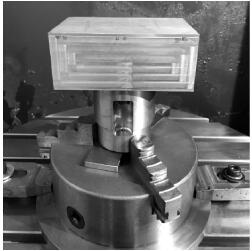
图 15 毛坯装夹
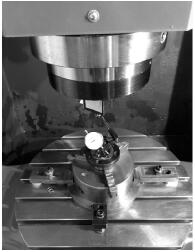
图 16 校正三爪卡盘
5. 2 机床运行加工
严格按照刀具参数表表 1 夹持刀具长度,按照刀具参数表序号依次把刀具装入机床对应刀库刀号。应用 EMCO LM600 定制后处理器,处理生成的刀位轨迹,转化成 NC 程序。通过 DNC
把加工程序输入机床控制系统,按照加工工序运行程序,加工过程中注意观察。加工过程如图 17 所示,加工完成泵体如图 18 所示。
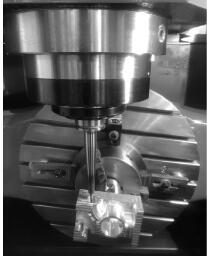
图 17 五轴联动加工过程
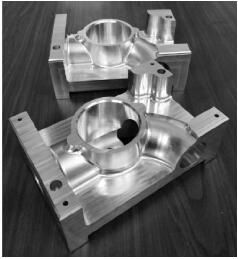
图 18 产品零件泵件
6 、结束语
核电冷却泵泵体作为具有代表性的五轴加工零件,本文作者应用 Power Shape 2016 尺寸中差建模,Power Mill 2016 编程,应用遗传算法,获得最优核电冷却泵泵体加工工艺方法; 利用
EMCO LM600 五轴联动加工中心加工完成,经 HEXAGON GLOBAL SDL07 10 07 三坐标测量机检测,尺寸精度及表面质量均到达要求; 解决了圆柱倒扣面、90°弯管管道、薄壁件等加工难题。该加工工艺可为企业生产,学员培训提供参考。
投稿箱:
如果您有机床行业、企业相关新闻稿件发表,或进行资讯合作,欢迎联系本网编辑部, 邮箱:skjcsc@vip.sina.com
如果您有机床行业、企业相关新闻稿件发表,或进行资讯合作,欢迎联系本网编辑部, 邮箱:skjcsc@vip.sina.com
更多相关信息