工业机器人在数控机床压铸件加工行业的集成应用研究
2021-8-20 来源: 广州数控设备有限公司 作者:何敏佳 江文明
1.压铸产品制造企业存在的一些问题
随着生活水平的不断提升,人们对生活质量的需要也逐渐提高 ; 汽车、家用电器、电子通信等产品的需求及更替越来越快,而这些产品的零部件大多采用压铸成型制造的工艺方式。因为压铸产品有着近终产品特性,具有成形状态各异经济指标优良,外形尺寸精度高和互换性好,设计材料利用率高,只需经过少量机械加工即可装配使用,制造效率高等优点,是今后更多任务业产品采用压铸制造工艺的发展趋势。
然而,为了满足日益增长的订单需求,压铸产品机械加工中企业又面临诸多问题,比如压铸产品种类较多,但差异化小,需要多次装夹定位、兼容互换等保证加工后品质一致性 ; 订单多次少量、交货期短,对产线物料供应计划及时性,生产计划需更加周密协调 ; 数控机床加工的性能效率、编程与操作的复杂,需要配置更加专业的操控技术人员 ; 生产连续化、工件的上下料装夹,主要依赖工人的体力和技能,生产效率低、劳动强度大、缺少熟练技工人才,很难以保障产品加工的稳定性和一致性 ; 同时,随着人口红利的缺失,企业更面临用工荒、招工难,劳动力成本的大幅度上升等困境。
鉴于上述存在的问题,促使机床加工行业越来越多地利用自动化、信息化技术改造传统工艺流程转型升级 ; 进一步提高企业的生产应变能力,在短时间内转换生产,并兼容多种产品在线加工的智能化产线。需研究工业机器人在数控机床压铸产品加工的智能生产线来解决企业存在的问题,并推动企业智能化改造升级的必然发展趋势。
2.改善企业生产制造问题集成工业机器人应用的主要方式
工业机器人在数控机床生产加工中主要是替代作业人员改变传统的人工生产模式,将生产物料在不同工序间进行搬运与转换功能,实现产线的自动化生产流程 ; 机器人与数控机床集成的方式主要有以下 :
(1)集成单机工作站生产
集成单机工作站是机器人在数控机床上实现自动化生产的典型应用。多应用于生产单次批量大、加工时间短的中小零件加工 ; 对比人工操作上下料更准确、迅速、安全,机器人替代人工上下料作业的优势明显,也是实现产线自动化的基础。
(2)集成多机数控机床与工业机器人组成自动化生产线
工业机器人与若干台数控机床组成自动化生产线,完成生产中的几个连续性加工工序 ; 机器人主要承担工件在各工序之间的转换搬运工作 ;比集成单机上下料更为复杂也更有价值的一种应用。在当前工业转型升级过程中,市场需求越来
越广泛。
(3)集成多机组成自动化、信息化的智能生产线
在与若干台数控机床组成自动化生产线的基础上,需要对生产状况、设备状态、能源消耗、生产质量、物料消耗等信息进行实时采集和分析,进行高效排产和合理排班,显着提高设备利用率(OEE),柔性灵活调整工艺,适应小批量、多品种的混合生产智能模式 ;
3.工业机器人与数控机床集成智能应用产线解决方案
3.1 智能生产集成设计依据
通过以压铸产品成型后需要进行自动上料、工件识别、铣装配面、钻孔、攻丝、清洗、自动下料生产工艺需求为例,阐述采用工业机器人与数控机床集成技术对产线智能改造升级方案制定。
(1) 压铸产品规格: 约为 520mm*320mm*20mm, 产品重量 <=12kg;
(2)压铸产品主要加工要求见图 1;
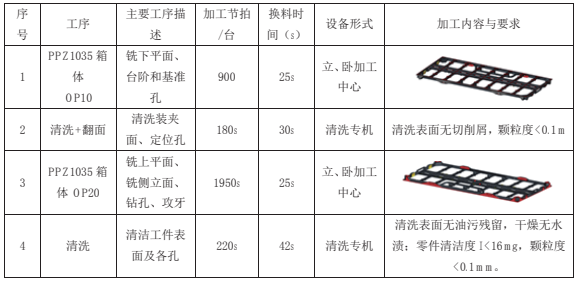
图 1
(3)料仓上下料、自动识别工件装夹、换产、生产信息监控等,实现数控机床连线自动生产。
3.2 智能生产线整体设计布局
项目采用3台数控机床加工系统、1台GSK-RB35 机器人、机器人第七轴移动系统、上下料仓、二次定位及识别系统、翻面装置及清洗系统,以及 GSK 制造执行系统等集成一体的智能加工生产线 ; 根据生产订单需求不同,可同时进行一种或多种产品柔性化混合生产 ; 实现不同工艺、型号批次产品的识别判断,可以快速制定生产计划、柔性转换智能生产,提高生产效率、保证产品质量。
3.3 集成的数控机床系统及工装夹具
集成高效五面体数控加工中心 YHV1165 机床,有立、卧、回转分度组合,实现车、铣及五面加工,可代替多台加工设备的机器人流水线,实现大零件复合加工,节约能量,提高空间精度,提升产品品质 ; 广泛运用于 LED 灯箱、新能源、通讯等压铸腔体加工。
(1)五面体加工中心是由一台卧式和一台立式加工中心组合而成 ; 使用同一套工作平面系统,并装有回转分度装置,可任意旋转角度实现多面、车铣复合加工能力 ; 一次装夹,减少多次装夹的误差,提高精度与加工效率。
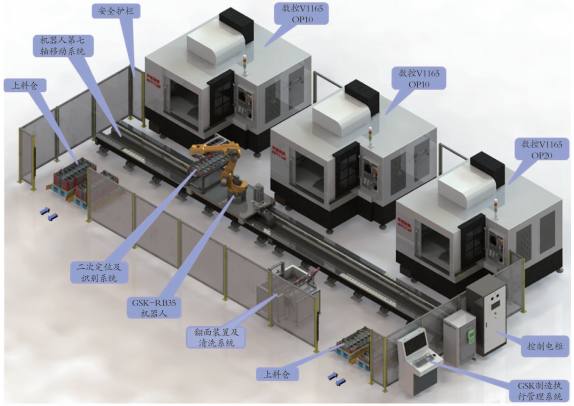
图 2 整体设计布局图
(2)机床有自动交换刀具的功能,通过刀库安装不同工艺用途的刀具,可在加工过程中自动切换主轴上的刀具,实现钻、镗、铰、攻螺纹、切槽等多道工序加工功能。
(3)一套系统控制立、卧两个加工中心组合。配备直线和圆弧插补功能外,还具有各种加工固定循环、刀具半径、长度自动补偿、加工过程图形显示、人机对话、故障自动诊断、离线编程等功能。
(4)机床专业装夹工装,采用液压夹紧、销柱定位 ; 具有夹持刚性强、重复定位精准及通用可靠,并实现加工系统自动控制夹紧松开命令。
3.4 GSK RB35工业机器人搭配机械手夹具
(1)系统采用 GSK RB35 机器人,重复定位精度高、速度快、控制灵活、服务半径大 ; 适合本产线加工中抓取工件在各工序间物料的搬运转换作业 ;
(2)针对工件的复杂性及应用环境。机械手夹具的设计采用膨胀销自定位 + 外抱夹紧方式 ;同时,还装有检测传感器、压控机构。设计特点如下 :
A.采用反重力外抱紧 + 膨胀销自定位结构,避免因有切削液等影响摩擦系数降低夹紧力因素;
B.膨胀销自定位夹紧 , 限制工件 XY 轴向自由度,保证工件定位精度的一致性 ;
C.整个夹具设计简单、紧凑,减小机器人选型及运行负荷 ;
D.具有断气、断电自保护功能,防止机器人运行过程中意外断气、断电夹爪不会自行松开。
3.5 机器人第七轴移动系统
设计机器人行走轴可极大地扩展工业机器人的工作空间,通过机器人行走轴,一台机器人可完成 3 个机床加工工位,以及上下料、检测、翻面、清洗工位之间的工作服务空间。
(1)运动由机器人系统直接控制,不需要增加控制系统。
(2)设计伺服马达控制,通过精密减速机,齿轮,齿条进行传动,重复精度高 ; 运行速度 3米 / 秒,有效负载大,提高工作效率,减少机器人配比数量。
(3)针对机床加工特定环境设计防护性,可适用于机床加工,涂胶,焊接、搬运等环境恶劣工况作业。
3.6 二次定位及识别系统
机器人从上料仓抓取的工件,先放在二次定位夹具定位、读取二维码数据,再进入机床调用匹配程序加工。
(1)二次定位夹具设计有销钉及基准定位面,并有吹气装置清洁工件表面杂质,保证工作放入机床夹具的精准性和一致性 ;
(2)工件二定位后,同时有非接触式扫描读取工件信息,将工件生产信息发送数据给 GSK总控制系统及生产管理系统。
3.7 翻面装置及清洗系统
翻面装置是依据工艺要求,在工件 1、2 机床加工完成后需要进行翻面定位,进行二次装夹加工另一面铣平面、钻孔、攻丝工序所设计 ;
清洗系统 :
(1)机床加工后会残留大量的切削液和切削屑,必须把切削液留在机床回收循环使用,而切削屑进行集中清除处理,保证加工零件清洁干净后传送到下工序 ;
(2)在数控机床内,机械手夹具上设计有高压气枪,利用机器人的空间作业性设定运动轨迹对加工零件进行全方位清理清洁不留死角位。
3.8 上下料仓及定位装置
料仓主要用于将贮存压铸工件,可持续集中为产线生产提供稳定的物料供应,节省人力,减轻劳动强度,提高工作效率 ; 项目上下料仓分别设计有双工位料仓、料仓定位机构、检测传感装置等装置 ; 可满足加工零件与机械手之间保持精确的位置关系,上料、卸料的准确、快捷 ; 同时,
实现在线不停机上下供应物料。
3.9 安全防护围栏
防护围栏采用标准金属网面搭配钢结构立柱设计,网面变形结实并耐冲击 ; 设置有安全门,安全感应光栅及安全锁 ; 用于建立防护围栏安全锁防护系统,对设备和现场工作人员起到很好的安全隔离防护作用。当发生异常时系统会报警警示,并整线停止工作,保证系统安全稳定生产。
3.10 GSK制造执行系统
GSK 智能制造执行系统针对企业生产特点建立以 GMES 为核心的生产计划协同管理平台,具备网络化监视、控制、数据采集等功能。利用GSK-LINK 总线实现数控机床、工业机器人系统、识别系统及生产辅助设备的连接进行智能化监控
管理。
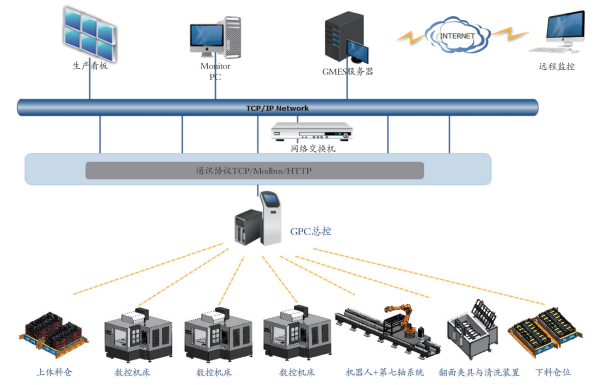
图 3 GSK 制造执行系统
(1)加工任务的创建规划、生产工序管理,及加工程序管理和信息数据上传 ;
(2)可在线检测实时显示和刀具补偿修正,及机床启停、初始化和管理 ;
(3)设置有智能广告牌功能 : 可数据采集与可视化管理,实时掌握设备运行情况、设备利用率、生产效率与产品质量,反馈生产信息以及机床刀具监控等功能应用,便于生产管理人员快速响应。
4. 生产工序流程图(见图4)

图 4
5. 工业机器人与数控机床集成应用效果
(1)机械手夹具采取快换设计,换产能自动切换夹具 ; 可以兼容多种工件的上下料工作,用较少的制造成本解决了多型号、小批量生产在同一产线柔性生产的难题 ;
(2)工业机器人完全替代人工装夹工件、工序转换及操控数控机床作业,实现 1 台工业机器人应对 3 台数控机床加工的上下料供给,并可24 小时持续作业 ; 人工生产配置 4 名工人 / 班,到升级后仅需要 1 名技术人员集中管理设备运行 ; 减少了设备及人员投入,还提高生产效率 ;
(3)改造前产线需准备物料、设备调机换产等准备工作,人工每班生产有效时间小于 7 小时,产线机器人改造升级后,每班可以连续生产 8 小时,平均生产效率提升 15%;
(4)工业机器人系统与数控机床、上下料仓、识别检测装置之间通过 GSK 制造执行系统紧密协调配合,节省工序转换、设备操控时间,并能连续稳定生产,最大化提升产线生产效率,降低生产运营成本。
6. 结语
通过阐述应用案例,机器人与数控机床集成可以装备应用压铸制造业智能化生产升级改造 ; “机器换人” 提高了工作效率,降低成本,缩短制造周期,适应小批量、多品种混合的智能生产模式。
未来企业需要根据市场需求,弹性地调整产能,实现个性化定制,制造出更智能的产品 ; 这不能仅依靠自动化技术来实现,还必须依靠信息化技术来解决业务层面的问题,为工厂赋予智慧,为需要市场决策、数据分析调控、质量管控、售后服务与追溯等提供依据和支持,实现工业机器人在制造业自动化与信息化结合才能够发挥最大功效,并将促使企业产品向专业化、连续化、智能化生产趋势发展。
投稿箱:
如果您有机床行业、企业相关新闻稿件发表,或进行资讯合作,欢迎联系本网编辑部, 邮箱:skjcsc@vip.sina.com
如果您有机床行业、企业相关新闻稿件发表,或进行资讯合作,欢迎联系本网编辑部, 邮箱:skjcsc@vip.sina.com