PLC 控制在转炉上的应用案例研究与分析
2015-12-24 来源:山东劳动职业技术学院 作者:李国伟
摘要:随着我国钢铁事业的发展,越来越多的新技术逐渐被运用到了炼钢领域中。其中,PLC 自动控制技术在炼钢厂转炉系统的应用就是其中最具代表性的技术项目。由于转炉工艺具有检测参数多、设备动作频繁以及工艺复杂等特点,PLC 技术在转炉工艺中的应用,能够在自动控制的基础上获得更为稳定、高效的生产效率。在本文中,将以某钢铁企业 PLC 控制在转炉上的应用案例进行一定的研究与分析。
关键词: PLC 控制; 转炉; 应用案例
0 引言
近年来,随着 PLC 在工业控制中的应用面越来越广,其对工业企业的影响也越来越大,必须保证 PLC 控制系统的可靠性。炼轧厂新建转炉系统在运行初期,技术部就面临六个常见技术问题:①通讯网络的高速、高效数据传递;②方坯拉矫机的平衡出力; ③板坯夹送辊电机的负荷平衡;④氧枪提升时的钢绳松弛与抖动;⑤四台转炉倾动电机的负荷平衡;⑥谐波干扰。本文将根据 PLC 控制技术的特点,针对这六项技术问题研究有效的应对策略,以确保系统稳定运行,同时提高系统的运行效率。
1 自动控制系统组成
在该钢铁企业中,其转炉自控系统为 2 台 S7-300PLC以及 1 台 S7-400 主站,在两者之间通过光纤组网架设实现数据的通信功能,而在主站下也设有一定数量的远程从站,以开放工作总线的模式来设计主站、从站之间的通信功能。同时,该企业互联网通过针对性系统软件的设计与调试,针对 3 个操作站的生产过程进行全方位监控。图 1表示自控系统构成。
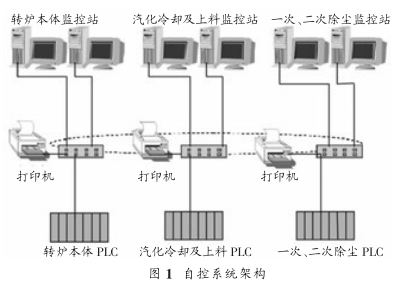
2 自动控制系统功能
在该转炉自控系统中,其一级自动化使用了 S7-400PLC 作为该系统的中心,二级自动化则使用了 WINCC6.2 与 STEP7 5.4 作为该系统的检测与编程软件。上位机方面,其通过互联网的应用同 S7-400PLC 实现连接,以此在实现对顺序逻辑控制的基础上,增加信号传输、数据采集、报警以及联动联锁控制等功能。
2.1 工程师与操作站
系统工程师站主要通过 STEP 7 软件进行操控,具体负责本系统中 3 台 PLC 站点系统的地址分配、硬件组态以及程序设计开发等工作。结构化编程方面,首先将不同功能模块整合成一套完整的控制系统,在软件方面针对系统干扰性设置相应的抗干扰措施。而在操作员站中,则通过 WINCC 6.2 以及 WINDOWS 系统的应用作为本系统的人机界面,并通过监控软件的应用实现整个系统的正常有序运行,并且除了上述功能外,其还具有报警、报表打印和信息归档等功能。
2.2 转炉本体 PLC 主站
主站的功能是实现氧枪升降、散装料胶料以及转炉倾动等的自动化控制,它可以对不同元素如氮气、氧气、水压力实施联锁控制,并且能检测系统流量。在水冷系统以及氧枪冷却系统中,其通过监控相关材料温度变化情况自动生成变化曲线,一旦系统操作过程异常,可及时发送报警信息,通过以太网将这部分监控所获得的数据在操作站与PLC 之间进行传送,整个转炉生产过程由系统人机界面进行有效监控。
2.2.1 氧枪升降控制
系统有两处位置可以实现该项操作,即氧枪机操作箱以及炉前主控室这两处无论是在哪一区域进行操作,都能使氧枪自动升降。由于转炉 PLC 中的数字量模板可实现对各项数据的采集、处理和传输等,变频器只要接收到相关的信号就会自动进行氧枪升降控制,这就是系统的开关信号。氧枪减速机轴上一般都装有增量编码器,用以定位氧枪升降高度,且在氧枪开、闭氧时也能调控风机的运转速度。将编码器脉冲信号传输到变频器中、与目标信号进行比较处理后,将此信号反馈到 PLC 中,经 PLC 通过该信号对氧枪高度进行定位。工作人员只需操作主站计算机即可完成画面操控任务。
2.2.2 转炉倾动控制
转炉倾动控制主要由操作员在炉后操作室以及主控室手动操作完成。为了完成操作任务,操作员可以在主操作台对炉后操作室和主控室这两个操作地点进行适当的切换。炉后操作室和主控室一般都装有主令开关,当操作员选定相关操作点后,主令开关就会根据操作员的选择情况自动前摇或后摇,然后这个结果会以硬线应用的方法传递给变频器,之后变频器根据接收到的信息。指令电机进行有效的操作。另外,在减速机轴上也装有具备零位联锁功能的主令控制器,钢温度和炉倾角温度也能够在计算机画面上显示出来。
2.2.3 安全限位与联锁
在系统的整个运行过程中,要想确保转炉一直处于正常运行的状态,必须设置现场设备的联锁回路,同时保证相关设备可以识别传输和处理后的联锁信号。为了最大程度的减少人员和设备损失,应在主操作台和炉后操作台两处都设置紧急停止按钮,这样即使出现意外情况,也能够在最短的时间内使设备停止运行,等到设备恢复正常状态时,再按下按钮复位即可。
在炉体施工方面,需要保证烟罩、氧枪在上升到设计高度、且整个装置没有发生油路故障时才能够进行倾动,以此最大程度的避免可能对设备造成的损坏。氧枪必须在炉体归于零位后才可以升降,如果炉体没有处于零位,会使氧枪出现钢丝绳卷反甚至被折断的情况。如果氧枪中氧气压力、氧枪冷却水及其流量所具有的温差同设定值之间的偏差超出预定值,则能够在系统控制下自动提抢,避免事故出现,且在氧枪达到开氧点时能够提高风机转速,并在停吹时自动转为低速。此外,为了保证在实际冶炼过程中氧枪不出现乱绳或断绳现象,氧枪左、右两侧的钢丝绳应该安装张力检测系统,在实际张力严重偏离设定值时自动停止氧枪的升降,同时为规避氧枪断电事故,系统中还装配了事故启动马达,以确保在问题出现时能够自动提枪,避免发生安全事故。
2.2.4 散装料下料
由主控室操作站完成散装料的称量和配料工作。操作员通过操控相关计算机系统进行称量和配料。自动下料时,首先称量下料量,然后是振捣,若提前量和实际称量值同称量设定值之间的差值是一样的,那么振料机就会停止振料,直到称量斗关到位后,才会进行下一步的操作,称量完毕后将称量斗汇总料下到钢水内完成加料任务。可以说,PLC 自动控制技术在该项操作中的应用,不仅能确保各项工作按预定顺序依次完成,同时可以有效提高系统运行的稳定性以及称量配料的精确性。
3 转炉炼钢 PLC 控制室配置及控制流程具体配置情况及控制流程详见图 2 和图 3。
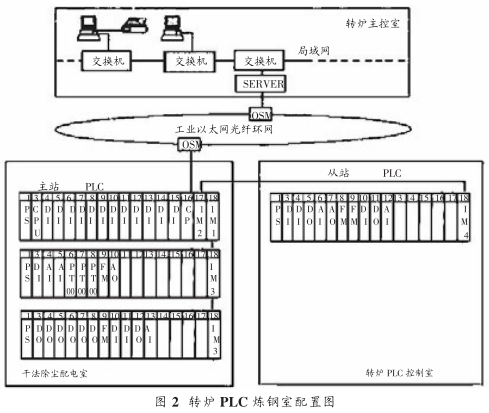

4 转炉 PLC 控制系统常见技术问题系统运行中,运行部门常常要面临六项技术问题:
①通讯网络的高速、高效数据传递;
②方坯拉矫机的平衡出力;
③板坯夹送辊电机的负荷平衡;
④氧枪提升时的钢绳松弛与抖动;
⑤四台转炉倾动电机的负荷平衡;
⑥谐波干扰。
5 针对六项常见技术问题的应对策略
5.1 针对 ①~ ⑤ 技术问题的控制策略
炼轧厂新建转炉工程选用的工艺装备都是在世界范围内都非常先进的,该工程的周期是十八个月,总投资达5.02 亿元,设计能力为年产钢二百万吨。针对系统控制中有可能出现的①~⑤技术问题,我们改进了传统的控制系统,选用了当今世界最先进的德国西门子公司的控制系统,该系统包括该公司的 PLC、通讯、工控软件及传动控制产品,通过利用该控制系统可实现对整个项目的过程及拖动控制任务。
该项目中采用的控制系统具有采集过程数据、控制系统设备、监视运行状态等功能,这些功能是由上位监控系统实现的,除此之外,上位监控系统还具有其他工业数据的采集、打印、报表生成和数据备份等工作。PLC 系统与传动控制系统间采用的是 PROFIBUS-DP 总线通讯方式,该方式是由西门子公司首先提出的,不仅能有效控制信号,还能够实现数据的高速传递和交换。另外,该系统中各个子系统 PLC 与其系统设备之间有充分的信号线连接,如此一来,即使某个子系统出现意外情况,也不至于全军覆没,未被波及的系统依然可以正常运行。
该项目中最大的难点在于四台转炉倾动电机的负荷平衡,要求其必须满足高速响应、高控制精度、高安全可靠性能。传统的控制装置很难满足上述要求,但是由于本课题选用的是西门子公司的全交流 MASTERDRIVE 6SE70系列变频器产品,再加上其配合西门子公司的 PLC、PROFIBUS-DP 通讯网络构建起高性能的传动系统,有效的解决了传统控制装置中存在的弊端,满足了上述该项目中的技术要求。不仅如此,它还大大提高了控制的响应速度和控制精度,效果明显。
5.2 抗干扰措施
供电系统中一般都存在大量的高次谐波,这会严重威胁本转炉系统的正常运行,对此,我们针对本系统特点设计了以下抗干扰措施:
5.2.1 接地
在接地方面,我们将计算机以单独的方式进行接地,保证接地电阻控制在 1.0Ω 以内,并保持电气接地的独立性,避免因为接地环在接地线位置上产生接地电流引发不必要的误操作。
5.2.2 通信电缆辐射
我们以钢管敷设的方式对 DP 网线以及以太网光缆进行敷设,并保证电力电缆间能够以分开的方式进行敷设。全部信号线走单独的电缆桥架,且对进入到 PLC 中的信号电缆都选择了具有屏蔽功能的电缆设备,以此起到消除耦合干扰以及辐射干扰的作用。
5.2.3 模拟量输入信号滤波
对于进入到 PLC 系统中的模拟量,我们在保证这部分输入信号实际进入到模拟量通道之前就通过光电隔离器的应用对可能存在的串模干扰进行了消除,以此起到了提升通道信噪比的效果。
5.2.4 电源隔离
对于实现系统完成自动控制的电源,我们专门为其安排了独立、具有屏蔽的隔离变压器供电,并保证该隔离变压器外壳能够以单独的形式接地,以此在同强电设备电位以及 PLC 进行良好隔离的基础上有效降低来自供电线路的干扰,同时,其还能够有效避免 PLC 系统出现误动作。
5.2.5 程序设计
在控制系统程序方面,为了避免模拟量瞬时干扰现象,应用了数字滤波技术,在输入信号方面,为了尽量避免出现误信号,应用了锁存和指令对比技术。
6 应用效果
经过一系列的改造,现场控制站在与设备自带 PLC通讯系统实现了 Profibus_FMS 控制,其通讯介质为屏蔽双绞线,通讯速率最大可达 1.5Mbit/s;10KV 及各变电所的相关信号,通过智能继电保护装置及智能空气断路器、用PROFIBUS-DP 的通讯方式与现场控制站交换数据,每个间隔保护及测量装置均作为现场控制站的从站;现场控制站采用西门子 S7 400 PLC,CPU 采用 4163DP 高档 CPU,不仅有效降低了人工劳动强度,也大大提高了运算效率和生产效率。且由于操作画面可以实时的传播出来,相关人员的系统操作难度有效降低了,系统设计更为人性化,对底吹及氮封系统的改进大大节约了氮气,提高了各钢种冶炼质量,同时进一步降低可冶炼成本。事实证明,采用西门子自控系统控制整个项目的实施是可行的,在采用该控制装置的过程中不仅整个系统运行比较稳定,而且使用效果良好,不仅事故的发生率大大降低了,而且取得了良好的经济效益。西门子自动系统不仅体现了其生产公司的智慧,属于国际先进的控制体系,同时该自控系统也是完全符合相关国际组织的规范标准的。
7 结论
可以说,转炉是炼钢生产过程中非常重要的一个环节,通过 PLC 在转炉上的应用,对于转炉工作的稳定、高效开展具有十分积极的意义。在上文中,我们对 PLC 控制在转炉上的应用案例进行了一定的研究,具有较好的研究与应用价值,建议将本文所述控制系统进一步推广应用到更多工业领域,通过提升设备自动化控制水平来提高生产效率和经济效益。
投稿箱:
如果您有机床行业、企业相关新闻稿件发表,或进行资讯合作,欢迎联系本网编辑部, 邮箱:skjcsc@vip.sina.com
如果您有机床行业、企业相关新闻稿件发表,或进行资讯合作,欢迎联系本网编辑部, 邮箱:skjcsc@vip.sina.com