2022年机床工具专业“机械工业科学技术奖”项目申报及获奖情况分析
2022-11-4 来源:机床协会 作者:-
日前,2022年度机械工业科学技术奖评奖公示期结束,业界人士注意到,有多项机床工具项目获奖,今对“2022年度机械工业科学技术奖”机床工具专业申报及获奖情况做简要分析。
一、项目申报情况
2022年度机械工业科学技术奖机床工具专业组申报项目合计41项,与上年度相比增加7项,增幅20.6%。今年机械工业科学技术管理委员会增加了网评流程,网评通过率整体控制在70%,通过网评的会评项目29项。在29个项目中,有4个项目申报技术发明奖,25个项目申报科技进步奖。
2011年至2022年申报机械工业科学技术奖(机床工具专业)项目数量情况见表1。
表1 2011-2022年机械工业科学技术奖(机床组)项目申报数
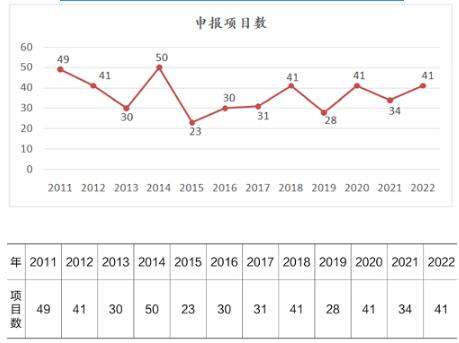
在进入会评的29个项目中,企业申报的项目22项,占比75.9%,企校(校企)联合申报7项,占比24.1%,企业成为2022年申报“机械工业科学技术奖”的主要力量,体现了企业是技术创新的主体。
参与评审的项目在行业和专业属性方面,金切机床类项目10项,占比34.5%;金属成形类项目8项,占比20.6%;铸造类项目5项,占比17.2%;工具类(刀具、磨料磨具)项目2项,占比6.9%;自动控制和生产线类项目2项,占比6.9%;机床功能部件和附件类项目2项。参评项目在行业和专业覆盖面上比较广,金切机床、成形机床和铸造类项目是申报机床工具组科技奖的主力军,铸造类项目今年增加比较多。
二、获奖情况及分析
经机械工业科学技术奖机床工具专业评审组评审以及机械工业科学技术奖评审委员会审核批准,申报单位确认,最终确定16个项目获奖,获奖比例为39%。16个获奖项目中,特等奖1项,一等奖1项、二等奖7项、三等奖7项。2022年度机械工业科学技术奖机床专业获奖项目见表2,2011-2022年历年机床工具专业获奖情况见表3。
表2 2022年机械工业科学技术奖(机床工具专业)获奖项目
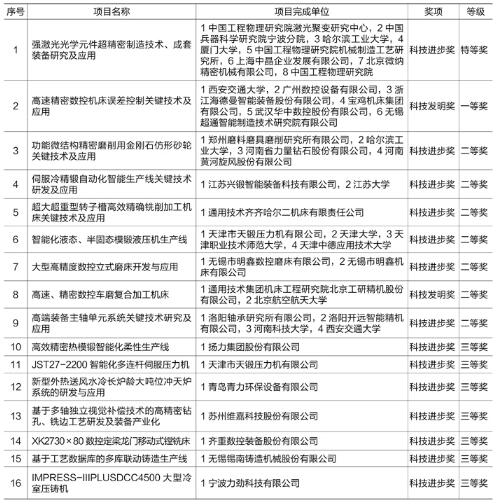
表3 2011-2022年机床工具专业历年获奖情况
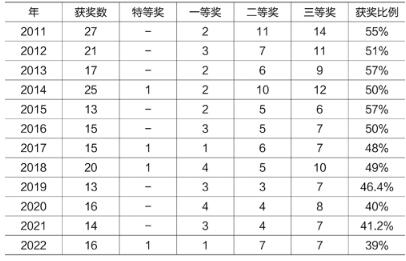
尽管2022年度机械工业科学技术奖机床工具组申报项目不多,但项目质量较高,获得特等奖1项,一等奖1项。获奖结果具有以下几个特点:
第一、本年度获奖项目比例历年偏低。获奖比例低或将成为今后机械工业科学技术奖评选中的常态。其原因,一是由于奖励办公室执行国家相关政策要求,对于获奖项目比例有严格要求。二是今年执行新的规定,本年度各等级指标数根据申报单位在申报时所填报的等级予以设定,申报单位可以选择一等奖以上、一等奖或二等奖、二等奖、二等奖或三等奖、三等奖和均可6种选项,如果发生评审等级低于提名等级的项目不予确认。2022年度,机床工具组会评项目中,有7个项目由于申报的等级高于实际评审的等级,项目申报单位对于项目获奖有较高的期望,从而放弃获得低于申报等级的奖项。由于规则是按本行业申报项目总数的一定比例分配获奖名额,为争取更多的行业创新成果获得表彰的机会,还需要行业企业、研究机构、大专院校更加广泛的参与。
第二、获奖项目覆盖的行业和学科广泛。金切机床、成形机床、铸造机械、工具类(刀具、磨料磨具)、控制技术及生产线、功能部件和附件项目均有获奖。
第三,高等级获奖项目集中来自企校、校企联合申报项目。本年度获得特等奖和一等奖的项目来自企校和校企联合申报。获得二等奖的7个项目中,5个项目来自企校联合申报,2个来自企业申报。获得三等奖的7个项目全部来自企业申报。企业在编写申报材料时,有可能对技术描述集中在应用效果方面,而对技术理论和数据上的分析有欠深入,今后申报时需多加注意。
第四,2022年申报机械工业科学技术奖(机床工具组)的项目质量很高,竞争激烈。由于各个等级对获奖比例有严格要求,同时,发生评审等级低于提名等级的项目不予确认,使得很多优秀的项目落选,令人惋惜。
三、部分获奖项目介绍
1.强激光光学元件超精密制造技术、成套装备研究及应用
荣获技术进步特等奖。由中国工程物理研究院激光聚变研究中心、中国兵器科学研究院宁波分院、哈尔滨工业大学、厦门大学、中国工程物理研究院机械制造工艺研究所、上海中晶企业发展有限公司、北京微纳精密机械有限公司、中国工程物理研究院共同完成。项目遵循工艺牵引、装备与工艺深度融合的总体思路,提出基于超精密形面创成的确定性控形流程制造新方法,创新高动态特性超精密光学制造机床设计,发明高性能工具及核心功能部件,构建强激光光学元件超精密制造技术体系,自主研发成套装备,社会效益巨大。创新点如下:
(1)提出“光学表面超精密创成+全空间频段误差确定性控制”的强激光光学元件全流程工艺方法,自主研制了 26 台套超精密光学元件加工系列装备,建成了平面、非球面等3条强激光光学元件先进制造示范线,实现了纳米级形状精度、纳米级波纹度、亚纳米级粗糙度的大口径强激光光学元件高效高精度制造。
(2)研制了高精度快速抛光机床,解决了基准面精密快速成形加工问题;研制了单点金刚石超精密机床,解决了大口径晶体亚纳米表面粗糙度切削加工难题。
(3)针对非轴对称非球面光学元件高效制造,发明了特殊的抛光算法,研发出气囊、磁流变、离子束等系列数控抛光设备,保证了元件高效制造需要。
(4)发明了大尺寸柔性抛光盘形状误差在位检测及精密修整技术,研制了平面快速抛光机床和全口径补偿抛光机床,提高了抛光材料去除效率,大幅提升了平面类元件制造效率。
2.高速精密数控机床误差控制关键技术及应用
荣获技术发明一等奖。由西安交通大学、广州数控设备有限公司、浙江海德曼智能装备股份有限公司、宝鸡机床集团有限公司、武汉华中数控股份有限公司、无锡超通智能制造技术研究院有限公司共同完成。项目在国家973及04专项等支持下,围绕机床热误差、空间轮廓误差、主轴高速不平衡误差等影响数控机床精度及稳定性的难题,在机床空间及动态误差的建模与补偿批量化工程应用、主轴高精度在线动平衡等方面取得了首创性技术突破,实现了国产数控系统等功能部件误差控制能力和机床精度及稳定性的显著提升,开发自主可控的国产数控机床,解决了航空航天、精密模具、汽车制造等行业关键零部件的精密制造难题。主要发明如下:
(1) 提出了机床热误差标准化建模与智能优化方法,发明了具有参数自校正功能的热误差建模和补偿软硬件模块,首次实现了同类机床热误差模型的批量化稳定应用。
(2) 发明了机床摩擦动态误差自适应控制技术,提出了考虑刀具空间矢量的机床空间几何误差测量与辨识方法,解决了机床配国产数控系统的空间轮廓误差补偿批量化应用难题,使普通机床体对角线误差<25μm、圆度误差<2.5μm,达到精密机床等级。
(3) 提出了一种基于动力学传递系数的主轴不平衡矢量的无试重辨识方法,发明了高效精密喷液式在线平衡终端和系统,实现了机床电主轴转子系统30000r/min下的在线动平衡,精度超过G0.4级,主轴在线动平衡误差控制处于国际先进水平。
(4) 发明了误差智能建模与补偿模块、在线动平衡装置等软硬件系统,突破了国外主流数控系统误差补偿接口限制,提升了广数和华中等国产数控系统误差控制能力,开发了GSK25i等4款国产高端数控系统,在海德曼、宝鸡机床等20余种国产机床上实现批量化工程应用。
3.功能微结构精密磨削用金刚石仿形砂轮关键技术及应用
荣获技术进步二等奖。由郑州磨料磨具磨削研究所有限公司、哈尔滨工业大学、河南省力量钻石股份有限公司、河南黄河旋风股份有限公司共同完成。金刚石仿形砂轮是实现高性能功能微结构器件制造的核心,其加工精度和质量对微结构的性能发挥具有决定性作用。项目攻克了高端金刚石仿形砂轮核心关键原材料设计制备、微细仿形结构高精度加工与检测、超声流固复合磨抛工艺和装置等核心技术,取得了如下创新成果:
(1)构建了砂轮动态硬度及载荷分布模型,揭示了仿形砂轮磨损失效及形性演变机制;开发了新型结构金刚石高效合成技术和新型结合剂,实现了金刚石磨粒与粘结剂界面的化学冶金键合。
(2)开发了金刚石仿形砂轮精密成形技术、自适应往复交叉加工和摩擦驱动修整与检测技术,实现了高精度制造与检测。
(3)提出了微结构磨削角概念,建立了面向微结构的超声复合磨削模型,揭示了在其影响下的磨粒动态轨迹演变和低损磨削机制;开发了裂纹损伤在线预警监测系统,实现了微结构表面裂纹崩碎损伤的有效监控;发明了低损高效超声流固复合磨抛工艺及装置,加工效率和质量显著提升。
4.伺服冷精锻自动化智能生产线关键技术研发及应用
荣获技术进步二等奖。由江苏兴锻智能装备科技有限公司、江苏大学共同完成。本项目重点在冷精锻装备的伺服化、自动化生产线集成,智能化技术应用等方面进行创新,实现了高强度铝合金锻件高节拍、高精度、高稳定、自动化生产的目标。主要科技创新工作包括:
(1)突破了多电机伺服直驱架构下高刚性机架与高刚性传动机构的关键技术,使用低速大扭矩直驱技术,研制出了16000kN 肘杆式冷温精锻伺服压力机。
(2)提出了四电机直驱高效率传动技术方案,突破了四电机同步驱动与控制技术,解决了齿隙非线性等关键技术难题。
(3)研制了具有接触感知功能的伺服直驱三次元十轴步进梁机械手和伺服冷精锻自动化智能生产线。
(4)开发了基于工控机和国产实时操作系统(SylixOS)的伺服压力机控制系统及智能化生产线运维服务平台。
(5)研发了6000Nm~35000Nm峰值扭矩的内嵌式(IPM)低速大扭矩伺服电机系列产品和高过载、大功率伺服驱动器系列产品。
5.超大超重型转子槽高效精确铣削加工机床关键技术及应用
荣获技术进步二等奖。由通用技术齐齐哈尔二机床有限责任公司完成,项目针对电机、汽轮机制造企业的生产需求和超大超重型转子槽高效精确铣削加工机床设计制造中存在的突出问题,研发超大超重型转子槽高效精确铣削加工机床关键技术,形成具有自主知识产权的超大超重型转子铣削加工专机设计制造与装调工艺技术,研制电机和汽轮机超大超重型转子铣削加工专机产品,通过成果推广应用,解决超大超重型转子槽高效精确铣削加工中亟待突破的关键技术瓶颈问题,为大型能源装备研制和生产提供技术保障。主要创新点如下:
(1)超大超重型转子槽高效精确铣削加工机床设计制造技术。研制出基于立柱的箱中箱整体结构、主轴箱中心热对称分布、四导轨冗余结构的重型转子轮槽铣床,转子加工范围最大长度15000mm,最大直径3400mm,工件重量300t,实现了超大超重型转子槽铣削加工机床设计制造技术上的突破。
(2)超大超重型转子自适应静压支撑与回转精度保障技术。转子主支撑采用静压球面轴瓦技术,保证了轴瓦与转子轴的接触面积,降低了调整难度,确保支撑更加安全可靠。
(3)超大超重型转子回转进给分度系统与精度可靠性保证技术。该系统由伺服电机直联高精度、低背隙减速机驱动,采用双列圆柱滚子轴承与双角接触球轴相结合,使系统主轴获得高刚度,通过双左右旋转齿轮相互啮合,利用碟簧预紧调整齿轮轴向距离,消除主轴的转动间隙,保证了回转进给分度系统的无间隙传动,分度最大扭矩达到 175680Nm,分度精度达到±3"。针对转子外圆加工误差、挠曲变形和转子滑动引起的分度误差对转子槽加工精度的影响,研发出双反馈系统误差检测校验技术。
6.智能化液态、半固态模锻液压机生产线
荣获技术进步二等奖。由天津市天锻压力机有限公司、天津大学、天津职业技术师范大学、天津中德应用技术大学共同完成。本项目应用轻量化车轮锻造技术与数字化控制系统,所建成的锻造生产线以液态模锻液压机为核心技术装备,优化了智能模锻液压机的主机结构设计、锻造过程的速度和压力的控制算法;再进行辅助装置的集成研发;最后,通过MES和工业以太网实现生产线的数字化控制,保证了液态模锻铝合金轮毂产品的稳定性和可靠性。主要创新点如下:
(1)研制出液态、半固态模锻专用液压机,并基于MES系统,依据铝合金轮毂成形工艺技术要求,将液压机与定量炉、取料机器人、冷却系统、自动喷淋装置、称重装置、刻字装置等集成,形成液态模锻工序生产单元。
(2)开发了恒升压速率与变升压速率的液态、半固态模锻成形控制系统,实现了液态、半固态模锻铝合金轮毂一次成形。
(3)开发了具有配方信息、工件信息和工艺数据智能化运维数据的管理系统,实现了液态、半固态模锻铝合金轮毂的工艺分析和质量追溯。
7.大型高精度数控立式磨床开发与应用
荣获技术进步二等奖。由无锡市明鑫数控磨床有限公司、无锡市明鑫机床有限公司共同完成。项目开发了5轴数控双立柱定梁机床结构、高精度大直径重载荷闭式静压工作台、高精度高刚性磨头主轴、高灵敏度进给系统、高刚性砂轮修整器等机床部件,满足了超大型风电主轴轴承的精密加工要求;研发了磨架液压自动平衡、断电自锁保护等关键技术以及带有二次开发交互界面的数控系统。产品具有高效率、高精度、高承载能力、自适应、大型化等特点。项目的主要创新点如下:
(1)单工位多复杂型腔精密立式磨床结构创新设计。设计了双立柱定梁、双磨架和高精度数控回转转塔结构的布局方式,考虑承受动静态交变载荷的高刚度底盘及立柱设计,研究了放射状磁极电永磁吸盘T形槽排布规律、电磁有效吸力与工件重量之间的参数匹配、导磁块安装方式等,开发了磁力调整与消磁装置。
(2)高性能大型精密功能部件的研究开发。高精度高刚性磨头主轴系统,高刚性砂轮修整器,高刚性高精度静压工件回转主轴,进给系统刚性和灵敏度设计。
(3)功能模块与磨床主结构相互作用下的精度控制。依据静力学分析、模态分析和谐响应分析,开展了磨架和工作台的结构优化设计。建立了磨床主体结构的虚拟样机,利用有限元分析和实验相结合的方法进行磨床主体结构在静动态载荷下的优化设计和可靠性设计。对整机热源敏感性进行分析和测试,优化机床结构。
(4)考虑动态多物理场特性的精密磨削工艺改进。对多刚体运动下的几何误差和载荷误差科学评估,创建基于动态效应和热变形分析的磨削工艺库,建立几何误差、载荷误差、热变形等影响磨床精度误差的主要误差源的综合精度误差模型。可实时高效、精确地对磨床误差进行补偿,提高磨削精度,提高磨床的工艺性能。
8.高速、精密数控车磨复合加工机床
荣获技术发明二等奖。由通用技术集团机床工程研究院北京工研精机股份有限公司、北京航空航天大学共同完成。项目依托04专项,针对汽车CVT自动变速箱关键零件批量加工的需求,从设计、制造、精度与可靠性保障等方面开展了系统研究工作,成功研制出μ4000TG车磨复合机床,可在一次装夹中实现外圆、端面、内孔及内沟槽的高效、高精度连续工序的车削、磨削加工,满足了零件精密加工要求。主要创新点有:
(1)建立了从零件加工需要与整机结构相适应的整机正向设计技术体系,设计了车磨复合加工机床。机床采用高刚度、高阻尼性的人造矿物铸件床身,床身上镶嵌着各个重要零部件的安装基面,安装基面彼此独立。X向导轨、直线电机及副工作台固定在安装基面上;工件主轴固定在十字溜板上,随十字溜板一起运行;各个加工工位包括内孔磨削轴(转速达45000r/min)、硬车削装置(可车削硬度HRC58~63的零件)、测量装置、沟槽磨削装置(转速达36000r/min)、锥面磨削轴(内置动平衡及AE声纳系统)等固定在副工作台上。机床集硬车削、外锥面磨削、内孔磨削、球道磨削等多种加工方式于一体,实现了工件在一次装夹中完成全部加工的要求,确保了批量零件的高精度、高效率加工。
(2)创新性设计了五爪弹性气动夹紧装置,解决了轴套类、盘套类零件在硬车削中大切削力下的装夹精度。该夹具采用双作用气缸+矩形弹簧执行松开夹紧功能,夹紧安全可靠;应用五角气缸杆推动五爪活塞轴杆同步运动,夹紧一致性好、导向精度高;中心配置接长冷却接头,内磨加工时冷却散热快,解决了工件磨削时发热烧伤问题。
(3)创新性设计了直线型沟槽磨削装置,解决了小直径内孔沟槽难加工的问题。该装置由伺服电机、同步带轮、同步带、砂轮轴系、底座、砂轮架等组成增速机构,变速比为4:1,砂轮的最高转速可达到36000r/min。砂轮架采用38CrMoAl材料经锻造而成,有效提高了砂轮架的刚度,减小了磨削振颤。
(4)加工系统整体温度控制技术。通过采用结构优化及整体温度控制专利技术,使加工区的温度可控,有效控制了机床的热变形,在使用中降低了机床对于周围环境温度的要求,具有很好的现场适应性。
(5)建立了硬车削及CBN砂轮高精、高速、高效的加工工艺体系,在用户生产中取得良好的应用效果。
9.高端装备主轴单元系统关键技术研究及应用
荣获技术进步二等奖。由洛阳轴承研究所有限公司、洛阳开远智能精机有限公司、河南科技大学、西安交通大学共同完成。本项目针对数控机床等高端装备所需核心关键功能部件电主轴开展设计及精密加工制造等系统研究,开发基于智能化需求的高性能数控机床系列主轴单元及精密轴承。掌握了高端装备主轴单元及电主轴的设计方法,形成了一系列具有自主知识产权的核心技术,提高了智能制造等相关功能部件企业的竞争力,为国产高性能主轴的推广打下了坚实基础。本项目关键技术如下:
(1)高速电主轴系统工作状态的瞬态动力学分析。基于有限元单元建模方法建立主轴动力学分析模型,提高了建模的快速性和分析的准确性。研究高速电主轴在工作状态的固有频率等动态性能,为主轴的优化设计以及状态分析提供依据。
(2)高刚度电主轴轴系单元系统设计技术。建立电主轴轴系模型,进行轴径、支撑跨距和一阶临界转速目标函数的优化设计。采用前端卸荷的轴系结构,实现主动卸荷。此轴系结构紧凑,作用在转轴轴系上的附加质量小,且动作可靠。
(3) 高速电主轴电机永磁转子设计技术。采用主副永磁体结构,能够平衡主轴在高速旋转过程中产生的应力,在电磁性能方面,磁阻更小,在增加恒功率段弱磁调速范围的同时优化气隙磁密波形,减小漏磁,降低电流谐波量,减小转矩脉动,平衡转子各处应力。
(4)超高速轴承长寿命、低功耗优化设计技术。研究了载荷、转速、预紧载荷等工况条件下轴承结构参数与轴承温升和摩擦力矩的关系,建立了超高速球轴承低功耗设计方法,掌握了工况条件、轴承结构参数及润滑参数对轴承温升和摩擦力矩的影响规律,形成了以额定动载荷和摩擦力矩为指标的超高速球轴承长寿命、低功耗设计技术。
(5)高端装备主轴单元润滑及冷却技术。建立高速电主轴在脂润滑下的有限元数学模型,从转速、填脂量、润滑脂粘度等多方面,对轴承腔内润滑脂分布、油膜特性进行数值分析,探明了摩擦和发热机理以及电主轴的热态性能,确定了特定工况下润滑脂最佳粘度和填脂量。对于电机部分,在定子外周采用“凹”字形截面的螺旋流道,提高热交换率,实现电机定子强制冷却。对于轴承部分,采用外圈轴承座“双环形槽”结构,进出油口“三进三出间隔”结构,连续通过冷却油,实现均匀、高效强制冷却。
(6)基于负泊松比材料的高速主轴轴承智能预紧技术。提出了一种基于泊松比可控结构轴承隔套的预紧力自适应调节方法。该隔套在离心力作用下会发生轴向变形,产生轴向力使轴承预紧力得以改变,从而可实现在不同转速下预紧力的自适应调节。
作者:沈华红(协会市场部) 责编:张芳丽
投稿箱:
如果您有机床行业、企业相关新闻稿件发表,或进行资讯合作,欢迎联系本网编辑部, 邮箱:skjcsc@vip.sina.com
如果您有机床行业、企业相关新闻稿件发表,或进行资讯合作,欢迎联系本网编辑部, 邮箱:skjcsc@vip.sina.com
更多相关信息