机械主轴轴承振动监测与故障诊断研究
摘要:针对数控机床机械主轴在故障发生时的非平稳特性及主轴运行状态监测的问题,提出了一种基于振速均方根值和频谱分析的振动监测分析方法。以某龙门机床机械主轴为对象开展研究,选择振动测试仪的振动速度值进行快速状态识别,发现异常后针对主轴重要部件轴承进行持续性监测,利用频谱分析诊断出轴承的缺陷位置。结果证明该振动监测分析方法可以快速有效地诊断出机械主轴故障位置,提前采取措施以避免故障进一步恶化,为主轴后期的检修和维护提供了可靠的依据。
关键词:机械主轴;状态监测;振动分析;轴承失效;频谱
在数控机床加工中,主轴是机床的重要部件之一,它的性能直接决定了加工工件的表面质量,一旦主轴出现故障,将造成机床长时间停机,为企业带来巨大的经济损失。其中主轴的很多机械故障是由于机床关键部件磨损、振动、超负荷加工等加工状态或外部环境改变引起的渐变性故障,因此对主轴进行预防性维修,尤其是监测其振动情况是很有必要的。万海波等研制了基于 HHT 时频分析方法的机床主轴振动分析系统进行振动监测。籍永建等利用 EMD 的方法对主轴振动信号进行分析。汪顺利等利用 Lab VIEW 对主轴进行振动测量与分析。目前很多学者对数控主轴的状态监测技术没有很好地应用在实际生产环境中,对实际发生的突发性故障也缺少实际案例分析。
为了保障数控机床的正常使用,对潜在故障进行预防性维修,本文针对某国外龙门机床的机械主轴展开振动监测与分析研究。基于高效的振动分析装置对该机械主轴运行过程中振动信号进行采集分析,与厂家允许的振动值对比发现异常位置;通过计算关键轴承的特征频率,诊断得到故障部件;对比历史故障信息,进一步确定故障部位,指导维修人员提前订购备件,制定相关维修计划。
1、 振动分析与诊断
1.1 状态监测
设备状态监测技术是指机器在运行情况下,了解和确定其状态的过程。工业领域应用的主要状态监测技术有振动分析与诊断、润滑油分析、红外热成像技术、超声波检测(材料厚度/缺陷检测)和电机状态监测与电流特征分析等,其中振动分析是最常用的状态监测技术。
在工程应用中,为了真实准确反映机械传动部件的振动状态,要注意选择监测点的位置和采集方法,传感器一般安装在主轴端面附近的轴承位置有较好的监测效果。另外必须注意对振动信号进行多次采集和分析,进行横向综合比较,也需要通过将设备的振动频谱与历史数据进行纵向比较,为预防性维修提供可靠的理论指导和故障信息。
1.2 轴承故障诊断
轴承是大多数机械结构中最重要的部件之一,轴承的工作状态与旋转机械的运行可靠性息息相关。然而在数控加工的复杂环境中,主轴系统内的轴承在使用中存在过早失效的现象。主要原因有超负荷运转、主轴润滑不足、误操作带来的隐形损伤、密封效果差或配合过紧等,这些因素都会产生特定类型的轴承故障,导致轴承振动加剧造成灾难性破坏。
在生产状态监测中发现,轴承在其使用过程中表现出很强的规律性,并且重复性强。轴承各部件都有其特殊的故障频率,若轴承发生故障,它的幅值增加,并有谐波,谐波两边产生边频。轴承有 4 个部件组成:滚动体、保持架、外环和内环。对轴承故障机理研究表明,当轴承损伤时,将出现 4 种故障频率之一或若干故障频率同时出现。轴承的故障频率可用下列公式计算:
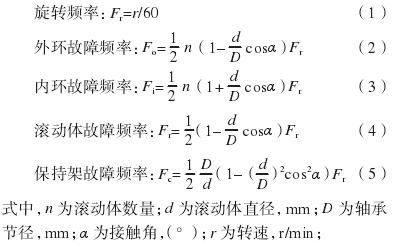
2 、案例分析
2.1 机械主轴状况
数控机床中的机械主轴有转速低、扭矩大的特点,适宜加工高强度、高硬度材质。本次以某国外高端龙门机床的机械主轴为研究对象进行振动分析。该主轴在一年前由于主轴端面的轴承磨损严重造成了滚动体脱落,等待备用轴承造成停工数月严重影响了零件的交付,在维修更换后,为了避免突发性设备故障造成的经济损失,设备人员开始对该主轴定期进行振动检测,监控主轴运行状态,重点关注主轴更换后的轴承使用状态。
2.2 振动监测
主轴振动分析采用了一款 Smart Balancer 的仪器进行振动测试,它是一个方便高效的检测仪器,搭配了一个三相加速度传感器,可以快速对振动信号进行采集分析而不用拆卸机床主轴。在每次进行振动监测时,需要保证主轴转动参数、装配刀具及传感器位置一致,测量数据才可以真实反映故障的变化趋势。具体参数信息如表 1,传感器位置如图 1 所示。
表1 振动监测参数信息
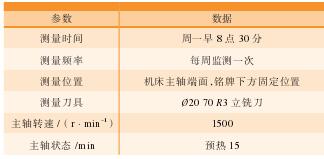
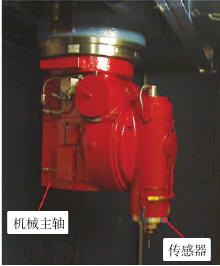
图1 机械主轴及传感器位置
2.3 轴承故障频率计算
该主轴大修后更换的轴承参数如表 2 所示。
表2 轴承参数信息
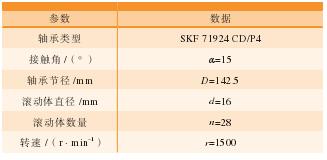
依据上述技术数据,分别计算轴承各部件在轴承内圈转速为 1500r/min 时的故障频率:
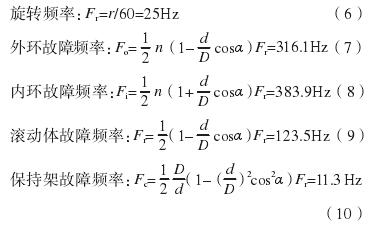
上面计算的各特征频率都是从理论上推导出来的,而实际轴承的几何尺寸会有误差,加上轴承安装后的变形,使实际的频率与计算所得的频率会有差异,所以在频谱图上寻找各特征频率时,需在计算的频率值上下找其近似的值来做判断。
2.4 故障分析
经过两个多月的持续性监测,发现该主轴的振动速度均方根值 RMS ≥ 0.2mm/s,超过了 SKF 轴承制造商建议的安全振动限值 0.2mm/s。针对此异常现象对主轴进行振动频谱分析,进一步发现故障原因,本文选取了近两个月的测量结果作故障分析,8 次频谱图分布如图 2 所示。
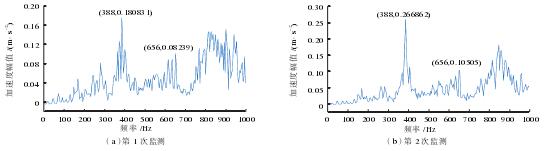
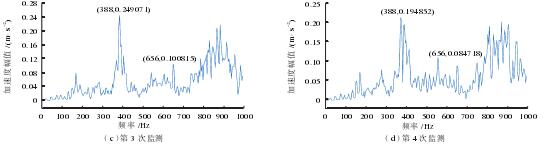
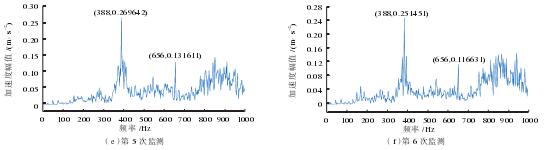
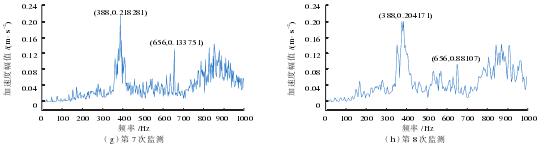
图2 故障频谱图
从频谱图的谱线分布来看,在 0~1000Hz 轴承范围内,轴承内圈故障频率 383.9Hz(实测为 388Hz,与计算值非常接近)的幅值非常明显,而且每次测量幅值都会较前一次增大(表 3),两个多月的时间内从 0.18mm/s(2次方)增大到 0.27mm/s(2次方),结合之前该主轴轴承故障进行综合考虑,由此可以判断该轴承的内圈已经出现了缺陷。同时内圈故障频率两侧均有明显边频带,说明该内圈故障在这段时间内持续扩展导致了幅值的增大。
表3 8次故障频率幅值记录
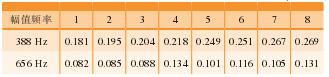
另外从频谱图中可以看到,轴承外圈故障频率316.1Hz 的 2X 幅值(实测值为 656Hz)也较为明显,推断出轴承的外圈受内圈故障影响出现缺陷的可能性比较大。在 800~900Hz 之间出现的高频连续谱,噪声底线明显抬高,分析认为是内圈故障正在进一步恶化,造成了主轴转动时会出现松动摩擦的现象。
通过上述分析可以得到该机械主轴的轴承已经出现了故障隐患,需要在下次检修中安排更换轴承。经过和维修人员确认,上次轴承故障就是内圈严重破损导致滚动体散落发出异响才进入维修,此次距离更换轴承后时间不超过半年,轴承内圈已经出现了缺陷,推断可能是主轴内部传动结构存在缺陷或者由轴承安装和润滑等因素导致的。为避免缺陷扩大导致停机故障,已经提交备件采购流程,同时采取机床限制性使用和按期振动监测等措施进行主轴状态跟踪。
3 、结论
通过对数控机床的主轴进行振动监测与故障分析,可以判断出主轴轴承的运行情况、出现缺陷的部件及缺陷的严重程度。在实际应用中,操作人员可以通过便携式仪器对主轴状态进行快速检查,诊断上可采取振动速度有效值结合频谱分析的方法进行综合诊断,为设备维修和备件采购提供可靠的理论指导,降低因轴承故障造成主轴事故扩大的可能性。对主轴诊断的技术还可以采取监测噪声、温度和润滑等多种技术手段结合,可以提高主轴故障识别与诊断的准确率。
投稿箱:
如果您有机床行业、企业相关新闻稿件发表,或进行资讯合作,欢迎联系本网编辑部, 邮箱:skjcsc@vip.sina.com
如果您有机床行业、企业相关新闻稿件发表,或进行资讯合作,欢迎联系本网编辑部, 邮箱:skjcsc@vip.sina.com
更多相关信息
- target=_blank> 动力卡盘对数控机床加工精度的影响
- target=_blank> 某数控机床Z轴异响故障诊断及维修
- target=_blank> 基于德国巨浪 DZ18W 数控机床的升级改造
- target=_blank> 高进给刀具的加工应用
- target=_blank> 加工中心电主轴结构分析及典型故障修理