高速电主轴的热态性能分析与计算
高速主轴是实现高速加工技术的关键功能部件,主轴的刚度、热态特性、疲劳寿命等性能参数均影响产品的加工质量和加工精度。日、德、意大利、瑞士等国家的数控设备多采用电主轴,相较于传统的主轴,电主轴具备结构紧凑、回转精度高、动态特性好等特点,是实现高速加工的核心部件。而电主轴由于采用电机主轴一体化的设计,会导致主轴内部温度的升高,过高的温度会影响主轴的加工精度,严重者会使轴承失效,造成主轴的损坏,影响生产的进行。因此有必要对电主轴的热态特性进行深入研究。
本文针对电主轴的热态特性,采用有限元的方法,对电主轴内部的温度分布进行了仿真分析,此举有益于电主轴的稳定运行,也可以为电主轴热变形的计算和补偿提供理论基础和有益参考。
1.电主轴热源分析
电主轴在高速运行过程中的主要热源分别是 : 高速轴承和内置电机,因此有必要对电机和轴承进行冷却设计,而在冷却过程中,电主轴所处工况、电主轴的转速、电机和轴承冷却结构的设计、冷却液温度控制、冷却液流速、轴承游隙、轴承润滑形式等均是影响电主轴冷却效果的重要因素,电主轴系统的热源、生热量的影响因素以及热量对电主轴系统的影响关系如图 1 所示。
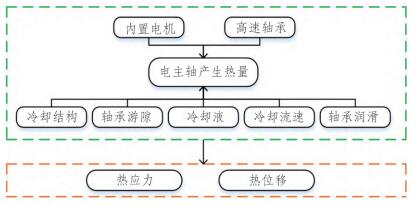
图 1 电主轴系统热量分布图
电主轴内部结构复杂,如果产生的热量未能得到抑制,或者未能及时的排掉,会使电主轴系统产生热应力和热位移,进而会导致机床的加工精度降低,使用寿命下降,严重时会导致轴承失效使主轴出现损坏。对电主轴系统的热态性能进行研究有益于了解电主轴内部的热量分布,可以为电主轴热变形的计算和补偿提供理论基础,有利于提高电主轴转速,促进主轴技术的发展。
2.电主轴系统的发热计算
本文以通用技术集团大连机床有限责任公司自主研发的 UF200 系列电主轴作为研究对象,此款电主轴的最高转速可达 30000r/min,端面跳动小于 0.001mm。首先对电主轴系统的生热量和电主轴系统内部的传热系数进行计算,为进行电主轴仿真分析提供参数。
(1)电机发热计算
对于整个电主轴的而言,内置电机是最为主要的热量来源。其中电机定子的生热量约占电机总生热量的 2/3,电机转子生热量约占电机总生热量的 1/3,并且在电主轴实际的工作过程中,转子所产生热量中的大部分会传入定子,因此在电主轴系统的温度分布中,温度最高的零件是定子。通过公式(1)、(2)可对电机定子和转子产生的热量进行计算。
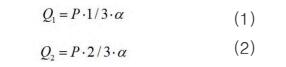
式中 :Q1、Q2 分别表示电机转子和定子产生的热量,kW;P 表示电机的额定功率,kW;α 表示电机损耗,一般取值 0.05。本文所深入研究的电主轴采用的是E+A电机,电机额定功率 56kW,电机的基本尺寸参数如表 1所示。
表 1 电机的基本参数
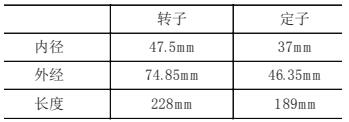
根据电机的基本尺寸信息,通过公式 3、4 可以求解出电机定、转子的生热率 q1、q2。
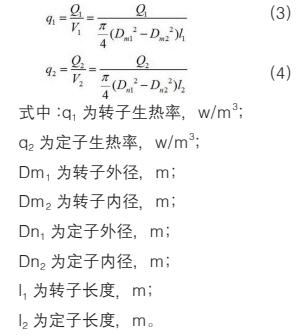
(2)轴承发热计算
在电主轴高速运行过程中影响轴承生热的因素有很多,分别包括主轴转速、润滑形式、轴承滚动体材料、轴承游隙等。本文所涉及的轴承产品选用 FAG 的角接触球轴承,共计 4 组。根据兰州理工大学王保民教授和南京航空航天大学杨阳教授研究可知,可采用 Palmgren 公式对角接触球轴承发热情况进行计算求解。
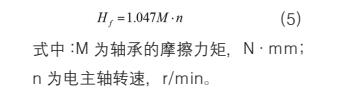
其中轴承的摩擦力矩是由两部分构成,计算公式如式 6 所示。
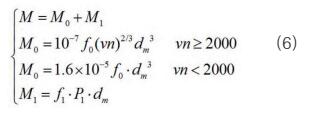
式中 :M 0 为与轴承、转速和润滑油性质有关的力矩参数,N · mm;M1 为与轴承所受载荷有关的力矩,N · mm;f0 为和电主轴系统轴承设计和润滑系统有关的系数,对于高速角接触球轴承而言,当采用油气润滑时,取值 f0=1;
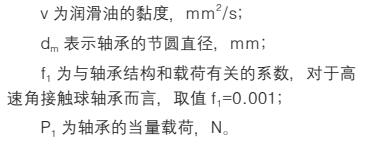
(3)换热系数的确定
为建立准确的电主轴热力学分析模型,需要计算出电主轴内部以及主轴机体与外界空气各种传热状态下的热边界条件,即换热系数。电主轴系统的换热系数主要包括轴承与润滑系统的换热系数、电机与冷却系统的换热系数、轴承与
冷却系统的换热系数、电主轴系统与外界空气的换热系数,电机定子转子间的换热系数,现对传热系数进行计算。
①轴承与润滑系统的换热系数 :
轴承与润滑系统的换热过程较为复杂,此过程的换热系数通常采用经验公式进行计算。

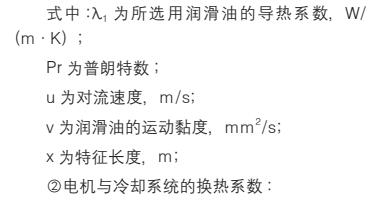
电机冷却在是整个电主轴系统最为重要的结构,电机冷却液与电主轴机体之间的换热过程属于管内流体强迫对流换热。根据传热学的计算方法,对电主轴电机与冷却系统的换热系数进行计算,由于冷却液在冷却槽内流动,冷却液不同的流态有着不同的散热能力,采用的求解公式也不相同,所以需要先对雷诺系数 Re 进行求解,确定冷却液的流态,然后再进行求解。
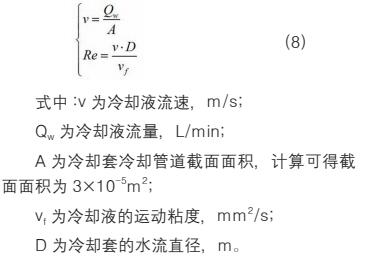
经计算雷诺系数可知,电机冷却系统属于湍流状态,冷却液处于湍流状态下的冷却效果要强于层流状态下的冷却效果,因此在进行电主轴冷却系统设计时,多采用增大冷却液流量,以保证冷却液的为湍流状态。湍流状态下的努塞尔数计算公式如式(9)所示。
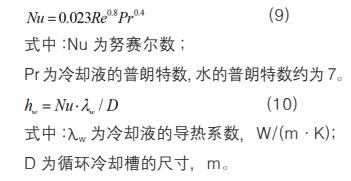
③轴承与冷却系统的换热系数 :
UF200 系列电主轴前后轴承均为角接触球轴承,轴承采用中度预紧,采用油气润滑。在前后轴承座增加轴承循环冷却槽,循环冷却可以有效抑制轴承的温升,保证轴承的正常运转,轴承循环冷却的换热系数的计算方式与电机冷却的计算方式相同,先确定冷却液的流态,再进行换热系数求解。
④电主轴系统与外界空气的换热系数 :
电主轴系统与空气之间的换热过程属于复合传热,根据机床热态特性学基础,取传热系数

⑤电机定子转子间的换热系数 :
电主轴电机的定子和转子之间存在气隙,气隙可以视为两个套在一起的空心套之间的环形间隙,在电主轴高速运转的过程中进行定转子间的热量传递。电机定转子间的换热系数计算与电机冷却换热系数的计算过程相同,首先计算雷诺系数 Re,判断气隙间的气体的流态,其次计算努塞尔数 Nu,最后计算定转子间的换热系数。
3.电主轴系统的稳态热分析
为了计算的简便,现对电主轴模型进行部分简化,取消无相对运动零件间的螺钉连接,采用bond 连接,取消电主轴拉刀机构以及通气、通油孔等细小结构。由于此款电主轴是对称结构而且为了更好的观察仿真结果,现取电主轴剖面进行仿真计算。
仿真条件的确定 :
(1)电主轴转速设置 : 本文所仿真的电主轴的额定转速为 8000r/min,最高转速可达 30000r/min,因此需要对 8000 r/min 和 30000 r/min进行仿真计算,为了增加仿真准确性,增加两组仿真试验,主轴转速取值 12000 r/min 和 20000
r/min。
(2)环境温度设置 : 电主轴进行试验的场所是在恒温净化车间,车间恒定温度 20±1℃,因此仿真计算时取环境温度 20℃。
(3)轴承油气润滑系统,设定温度为20℃,压缩空气压力0.4Pa,冷却系统,冷却液入口温度设定 20℃,出口温度设定 30℃,冷却槽截面前轴承设置为 30×5mm,电机冷却设置为 15×2mm 循环冷却,后轴承冷却设置为26×6mm。
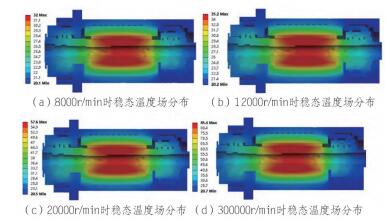
图 2 主轴稳态温度场分布
根据图 2 主轴稳态温度场分布可知,当电主轴的转速为 8000r/min 时,整个电主轴系统的最高温度约 32℃,前轴承温度约 23.8℃,后轴承温度约 22.9℃ ; 当电主轴的转速为 12000r/min时,整个电主轴系统的最高温度约 35.2℃,前轴承温度约 24.8℃,后轴承温度约 24.8℃ ; 当电主轴的转速为 20000r/min 时,整个电主轴系统的最高温度约 57.6℃,前轴承温度约 31.1℃,后轴末温度约28.4℃;当电主轴的转速为30000r/min时,整个电主轴系统的最高温度约 85.4℃,前轴承温度约 40.6℃,后轴承温度约 35.6℃ ; 在电主轴运行过程中,内部最高温度位于内部电机定子处,温度以定子为中心向电主轴前后两端逐渐降低,符合电主轴系统的热量发散规律。
4. 电主轴高速运行试验测试
为了验证仿真结果的准确程度,对电主轴进行试验测试,由于温度传感器的放置会影响测量的准确性,若测量电机定子温度,传感器难以确定放置位置,也无法保证测量的准确,所以采用对电主轴前后轴承进行温度测量,本次测量选用的是德国 isotemp 温度传感器,电主轴综合测试试验台如图 3 所示。
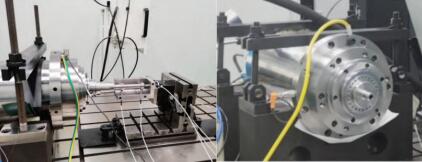
图 3 电主轴综合测试试验台
通过综合性能测试平台测得电主轴在不同转速下的前后轴承温度,在电主轴转速达到8000 转时,前轴承的最高温度为 22℃,后轴承最高温度为23℃ ; 在电主轴转速达到12000 转时,前轴承的最高温度为23℃,后轴承最高温度为 24℃ ; 在电主轴转速达到 20000 转时,前轴承的最高温度为 29℃,后轴承最高温度为 29℃ ; 在电主轴转速达到30000 转时,前轴承的最高温度为 39℃,后轴承最高温度为39℃。
根据公式(11)对电主轴不同转速下轴承的温度误差进行计算。
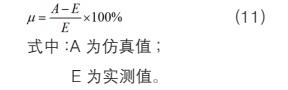
计算得当电主轴转速为 8000r/min 时,前轴承误差为 8.2%,后轴承误差为 -0.4%; 当电主轴转速为 12000r/min 时,前轴承误差为 7.8%,后轴承误差为 3.3%; 当电主轴转速为 20000r/min时,前轴承误差为 7.2%,后轴承误差为 -2.1%;当电主轴转速为 30000r/min 时,前轴承误差为4.1%,后轴承误差为 9.0%,电主轴轴承稳态温度仿真误差在 ±10% 以内,可以认定仿真结果准确。
5. 总结
本文对高速电主轴运行过程中的热量来源和散热过程中的换热系数进行了分析和计算,对电主轴系统不同转速下的温度场分布进行了仿真分析,并通过试验对电主轴仿真结果进行了验证,通过本文的研究可以为电主轴系统的热变形计算提供有益参考。
投稿箱:
如果您有机床行业、企业相关新闻稿件发表,或进行资讯合作,欢迎联系本网编辑部, 邮箱:skjcsc@vip.sina.com
如果您有机床行业、企业相关新闻稿件发表,或进行资讯合作,欢迎联系本网编辑部, 邮箱:skjcsc@vip.sina.com
更多相关信息
- target=_blank>空间凸轮在刀库和自动换刀装置中的设计和加工工艺
- target=_blank>HELI系列的新发展
- target=_blank>西门子828D数控系统在展刀上的应用研究
- target=_blank>4大场景示例 带你穿透理解台达电子组装智造方案内涵
- target=_blank>改善工艺提高数控车床交付能力