发动机缸体曲轴孔铰珩加工设备及加工工艺分析
2019-2-15 来源: 上汽通用五菱汽车股份有限公司 作者:武 书
摘 要:发动机缸体作为发动机核心的部件之一,直接影响着发动机的性能。发动机曲轴通过轴瓦支撑,安装在缸体曲轴孔上。缸体曲轴孔支撑整个发动机曲轴,是发动机的动力输出的核心的部位之一。因此,缸体曲轴孔需要通过铰珩加工来保证加工精度,确保整个发动机的性能。
关键词:缸体曲轴孔;铰珩加工;加工工艺分析
随着社会经济的发展,汽车已经逐步成为人们生活中必不可少的一种生活工具。汽车行业已成为我国重要的经济产业支柱。发动机作为汽车的动力核心部件,始终制约着我国的经济发展。发动机缸体作为发动机核心的部件之一,直接影响着发动机的性能。
发动机曲轴通过轴瓦支撑,安装在缸体曲轴孔上,缸体曲轴孔支撑整个发动机曲轴,是发动机的动力输出的核心的部位之一。因此,为了确保缸体曲轴孔的精度,通常采用铰珩的精加工工艺来保证其最终的产品尺寸要求。本文将会介绍一种完全进口的美国 NAGEL 珩磨机的设备的加工原理、加工工艺以及设备加工过程的调整与质量控制。
1 、设备结构及工作原理
该进口的美国 NAGEL 珩磨机设备主要分为三大系统:机械系统、伺服控制系统、人机交互系统。机械系统包括:机床主体结构,其主要功能是给整个夹具、主轴等提供有效的支撑;定位夹紧部分,该结构功能主要提供加确保工件在机床的固定位置,特别是相对于机床加工主轴的位置,从而确保其加工结果的精度;主轴导轨部分,主要为了加工提供机械结构支撑。
伺服控制系统包括:涨刀控制部分,曲轴孔铰珩采用的刀具寿命较高,在加工过程中刀具会不断的磨损,刀具磨损后为了确保加工直径的合格,在加工过程中,涨刀系统会根据测量结果进行实时补偿;进给控制部分,主要是用于控制加工进给速度、主轴转速及主轴退回速度;测量控制部分,该系统有两个作用:一是在线百分百测量,确保加工结果百分之百合格,及时剔除不合理工件;二是,将测量结果反馈给涨刀系统,为涨刀系统实时补偿提供参数依据。人机交互系统,主要载体是 HIM,用于操作人员指令输入,珩磨加工过程受各方面的影响,现场的操作人员根据实际情况实时调整加工参数来控制加工质量。
2、加工工艺过程
2.1 加工工艺
本文以一款四缸直列发动机缸体曲轴孔铰珩工艺来说明,在制造过程中如何确保最终产品尺寸要求。曲轴孔的加工工艺大致分为 4 大步骤:粗镗曲轴孔半圆;安装曲轴主轴承盖;半精(精)镗曲轴孔;铰珩曲轴孔。
铰珩曲轴孔的工艺主要是为了确保最终的直径、粗糙粗、圆度的要求,曲轴孔的位置度主要
通过精镗来得到保证,铰珩对位置度的修复能有限,几乎可以忽略不计。缸体曲轴孔铰珩加工机械示意图,如图 1 所示,工件采用一面两销定位,通过夹紧压板来压紧缸体顶面。
铰珩加工刀具连接在主轴上,通过加工滑行平台,保证加工的进给跟返回。刀具与主轴连接成一体,类似一根细长轴,具有一定的柔性,在主轴达到一定的转速的情况下,主轴具有一定的矫正能力。
因此,在机床主轴相对工件同轴度满足条件的条件下,刀具的导条将会影响到曲轴孔的加工质量。
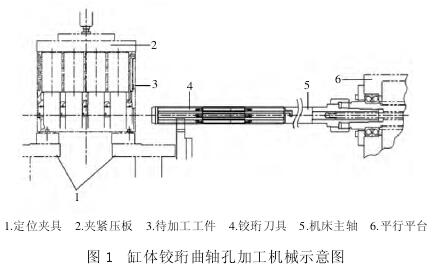
2.2 刀具结构及加工参数选定
铰珩所采用的刀具属于特殊刀具。曲轴孔的加工刀具的选择及设计取决于需要加工缸体每档曲轴孔之间的间隙以及曲轴孔的轴向宽度。该缸体铰珩加工选择的刀具如图 2 所示。
包含区域 1 前导条、区域 2 加工刀具砂条、区域 3 后导条、区域 4 与主轴连接及涨刀连杆。前导条主要是在加工过程中起导向作用,避免加工时晃动大。加工砂条的作用,切削多余加工余量,保证最终产品尺寸。刀具的后导条的作用是在刀具加工完成后,退刀起到导向作用,防止曲轴孔被碰伤。
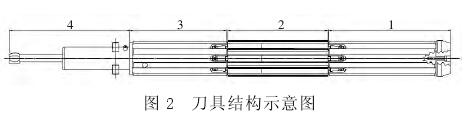
刀具设计要求:前导条的长度要求能够满足 3 个曲轴孔的导向,如 3 图所示。这样可以保证导向的稳定性,进而保证加工质量。切屑砂条的直径设计:为了确保切屑的平稳性,切削砂条需设计成锥度过渡。如下图 4 所示,整个砂条长度为 150 mm,前段初始直径为 准52.95(-0.01,0)mm 到 120 mm 处,按圆锥过渡至直径 准53.01(-0.01,0)mm,最后 30 mm 处的直径要求为 准53.01(-0.01,0)mm,为产品最后的要求尺寸。刀具后导条,只是在刀具返回时,起到导向作用。
因此,在尽量减少设备的整体空间要求下,只要满足2 个曲轴孔同时导向,就能完成导向的作用。该缸体加工所用的刀具的相关参数如下表 1 所示.
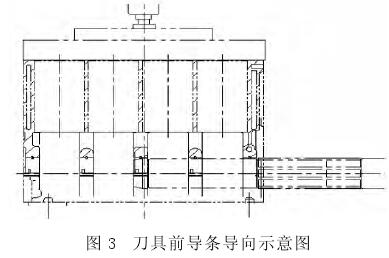
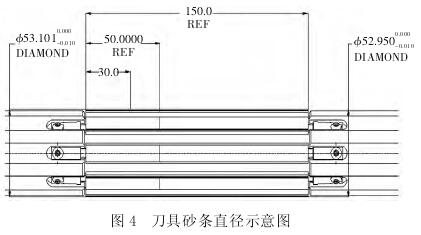
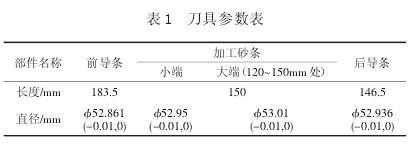
铰珩曲轴孔的加工余量设定与前道加工工序的质量有关,一般情况下,珩磨的加工余量越小加工成本越低,质量控制越好。本文涉及的机型的铰珩加工余量为 0.03 mm.正常工艺控制情况下,要求加工余量不小于以下计算结果:缸体曲轴孔的加工参数包含主轴转速、进给速度、返回速度。
加工参数的选择,影响加工质量跟加工节拍(成本)。主轴的转动是切屑加工的动力来源,主轴转速过快会导致主轴震动大、切削力过大等,从而造成加工质量不稳定、曲轴孔圆度差、加工变形等质量问题。
主轴转速慢会导致切削力不够,工件切不动且加工效率低等问题,根据实际工况条件本机选择的主轴转速为 360 r/min。
加工的进给速度跟加工过程中刀具的导向状态有关,切屑进给是工件能够持续加工的前提条件,进给过快将会导致工件切屑力过大,导致加工变形,刀具砂条挤伤脱落以及加工不充分问题。进给速度过慢,将会导致曲轴孔过量加工,工件直径超差。本机选择的切削参数如下表 2 所示。
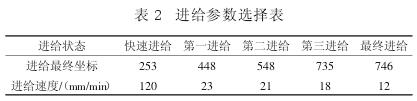
该直列发动的缸体的曲轴孔铰珩加工共分为五个阶段,分别如下:第一阶段:快速进给。该阶段刀具从机床的零点开始到刀具的前导条进入到曲轴孔中,但是砂条还未接触到待加工曲轴孔,留有一定的安全距离,最终进给位置如下图 5 所示,该阶段主要是让刀具贴近加工曲轴孔,进给需要尽量快,以保证加工节拍。
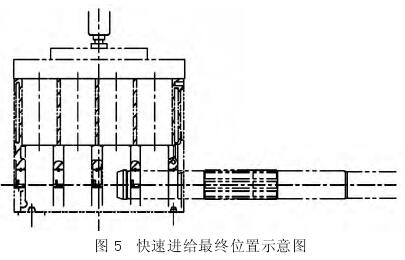
第二阶段:第一进给。该阶段刀具前导条有 3 个曲轴孔作为导向支撑,导向效果好,是所有正常切削过程中进给最快的阶段,直至前导向开始变成 2 个轴孔作为导向支撑,第一进给的最终进给位置如图 6 所示。
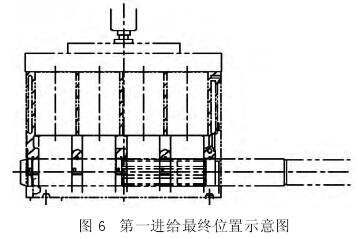
第三阶段:第二进给。该阶段刀具前导条有 2 个曲轴孔作为导向支撑,此时导向效果开始下降,但加工过程比较稳定,此时的进给较第一进给时有所降低,该进给速度一直持续到前导条为单个曲轴孔作为导向支撑,其最终进给的位置如图 7 所示。
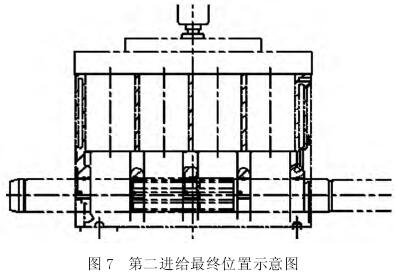
第四阶段:第三进给。该阶段刀具前导向由 1 个曲轴孔过渡到无导向支持,但是此时切削的砂条还处于锥度切削还还未达到成品加工砂条阶段。此时砂条加工的状态容易晃动,只能通过不断降低进给速度保证加工质量,其加工的最终位置如图 8 所示。
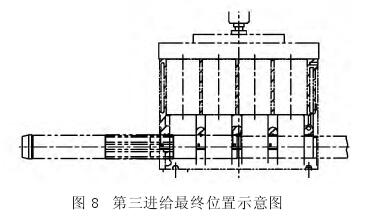
第五阶段:最终进给。该阶段最后一个曲轴孔即将完成加工,此时加工晃动大,进给降到最低。由于设计刀具最后成型的直径长度为 30 mm,而最后一档曲轴孔的轴向宽度为 20 mm,所以最终为了保证加工质量,刀具没有完全伸出到最后一个加工曲轴孔外,只是在最终进给位置停留
1~2 s 的时间,同时也是为了确保在返回的过程的发生碰撞。其加工最终位置如图 9 所示。
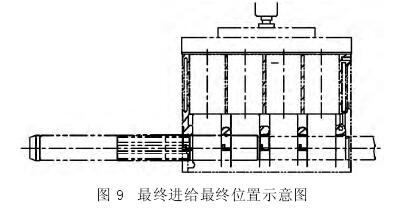
刀具退回,由于本设备采用的是自动涨刀系统,刀具可以根据测量值自动涨刀,但不具备自动收刀功能,加工主轴又具有一定的浮动量,所以工件加工完成后,退刀时,刀具会再次碰到曲轴孔表面。因此,退回速度慢,将会导致曲轴孔直径被二次加工,曲轴孔直径超上差。退回速度过快可能导致曲轴孔直径碰伤、拉伤等问题。本机采用的退回速度为 120mm/min,如果采用自动收刀,那么退回速度可以进一步提升。
3 、结束语
缸体曲轴孔铰珩加工是一种复杂的加工工艺过程,加工质量受到加工环境、设备状态、加工方式的等因素的影响,在日常的生产过程中,需要根据现场生产的实际情况,实时调整控制加工参数,从而来确保最终的产品加工质量。目前国内珩磨加工技术还比较落后,大多数发动机缸体加工所需的机床均是靠进口。珩磨加工的技术的国产化,还有很长的一段路要走,需要一代代工程人的不懈努力与奋斗。
投稿箱:
如果您有机床行业、企业相关新闻稿件发表,或进行资讯合作,欢迎联系本网编辑部, 邮箱:skjcsc@vip.sina.com
如果您有机床行业、企业相关新闻稿件发表,或进行资讯合作,欢迎联系本网编辑部, 邮箱:skjcsc@vip.sina.com
更多相关信息